rodoe
|
posted on 11/7/16 at 08:07 PM |
|
|
Thanks Sam, had checked the Inverter out a few years ago but forgot about the the chassis stiffening there.
As for the 'oil canning' issue, i read an old air sheetmetal book written for US aircraft builders
in possibly WW2 days. Their practice was to run (and i forget what they're called now) stringers or ribs every 20 inches
of sheet aluminium. Looking at the Elfin mono bare chassis or the Elwin with the outer sheet removed, you can see the extra ribs for stiffening.
I wonder what help this would be to preventing the Oil canning issue?
|
|
|
ftaffy
|
posted on 13/7/16 at 02:46 AM |
|
|
Nice links, thanks. Enjoying taking a look at the build blog.
While i am an engineer i dont work in this field, so take any of my comments with a grain of salt.
The extra stiffeners along the chassis is something i am keen to do, i believe that it would reduce this in that it will isolate the zones more. But
obviously 1 weak area stuffs the whole thing, but the same is true for a locost chassis. Make the entire car super stiff but have 1 weak area it will
fatigue and fail over time.
The 25 had these along its length while the 49 removed them, seeing the crash pictures they didnt seem to matter strength wise but even those cars
which ran on for a few years in private hands seem to have on going mods and i would guess they got refreshed. They were not glued which would have
made it easier to do.
The lotus 35 had a steel inner U of something around 0.8/1mm at some stage in its life as opposed to the AL U seen in the 25/49. Thinking about
copying this as it opens up a few other options for me with a small weight addition. To me that is not critical given this is not to win sheep
stations, but for the fun of it. Means i can weld the damn thing together instead of 3000 rivets.
If i was racing and wanted this shape i would go the honeycomb core and keep the additional bulkheads with the outer single skin, take a look at
'The Race Car Chassis' by Forbes Aird for info on materials in chassis including monocoques.
Also note that the 25 was not that good of a design, without the rigid mounted engine the torsional strength was less then half the strength.
A fully steel mono core is around 60kg
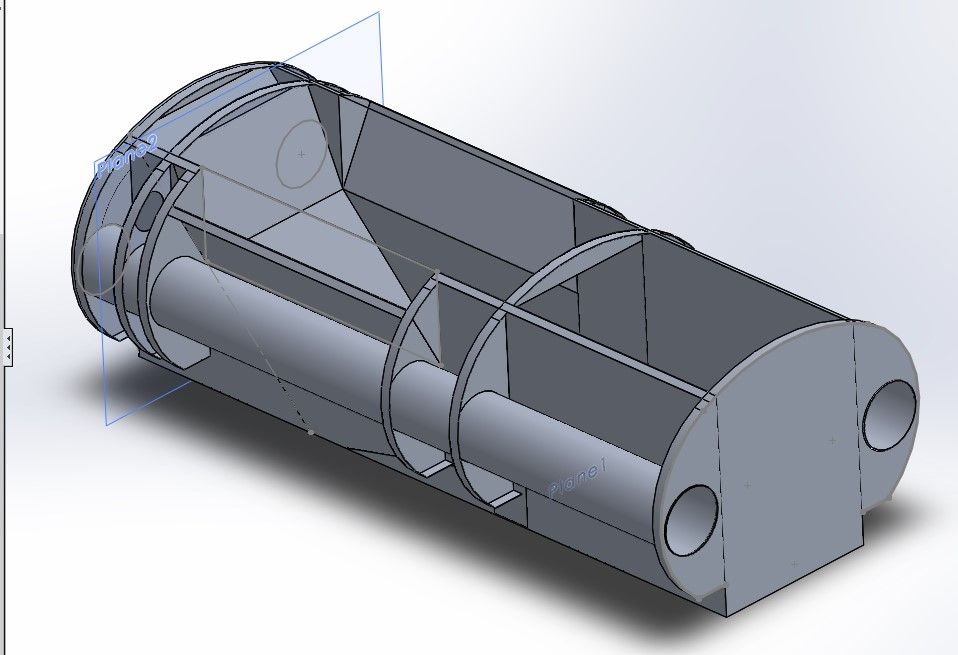
What i mean by honeycomb and keeping the additional formers/ bulkheads.
The 25 data:
Tub 12in deep
Outer skin 16 gauge L72 Alcad (R4 onwards, before that 18 gauge)
Inner skin, floor, seat back 14 gauge
Engine bay inner skin 20 gauge.
The inverter would be a great project to build but alot of machining and custom body work required, a group build would be a better option if one
wanted to do this IMO.
Rivets wise, my knowledge is limited, i used simple pop rivets in my locost. But if you want to play monocoques i would be using solid and really
thinking about the flanges in stressed areas. The idea of just cutting slots in an angle, bending into a curve an riveting it on to is not a good idea
for anything more then a radiator shroud.
http://www.gt40s.com/forum/lola-t70-lounge/22490-lola-t70-scratch-bu
ild.html
Been keen to hear what you come up with, happy to keep putting what i have on the table as i no commercial interest in this field.
Cheers,
Taffy
|
|
rodoe
|
posted on 13/7/16 at 01:37 PM |
|
|
Good point about the engine stiffening the chassis. I'd read that before and thought if i put a bike engine in, with its mounting points it
won't really add much stiffness.
Apart from this, I've been offered access to a Brabham body mold and so looks like the mono dream will end for something more traditional.
As for those models you put up Taffy, those pipes running the length of the chassis were retro fitted to one of the Elfin Mono's when it was
restored many years ago (was privy to the rebuild photos).
Lola T70, mmmmmmmmmm (insert Homer Simpson drooling here).
The all steel outer skin sounds like a great idea, easy to weld and all. Another idea is to go the Alan Staniforth method (used in the Terrapin , for
which i have the book and plans) of space frame chassis witb outer side skins of aluminium for extra stiffness.
Will be keeping a keen eye on this thread though.
Rod
|
|
Sam_68
|
posted on 13/7/16 at 02:53 PM |
|
|
quote: Originally posted by ftaffy
...obviously 1 weak area stuffs the whole thing, but the same is true for a locost chassis.
As an aside, Axion/Westfield used that as partial justification for the reason that only the centre tub on the new Westfield prototype chassis is CF,
with spaceframe subframes front and rear: one of their objectives was a 30% increase in total stiffness, but to achieve that, they needed a 70%
increase in the stiffeness of the cockpit section, which is the weak area on the typical 'Seven' chassis. By comparison, the engine bay
was less crucial, and the spaceframe made sense for flexibility of different engine installations in this area.
quote: Originally posted by ftaffy
A fully steel mono core is around 60kg
I would have to ask myself what the point of a monocoque was, other than 'because I can', at that weight: for a small single-seater
it's easy to do a steel spaceframe of perfectly adequate stiffness for quite a bit less weight than that. Hell, I've just done a 2-seater
'Seven' spaceframe (complete with traditional 'weak' cockpit bay and stressed for 300+ bhp and slicks) that's a good
chunk lighter than that!
quote: Originally posted by ftaffy
Rivets wise, my knowledge is limited, i used simple pop rivets in my locost. But if you want to play monocoques i would be using solid and really
thinking about the flanges in stressed areas.
Google 'structural pop rivets': you can get blind rivets that are designed to give high strength in both tension and shear, and use of
these is normal practice in monocoque tubs. There's plenty of advice available from manufacturers.
|
|
Neville Jones
|
posted on 13/7/16 at 05:38 PM |
|
|
The easiest way of solving the torsional problems in cars with open cockpits(ie '7' type cars), is fit a full cage with diagonals. The
rest of the chassis then becomes the soft areas, not the caged areas.
Not a lot of help for this chap with his open wheeler though.
Westfield??? Just another gimmick, to try and resurrect sales.
[Edited on 13/7/16 by Neville Jones]
|
|
Sam_68
|
posted on 13/7/16 at 07:01 PM |
|
|
quote: Originally posted by Neville Jones
Just another gimmick, to try and resurrect sales.
Just another gimmick to try and extract large sums of money from the Government, in fact.
And very successful at it they've been too... this has been the 6th funded project that Westfield/Potenza have undertaken in the last 4
years.
My bet is that they're making a lot more profit from NVN funding bids than they are from manufacturing cars, just at the moment. 
|
|
ftaffy
|
posted on 13/7/16 at 11:34 PM |
|
|
quote: Originally posted by Sam_68
quote: Originally posted by ftaffy
A fully steel mono core is around 60kg
I would have to ask myself what the point of a monocoque was, other than 'because I can', at that weight: for a small single-seater
it's easy to do a steel spaceframe of perfectly adequate stiffness for quite a bit less weight than that. Hell, I've just done a 2-seater
'Seven' spaceframe (complete with traditional 'weak' cockpit bay and stressed for 300+ bhp and slicks) that's a good
chunk lighter than that!
But what is the torsional stiffness:weight? i made a ~5000nm/deg locost with no roll cage that is dragged around by BMW M44 (135hp, a lot less then
what you are talking about). Total weight wet was 650kg, not the lightest i will agree but if you take a look at a <2000NM/deg westfield (Real
world test) that comes in at 550-600kg (dont know the final figure as the car has been modified a few times). What is better?
The 24 and had basically the same weight but the 25 was much stiffer and considered the better car, but there must be a tipping point some were in all
that and for racing that will probably be weight. I remember the story of MP4/1 that they designed it the same as a AL honeycomb and ended up 3-4
times the stiffness at the same weight, so cut it down to only be ~double the stiffness but was 25%? lighter (memory is foggy on the exact figures but
does indicate at that leveling the thinking is weight is king vs stiffness).
You can cut the design above down by another 10 maybe 15kg (lightening holes, use AL in a couple of simple areas, etc) and still have a fairly
straight forward build. Laser cut all the panels with tabs for self alignment when assembling, have the U folded up by the cutter on a ~2m brake.
Small 300mm roller for the weld on flanges on the bulkheads, small <1m folder for the rest of the panels and away you go welding up the joints. The
idea is accuracy you wont get with a space frame without making a lot of jigs and stuffing around, with the strength a mono offers and the easy build
mild steel will give you all at the sacrifice maybe 10% of the total weight.
For those coming from a Locost with only backshed tools not may will be skilled beating AL to a near enough shape, then flattening using a an english
wheel, forming a flange and then safely preparing, gluing and riveting 3000 spots on a car. The end goal we are looking at is different, a cheap toy
vs a race car.
If i was going for a winning race car i would ditch the VW V6+ road car uprights + the skin type mono, go a bike powered honeycomb chassis as you
suggest. Remove all weight possible, custom uprights, etc.
For reference sake, weights of 1960's race cars we are talking about:
Lotus 49: ~530kg (Engine was 168kg of that, chassis: No idea sadly...)
Lotus 25: 452kg, with a chassis weight of just 31kg...
The odd ball is the space frame W196 weight 10% more then a 25 but over 50% stiffer. Good design by the Germans.
A big take away i learnt from time in F-SAE was a simple car finished and tested will beat an advanced minimally tested one. So always work towards
the simplest solution even if its not the absolute best.
quote: Originally posted by Sam_68
Google 'structural pop rivets': you can get blind rivets that are designed to give high strength in both tension and shear, and use of
these is normal practice in monocoque tubs. There's plenty of advice available from manufacturers.
Thanks will take a look for those, like my pop/blind rivets as opposed to solid.
One area that always worried me with these designs is the floor being just a single sheet flat sheet. In my locost i made the floor a swedged shape
like what you do in retaining walls/ ships bulkheads to stiffen it, the use of a single sheet worries me.
I am worrying about nothing as people keep doing it without major effect?
Cheers,
Taffy
|
|
Neville Jones
|
posted on 14/7/16 at 08:52 AM |
|
|
quote: Originally posted by Sam_68
My bet is that they're making a lot more profit from NVN funding bids than they are from manufacturing cars, just at the moment.
That's a fairly sad statement on the state of the company.
They should be making many, many times more profit from genuine sales, than the small amounts(relatively) that come from their possible portion of the
NVN grants.
-------------------------------
To stiffen the old style chassis in the cockpit area.....needs bigg side additions, to bring up the numbers, then a smooth transition into the front
and back.
Start the design from the cockpit, and work outwards, and not design the chassis hen try and stiffen the cockpit. Back to front thinking!
Cheers,
Nev.
|
|
rodoe
|
posted on 24/7/16 at 08:05 PM |
|
|
An aside question here. How are the lotus 25 front rocker arms made? Google gives no clues.
|
|
Sam_68
|
posted on 24/7/16 at 08:32 PM |
|
|
quote: Originally posted by rodoe
An aside question here. How are the lotus 25 front rocker arms made? Google gives no clues.
They were fabricated from 16 gauge sheet steel, including an internal lattice web, pivoting on 1/2" bolts though needle roller bearings.
|
|
ftaffy
|
posted on 15/8/16 at 03:12 AM |
|
|
Rodoe, Any progress on your build?
I came to the conclusion a 49's shape is simply too complicated for a first round, the 25/33 is must more suitable as a stepping stone.
Nothing exciting to show for all of that, but essentially going widen the car 360mm tub with 2 180mm D's. Keeping the same wheelbase but
slightly widening the track to sit between the 25 and a 49 to suit the golf mk3 rack and the drive shafts off the 5HP19 gearbox (VW Passat).
Again not going to run fuel tanks in the side pods, a single ~20L tank behind the seat which will mean a slight extension to that space which is fine
as the V6 is shorter then the V8 and would have been dead space anyway.
The other benefit is the extension of the tub backwards of the seatback is mild steel which means you can weld on engine mounts, etc without fatigue
concerns if it was AL.
Also racking up the hours reading aircraft construction and metal working books. Been holding off pulling the trigger on buying the english wheel, etc
until i finish the design and really commit i am going to do this thing.
Cheers,
Taffy
|
|
ftaffy
|
posted on 6/5/17 at 12:39 PM |
|
|
This might inspire some people:
http://www.gt40s.com/forum/wings-wheels-keels/49645-lotus-38-ish-re
plica.html
Mono Lotus 38 inspired build, great detail in the photos.
|
|
Sam_68
|
posted on 6/5/17 at 02:49 PM |
|
|
Very nice!
"Then it was just a matter of translating each paper component to sheet metal..."
The man is a master of understatement! 
|
|
sam919
|
posted on 14/5/17 at 09:32 PM |
|
|
Great thread guys, very interesting about chassis design....keep the pics coming !
|
|