StuartBJ
|
posted on 13/11/11 at 09:37 PM |
|
|
Budget 8 Piston Brembo Calipers - Ford & Mercedes
Evening Ladies & Gents.
Finally got all the parts together to allow me to install the front calipers on the car V12, little bit more fine adjustment needed and it will be
finito. I thought I would show you how it was all done incase you are running a powerful & heavy car (ultima/GT40..types) and need/want extra
stopping power..... but don`t want to pay the quite stupid prices these things seem to sell for.
I`m running such mahoosive calipers because they were locost and I wanted to make them work, yes I`m sure I could of used ultra lites and had lower
unsprung weight and yes I`m probably over braked etc but that`s not really the point of this little 'rant'...so with that in mind....here
we go
Once upon a time....when I naively thought I could use Mercedes running gear and hubs, I managed to get hold of a very reasonally priced set of 8
piston Mercedes calipers (made by Brembo), from a SL55.
As the project moved on and the Mercedes running gear was binned in favour of a hybrid Mercedes/Ford set up I found myself with a set of discs/pads
and calipers that I couldn`t use with ford 4 stud hubs....(5x112). I realised that Ford used this same stud pattern on the Granada (BINGO), Okay yes I
had to get some custom mushrooms made for the hub but that was a small price to pay....cheap too (£50)...to avoid paying out for a complete new brake
system and in theory it would work....in theory.
The mercedes caliper bracket had to go.....it wasn`t even close and dedicated brackets had to be made. The material for the job is our old friend 2024
aluminium (nice and strong).
I decided the calipers needed a good clean and a lick of paint, my friend has a parts washer (which made my life much less messy) and I decided to
restore the Brembo`ness, making sure you use high temp paint....... What makes me smile is that I`m trying to make the brakes look like high
performance Brembo upgrade (along similar lines as to the fake stick on Brembo cover you can get from Flea bay)....but ironically these are
Brembo`s....well it makes me smile.
I have made sure the bolts were HT, 12.9 for the caliper/bracket (M12 x 100) and 10.9 (M10 x 60) spaced with washers where required.
So before it all comes off for a clean and polish (wheels also here is the dry install....enjoy.
If you fancy having a go and need any brackets machining, drop me a message and I`ll put you in touch with a very skilled chap, good job and very
reasonably priced.
|
|
|
SeaBass
|
posted on 14/11/11 at 09:13 AM |
|
|
Looks good - I would be slightly concerned about the loadings on your adapter bracket though. There seems to be a large amount of leverage generated
around the original mounting holes.
|
|
StuartBJ
|
posted on 14/11/11 at 09:50 AM |
|
|
quote: Originally posted by SeaBass
Looks good - I would be slightly concerned about the loadings on your adapter bracket though. There seems to be a large amount of leverage generated
around the original mounting holes.
Thanks. The original bracket hub mounting points did indeed have a wider span, sadly there is no easy way to change the mounting geometry. The only
mitigation avaliable to me at the moment is to replace the cast material (bracket) and the fasteners with something stronger. If i were to ever do it
again I might ensure that I increased the Radi of all the bracket edges to reduce any stress raisers.
|
|
MakeEverything
|
posted on 14/11/11 at 11:20 AM |
|
|
Looks good, and love your project.
I would beef up the bracket a little, and get load rated bolts to replace the allen bolts you have there. Also, rounding off the edges will reduce
the potential for fracture. Notice none of the other suspension components have square edges.
Good luck. I would get some serious testing in before hitting the road or track though.
Kindest Regards,
Richard.
...You can make it foolProof, but youll never make it Idiot Proof!...
|
|
MikeRJ
|
posted on 14/11/11 at 06:53 PM |
|
|
quote: Originally posted by MakeEverything
I would beef up the bracket a little, and get load rated bolts to replace the allen bolts you have there.
Agreed on the bracket, but what are" load rated bolts"? The bolts the OP is using are 10.9 and 12.9; if he needs higher tensile bolts
than that then something is seriously wrong with the design.
|
|
maccavvy
|
posted on 14/11/11 at 07:10 PM |
|
|
Look awesome...but when you say budget..what was the rough cost.
I got these fitted on my car..325 mm disc and 4 pot monoblock stops a treat for less than 500
|
|
steve m
|
posted on 14/11/11 at 07:32 PM |
|
|
looks like you have a wheel bolt missing,
or is it just the way the picc is?
|
|
StuartBJ
|
posted on 15/11/11 at 10:58 AM |
|
|
quote: Originally posted by steve m
looks like you have a wheel bolt missing,
or is it just the way the picc is?
They are all about..."somewhere" 
|
|
Fred W B
|
posted on 15/11/11 at 05:14 PM |
|
|
So If I understand correctly you have m12 bolts through a 25 mm thickness. So leaving at best 6 mm of ally on each side of the bolt to resist the load
imposed by the calipers trying to rotate when applied? I don't think they will last a minute.
Cheers
Fred W B
You can do it quickly. You can do it cheap. You can do it right. – Pick any two.
|
|
MikeRJ
|
posted on 15/11/11 at 06:48 PM |
|
|
quote: Originally posted by Fred W B
So If I understand correctly you have m12 bolts through a 25 mm thickness. So leaving at best 6 mm of ally on each side of the bolt to resist the load
imposed by the calipers trying to rotate when applied? I don't think they will last a minute.
Cheers
Fred W B
I had totally missed the fact they were alloy brackets, that does sound a bit weak. Looking at the spacers required to at either end of the bracket,
it should be possible to dispense with them and add extra material around the mounting area to compensate e.g.
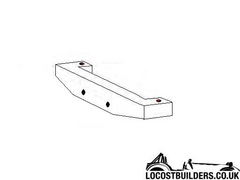 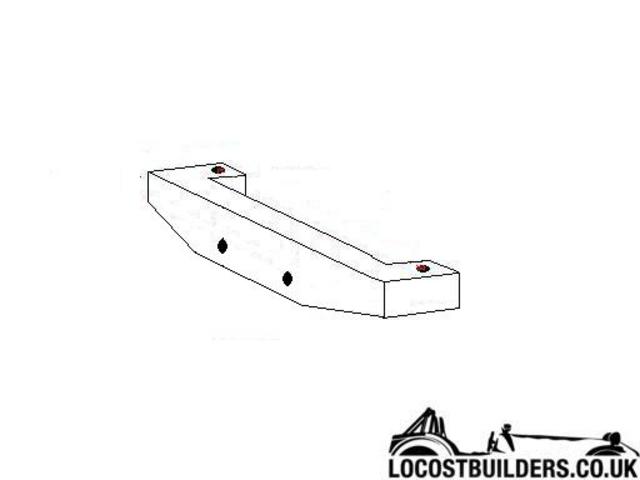 Description
I'd probably also get rid of those sharp inside corners on the "ears" that the caliper bolts onto and replace with a decent sized
radius.
[Edited on 15/11/11 by MikeRJ]
|
|
phelpsa
|
posted on 15/11/11 at 06:51 PM |
|
|
I don't like the lack of rads in these sketches. You might get away with it with steel but definitely not with ali.
|
|
MakeEverything
|
posted on 16/11/11 at 09:32 AM |
|
|
quote: Originally posted by MikeRJ
quote: Originally posted by MakeEverything
I would beef up the bracket a little, and get load rated bolts to replace the allen bolts you have there.
Agreed on the bracket, but what are" load rated bolts"? The bolts the OP is using are 10.9 and 12.9; if he needs higher tensile bolts
than that then something is seriously wrong with the design.
I didnt see the HT bolts comment between the pictures, as they look like standard allen bolts as said in my original post.
Kindest Regards,
Richard.
...You can make it foolProof, but youll never make it Idiot Proof!...
|
|
daviep
|
posted on 16/11/11 at 09:56 AM |
|
|
quote: Originally posted by MakeEverything
I didnt see the HT bolts comment between the pictures, as they look like standard allen bolts as said in my original post.
Apart from stainless I don't think I've ever seen a cap screw with a tensile rating of less than 10.9, I'm sure you probably get
them but a "standard" allen cap screw will be 10.9 or 12.9 in my experience.
Davie
“A truly great library contains something in it to offend everyone.”
|
|
StuartBJ
|
posted on 18/11/11 at 09:02 AM |
|
|
quote: Originally posted by phelpsa
I don't like the lack of rads in these sketches. You might get away with it with steel but definitely not with ali.
I`m rounding off all the edges to prevent stress raisers .....then time for some serious testing.....any volunteers?
[Edited on 18/11/11 by StuartBJ]
|
|
liam.mccaffrey
|
posted on 18/11/11 at 12:23 PM |
|
|
you're most lilkely to get cracks forming on the internal corners of the bracket. You can't really round them out as the material is
already gone. I would make them from steel and at least put as large a rad as possible in there if you're making from Ali
This is meant to be be constructive, please don't take offence. I'm doint this exact same process with Rx7 twin turbo calipers and mx5
uprights.
Build Blog
Build Photo Album
|
|
StuartBJ
|
posted on 18/11/11 at 12:35 PM |
|
|
quote: Originally posted by liam.mccaffrey
you're most lilkely to get cracks forming on the internal corners of the bracket. You can't really round them out as the material is
already gone. I would make them from steel and at least put as large a rad as possible in there if you're making from Ali
This is meant to be be constructive, please don't take offence. I'm doint this exact same process with Rx7 twin turbo calipers and mx5
uprights.
None taken, it`s all in the name of development .... With respect to internal radi, I`m looking at my options. I may be able to build it up with weld,
but I can`t remember how well 2024 takes to welding. I`ll probably end up machining them again to be on the safe side. At least the theory and
geometry will be sound.
[Edited on 18/11/11 by StuartBJ]
|
|
jossey
|
posted on 18/11/11 at 02:29 PM |
|
|
quote: Originally posted by steve m
looks like you have a wheel bolt missing,
or is it just the way the picc is?
its an invisble wheel locking nut to confuse the thiefs....
Thanks
David Johnson
Building my tiger avon slowly but surely.
|
|
TAZZMAXX
|
posted on 18/11/11 at 03:15 PM |
|
|
If you worked on edge distances used in structural steel marking out, the centre of the holes are 1.5xhole dia to closest edge. Assuming 13mm and 11mm
holes the relative sections would need to be increased from 30 to 39 and 25 to 33. Agree with large internal radii as well but I think the sections
are the greater cause for concern.
|
|
maccavvy
|
posted on 18/12/11 at 07:09 PM |
|
|
the bolts are chrome...but the locker is black. so very hard to see.
heres a close up of my brackets..been on a year with no issues whatsoever

|
|