Matthew_1
|
posted on 19/2/04 at 07:21 PM |
|
|
I sent them a drawing in .dxf format from Autocad. They produced the parts straight from that. But when I asked they said they would have been happy
with faxed through drawings.
|
|
|
dozracing
|
posted on 20/2/04 at 12:06 AM |
|
|
If you are after hub flanges from which to make rear uprights, then i can sell the flanges we use on our irs uprights and de dion kit. Pic attached.
Email off list darren@gtstuning.co.uk
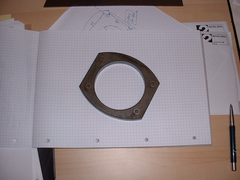 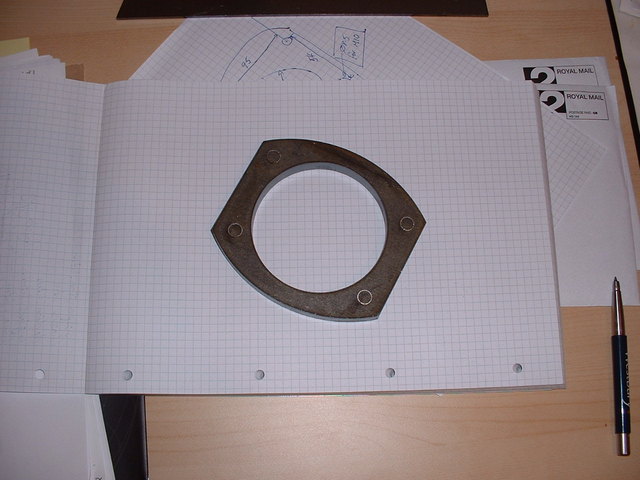 Rescued attachment DSCF0186.JPG
|
PLEASE NOTE: This user is a trader who has not signed up for the LocostBuilders registration scheme. If this post is advertising a commercial product or service, please report it by clicking here.
|
Rob Allison
|
posted on 20/2/04 at 03:26 AM |
|
|
A little bit off topic but, i'll be after one of your axles soon. how easy is the kit form to weld up.

|
|
James
|
posted on 20/2/04 at 10:19 AM |
|
|
quote: Originally posted by Alan B
Aha...you see I didn't say they didn't (because I don't know)....just that I thought that wire cut gears would be in the
minority..IMO...if more than 50% of F1 gears are wire cut then I'll hold up my hand....
<begin excuses> As I say though we all learn all the time and if I'm wrong (entirely possible) then I will have learned my new thing for
the day...and after all it is 10 years since I designed my last gear.....<end excuses>
    
Ah well, if your going to go and qualify your statements what hope do I have!
Pity though... I fancied 50 quid!
You're right in that certainly less than 50% of F1 teams wire cut the gears- the only one I know of is Mclaren. I didn't want to say
before as I wasn't sure if it was a company secret- but I checked with the boss last night and it's published apparently.
Cheers,
James
|
|
philgregson
|
posted on 20/2/04 at 12:50 PM |
|
|
OK then - another car application (F1 again):
Benneton apperently used wire cut titanium hubs/carriers/uprights or something - I didn't know this but read it off a web site (can't
remember which one).
Phil
|
|
dozracing
|
posted on 20/2/04 at 01:56 PM |
|
|
Pretty much every F1 car had wire cut titanium uprights. Now more and more are using investment cast tianium instead.
Kind regards,
Darren
|
PLEASE NOTE: This user is a trader who has not signed up for the LocostBuilders registration scheme. If this post is advertising a commercial product or service, please report it by clicking here.
|
Alan B
|
posted on 20/2/04 at 02:37 PM |
|
|
It's good to hear about these applications for wire EDM.....when I was involved maybe15 years ago production jobs were very rare....some wear
pieces cut from solid carbide blanks for an aircraft part is an example that springs to mind.....
To me learning how stuff is made or can be made is quite fascinating....I'm amazed most days when I learn of new ways stuff can be done.....
And I guess seeing which of these ideas/methods can be adapted for home use is part of the whole locosting concept...
|
|
timf
|
posted on 20/2/04 at 02:56 PM |
|
|
quote: Originally posted by Alan B
And I guess seeing which of these ideas/methods can be adapted for home use is part of the whole locosting concept...
spark erosion lends itself to this very well.
|
|
Alan B
|
posted on 20/2/04 at 03:14 PM |
|
|
quote: Originally posted by timf
quote: Originally posted by Alan B
And I guess seeing which of these ideas/methods can be adapted for home use is part of the whole locosting concept...
spark erosion lends itself to this very well.
Yeah yeah...maybe not the best example....but you get the point...  
|
|
Alan B
|
posted on 20/2/04 at 03:18 PM |
|
|
quote: Originally posted by Syd Bridge
I don't know if I'm getting confused, but are 'wire cutting' and 'spark erosion' different things? I say this,
because I know that some of the F1 teams had their uprights made by spark erosion. Very expensive, gotta make the sparker first. Investment casting
makes a lot more sense.
Just remember to use the right colour wax ! I caused a few laughs recently when I turned up with 'pretty pink' wax patterns. Dental wax
was sent to me instead of industrial green.
They certainly remembered when I turned up to collect the castings!
Cheers,
Syd.
Syd,
Basically there are 2 types of "spark erosion" or EDM.
The plunge or sinking type were a female die is made from copper or graphite.
And the wire type, which is more like bandsawing in concept using brass wire.
|
|
timf
|
posted on 20/2/04 at 03:25 PM |
|
|
quote: Originally posted by Alan B
quote: Originally posted by timf
quote: Originally posted by Alan B
And I guess seeing which of these ideas/methods can be adapted for home use is part of the whole locosting concept...
spark erosion lends itself to this very well.
Yeah yeah...maybe not the best example....but you get the point... 
alan i'm serious
i saw plans on the web for a home made spark eroder made from a 12v car coil and such parts.
Tim
|
|
Screwy
|
posted on 20/2/04 at 03:32 PM |
|
|
IIRC Model Engineers Workshop magazine carried a series of articles on building a home build EDM machine (Also a home build cnc lathe-miller) also
think there was some talk of a homebuild wire edm machine but not to sure but i am sure there was an article on producing gears for a traction engine
with wire edm all intresting stuff tbh .
btw i,m pretty sure the EDM machine was mains powered and used a stepper motor and home produced circuit boards , dont know if it would be up to
making locost parts though
[Edited on 20/2/04 by Screwy]
|
|
dozracing
|
posted on 20/2/04 at 10:49 PM |
|
|
Its horses for courses, you can get wiring done for £14 per hour if you run it over night etc.. Depending on the part and the number of parts you want
etc it could be cost effective. At the end of the day its a lot more expensive than laser cutting, more accurate though.
Kind regards,
Darren
|
PLEASE NOTE: This user is a trader who has not signed up for the LocostBuilders registration scheme. If this post is advertising a commercial product or service, please report it by clicking here.
|