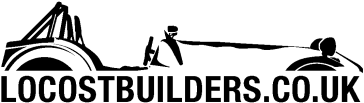
Inboard disks on a transaxle?
tegwin - 5/1/08 at 10:56 PM
In my mission to make things as complicated as possible, the thought of fitting inboard rear disks came up...
Im planning to use a transaxle though so this confuses things more...
Given the fact that the engine/transaxle will be floating around the back of the car on rubber mounts, is it even possible to fit inboard disks?
I assume you would have to mount your callipers on the transaxle its self, so would therefore have to assume that it can handle the forces put though
it...
Is it practical/safe to consider doing this?
Do the gains in reduced unsprung weight outweigh the inconvinence and issues caused by the inboard system...
Anyone have any nuggets of helpfull information to confuse me more?
pictures of it being done...
[Edited on 5/1/08 by tegwin]
Simon - 5/1/08 at 11:06 PM
While the whole engine/transaxle assemblies may may floating on rubber bushes, the discs form part of the driveshafts as they would in any
configuration of diff/trans or live axle and the calipers are indeed solidly mounted to the transaxle, it doesn't matter whether they are
attached to the hub/upright, or gearbox, so long as what they are mounted to, is strong enough to stop them sp[inning when brakes are applied.
Alfa did it with the alfasud (as one example of transaxle) and the old Jag IRS's had inboard brakes.
ATB
Simon
iank - 5/1/08 at 11:25 PM
Alfasud did it that way (as did a number of cars over the years on the diff Jaguars being the one I remember
http://en.wikipedia.org/wiki/Inboard_brake)
There are alfasud manuals on the net (here http://alfasprint.extra.hu/) but I've not looked to see if they have usable pictures.
Problems with inboard brakes (IIRC) include keeping them cool (some ducting will probably be required) and general awkwardness of maintenance.
Think most transaxles should be strong enough (calipers bolted via aluminium adaptors seem to be safe enough on hubs so the forces can't be huge)
assuming you can find something close to mount them on. Mounting the disk may be harder depending on the driveshaft arrangements.
Personally I doubt it's worth the extra hassle and lighter wheels will be an easier/cheaper option unless you are going for the ultimate.
[Edited on 5/1/08 by iank]
CGILL - 6/1/08 at 05:08 AM
As mentioned, if you can keep them cool, it's a great idea, not only removing unsprung weight, but removing torque reaction from braking from the
suspension, which normally can create lift or downforce through the links.
rpmagazine - 6/1/08 at 05:18 AM
errr...there is no lift/downforce from braking loads.
CGILL - 6/1/08 at 06:19 AM
Urm... yes.... the torque reaction on the trailing links, if the brakes are hub mounted and applied, the hub will attempt to twist in the same
direction as the wheel, depending on the angles of the links at the time, this can cause the rear to lift or drop, so if the upper link was higher at
the hub than the chassis and travel forward, the twisting action from the brake force on the hub would try to make the top link closer, which would
create a lifting force in the rear because to be in a closer position the link would have to travel in an arc downwards at the hub end. This is mainly
on multi-link or dedion setups and not really double wishbone. If the brakes are inboard, the force is removed from the hub and is transfered to the
transaxle wanting to cause the front end trans to dip.
Johnmor - 6/1/08 at 07:18 AM
HI
The pic you have is of an Alfa 75 trans axle that also incorperates the clutch at the rear. The sud was differant with front wheel drive and the
engine in front of the drive wheels. So it would be a challenge in a rear wheel drive car
I think its going to make your seating position very high to clear the transaxle but you can build that into your design.
The brakes inboard are a great idea and I dont think cooling will be an issue as the rear brakes do only around 30% of the effective braking at
speed.
Sud box
Good luck

tegwin - 6/1/08 at 09:22 AM
Thanks for your input guys.
I have two worries:
1. Will the engine/gearbox flexi mounts handle the twisting forces put upon them under braking? (Having said that, the twisting force under braking
cant be any more than the twisting force under heavy acceleration...its just in a different direction...
2. Will the driveshafts be able to handle the extra load on them caused by fitting the brakes inboard?
rpmagazine - 6/1/08 at 09:36 AM
quote:
Originally posted by CGILL
Urm... yes.... the torque reaction on the trailing links, if the brakes are hub mounted and applied, the hub will attempt to twist in the same
direction as the wheel, depending on the angles of the links at the time, this can cause the rear to lift or drop, so if the upper link was higher at
the hub than the chassis and travel forward, the twisting action from the brake force on the hub would try to make the top link closer, which would
create a lifting force in the rear because to be in a closer position the link would have to travel in an arc downwards at the hub end. This is mainly
on multi-link or dedion setups and not really double wishbone. If the brakes are inboard, the force is removed from the hub and is transfered to the
transaxle wanting to cause the front end trans to dip.
The Mark Ortiz Automotive
CHASSIS NEWSLETTER
EFFECT OF CALIPER MOUNTING POSITION
What effect on wheel loading does the positioning of the calipers in a leading or trailing location have i.e. mounted at 3 and 9 o clock positions?
Does a trailing caliper add or subtract load on the front tires? In a rear independent suspension, does a leading caliper add or subtract wheel
loading, and is it the same in a live axle situation?
The short answer is no. Caliper location has no effect whatsoever on wheel loading. Having the caliper s mass lower or higher does have a very minute
effect, because it affects the CG location a tiny bit, but there is no difference between a 3 o clock mounting position and a 9 o clock position.
However, there is an effect on bearing loads. It might seem counterintuitive that we can change the bearing loads and not change the tire loads, but
that is in fact the case. As the questioner appears to have considered, the disc tries to carry the caliper upward if the caliper is trailing, and
downward if the caliper is leading. That reduces bearing loads if the caliper is trailing, and increases bearing loads if the caliper is leading.
However, these forces are reacted entirely within the hub/bearing/spindle/upright/caliper/disc/hat assembly, and do not change the loads on other
parts of the car.
We can think of it like this: Gravity acts downward on the car, with additions and subtractions due to inertia effects and aerodynamic effects. The
road surface holds the car up. Or, we may say the road holds the tire up; the tire holds the wheel up; the wheel holds the hub up; the hub holds the
bearings up; the bearings hold the spindle up; the spindle holds the upright up; the upright holds the suspension up; the suspension holds the sprung
mass up. If the caliper exerts an upward force on the upright and a downward force on the disc, that just means the brake is helping the bearings and
spindle hold the upright up. It doesn t change the total support force, only the load path within some of the unsprung components.
It is worth noting that in braking there are also horizontal forces acting through the wheel bearings. The car is trying to keep going forward at a
constant speed. The road surface is exerting a rearward force on the car, through the tires, wheels, hubs, bearings, spindles, uprights, and
suspension. We can reduce the bearing loads due to this component if we mount the caliper below center, or increase the bearing loads if we mount the
caliper above center. In fact, the horizontal force may be greater than the vertical force on the tire. With racing slicks on dry pavement, the
horizontal force may be 1.3 or more times as great as the vertical load on the tire. So for least bearing loads during braking, the caliper should be
somewhere in the upper rear quadrant around 5 o clock or 7 o clock, depending
on which wheel we re looking at, and from what direction.
Now, do we actually want maximum cancellation of the bearing loads by the brakes? We might suppose so, but actually there is an argument for not
having maximum cancellation. The effective radius of the brake (roughly the radius to the middle of the pad) is often less than half of the tire
effective radius. This means that the force at the caliper is more than twice the rearward force at the tire contact patch, and it may also exceed the
vector sum of the vertical and horizontal forces at the contact patch. Consequently, the caliper force may not only reduce the bearing loads, but
reverse
them. If there is any free play in the bearings, or deflection in the components, this load reversal may result in a vibration or a small variation in
the steer angle of the wheel. So there is a case for building the components nice and strong, and positioning the calipers so the bearing loads will
not reverse.
Of course, as a practical matter, if we are using purchased calipers we need to mount them with the bleed screws at the top, or very nearly so, just
to facilitate good brake bleeding without requiring the calipers to be dismounted. This may well outweigh any theoretical considerations. If we are
designing from a blank sheet of paper, we don t face this constraint, but most of us, most of the time, are designing around purchased calipers.
Another practical constraint is packaging, particularly of the steering arms and cooling ducts.
There are some ways in which we can affect wheel loads by the design of the brake system and the suspension. I am referring here to the longitudinal
anti or pro effects: anti-dive or pro-dive in the front suspension, anti-lift or pro-lift at the rear. With independent suspension, it makes a
difference to these effects whether the brakes are inboard or outboard. With a beam axle, it makes a difference if the calipers are mounted directly
to the axle, or on birdcages or floaters that rotate on the axle and have their own linkages.
However, with all of these, we cannot significantly alter the loading on the front or rear wheel pair, nor on all four wheels. We can change the way
the sprung mass moves in response to braking, and this may have small effects on CG height, with corresponding small effects on overall load
transfer.
But the big effects come from having geometry differences on the right and left sides of the car. These may be present even in supposedly symmetrical
road racing cars, because no car stays symmetrical when it rolls. In oval track cars, we often design in, or adjust in, asymmetry even in the static
condition. Such asymmetry can produce significant changes in diagonal percentage when braking, and we can use these to tune corner entry behavior.
All such effects are independent of the clock position of the caliper mount.
nitram38 - 6/1/08 at 10:07 AM
One of the big considerations is the extra stress put on your driveshaft joints as you will be using them to slow the wheels down.
I would personally keep my discs out board, especially if they are rears as they are small and light anyway.
andygtt - 6/1/08 at 10:32 AM
Am I not right in thinking that the loads will remain unchanged by the possition of the brakes?.... as the twisting loads are generated by the tyre
gripping when braking and the chassis still wanting to move!
the big win is with unsprung weight reduction, but the trade off is cooling issues.
froggy - 6/1/08 at 12:05 PM
i run inboard discs on the back of my kitten which are 10" and have no issues with them at all
Doug68 - 6/1/08 at 01:00 PM
2CV's had inboard drums or discs at the front, I think this was a common Citroen thing in their 'funky' era.
I also remember seeing a TVR with this also.
One thing to do might be to mount the calipers on a floating mount where the torque load from them can taken directly into the frame rather than
through the transmission case.
Some motorcycles have a similar arrangement for their rear brake, but thats for different treasons.
gazza285 - 6/1/08 at 01:00 PM
quote:
Originally posted by iank
Alfasud did it that way
Took about five hours to change the brake pads, and the windup in the drive shafts when you put the brakes on hard was scary.
iank - 6/1/08 at 01:25 PM
quote:
Originally posted by gazza285
quote:
Originally posted by iank
Alfasud did it that way
Took about five hours to change the brake pads, and the windup in the drive shafts when you put the brakes on hard was scary.
Does that count as better or worse than " general awkwardness of maintenance"?
I know the Alfa 33 reverted to outboard discs.
Jag rear pads are also a pig to change I understand.
CGILL - 12/1/08 at 08:05 AM
quote:
Originally posted by andygtt
Am I not right in thinking that the loads will remain unchanged by the possition of the brakes?.... as the twisting loads are generated by the tyre
gripping when braking and the chassis still wanting to move!
There is a twisting force generated at the hub. The previous document was debating the caliper being mounted forward or aft of the hub center line.
The braking affect itself does not cause a rise or drop in the suspension, but the twisting effect acting on the geometry of the arms causes this.
This can be demonstrated by jacking up the rear of something with a trailing arm, say a sierra, applying the handbrake and applying a tyre lever in
the attempt to turn the wheel, turning in the forward direction will cause the wheel to lift, turning the reverse direction causes the wheel to drop,
this is because of the rotational force at the hub acting on the geometry, regardless of which side of the wheel you are standing with the bar.
This is why leading arm suspension in the rear would be arse
Parallel arms help more than a single arm, but is the arm lengths are not equal then this will cause more movement.
Now with the same setup and vehicle in gear and opposite wheel locked with handbrake off, this is similar in effect to an inboard brake as the locking
is done at the diff, the rotational force at the hub is pretty much removed, apart from direct upward or downward movement applied from lever, the
changes to lift or droop in the suspension are minimal.
The lift or dropping force generated is not directly from braking, but from the rotational force on the hub acting on the geometry, this can be pretty
much dialed out depending on your choice of suspension setup.
The same advantages as a dedion over a live axle really, live axle tries to turn in opposite direction of wheel rotation, this acts on arms, dedion
removed these forces from acting on geometry as forces are now through the frame where the diff carrier is mounted.
A model would demonstrate
[Edited on 12/1/08 by CGILL]
MrFluffy - 25/1/08 at 08:16 AM
Theres also another classic example of inboard discs, the lotus esprit s1 and s2's, as they used the mazzerati/peugeot sm transaxle. Lotus went
to outboard discs on the S3 and later series because they changed to the Renault UN1 transaxle and redesigned the rear of the chassis to have seperate
upper links and mounted the brakes outboard in a more conventional manner.
There were durability issues with the citroen transaxle but this I think was mainly due to using the driveshaft as a upper wishbone link rather than
pushing braking force through the uj's...
austin man - 7/4/08 at 10:39 PM
just seen an article in a kit car magazine, a chap has done the inboard discs usin the Sierra diff and having the discs drilled and mounted to the
drve flanges and then mounting brackets made for the callipers. State a masive improvement in unsprung weight
Bart Vangampelaere - 9/4/08 at 10:35 AM
inboard brakes improve unsprung wheight, so it's a good thing. And changing brake pads on my NSU Ro80 isn't hard at all. It's very
simple: nothing hard at all. Just pulling out two pins, and lifting the pads out.