philgregson
|
posted on 8/11/02 at 03:24 PM |
|
|
Rear arches - how wide are yours?
Having pondered for ever, I have now decided to put a De Dion rear end on my locost (recent discussions on the matter have now convinced me).
My question is:
As I am now fabricating my axle I can make it as wide as I want and deal with those embarassing empty arch problems.
So -
To those who have bought your rear arches. How wide are the arches obtained from the different suppliers?
Thanks
Phil
|
|
|
Liam
|
posted on 10/11/02 at 08:47 PM |
|
|
But surely it has to be as wide as the Sierra driveshafts define it to be? Unless you want to have the shafts cut and shut - but why bother.
Liam
|
|
philgregson
|
posted on 10/11/02 at 11:17 PM |
|
|
chassis is standard width chassis so I am building the axle so that the wheels fit in the arches - I presume that a sierra in standard form is too
wide.
Also I am hoping to machine my own uprights and the closer to the hub my suspension pickup points are the easier the whole system is to design (or the
way I'm thinking of doing it it is anyway).
Yes I am thinking of modifying (or having modified) the sierra drive shafts.
|
|
Peteff
|
posted on 11/11/02 at 10:36 AM |
|
|
Unequal sierra driveshafts
Aren't Sierra drveshafts two different lengths. If you mount the diff in the middle you could use two long ones or two short ones to vary the rear
track.
yours, Pete
yours, Pete
I went into the RSPCA office the other day. It was so small you could hardly swing a cat in there.
|
|
Simon
|
posted on 11/11/02 at 12:26 PM |
|
|
Petef
In theory, you could use two driveshafts the same length, but your diff would have to be offset to the offside of car, meaning the prop would be at an
angle in the tunnel!
I'd suggest looking at pics in the archive but it don't seem to be working!
Luego do shortened driveshafts.
ATB
Simon
|
|
stephen_gusterson
|
posted on 11/11/02 at 07:44 PM |
|
|
the granada (basically same car) are different lenghts by about 40 - 60mm. Suspect Sierra is similar.
I had a shaft shortened and gas welded / pinned.
I am gonna change it tho. The shafts are hardened, and I dont trust what a weld (done professionally) would do to the shaft. I am going to see if I
can get it shortend and re-splined locally.
My propshaft runs straight in the tunnel and the diff flange is central.
ATB
Steve.
PS - the shafts are solid
[Edited on 11/11/02 by stephen_gusterson]
|
|
Viper
|
posted on 11/11/02 at 07:56 PM |
|
|
quote: Originally posted by Peteff
Aren't Sierra drveshafts two different lengths. If you mount the diff in the middle you could use two long ones or two short ones to vary the rear
track.
yours, Pete
Sierra shafts are equel length..
|
|
Liam
|
posted on 11/11/02 at 09:09 PM |
|
|
Nope the Sierra driveshafts are different lengths - I've got some and I'm 100% certain. I have the Lobro type but I assume the Tripode type will
also be unequal length.
I honestly dont think the sierra track is too wide for a standard chassis. It's only about 6" wider than an escort so you will fill out nicely a
pair of slightly wider arches. They'll need to be about 12" wide - i.e. they'll look cool. I'm using the standard driveshafts and my chassis is
1" wider than standard.
I'm certain the MK Indy chassis is standard width (42") and uses standard Sierra track (Martin told me himself). So presumably his arches would be
fine.
I'm using Dax Rush arches (cos I think they look sexy) and they will have to be cut down slightly.
Liam
[Edited on 11/11/02 by Liam]
|
|
Viper
|
posted on 11/11/02 at 09:44 PM |
|
|
OH SHIT.......i have just refurbished two shafts of the same length...and Liam you are right they are of different lengths, so now i have to refurb
another shaft
|
|
Stu16v
|
posted on 11/11/02 at 10:17 PM |
|
|
L/H and R/H shafts are definately different lengths.
Dont just build it.....make it!
|
|
Liam
|
posted on 11/11/02 at 10:46 PM |
|
|
quote: Originally posted by Viper
OH SHIT.......i have just refurbished two shafts of the same length...and Liam you are right they are of different lengths, so now i have to refurb
another shaft
LOL!!
|
|
philgregson
|
posted on 12/11/02 at 10:26 AM |
|
|
Thanks for the info.
Ok - So I can get away with the wider track in a standard chassis - that's good.
Now if I widen my front track just by lengthening the standard wishbone design will this affect the front geometry significantly?
I'm sure that generally wider track can only be a good thing.
Phil
|
|
Simon
|
posted on 12/11/02 at 11:24 AM |
|
|
Phil,
I believe Luego do the wishbones you need.
Give'm a call.
Unless you want to make them
ATB
Simon
|
|
cymtriks
|
posted on 24/11/02 at 09:54 PM |
|
|
shortening shafts
I once read that the best way to shorten a shaft is not to cut the end off and make a new spline as shaft ends can sometimes be of a different
diameter, bore (not applicable to solid shafts), heat treatment or case depth etc. Somtimes it isn't possible to reproduce the original end details
without some corners being cut.
Aparently the way to do it is to cut the middle, remove the require lenght and clean up the OD either side of the cut by turning down to clean
material. make a collar about three to four inches long with a bore 0.010/0.020mm tight on the new shaft OD. Drill 3/8 holes through the collar, two
or three each end, about 3/4 from the ends and equally spaced around the circumference. Press fit half the collar over one of the shaft ends and weld
up the holes to secure it. Repeat with the other half of the shaft.
That's all from memory so I would suggest you check this out!
|
|
Rorty
|
posted on 25/11/02 at 05:48 AM |
|
|
Works for me on budget jobs. I true them in the lathe and straighten them in the press.
You must assemble and fit them in the same orientation as they were in the donor car, as shafts take on a "set" and can fail if they're "un wound".
When they're finished, I wrap a bit of electrical tape around the inner end of each shaft to "hand" them....red for left hand, and green for right
hand.
  Rescued attachment R2 rear shaft.jpg
Cheers, Rorty.
"Faster than a speeding Pullet".
PLEASE DON'T U2U ME IF YOU WANT A QUICK RESPONSE. TRY EMAILING ME INSTEAD!
|
|
stephen_gusterson
|
posted on 25/11/02 at 09:36 AM |
|
|
Rorty and Cym....
Interesting info.
I would have thought that the best was WAS to have the splines lengthened and then have the ends chopped off.
The reason I say this is that I had my father, in his companies machine shop, shorten a shaft for me.
What he did was to cut the shaft. A dowel was then made on one end, which went into a hole in the centre of the other. Before being engaged, the sides
were machined at an angle right down to the dowel. This allows a gas weld all the way though to the dowel, giving a thick fillet of weld - gas was
used to give max penetration.
I also considered that welding a collar over would be good. Why suggest whats basically a spot weld process, through holes? Is this so that the heat
treatment isnt damaged?
I have been considering junking this shaft. The reason is that its solid, and was heat treated - confirmed by how hard it was to cut! Welding it has
got to have shagged the heat treatment. Do you recon a 5 inch or so sleeve would still make this shaft useable, welded through holes as suggested?
If not, I feel enclined to get one splined and cut at the ends.
As far as heat treatment is concerned, would it be re-hardened if I heated it up in say a pile of coal or charcol, and then quenched it?
Last question, is would this 'unwind' the shaft, ans im cluless what side this came from! I have used a 'long' shaft from donor, unmodified, and a
'long' shaft from another car, cut down. This therefore has gotta be run 'wrong way'. The alternative is to get two short shafts, and repeat whole
process with a sleeve.
The think I like about the sleeve is that if the weld fails, the sleeve might hold the shaft together rather than have a flailing shaft wreck the
car.
comments appreciated!
atb
steve
|
|
Rorty
|
posted on 25/11/02 at 11:41 PM |
|
|
I should have read the post more acurately, as I thought we were talking about LENGTHENING shafts.
Shortening shafts, and re-splining them is often false economy, as some shafts have a difference in metallurgy between the shaft and the ends. If you
are certain the entire shaft has recieved the same treatment, then, providing there is enough meat in them, there's no problem with re-splining them.
Most CV shafts are wasted, and haven't got enough meat to re-spline them.
I believe doweled joints are a waste of machining time, and aren't as strong as sleeved shafts. Do drill holes near the ends of the sleeve as
Cymtricks points out, and rose-weld them. It's immensly stronger. Choose a grade of seamless tube for the sleeve, that matches, as closely as
possible, the strength of the shaft. Tube from the hydraulic industry is a good starting place.
Whether you shorten or lengthen a shaft, you MUST true it up afterwards. A shortened/lengthened shaft that is even slightly out of true, will, without
fail, fail. Eh? You know what I mean.
If you are going to have a shaft resplined, re-think your plan. it's really not that much more expensive to have shafts made up. There are a few
things you should know though.
Try and find an engineer who has made them before, as he should know the short cuts.
Otherwise just approach any good engineer, with this information. There are several ways to machine the splines. Without getting technical, there are
expensive ways, and cheaper ways. The expensive way (for you, doing one-offs), is the original manufacturer's method. Look at the end of a shaft,
about an inch from the end, and you'll see a shoulder where the splines end, and the inner star of the CV butts up against.
An easier/cheaper method is to cut the splines with a fly/gear cutter, and just let the splines run out past where the shoulder would be on an
original shaft. Wasting the shaft means these splines basically run out to nowhere, and also reduce weight.
Now, machine a groove where the shoulder should be, and fit a circlip. Simple, and cheap!
Talking about weight, you could specify gun-drilled bar (hollow) for the shafts, which will save another 30% roughly.
To acurately measure the length of shaft needed, make an axle gauge like mine in the pic below.
 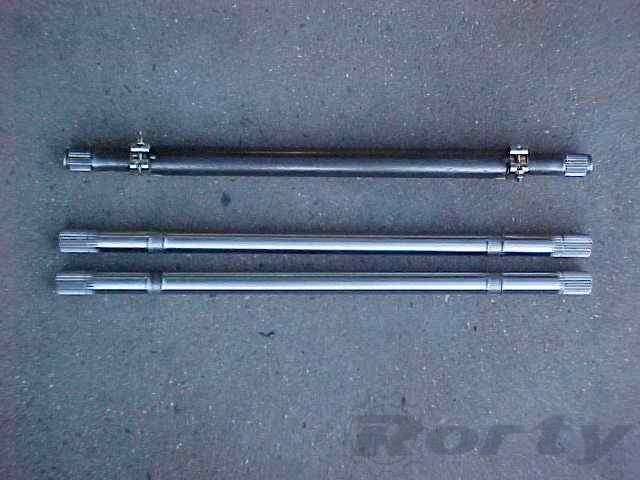 Rescued attachment Axle gauge & axles.jpg
Cheers, Rorty.
"Faster than a speeding Pullet".
PLEASE DON'T U2U ME IF YOU WANT A QUICK RESPONSE. TRY EMAILING ME INSTEAD!
|
|
Rorty
|
posted on 26/11/02 at 12:19 AM |
|
|
Steve: You really can't re-heat treat a sleeved shaft, as the two materials would contract at different rates, building up probably more stress than
if you'd just left them alone.
Best bet before welding them, is to turn on the oven in the kitchen, and set it to "Melt Down".
As soon as the shafts are welded, throw them in the oven, and turn the oven off. Don't open the oven again until it's stone cold. If you only eat
carry outs, bury the shafts in the ashes of a fire....anything at all to slow the cooling process. If you quench them, they'll be super brittle, and
will shatter the first time you stick the wellie into it.
There's nothing you can do about heating the shafts to normalise the grain to remove the "set". If you already have the shafts, and don't know
which way they were orientated, just go ahead and modify them anyway. Chances are they'll be OK. You'll soon hear them if they're not! I'm just
super cautious, as I give my shafts a severe workout going over 4' jumps etc.
I heard an old bloke one day describing his method of prepping shafts. He would turn down the two splined ends, and press them into the ends of a
length of seamless tube, install them in the car, and set off driving. The first time the splines would try and spin in the tube, they would weld
themselves in position, and never move again. They'd need to be a reasonably tight interference fit, but they'd be centred. Simple, if true.
Cheers, Rorty.
"Faster than a speeding Pullet".
PLEASE DON'T U2U ME IF YOU WANT A QUICK RESPONSE. TRY EMAILING ME INSTEAD!
|
|
johnston
|
posted on 26/11/02 at 01:52 PM |
|
|
why not get shafts made up theres a company does it advertise in most mags canny remember the name got a quote to make up lenghted mk3 escy ones cant
remember exact prize but it wasnt dear
but a gd egineering firm shold be able to make a shaft
|
|
stephen_gusterson
|
posted on 26/11/02 at 08:45 PM |
|
|
rorty advice
thanks for the advice Rorty.
I already have the shaft made up, and so if I went to an engineering workshop, that would be a pattern for them to work from.
My company used to use a local machine shop quite a lot.
They are in the same small town I live in and are only 4 minutes away.
Might be a good idea to get a costing from them - if I cant see anything else in magazines.
Could also get them to sleeve the one I have - that might work. What about getting someting turned out of bar?
Could get them to true it up at the same time.
cheers
Steve
|
|
Liam
|
posted on 26/11/02 at 09:40 PM |
|
|
Steve - I dont understand your driveshaft situation. Maybe you could enlighten me?
How come you can use one long shaft unmodified then need another one shortened - can't you just use the short shaft from the donor. How wide is your
track - I thought your car is a bit wider than standard isn't it. Cant you use the standard Sierra track? If you're not using sierra track width
how can you use one of the shafts unmodified - your diff flange is central isn't it?
Liam
[Edited on 27/11/02 by Liam]
|
|
stephen_gusterson
|
posted on 26/11/02 at 10:02 PM |
|
|
never think anything is central.
Not thinking of using a sierra dif hey Liam
The pic shows the diff mounted between two channels. (Not white on the car - managed to get some 2.5mm from an old food conveyor system at work. Its a
bugger getting that white off).
Follow the casting line from the prop flange to the runner mount at the back. Is it central? Bu#^er is it.
If you mount the diff with the prop flange central in the tunnel, you get different length requirements for the shafts.
Didnt occur to me until it was all welded in a year ago. So I have had time to think about it!
As far as I recall, the offset is worse than 20mm or so - and more like 40mm.
One shaft fits great. About 30mm side float (to allow length movement as the suspenison scribes an arc) as per the donor. Std shaft on other side,
was too short. Swapping shaft thats fits on other side is too long. Totally compressed with no movement available.
I mixed and matched the shafts to fit so there is a chance that the shaft is from the other side. (Hope Rortys 'set' on the shafts isnt a problem).
So, I got another shaft, and had them modified as per my earlier post.
The track of my car, from inner wheel to inner wheel is about 51 ins. Just about as per Granada / Sierra.
However, the friggin diff on those cars isnt quite central.
So there is the story.
I got shafted (or need to be!)
atb
Steve
Anyone noticed that this used to be a thread on rear arches?
[Edited on 26/11/02 by stephen_gusterson]
 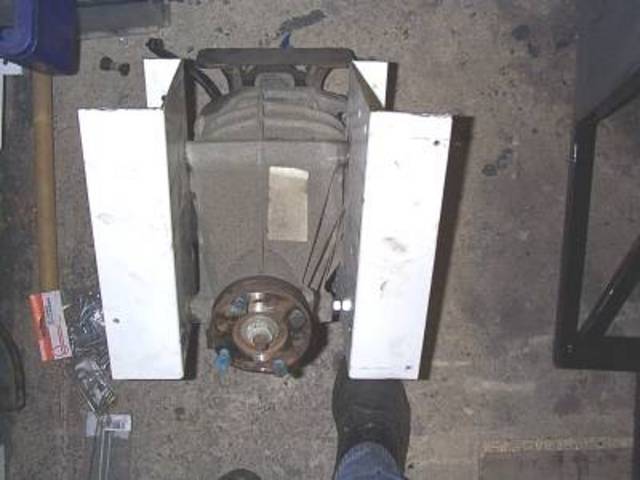 Rescued attachment diff.jpg
|
|
Liam
|
posted on 27/11/02 at 12:11 AM |
|
|
Huh? I dont get it...
I know the big mount at the back of the diff isn't central, but that isn't central in the Sierra either. I'm sure I concluded the prop runs
straight down the middle in the sierra when i measured it before chopping it apart.
Worried, I just went and measured up my diff and shafts again. The distance from centre to the drivers side flange is 130mm and from centre to the
other flange is 170mm. Difference is 40mm and my long shaft is 40mm longer than the other one. That puts the prop flange central to the car.
This is all give or take a couple of mm. How much are you talking about when you said your short shaft was too short?
From the pics it looks like the MK indy mounts the sierra diff with the prop flange central, and i've seen a few CAD drawings with it central too.
But how can your experience be wrong?
Wierd. Maybe I'll post something on the indy list and ask them where the diff goes. Luckily mine isn't mounted yet.
Hmmmmm
Liam
[Edited on 27/11/02 by Liam]
|
|
Liam
|
posted on 27/11/02 at 12:45 PM |
|
|
Little update...
Just spoke to Martin Keenan. "100%, bang centre" were his exact words when queried about the lateral position of the propshaft flange of the Sierra
diff. That and my own measurements are good enough for me, so in the middle it goes.
That still leaves me baffled about your experience then Steve - hmmmmm. Is it possible your hubs are a little further out than the Sierra? But then
how on earth does just one shaft fit? I'm assuming there's no way you could have made your car assymetrical by accident, so I'm a bit
clueless...
Oh well as long as we're both happy.
Liam
|
|
James
|
posted on 27/11/02 at 01:03 PM |
|
|
My experience (such as it is! ) is the same as Liam's. That the side of the diff that is wider just has a shorter shaft to compensate.
As long as you mount the diff such that the propshaft connecting plate is central on the car I can't envisage any problems.
Yes, the upper mount will be offset (if you use it- MK appear not to) but that shouldn't be a problem.
Or maybe (and more likely) I've missed something fundamental....
Cheers,
James
|
|