Micael
|
posted on 17/7/07 at 05:54 PM |
|
|
Escort axle oil leak
I have a major oil leak from my escort axle. The whole drum on the right side was full of oil.
Does anyone know if there should be any gaskets between the axle casing and the half shaft/bearing/flange?
This explains why the rear brakes worked so bad.
Micael Moose Åman
Petrolhead and all around nice guy
"Don't leave the duck there. It's totally irresponsible. Put it on the swing, it'll have much more fun." //Sleep Talkin Man Dec 23
2009
|
|
|
watsonpj
|
posted on 17/7/07 at 06:21 PM |
|
|
ho gasket afaik but the bearing has seals and has an o ring bearing around the outside that seals against the casing. So its half shafts out and new
bearings I guess.
|
|
Danozeman
|
posted on 17/7/07 at 09:00 PM |
|
|
IIRC The seal is in the brg. I have changed a few on a cortina axle on a tiger for a bloke because it kept blowing the seal.
Dan
Built the purple peril!! Let the modifications begin!!
http://www.eastangliankitcars.co.uk
|
|
Micael
|
posted on 17/7/07 at 09:38 PM |
|
|
ok thanks.
I'll have to change the bearing then
Micael Moose Åman
Petrolhead and all around nice guy
"Don't leave the duck there. It's totally irresponsible. Put it on the swing, it'll have much more fun." //Sleep Talkin Man Dec 23
2009
|
|
britishtrident
|
posted on 19/7/07 at 08:48 AM |
|
|
When you get a bearing make sure the retaining collar comes with it.
These bearings are quite easy to change without a press --- do a search and you should find one of several threads in which I have given the
procedure.
[I] “ What use our work, Bennet, if we cannot care for those we love? .”
― From BBC TV/Amazon's Ripper Street.
[/I]
|
|
Micael
|
posted on 31/7/07 at 01:01 PM |
|
|
I have now changed bearing on one side. It wasen't that hard. The bearing itself was a tight fit, but not to hard. The collar slide right on
after i had heat(red) it up with my gas welder.
I had to use the anglegrinder to remove both the old bearing and the collar.
Micael Moose Åman
Petrolhead and all around nice guy
"Don't leave the duck there. It's totally irresponsible. Put it on the swing, it'll have much more fun." //Sleep Talkin Man Dec 23
2009
|
|
ChrisGamlin
|
posted on 31/7/07 at 01:38 PM |
|
|
If you're going on track its worth putting a small tack weld on the retaining collar to ensure it can't move as all the race / rally boys
do. The press fit of the bearing is the only thing that holds the halfshaft (and therefore the wheel) in place and in high load cornering it has been
known for the bearing / retainer to slip on the halfshaft (ie your rear wheel goes AWOL!) when subjected to high cornering forces and rough treatment.
|
|
Micael
|
posted on 31/7/07 at 01:50 PM |
|
|
good idea! will do that.
Is there any risk that the heat from the weld weakens the halfshaft?
Micael Moose Åman
Petrolhead and all around nice guy
"Don't leave the duck there. It's totally irresponsible. Put it on the swing, it'll have much more fun." //Sleep Talkin Man Dec 23
2009
|
|
britishtrident
|
posted on 31/7/07 at 06:37 PM |
|
|
Don't touch the shaft with a welder it will cause failure due to local stress raiser and undoing heat treatement.
I have seen shafts on racing escorts fail due to this --- failure at the outer end of a half shaft isn't good.
[I] “ What use our work, Bennet, if we cannot care for those we love? .”
― From BBC TV/Amazon's Ripper Street.
[/I]
|
|
ChrisGamlin
|
posted on 31/7/07 at 07:38 PM |
|
|
I bet theres been many more failures due to not doing it though, and we're only talking one or maybe two small tack welds, not MIG'ing it
all the way around!
[Edited on 31/7/07 by ChrisGamlin]
|
|
britishtrident
|
posted on 31/7/07 at 08:04 PM |
|
|
quote: Originally posted by ChrisGamlin
I bet theres been many more failures due to not doing it! We're only talking a couple of small tack welds, not MIG'ing it all the way
around!
Even ignoring the effect on the mettalurgy of the heat affected zone applying Fracture mechanics reveals small tack welds are worse, as a
singularlity such as a tack weld represents a point of infinite stress, the point at which fatigue faliure starts..
Over hundred years ago an engineer called August Wöhler did an indepth investigation of the failure of axles --- well worth doing a google on.
[Edited on 31/7/07 by britishtrident]
|
|
Micael
|
posted on 31/7/07 at 09:53 PM |
|
|
I have now put two tack weld on each shaft. Time will tell if it was a good choice or not.
Micael Moose Åman
Petrolhead and all around nice guy
"Don't leave the duck there. It's totally irresponsible. Put it on the swing, it'll have much more fun." //Sleep Talkin Man Dec 23
2009
|
|
ChrisGamlin
|
posted on 31/7/07 at 09:53 PM |
|
|
The theory is sound, but considering breaking halfshafts seems to be a pastime in itself in rally circles when putting big power outputs through live
axles, Im not sure without proper analysis of each break that you could categorically say that a shaft broke on a rally car directly because of a
weld, rather than simply being stressed beyond its working limits due to the terrain or excess torque applied etc. I did do a quick google to see if I
could find any mention of Escort halfshaft failing due to welds though or for competitors recommending not to, but couldnt find anything.
Anyway, Im happy to accept the theory and will leave it to Micael to decide what he wants to do, but I will will say that Im perfectly comfortable
with my tack welded half-shafts, a mod that was recomended to me by my uncle who preps cars for Alan Mann amongst others, and considering his 40 year
racing history with live axle'd Fords he should know more than most what does and doesn't work, with these particular axles at least.
cheers
Chris
|
|
britishtrident
|
posted on 1/8/07 at 10:16 AM |
|
|
No investigation required, generally its really easy to identify a fatigue failure and pin point the the exact feature it started at.
Every failled halfshaft I have examined displayed very clearly the the classic shore line striations which start from a single point at a stress
raising feature.
With axles and torsion bars great attention has to be payed to surface finish and the detail design of fillet radi at features such as splines.
Illustration taken from this url http://www.sv.vt.edu/classes/MSE2094_NoteBook/97ClassProj/anal/kelly/fatigue.html
More here http://materials.open.ac.uk/mem/mem_ccf4.htm
 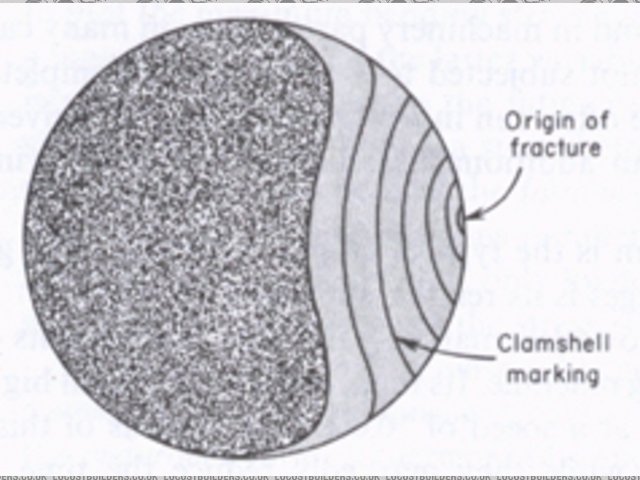 Rescued attachment img00007.jpg
[I] “ What use our work, Bennet, if we cannot care for those we love? .”
― From BBC TV/Amazon's Ripper Street.
[/I]
|
|
ChrisGamlin
|
posted on 1/8/07 at 05:32 PM |
|
|
Thinking about it though, a failure induced by a weld on the inner most edge of the retaining flange will occur inboard of the bearing, meaning it is
no different to breaking a halfshaft at any other point along its length inboard of the bearing (ie within the axle tube). Even if the halfshaft did
break at that stress raiser, the outer half of the stub axle will still be retained by the same press fit into the bearing and the retaining cap as it
was before the failure, and if it tried to twist in the bearing under the weight of the car, the drum / disc would prevent it moving out of alignment
significantly.
Its only if you create a stress point outboard of the bearing and it fails at that point will a failure likely culminate with the loss of a wheel, so
to me it seems by welding the flange on the inside the trade-off for a reduction in the chance of the driveshaft being pulled out of the bearing
causing a criitical failure is the possibility of increased inboard driveshaft failure which in 99% of circumstances is far less dangerous.
cheers
Chris
|
|
britishtrident
|
posted on 1/8/07 at 07:46 PM |
|
|
Halfshafts unmolested by welding 99.9999% of the time only fail at the splined end. This is because of the stress raising effect of the end of
splines. In days gone by this type of halfshaft failure was a very common roadside mechanical failure until about 1960 when manufacturers got wise to
reducing the stress concentrations by under cutting the end of the splines with very a generous radius, if you examine an Escort Engish axle you will
see the designer has taken great care to do this.
The surface layer of halfshafts and torsion bars must be defect free or they will fail apart from the stress raiser effects of the weld halfshafts are
normally made from a molybenium alloy steel contain significant % of nickle, manganese and chromium, not that different from the sort of grade of
steel used to make spanners.
Tack weld the with a MIG welder and a mild steel filler rod and it is anybodies guess what the hardness and compostion of the heat affected zone will
be but it is a safe bet will at some point be brittle because of the rapid cooling caused by the the heat sink effect of of the material thickness
and the small size of the weld.
|
|
ChrisGamlin
|
posted on 1/8/07 at 10:48 PM |
|
|
As mentioned previously Im happy to take what you say about the meallurgy as read, but from my point of view in the real world many many race and
rally cars have had this mod done over the last 40 years, if it was as dangerous and as likely to lead to failure as you seem to be suggesting then it
simply would not still be done today (by the very same people that did it 40 years ago no less), so I can only assume that although yes maybe it does
add a potential stress raiser, on an Escort halfshaft this is not sufficient to cause failure in all but the most extreme of circumstances, and as I
mentioned even if it did fail Im not convinced it would be any worse than a failure at the splines which as you mention, is/was much more common and
doesn't usually cause any catastrophic loss of running gear.
cheers
Chris
|
|