chrsgrain
|
posted on 27/12/12 at 06:24 PM |
|
|
Lathe help needed - beer tokens waiting!
Hi all,
I was hoping someone could help - I need to have the bit that holds discs onto a grinder reduced in thickness so my shrinking disc can't hit
anything it shouldn't..... a picture is worth a thousand words, this should make things clearer...
 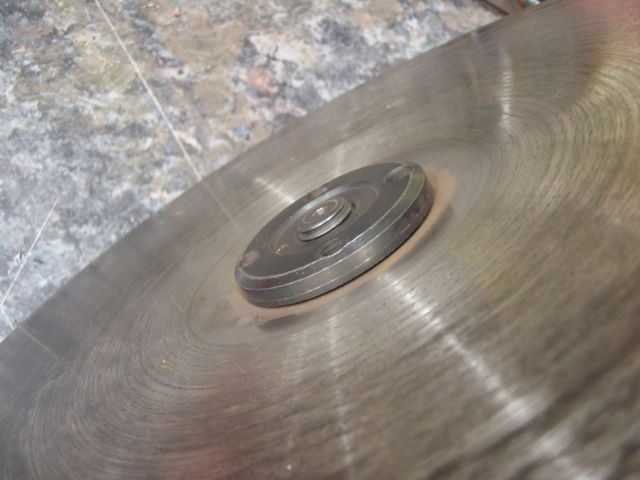 Description
 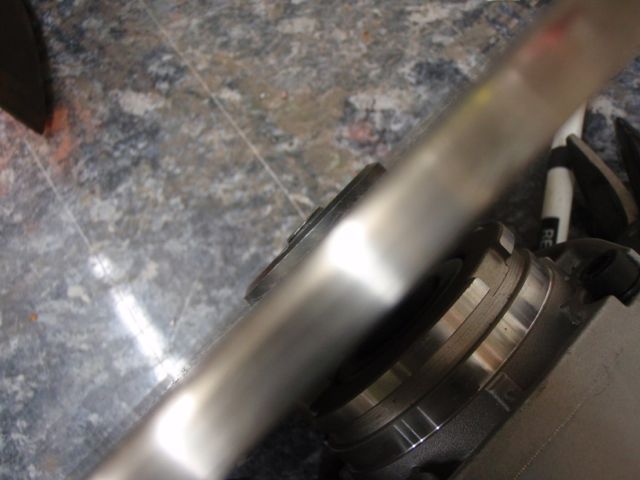 Description
See how it pokes out above the plane of the disc - that means it can hit on bits of bodywork which is obviously bad! What I'd like is it turned
down so that it lies at least level with the plane of the disc, if not a tiny bit below. The plane of the disc isn't flat, its slightly inclined
into the centre, so the attaching disc could do with following that plane, or kept entirely below it - if that makes sense! Another picture may
help... Although it doesn't look like it in the picture, there will be enough metal left, especially as there is very little force through the
disc when its used.
 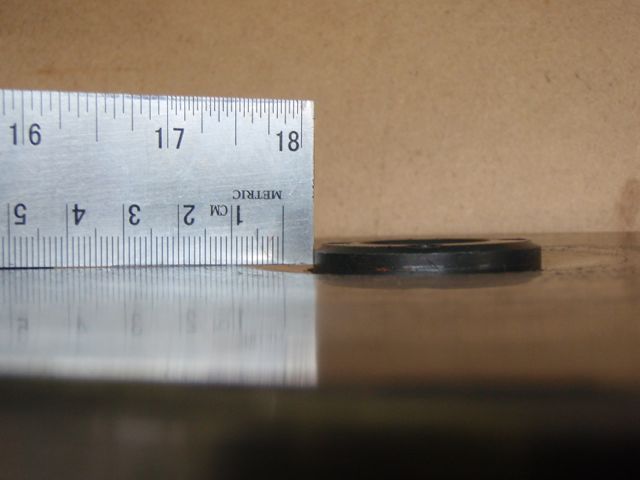 Description
If anyone is wondering what its for, its for accurately shrinking metal, which helps turn this hole....
 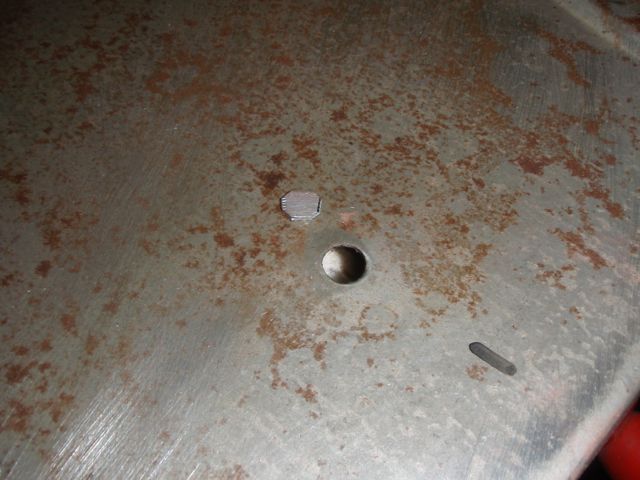 Description
via this....
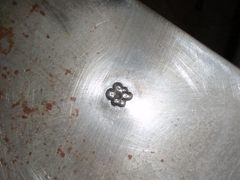 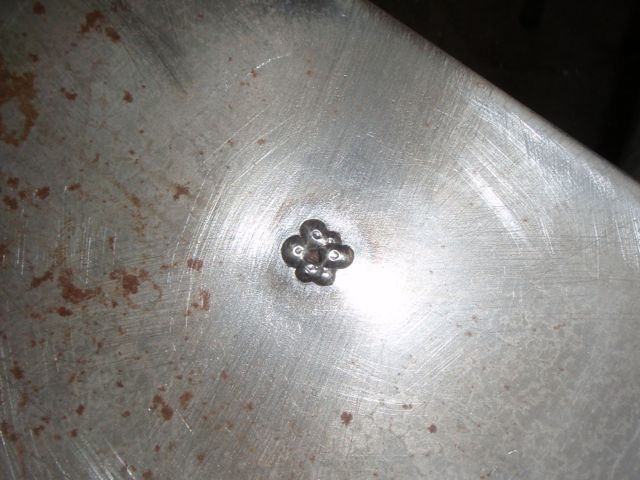 Description
into this... (the dark lines are bits of guidecoat stuck in the grooves from the body file)
 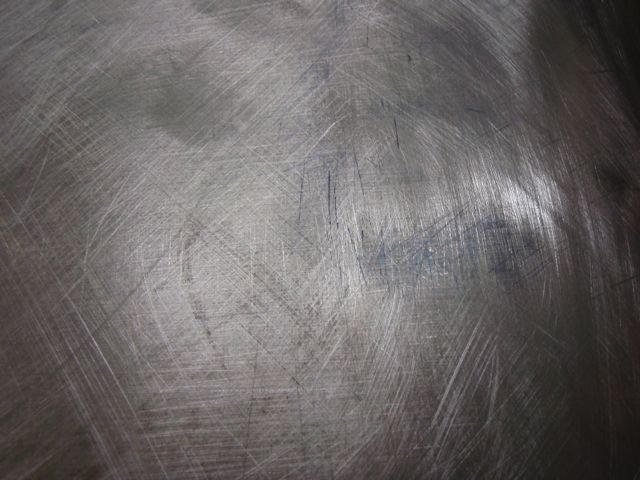 Description
Here's hoping someone can help! Cheers
Chris
Spoing! - the sound of an irony meter breaking...
|
|
|
ReMan
|
posted on 27/12/12 at 07:49 PM |
|
|
Sorry cant help, but thats not natural.
More witchcraft!
www.plusnine.co.uk
|
|
theprisioner
|
posted on 27/12/12 at 08:35 PM |
|
|
I have done exactly the same thing to my 115mm grinder for exactly the same reason. Unfortunately I am at the opposite end of the country from you. I
will send you U2U and you can pop it in the post to me if you want.
|
|
Fred W B
|
posted on 28/12/12 at 07:38 AM |
|
|
if you only want to take material off the outside why not just spin it up with a spacer underneath in the place of the disc and apply a flap disc on
another grinder to the surface?
Cheers
Fred W B
[Edited on 28/12/12 by Fred W B]
You can do it quickly. You can do it cheap. You can do it right. – Pick any two.
|
|
Peteff
|
posted on 28/12/12 at 09:23 AM |
|
|
quote: Originally posted by Fred W B
if you only want to take material off the outside why not just spin it up with a spacer underneath in the place of the disc and apply a flap disc on
another grinder to the surface?
Cheers
Fred W B
I've used the same method with the part held on a bolt or old spindle in the pillar drill chuck and to shape the backs of inlet valves as well.
yours, Pete
I went into the RSPCA office the other day. It was so small you could hardly swing a cat in there.
|
|
907
|
posted on 28/12/12 at 10:10 AM |
|
|
Could you form a depressed centre into the shrinking disc?
From your pics it looks as if it's slightly depressed already, and retaining more threads
in the nut would be safer.
If you do "thin" the nut you will also need to shorten the male spindle, or use a spacer.
Cheers,
Paul G
|
|
rf900rush
|
posted on 28/12/12 at 10:50 AM |
|
|
Hi
If you do not find any one closer, I am in Epsom Surrey, With a small ish lathe, willing to help.
Could also make a spacer for he back if required.
Martin
|
|
chrsgrain
|
posted on 29/12/12 at 01:11 PM |
|
|
Thanks guys for all the suggestions... I think I'll take Martin up on his offer of thinning the part and making the spacer!
Cheers all...
Chris
Spoing! - the sound of an irony meter breaking...
|
|
rf900rush
|
posted on 29/12/12 at 10:11 PM |
|
|
U2U sent
Sadly the Dax Was sold this year.
New project under way but for the kids this time
Just sent to the Painter.
Fortunately I have a brother who Beats Panels and paints, and is now the favorite Uncle.
Primer
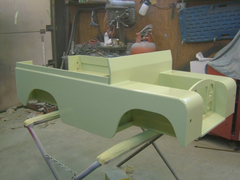 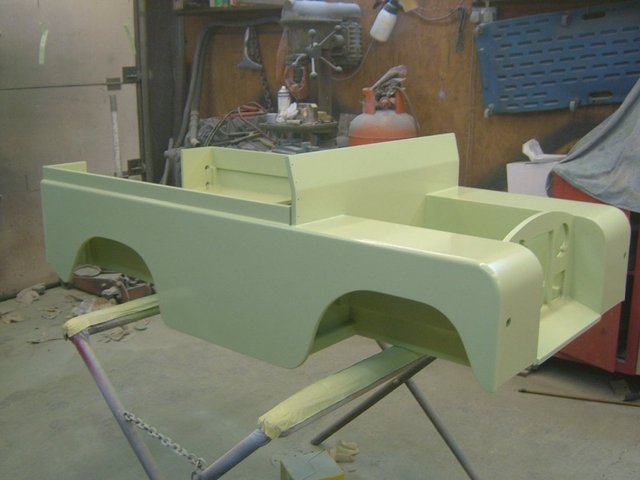 Body Primer
Top coat
 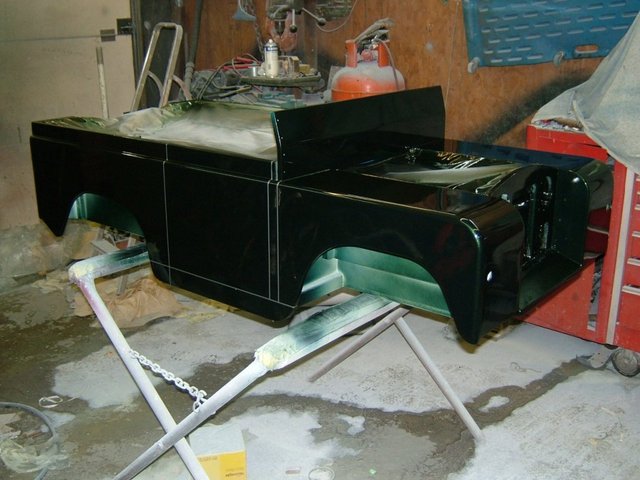 Body Top coat
|
|
r1_pete
|
posted on 30/12/12 at 12:36 PM |
|
|
Will this do? was in the workshop doing some work on the lathe and remembered your post.
Its an M14 thread, and about 1.5mm thick now, 4mm in the raused centre section....
 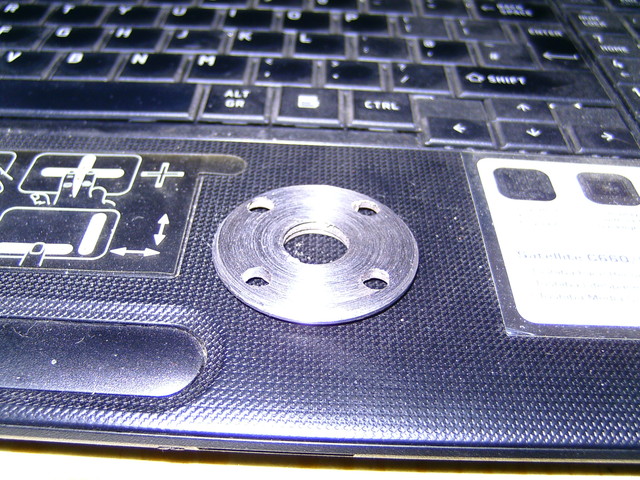 Description
|
|