Liam
|
posted on 11/5/04 at 10:12 PM |
|
|
Here's a piccy of how it's shaping up in the metal.
Main reason I'm doing it this way is to have the different mounting positions for the shocks. I'll have a range of about 80 - 130 cycles
per minute wheel frequency which should be fun playing around with. The idea is softish and comfyish on the road and hard for the track
Top wishbones needs finishing and they will be triangulated structures themselves to take the large loads they're subjected too.
Liam
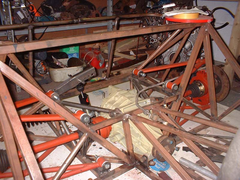  Rescued attachment rear.jpg
|
|
|
pbura
|
posted on 11/5/04 at 10:17 PM |
|
|
Very fine piece of work, Liam
Where will the shocks go? And how about turning that baby around and giving us a show and tell on the front and the left side?
Pete
Edit: My post crossed with your putting up your 2nd pic! 1st question answered, and I was hoping for something like that.
So, you just welded the rocker to the bush tube, apparently. Certainly nice and simple. Got any concerns about it holding up? Great-looking
wishbones, btw.
[Edited on 12/5/04 by pbura]
Pete
|
|
MikeRJ
|
posted on 12/5/04 at 08:46 AM |
|
|
quote: Originally posted by pbura
So, you just welded the rocker to the bush tube, apparently. Certainly nice and simple. Got any concerns about it holding up?
That is a neat design. Should hopefully be plenty strong enough when the appropriate triangulation has been added.
|
|
ned
|
posted on 12/5/04 at 09:06 AM |
|
|
Sorry,
Hope this isn't a stupid question, but is there enough room to get the dif in and out, as on a lot of designs I've seen that are ultra
stiff you end up closing a gap that the dif might need if it were to be removed.
Ned.
beware, I've got yellow skin
|
|
James
|
posted on 12/5/04 at 10:05 AM |
|
|
quote: Originally posted by ned
<snip>
is there enough room to get the dif in and out, as on a lot of designs I've seen that are ultra stiff you end up closing a gap that the dif
might need if it were to be removed.
Ned.
Who on earth would go and do a silly thing like that! Doh!
The one thing that bothers me about some of these designs is the shear amount of metal in them!
If you look at pictures of how MK has done their IRS backend it's a lot lighter. At the same time I've not heard of anyone complaining
that the back end of their MK chassis has collapsed!
Not that I know anything about chassis design so I'm probably talking rubbish!
Cheers,
James
|
|
spunky
|
posted on 12/5/04 at 10:41 AM |
|
|
I agree with you James,
I also no nothing about chassis design but there is a lot of steel in use in some of the chassis posted on this forum.
I worry when I look at my chassis and wonder if its up to the job, but it was designed and built by Stuart Taylor who has a fair racing pedigree.
I guess the "better safe than sorry" is particularly relevent in chassis building.
I really like Liams design of the rocker/wishbone assy. Got me thinking of future projects...
John
|
|
stephen_gusterson
|
posted on 12/5/04 at 11:24 AM |
|
|
I mounted my diff by using two 3mm plate arrangements - but then my IRS bones are not hanging off that point...........
atb
steve
|
|
chrisf
|
posted on 12/5/04 at 12:56 PM |
|
|
That was a cool box design. I have not welded my lower supports yet. I am concerned about being able to remove the diff as well.
Yes, the back of the car can acquire quite a bit of weight. But I'm planning to use other materials for the removable supports. Honestly, I
suspect the portly Sierra diff is cause of most of the weight. The steel I used for the 'box' so far pales in weight comparison to the
diff!
--Chris
|
|
pbura
|
posted on 12/5/04 at 02:34 PM |
|
|
There's some comfort in the fact that 20 feet of extra tube weighs only about 16 lbs. 
I got interested in IRS because it seems to be the cleanest way to do inboard shocks. For someone interested in a conventional shock layout,
Donkervoort has a very efficient design, much stronger-looking to me than the Tiger-style "box" and not a ton of metal:
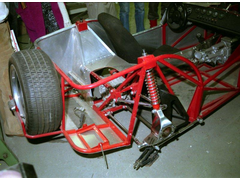 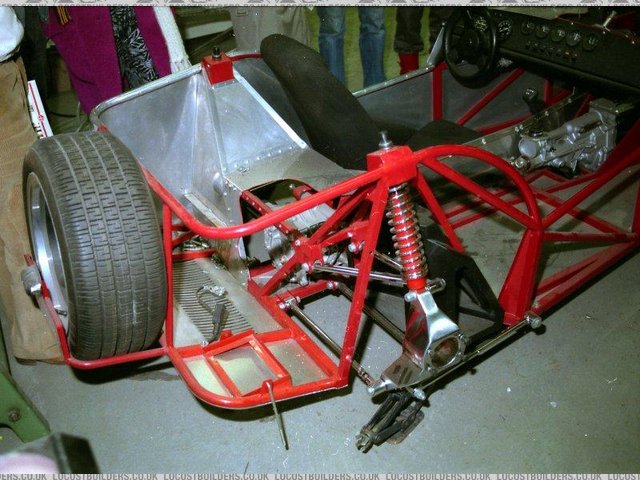 IRS rear
Pete
|
|
Mave
|
posted on 12/5/04 at 03:17 PM |
|
|
Yep, the Donkervoort design is very good indeed. I modelled my design like that, (see http://www.mk-indy.nl/images/chassis%20assy.jpg) and had it FEA
analysed. It is VERY stiff. And pretty easy to make: aligning the brackets is easy. (well, it is easy when you know how to weld, which was my problem)
|
|
Mave
|
posted on 12/5/04 at 03:20 PM |
|
|
Oh, by the way: have you noticed where they place the fueltank? It is in the picture, look hard!
|
|
chrisf
|
posted on 12/5/04 at 05:51 PM |
|
|
Mavee
Great job on the IRS 'box' design. You wouldn't want to share those files, would you? I'd like specifically to see how you
designed the roll bar mounts, as well as study up on the diff box bracing.
--Chris
|
|
Liam
|
posted on 12/5/04 at 09:00 PM |
|
|
Hello...
Cheers for the positive comments dudes. I'm stupid, and almost that stupid, but not quite - the diff comes out of the top of the box. The
room behind the diff where the shocks go provides just enough space to get it out. Bit of a jiggle - but not as tight as the front diff
As for the weight, the triangulation is only 3/4" 16swg, and to vaguely quote someone else: lots of it weighs not much. My chassis has
something like 15-20 kg extra tubing in it compared to a book chassis, and that's including all the irs, my structural scuttle and my removable
bracing over the engine linking the scuttle to the front suspension. If I remember, that's roughly all offset by using aluminium panelling
instead of steel in the floor and such like. The chassis in these cars isn't very heavy and isn't really the place to save weight (unless
you're building an extreme BEC). It is the place to chase excellent stiffness imho and the benefits that gives.
No one's MK or whoever's chassis is gonna fall apart or anything, but that sort of thing has to be designed to be cheap, quick and easy to
produce to be viable for the seller, and still perform more than acceptably. People like me can spend ages chopping up tube in the quest for ultimate
stiffness (if they think that's important).
I really like the donkervoort rear end, but am surprised it seems to have no tunnel at all. Oh well. Dax rush irs chassis is nice too. Mave your
design looks cool - in fact your rear bulkhead looks almost identical to mine. Great minds eh . I'd really like to get mine FEA'd to
see if it's all been worth it. I doubtless have a few tubes sitting there doing nothing, but hopefully dont have any glaring weaknesses that
ruin all the good parts. Hopefully will get some FEA software before I just go ahead and paint the chassis!
Oh yeah - my wishbones as they are are definately not up to the job! In my softest setting my suspension leverage is 2.5 to one so
there's some big load on the rocker and it's pivot. The wishbones are still to receive a tube from the other bush to the inner end of the
rocker for fore/aft location, and the most important tube from outer balljoint (where the upright connects) also to the inner end of the rocker, to
eliminate bending.
The pivot point is quite heavily loaded (about 500kg upwards when the car is just sitting there in the softest setting) and the rearmost bracket which
is almost in line with the inner and outer ends of the wisbone takes most of the load. The bracket there is doubled up to 6mm thick and I'll
use decent M12 shoulder bolts. All plenty strong enough - but it did surprise me a bit when I calculated the load on the pivot. It's the high
leverage on my soft setting that does it - something to bear in mind if you're doing a similar design.
Time to shut up...
Liam
|
|
MikeRJ
|
posted on 12/5/04 at 09:30 PM |
|
|
quote: Originally posted by Liam
The pivot point is quite heavily loaded (about 500kg upwards when the car is just sitting there in the softest setting)
The only thing that would worry me would be the ability of a poly bush to take those kinds of loads for any length of time.
The Donkervoort design is very nice, gives loads more storage room as well. Shame there isn't any McSorely type plans for something like this.
[Edit] talking nutsack again.
[Edited on 12/5/04 by MikeRJ]
|
|
Liam
|
posted on 12/5/04 at 09:59 PM |
|
|
Yeah that's my only concern really. I think they ought to be abe to take it (i'm not exactly the first person to try this), but
I'll be keeping an eye on the bushes. I may eventually upgrade them to proper bearings if they're not up to the job.
LIam
|
|
Mave
|
posted on 13/5/04 at 04:54 PM |
|
|
Why need a McSorely-plan when you can have a Mave-plan? (well, sort of; I'll not make all those tube drawings like McSorely).
If anyone is interested, drop me a mail, and I'll send you a 2,7 Mb 3D file you can look at, turn around, etc.etc.
Ah, let me see if I can attach it to this message....
|
|
chrisf
|
posted on 22/8/04 at 08:01 PM |
|
|
Finshed (...Sort of)
Hi All:
Many thanks to everyone who helped guide me many months ago. I've finished the final design and just have some minor revisions to some little
things.
Concerning the original post, this is what I came up with. On the bottom of the diff box, I'll use the 5mm 6061 or 1.5mm Ti. i realize the upper
arm angle looks a bit concerning. I hope that the chassis will settle to ride height as the weight builds. I also need to adjust the spring preload.
Of course, if all else fails, some Eibach spings may be in the cards. But that is a different post! Again, thanks for all the help.
--Chris
[Edited on 22/8/04 by chrisf]
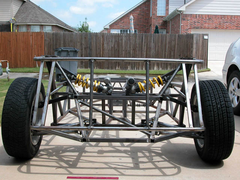  Rescued attachment RearSuspension1Small.jpg
|
|