mangogrooveworkshop
|
posted on 15/2/05 at 08:53 PM |
|
|
How much to machine this up
The measurements: Height 40mm
Inside Diameter 40mm Weight 740g it fits on shafts and costs a shed load of money.
 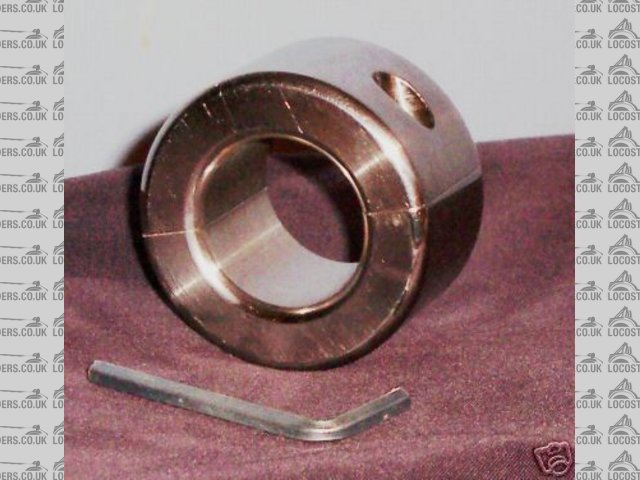 Rescued attachment aaaaaaaaaaaaah.JPG
|
|
|
Mark Allanson
|
posted on 15/2/05 at 09:07 PM |
|
|
Much depends on the tollerances, and number to be produced. With CNC, the first would cost £400 and about £3 thereafter
If you can keep you head, whilst all others around you are losing theirs, you are not fully aware of the situation
|
|
mangogrooveworkshop
|
posted on 15/2/05 at 09:23 PM |
|
|
tolerences dont have to be that good Its pretty much a universal fit.
[Edited on 15-2-05 by mangogrooveworkshop]
|
|
flak monkey
|
posted on 15/2/05 at 09:37 PM |
|
|
What is it? And whats it made of? Then someone may be able to give you a better idea...
David
Sera
http://www.motosera.com
|
|
krlthms
|
posted on 15/2/05 at 09:54 PM |
|
|
quote: Originally posted by Mark Allanson
Much depends on the tollerances, and number to be produced. With CNC, the first would cost £400 and about £3 thereafter
It appears to be made in two halves screwed together. Can CNC do threading?
KT
|
|
flak monkey
|
posted on 15/2/05 at 10:03 PM |
|
|
Yes CNC machines can do tapping. Very quickly, efficiently and accurately...
That part would be made in 3 main operations i reckon;
It would be turned/ground to the final dimensions.
The holes would be drilled and tapped for the bolts.
Then it would be slit using a very thin (<0.5mm) slitting wheel.
The out of round caused by the slitting is very small, and would actually not affect the performance of the part.
This is the way similar parts to that were produced at a bearing company i was working at over the summer... actually they were bearing inner and
outer races. Slit after all of the final grinding etc...
Cheers,
David
[Edited on 15/2/05 by flak monkey]
Sera
http://www.motosera.com
|
|
David Jenkins
|
posted on 15/2/05 at 10:22 PM |
|
|
It also depends on the desired material - if it's phosphor-bronze (it looks like it might be) it can be a real bar-steward to machine. If
it's brass it's a doddle.
rgds,
David
|
|
britishtrident
|
posted on 15/2/05 at 10:27 PM |
|
|
Have you tried your local bearing suppliers ?
|
|
big_wasa
|
posted on 15/2/05 at 10:54 PM |
|
|
I would doubt that it would be cut in half?In my experiance it would be made from 2 bits of plate and turned down together .Whats it for ?and what
does it need making from?
|
|
Hellfire
|
posted on 16/2/05 at 12:34 AM |
|
|
That's a very basic question which I think was done intentionally...
There are many factors involved in costing that job...
- Do you have a drawing to work from?
- What is the material?
- How many do you require?
- Are you supplying the material...
£400 is a lot steep - one off wouldn't do on CNC - minimum 10.
CNC have problem with tapping depending on diameter and by the look of it, it is radial so a special attachment is required - if the machine has the
capability. I have a number of options available but I would need more information. Logistically it could be a problem also...
Just for the record - I'd split larger material first, then drill, counterbore and tap, fasten two halves together then turn and bore it to keep
it all round and concentric.. which is good if it's spinning.
Just my opinion
|
|
flak monkey
|
posted on 16/2/05 at 08:15 AM |
|
|
quote: Originally posted by Hellfire
Just for the record - I'd split larger material first, then drill, counterbore and tap, fasten two halves together then turn and bore it to keep
it all round and concentric.. which is good if it's spinning.
Just my opinion
Many ways of reaching the same outcome. That way was also used in the company I was working at...IIRC
David
Sera
http://www.motosera.com
|
|
Dick Axtell
|
posted on 16/2/05 at 10:17 AM |
|
|
Damper
Looks like a harmonic damper, for drive shafts on FWD cars.
Harmonic damper = Lump of metal, whose mass is tuned to minimise vibrations.
How mucha da costa??
Work-in-Progress: Changed to Zetec + T9. Still trying!!
|
|
bob
|
posted on 16/2/05 at 10:33 AM |
|
|
Looks like one of our rollers off a print finishing machine,if so yes they are a fortune to buy from machine suppliers.
|
|
Peteff
|
posted on 16/2/05 at 10:41 AM |
|
|
That's what I thought Bob. Draw rollers look like that and have to be adjustable. The ones I worked on were slightly knurled though
yours, Pete
I went into the RSPCA office the other day. It was so small you could hardly swing a cat in there.
|
|
mangogrooveworkshop
|
posted on 16/2/05 at 01:01 PM |
|
|
51 quid each they are 78 quid normaly
I recon I could pay for a lathe buy making a few of these.
[Edited on 16-2-05 by mangogrooveworkshop]
|
|
mangogrooveworkshop
|
posted on 16/2/05 at 01:14 PM |
|
|
fits on shafts and costs a shed load of money cryptic clue
[Edited on 16-2-05 by mangogrooveworkshop]
|
|
krlthms
|
posted on 17/2/05 at 05:14 PM |
|
|
Does it need to be in two parts for fitting?
How about casting; does anyone cast metal anymore, or only for vintage cars?
Cheers
KT
|
|
Wadders
|
posted on 17/2/05 at 05:32 PM |
|
|
Yup, looks like it came off the slitting shaft of a folder.
Originally posted by bob
Looks like one of our rollers off a print finishing machine,if so yes they are a fortune to buy from machine suppliers.
|
|
nick baker
|
posted on 17/2/05 at 06:17 PM |
|
|
erm... if cutting/drilling etc before turning, I'd suggest putting a .2mm shim-plate between the two parts: you want to KNOW that it's
going to be clamped tight.
I'd want to know if those rounds are entirely nessecarry: would chamfers do?
In the interests of cheapness though, (I'm assuming it's a drive-shaft mass)... I'd turn it first, (do the drilling before I part it
off)(pocket it with a milling tool before drilling and tapping)... Then part it off, and then split it with a 1mm disk.
With regards to positioning the halves while bolting it up... use two 1mm shim-plates.
But I'd only be able to do it in stainless or 7005. It's all i have readlily available.
|
|
bob
|
posted on 17/2/05 at 06:24 PM |
|
|
quote: Originally posted by Wadders
Yup, looks like it came off the slitting shaft of a folder.
Originally posted by bob
Looks like one of our rollers off a print finishing machine,if so yes they are a fortune to buy from machine suppliers.
Wadders
Sounds like we are in the same trade
|
|
Wadders
|
posted on 17/2/05 at 07:20 PM |
|
|
Not for a few years Bob, but yes iv'e spent many a stressful hour fiddling with an unwilling MBO.
Sounds like we are in the same trade
|
|
mark_UK
|
posted on 17/2/05 at 09:59 PM |
|
|
Looks like what we called shaft collars at the last place I worked,used to hold things in place on shafts(one either side)such as carrier plates
etc.Also come in one piece(slit thru one side)
http://rswww.com/cgi-bin/bv/browse/Module.jsp?BV_SessionID=@@@@0491162235.1108677426@@@@&BV_EngineID=ccchadddlellglgcfngcfkmdgkldfik.0&cacheID
=ukie&3286130236=3286130236&stockNo=2899537
|
|