Puk
|
posted on 9/1/08 at 10:10 AM |
|
|
I agree with Cymtriks, to take advantage of aluminium's properties would mean abandoning the space frame and replacing it with a monocoque.
Employ a couple of deep sides planks running from the front suspension pickups to the rear and tie the planks too each other with transverse bulkheads
between the front wheels, behind the engine and behind the seat backs.
What you'd end up with is a wider version of this:
Check later post for the picture - teething problems :-(
But would it be lighter - can't promise that.
Would it be cheaper - well probably. If you cost in the hours spent cutting and welding tubes into a space frame and compare tht to the cost of buying
a composite panel that has been CAD routed to shape then I'll bet the composite solution come sout cheaper. I did the cost analysis on the car
above and it was cheaper than a Formula Ford car.
What about the bonding - this is the weak spot. To date creating structural bonds has been difficult but since Jaguar started gluing pieces of
aluminum together to make XKs and XJs things have moved on. These cars are built on a production line, so the adhesives used must tolerate a less
clinically clean environment than aircraft and race car chassis are built in. Plus there must be solutions for making repairs to crash damaged cars
outside of the Jag factory. If there weren't then the insurance companies would have charged exorbitant premiums, and you can trust Ford to have
consulted with them before launching the XJ.
The composite aluminium monocoque has one card left to play - they absorb impacts progressively. A space frame is very stiff whilst all of its members
are still straight - but once one member gets buckled the whole thing becomes greatly weakened. That Formula Lotus chassis in the picture had a
terrific reputation for protecting its drivers in a crash. The composite 7 built in Oz
(PRB) had a similar reputation.
Right I'll get off my soap box and get on the phone to Jaguar to see if I can cadge a pot of glue of them.
[Edited on 9/1/08 by Puk]
[Edited on 9/1/08 by Puk]
Before you judge a guy, walk a mile in his shoes. Then when you judge him, you're a mile a way and you've nicked his shoes.
|
|
|
02GF74
|
posted on 9/1/08 at 11:07 AM |
|
|
quote: Originally posted by cymtriks
An aluminium space frame is never going to be as good as a steel one.
To be as stiff it will need to be made of tubes with three times the cross section of a steel tube. The aluminium has a density about three times less
than steel so you end up back where you started.
without looking up the specs. I seem to recall that the strength (I usethe work in the most non technical sense) was 1/2 but density as you say is 1/3
so to get the same as steel, there is still a weight savving.
Otherwsie why use aluminium on aircraft? It would be more bulky for the smae strength as steel.
re: the RC chassis photo - that really is aluminium???!?!? would make sense as I think it would be hard to lift the chassis above your head if it
were steel.
|
|
Doug68
|
posted on 9/1/08 at 12:42 PM |
|
|
Here's a Titanium aircraft...
Here's a Stainless Steel one...
Here's one that mostly plywood...
The point is that these structures are Engineered to make best use of the chosen construction material.
Doug. 1TG
Sports Car Builders WA
|
|
Puk
|
posted on 9/1/08 at 05:26 PM |
|
|
This is a picture of the Formula Lotus chassis - basically two composite aluminium planks tied together by transvers bulkheads. It was a simple and
cheap car that was strong in a crash:
 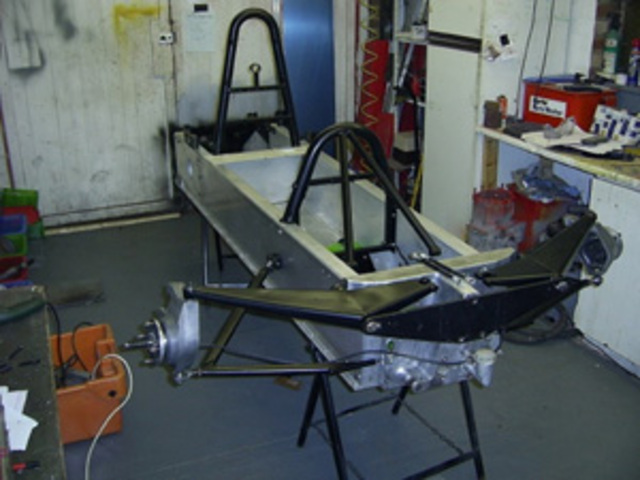 Rescued attachment FormulaeGMLotus300.jpg
Before you judge a guy, walk a mile in his shoes. Then when you judge him, you're a mile a way and you've nicked his shoes.
|
|
scootz
|
posted on 9/1/08 at 09:04 PM |
|
|
That's my chassis! Had a wee surprise moment until I remembered that I sent you a picture of it...
PS - Wasn't that cheap... still cost just under £20k back in the late 80's!
[Edited on 9/1/08 by scootz]
|
|
Puk
|
posted on 9/1/08 at 09:19 PM |
|
|
That what they sold for, believe me they didn't cost that much to make! But that is why Adrian Reynard used to arrive for work in a helicopter
:-)
[Edited on 9/1/08 by Puk]
Before you judge a guy, walk a mile in his shoes. Then when you judge him, you're a mile a way and you've nicked his shoes.
|
|
scootz
|
posted on 9/1/08 at 09:30 PM |
|
|
Very helpful chap is Mr Reynard - I made an enquiry about the chassis design on his business website and I got a reply directly back from him... not
often that happens!
|
|
flak monkey
|
posted on 9/1/08 at 09:35 PM |
|
|
quote: Originally posted by 02GF74
quote: Originally posted by cymtriks
An aluminium space frame is never going to be as good as a steel one.
To be as stiff it will need to be made of tubes with three times the cross section of a steel tube. The aluminium has a density about three times less
than steel so you end up back where you started.
without looking up the specs. I seem to recall that the strength (I usethe work in the most non technical sense) was 1/2 but density as you say is 1/3
so to get the same as steel, there is still a weight savving.
I wasnt going to post, but I can't resist tempatation.
Stiffness, not strength they are very different things, as I am sure I and other have mentioned many times. Ali is 3 times less stif than steel. So to
get the stiffness back you effectively need to use 3 times as much material in the construction of the frame.
The best way to achieve this is through the use of much larger tubes, e.g. 75x75mm.
It is possible to make a chassis from aluminium, and one that works very well (just look at the lotus elise) BUT you have to design for the specific
properties of the material. Spaceframe chassis do not lend themselves to construction with aluminium as they tend to use lots of small tubes to spread
the load. The better option for an aluminium frame is either a monocoque or a beam chassis (a la elise) to take full advantage of the massive
stiffness gains through using much larger second moment of area (moment of intertia) sections without the weight penalty.
A direct aluminium copy of the locost chassis will be abismally floppy and at a guess wouldnt last 1000 miles of road use before it started falling
apart at the seams (literally).
Any strutural welded aluminium construction needs to really be heat treated (both stress relieved and age hardened) to avoid the potential of fatigue
cracking. Some of the best strength aluminium alloys are not weldable (not impossible, but very difficult!) as they just crack on cooling. IIRC its
the 5 and 7 series ones, the ones that strength wise are equivalent to a good alloy steel which is another major drawback. but what they do lend
themselves to is bonded constructions or monocoques!
I didnt write a thesis on aluminium chassis for my 3rd year uni project, honest...
David
Sera
http://www.motosera.com
|
|
scootz
|
posted on 9/1/08 at 09:38 PM |
|
|
Right - that's ali dealt with...
So what would be the optimal material to use for a lightweight spaceframe assuming money was no object... titanium?
|
|
flak monkey
|
posted on 9/1/08 at 09:41 PM |
|
|
quote: Originally posted by scootz
Right - that's ali dealt with...
So what would be the optimal material to use for a lightweight spaceframe assuming money was no object... titanium?
Have you tried welding that stuff?
The ultimate chassis material if money is no object is carbon fibre, in a monocoque construction.
IMO for proper spaceframes, for stiffness to weight, you'll have a hard job beating old fashioned steel.
Sera
http://www.motosera.com
|
|
scootz
|
posted on 9/1/08 at 09:58 PM |
|
|
No
Bit of a PITA is it?
That aside... I understand that Titanium is both stronger and lighter than steel.
|
|
flak monkey
|
posted on 9/1/08 at 10:04 PM |
|
|
quote: Originally posted by scootz
No
Bit of a PITA is it?
That aside... I understand that Titanium is both stronger and lighter than steel.
Titanium is a pig to weld, not impossible, but a pain. I shant type it out, I'll just let you read this:
http://www.twi.co.uk/j32k/protected/band_3/jk24.html
The UTS of unobtanium is about the same as steel, but its 45% lighter. So strength to weight its much better than mild steel.
Stiffness wise its a little bit less than steel (116GPa compared to about 121GPa), but again, for the weight its much better than steel.
David
Sera
http://www.motosera.com
|
|
scootz
|
posted on 9/1/08 at 10:07 PM |
|
|
David... step away from the books and go to the pub - you need to get out more! 
|
|
flak monkey
|
posted on 9/1/08 at 10:10 PM |
|
|
quote: Originally posted by scootz
David... step away from the books and go to the pub - you need to get out more!
You aint wrong Engineering geek and proud of it.
Sera
http://www.motosera.com
|
|
907
|
posted on 9/1/08 at 10:22 PM |
|
|
Actually titanium is gorgeous to weld. It flows like a dream.
The problem is keeping out the oxygen from the surrounding air. Ideally the weld should stay silver, straw is OK, but blue is a no no.
I've used all sorts of masking techniques and followers on the torch and it therefore is very time consuming.
I have done shapes that have had 6 argon lines running at once.
Paul G
|
|
scotmac
|
posted on 10/1/08 at 06:34 AM |
|
|
quote: Originally posted by gazza285
quote: Originally posted by iank
what's not carbon is titanium
Ask him why the Tour De France boys still use steel frames then......
Steel alloys I know before anybody calls me, but still more iron than anything else.
A good many of the tour bikes are carbon and titanium. eg, remember that Lance Armstrong was sponsored by Trek...All Carbon All the Time!
|
|
scootz
|
posted on 10/1/08 at 09:23 AM |
|
|
So... if you were to make a Ti space-frame would it be safe to assume that the Ti tube thickness could be the same, or slightly thinner even, than
that used on an identically proportioned steel-chassis car?
|
|
Benonymous
|
posted on 10/1/08 at 10:58 AM |
|
|
Ti...PFFFFT
Nice academic conversation. Ti is a superb material but completely impractical for a 'low-cost' home made clubman. when the subject of
light weight and lightening comes up I always remember a lovely story I heard once. The story concerns a guy involved in production motorcycle racing
in the late 70's. It was the era of the Kwakka 1000 and other behemoths. The racer had drilled holes in everything that looked like it could
use less weight. This activity culminated in the heavily drilled gear lever snapping off mid-race. The dejected rider was sitting in the pit feeling
sorry for imself when an old guy, who'd been racing for years, stopped by to lend a sympathetic ear. He scanned the machine and offered this
advice, "instead of drilling holes in everything to lose some weight, take my advice, just have a big sh!t before the race"
|
|
scootz
|
posted on 10/1/08 at 12:41 PM |
|
|
Well aware that no-one's going to spunk out the thousands required to get the necessary Ti materials, but hypothetically speaking...
|
|
britishtrident
|
posted on 10/1/08 at 01:46 PM |
|
|
I would say a GRP composite monocoque with some Kevlar and CF reinforcement would be a good option but trying to get it through SVA would be fun,
and I don't think it would be lighter than a spaceframe.
[I] “ What use our work, Bennet, if we cannot care for those we love? .”
― From BBC TV/Amazon's Ripper Street.
[/I]
|
|
Doug68
|
posted on 10/1/08 at 02:08 PM |
|
|
Mean while back in the real world Ducati won the Moto GP world championship using a steel tube frame.
And I think their budget would stretch to whatever material they felt like.
This isn't a GP7 but their WSB which is close enough in its frame deign to get the idea...
[Edited on 10/1/08 by Doug68]
Doug. 1TG
Sports Car Builders WA
|
|
crafty
|
posted on 11/1/08 at 01:50 AM |
|
|
quote: Originally posted by britishtrident
I would say a GRP composite monocoque with some Kevlar and CF reinforcement would be a good option but trying to get it through SVA would be fun,
and I don't think it would be lighter than a spaceframe.
Your profile pic reminded me of this
Ultima GTR - 600hp Magnacharged LS2
MNR Vortx - Supercharged R1
Porsche 356 - midmounted Audi V8
|
|
Delinquent
|
posted on 11/1/08 at 11:46 AM |
|
|
quote: Originally posted by britishtrident
I would say a GRP composite monocoque with some Kevlar and CF reinforcement would be a good option but trying to get it through SVA would be fun,
and I don't think it would be lighter than a spaceframe.
I've been having some fairly extended chats with the SVA chaps about this - and it might ... might not be as bad as it seems.
I've been given loads of tips from both the VOSA people and local SVA chap. The main outcome of the discussions is to show other cars that have
used very similar layup construction and been through the SVA without problems - i.e. GTM, or for more up to date Murtaya. Couple that with a full
photo build of the layups as proof... I've been told it "shouldn't be a problem" (yeah right...)
My current spare time is spent trying to get detailed info from current manufacturers regarding their layup techniques and materials... which is not
exactly simple, however if I DO ever get it built, and SVA'd, I would of course be more than happy to give detailed info on my own layup to
anyone that wanted a go at it.
BTW - re the Tour bikes, there are as many different materials and constructions as there are riders. My brother does the mountain stages when time
allows - last year he went steel frame with everything else carbon or titanium. Unfortunately the chap building it for him cocked up one of the
measurements at the fitting session so don't think that bike will be used again!
|
|
Peteff
|
posted on 11/1/08 at 12:05 PM |
|
|
Mean while back in the real world Ducati won the Moto GP world championship using a steel tube frame.
Not 16g mild steel though, and the engine is the main stress bearing member with the frame bolted to it to hang the steering and seat on. If they used
aluminium it would need to be bigger section and make access awkward. Different designs need different materials as already put forward.
yours, Pete
I went into the RSPCA office the other day. It was so small you could hardly swing a cat in there.
|
|
Puk
|
posted on 11/1/08 at 12:21 PM |
|
|
Its been stated several time that different design objectives need different solutions. So what do folk feel are the objectives of a 7esqu frame?
Being light is probably the one that drives the suggestion to try aluminium, but there must be others too. How about, and in no particular order of
importance:
Light weight.
Easy for a novice to build without any high level of expertise - and get right first time.
Good ratio of stiffness to weight.
Acceptable to SVA/VOSA (or who ever the grown ups are in your part of the world)
Materials readily available.
Able to withstand temperate climate (and road salt ?).
Already proven fabrication technique.
Already proven chassis design.
Every now and then people talk about crash worthiness, but we always seem to come back to 'its safer than my motorbike' or 'its an
acceptable fun/risk compromise'.
Anything else, anything to remove?
Before you judge a guy, walk a mile in his shoes. Then when you judge him, you're a mile a way and you've nicked his shoes.
|
|