Alan B
|
posted on 11/1/07 at 07:05 PM |
|
|
Got my plasma up and running
Some pics of the machine and some parts. It went together well, I very pleased with it.
Alan
 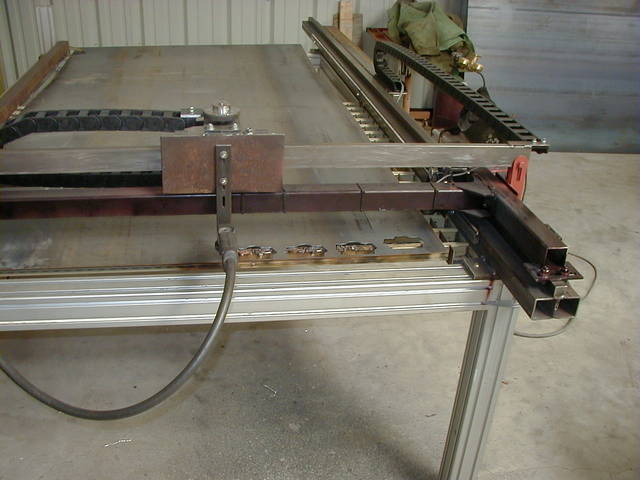 Plasma 1
  plasma 2
 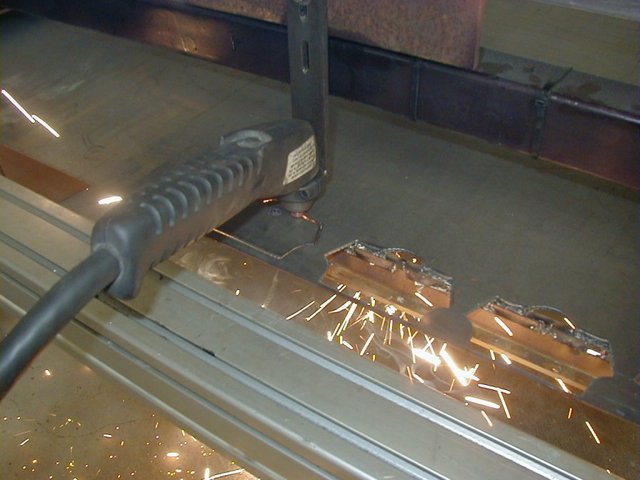 plasma 3
 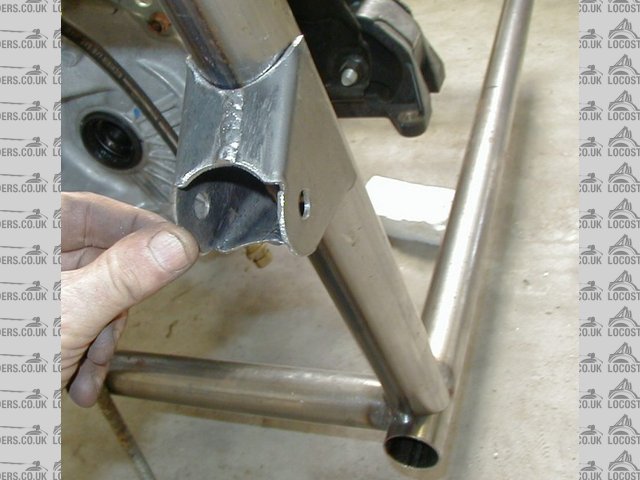 plasma 4
|
|
|
DIY Si
|
posted on 11/1/07 at 07:08 PM |
|
|
Looks very tech that does! Just a shame you live on the wrong side of the pond!
“Let your plans be dark and as impenetratable as night, and when you move, fall like a thunderbolt.”
Sun Tzu, The Art of War
My new blog: http://spritecave.blogspot.co.uk/
|
|
Alan B
|
posted on 11/1/07 at 07:11 PM |
|
|
I guess it depends on the cost of shipping really....it may be non-viable but I'm happy to quote stuff....
Alan
|
|
DIY Si
|
posted on 11/1/07 at 07:14 PM |
|
|
Once I sell the Indy and start crafting something silly, I may have a few bits for you! Just need to persuade her in doors first.
“Let your plans be dark and as impenetratable as night, and when you move, fall like a thunderbolt.”
Sun Tzu, The Art of War
My new blog: http://spritecave.blogspot.co.uk/
|
|
macnab
|
posted on 11/1/07 at 08:54 PM |
|
|
you built all that to make your brackets.
I would have just used an angle grinder
|
|
JoelP
|
posted on 11/1/07 at 09:07 PM |
|
|
very impressed alan, that opens whole new areas for you 
|
|
Alan B
|
posted on 11/1/07 at 09:10 PM |
|
|
My design will use a LOT of brackets....trust me...LOL
Seriously, the need to make brackets much quicker than by hand WAS the motivation....the ability to use for other stuff was the justification for the
investment.
Time wise it took about 40 hours to build and within 1 day I've probably saved 20 hours work on the parts I've made so far.
|
|
JoelP
|
posted on 11/1/07 at 09:16 PM |
|
|
how did you automate the trigger? was it hard to make it time correctly?
|
|
tks
|
posted on 11/1/07 at 09:50 PM |
|
|
mhh
looks good altough "lowost"
only thing i would make was like a schock absorber idea for the plasma head (Z axis) in that way it basculates when needed and keeps be pressed to the
sheet. in this situ it will try to lift your Y axis
anyway looks the dogs ....
if you can make more pics! i'm def interested since i'm into this kind of things to.
wich software do you use? Mach 2 /3 ??
Drives? motors?? Servo or stepper??
Tks
The above comments are always meant to be from the above persons perspective.
|
|
ayoungman
|
posted on 11/1/07 at 09:59 PM |
|
|
Congratulations. I assume its based on an XY plotter type design. Good job.
"just like that !"
|
|
MikeRJ
|
posted on 11/1/07 at 11:13 PM |
|
|
Superb! I'd have been envious if you'd just shown a pic of a plasma cutter, but your CNC Plasma Cutter is an awesome bit of kit!
How many people opened this thread expecting to find a widescreen TV then?
[Edited on 11/1/07 by MikeRJ]
|
|
Middy Tim
|
posted on 11/1/07 at 11:23 PM |
|
|
Wow, that's quite the tool. Mechanical things I usually have no problem understanding, electrical and computer bits are my weak point.
|
|
Peteff
|
posted on 12/1/07 at 12:10 AM |
|
|
If you can cut one one way up and the next upside down and get them closer together you will save a lot of material, does the program allow for this?
yours, Pete
I went into the RSPCA office the other day. It was so small you could hardly swing a cat in there.
|
|
Alan B
|
posted on 12/1/07 at 12:58 AM |
|
|
Thanks guys good feedback..
Joel:
No timing issues, the CNC code gives a start signal I just had to interface it with the torch trigger...not too hard.
Tks:
It really should not touch the metal ideally. The object is to keep it around 1 to 1.5 mm away. It is possible to use current feedback to move a Z
slide and maintain the gap....for me it will be mainy smaller parts in thicker material hence not much surface variation. The kit was from torchmate
who use the flashcut software...doing it again I'd know what bits to use and buy them seperately....this time round I was trying to save time
and money..next time I'd save even more.
ayoungman:
I guess it must be a lot like a plotter....
Middy Tim:
Same here, that's why all the electrics came as a package...there was a bit of head scratching but it was mostly plug and play.
Peteff:
There is an extra program that will do the optimised nesting, but you can do it yourself....in fact I was experimenting with that earlier.
[Edited on 12/1/07 by Alan B]
|
|
kreb
|
posted on 12/1/07 at 01:40 AM |
|
|
Kudos Alan. I run a small to mid-sized sheet metal shop and am trying to figure whether the the best route for our entry into CNC Plasma is a
Torchmate or one of the "higher end" systems.
What software are you running? Do you have any feedback on Torchmate quality, support and such?
https://www.supercars.net/blog/wp-content/uploads/2016/04/1966_FiatAbarth_1000SP1.jpg
|
|
Alan B
|
posted on 12/1/07 at 02:25 AM |
|
|
quote: Originally posted by kreb
Kudos Alan. I run a small to mid-sized sheet metal shop and am trying to figure whether the the best route for our entry into CNC Plasma is a
Torchmate or one of the "higher end" systems.
What software are you running? Do you have any feedback on Torchmate quality, support and such?
With a choice like that the answer is the typical "it depends". The Torchmate 1 is inexpensive and probably perfect for low volume work.
Their other models seem to have more robustness and durability which I guess puts them closer to high end stuff. The software appears to be a modified
version of whatever flashcut use (maybe their own) and the hardware is flashcut.
I opted for not buying the plasma interface and save a couple of hundred figuring out my own (turned out quite easy actually)
Verdict on Torchmate....overall very pleased.
Part quality and packaging 10 out of 10
Documentation 8 out of 10
Delivery 7 out of 10
Value 9 out of 10
Service..... no mark, didn't need any help to get it up and running.
Anything else just shout.
Alan
|
|
locostv8
|
posted on 12/1/07 at 05:36 AM |
|
|
FWIW I used to be part owner of a fab shom where we had a CNC plasma. We went to bottled compressed air for cutting it was cleaner, faster, more
precise, and required less deburing.
http://wrangler.rutgers.edu/gallery2/v/7slotgrille/hssss/
|
|
kreb
|
posted on 12/1/07 at 06:36 AM |
|
|
Bottled compressed air? How's that different from compressor air? Unless you're talking about pure oxygen. Can you clarify? And how
quickly did you go through it?
I'm also curious about when the bevel became a problem. I'd like to be able to cut thicker materials - 1/2" to 1" plate on
occasion, but if the edge becomes significantly off of perpendicular to the face that isn't good - particularly on holes. Alain's holes
look fine, but it's relatively light gauge material.
Oh and Jim - who's Willys kit is that? Is that S-10 based? Looks like my dream company vehicle!
[Edited on 12/1/07 by kreb]
https://www.supercars.net/blog/wp-content/uploads/2016/04/1966_FiatAbarth_1000SP1.jpg
|
|
NS Dev
|
posted on 12/1/07 at 08:22 AM |
|
|
I used to use a 4m x 3m CNC plasma in the prototype shop where I used to work.
You sent the dxf files to its pc, picked the cut lines in order (clockwise put kerf one side, anticlock put kerf the other iirc ) and then sent the
path file to the cutterhead box.
You cut with the work just submerged in water, which gave a MUCH cleaner cut, and stops most of the dust and metal smell.
Bevel became a problem at about 6mm, and was quite bad at 8mm.
This all ran on triple filtered shop air supply. We used nitrogen occasionally for cutting the odd bit of ally.
[Edited on 12/1/07 by NS Dev]
Retro RWD is the way forward...........automotive fabrication, car restoration, sheetmetal work, engine conversion
retro car restoration and tuning
|
|
John P
|
posted on 12/1/07 at 09:11 AM |
|
|
Slight Word of Caution
We've just installed a commercial plasma cutter which comes with an extremely powerful extraction bed.
The installation engineers wouldn't even consider running the machine without the extraction on because the fumes are potentially
carcinogenic.
I would have thought that without really good extraction some sort of mask would be very important.
For reference I have attached a report on this prepared by the plasma cutter manufacturer.
|
|
locostv8
|
posted on 12/1/07 at 09:18 AM |
|
|
The difference is the compressed air was much cleaner. We used a LARGE tank, 6'(?) x 4'(?) (close) and changed it out about once a week
with the table very active. We could program for kerf and had no real problem, if I remember correctly (15 years ago) we also did 2" with a
torch head.
The Willys is an Antique & Collectable 6" stretch cab 40/41 intended for a S10 but the frame you see is a Jeep TJ stretched. With the
blower I wanted AWD to keep it going kinda straight. If interested You could be the proud new owner.
[Edited on 12/1/07 by locostv8]
http://wrangler.rutgers.edu/gallery2/v/7slotgrille/hssss/
|
|
kreb
|
posted on 12/1/07 at 02:56 PM |
|
|
Thanks for the info. I hadn't considered the zinc fume issue, so that'll warrant additional research.
Jim, I wish that I could afford your Willys, but unless you offer really generous financing, or will consider a funky Miata, a rusty Locost frame, a
couple old bicycles and some tin cans in trade, I don't think that I can swing it!o
https://www.supercars.net/blog/wp-content/uploads/2016/04/1966_FiatAbarth_1000SP1.jpg
|
|
sgraber
|
posted on 12/1/07 at 08:33 PM |
|
|
Oh my sweet lord. That is cool. I am trying to determine which of my body parts could bring me enough money to buy one of those.
Bad eyes, bad back, bad hair, bad liver, snipped 'nads, shit! Out of luck.
Steve Graber
http://www.grabercars.com/
"Quickness through lightness"
|
|
Jamie G
|
posted on 9/2/07 at 08:44 PM |
|
|
Nice!
I would love to have one of those. I would be able to just make whatever I wanted for the car/house/garden..... mmmm I think that I have just conviced
myself..... shame I can't fit a 4'x8' table in the shed.......
|
|