Minicooper
|
posted on 12/5/09 at 10:16 AM |
|
|
The Rally Design ones I purchased are the domed bottom ones, I don't want the things falling apart on me!
Cheers
David
|
|
|
Liam
|
posted on 12/5/09 at 11:37 AM |
|
|
Matt - the photos are also in his photo archive - can you see them there?
liam
|
|
procomp
|
posted on 12/5/09 at 02:19 PM |
|
|
Hi
Hooray got computer fully working.
Looking at those pictures it dose not look like anything has actualy broke as such. But looking at the alignment of the front and rear pivot bolts for
the top wishbone. They are not in alignment. Could be poor jigging but my gues would be that the chassis upright has bent. Especially if the outer
frame is of the type that is not supported by a diagonal going back to the bulkhead.
I would suggest running a straight edge down the inner face of the tube and along the edge of the outer frame and check for straightness as a starter.
Mind if that it the problem it should be quite visible to the naked eye.
PS i should also say that although i keep referring to the better and poorer designed joints. It should be said that the domed ( poorer ) joint is
still perfectly aceptable for use in the aplication. Just that is is not as well designed at the other version.
Cheers Matt
|
|
procomp
|
posted on 12/5/09 at 02:45 PM |
|
|
Hi
Just re read and the " loud bang " and wheel falling over dose not support my theory. Unless the whole sodding chassis upright parted
company.
Got me puzzled.
Cheers Matt
|
|
rusty nuts
|
posted on 12/5/09 at 06:24 PM |
|
|
I to think the problem is with the lower arm rear bolt/ bracket area .
|
|
JohnN
|
posted on 12/5/09 at 08:54 PM |
|
|
Ball joint failure - the verdict
Just in case anybody were to miss the sequel to my earlier thread - I now have the answer, and its a bit of a worry.
Following Dusty's suggestion and I think later Rusty Nuts, I had No.1 son have a look at the bottom rear wishbone mount.
And guess what - it's torn the "U" bracket out of the chassis rail. So, that'll be a major repair. I haven't actually seen it
myself yet, just an iPhone picture. But I'm concerned that with the top torn out of the chassis rail, it may have also got bent.
Hey ho, I'll have to trailer it home and get the tig set out and think of some reinforcement in that area.
Here's the picture:
 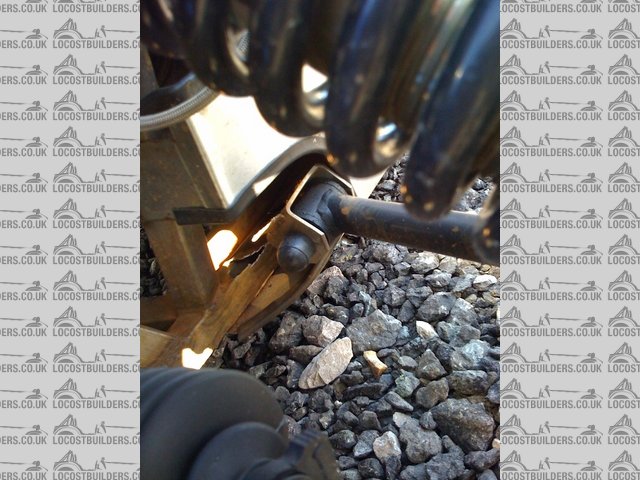 Suspension failure
Wow - doesn't the wall of the box section look thin - I'll get a measure on that asap
[Edited on 12/5/09 by JohnN]
|
|
MikeRJ
|
posted on 12/5/09 at 10:08 PM |
|
|
It looks like it was never fully welded onto the chassis rail, has it torn the chassis rail at the other end of the bracket?
Shouldn't be too bad a job to fix that, though you may have to partially remove the side panel to get access. Time to check the other side
though!
[Edited on 12/5/09 by MikeRJ]
|
|
procomp
|
posted on 13/5/09 at 07:33 AM |
|
|
Hi
Unbelievable that a manufacturer would only weld the bracket on 2 or 3 sides.
Tubing thickness is where virtually all chassis manufacturers are not paying attention these days. All the tubing that is supplied these days is down
on MIN tolerance IE 16g will actualy be 17 1/2 g. These days you have to ask for certificated tubing when ordering to get what you actualy asked for.
Or order a gauge size up IE order 14g to get 16 1/2 g tubing.
It is perfectly aceptable to build the chassis out of 17 1/2g - 18g as many of the race chassis are. But it requires a bit more attention to detail
and bracing. Something that is lacking in many of today's chassis. And is starting to show espesialy as more and more people are using there
cars for trackdays with sticky tyres fitted to them.
Maybe this is a bit of a reminder to all of us that it realy dose pay to give the car both mechanically and the chassis a good looking over a bit more
often than just prior to the MOT.
Cheers Matt
|
|
40inches
|
posted on 13/5/09 at 08:55 AM |
|
|
quote: Originally posted by procomp
Hi
Unbelievable that a manufacturer would only weld the bracket on 2 or 3 sides.
Cheers Matt
Is it a manufactured chassis? I thought it was a home built chassis with Luego wishbones.
Either way I would check all major welds, because it looks to me as though the bracket that failed has only been tacked on, plus is there any weld
visible on the front top wishbone bracket? looks not to me.
|
|
907
|
posted on 13/5/09 at 10:00 AM |
|
|
Hi John
I'm probably almost as concerned as you about this as I have a similar chassis.
I note that it broke when on full lock and in reverse gear, I presume then at very low
speed and not bumping up a kerb or suchlike?
Full lock does exert a lot of force into the bones.
When I push mine in and out of the garage I can hear the tyres scrubbing.
I also note it was welded as 4 stitches, not weld all round, and the box does look thin
but photo's can be deceptive.
My own chassis is a +4, wide nose & book length w/bones.
Is yours a 442, and does that mean standard width nose and long w/bones?
Long bones (if you have them) do increase the force on the chassis and the mounts
simply by the law of leavers.
I sincerely hope you find the problem cause and engineer a suitable solution.
Cheers
Paul G
|
|
MikeRJ
|
posted on 13/5/09 at 11:19 AM |
|
|
What grade of stainless was used? I'm sure Paul will know a lot more about this than most, but I believe some grades can become very brittle
around welds without post heat treatment?
|
|
JohnN
|
posted on 13/5/09 at 12:23 PM |
|
|
Just to clarify. This isn't a Luego chassis, its a self built stainless 442 chassis, with Luego sourced wishbones (Velocity XT).
I am at fault for not fully welding the bracketry (when it was far more easily accessible ) Now I'll have to check all the bracket welding.
I did all the original chassis welding by tig, (which was sometimes more difficult to do into the root under the curve of the bracket in awkward
locations). However, I now also have a mig, so the additional, less accessible welding should be easier to accomplish - I hope.
PaulG, yes, as a stainless chassis, there has always been concern expressed for potential stress related brittle failure. I believe that's what
I've now experienced, and I guess largely as a result of not fully welding the "U" bracket and allowing small flexing to work harden
the local area and a crack to develop from the end of a weld bead.
I suspect that the crack has been there for a small while, and that reversing and braking whilst travelling backward on full lock, provided the pull
on the joint that finally tore the metal.
Thanks for all the observations, diagnoses etc, now I need to get my hands dirty again, and quickly, I'm wasting tax, insurance and driving fun
now.
|
|
alistairolsen
|
posted on 13/5/09 at 03:41 PM |
|
|
quote: Originally posted by JohnN
stainless chassis
 
|
|