procomp
|
posted on 29/3/06 at 12:42 PM |
|
|
Hi syd first off i am not going to get in to a slanging match with you . all i will state is that if you use a compliant bush setup you will achive
more free axle movment than with rod ends. please remember we are talking locost geometry pesific here as ime pretty shure that nascars and oz
v8's dident look at a locost for their insperation. The fact that we are stuck on such a short lenght arm is the main problem and ive already
said that the likes of mallock dont have this problem with longer arms.
As for my reputation well i dont care what you think but i do have many customers who will testify that they are hapier whith thier setup after
switching to a complient rear end after using rodends.
You dont seem to want to agree to disagree or explore the other side of the fence.
as i said im'e not going to get into a slanging match.
hoever if you would like to join us when we are at a trackday i will gladly let you drive one of the cars and you can make up your own mind.
this is the last post im'e going to make on this thread as their is a big fence with two sides and a wide ledge on top and this could carry on
till the cows come home.
cheers matt
|
|
|
MikeRJ
|
posted on 29/3/06 at 01:18 PM |
|
|
US racers use something called a birdcage to eliminate binding in their rear suspension setups, ever heard of these Syd?
[Edited on 29/3/06 by MikeRJ]
|
|
NS Dev
|
posted on 29/3/06 at 01:28 PM |
|
|
not remotely expert on this stuff but they would appear to solve the problem by allowing one end of the 4 link to rotate on the axle tube????
Don't really understand that as you must get strange torque reactions, but as you say, it seems that this is used to prevent bindup.
[Edited on 29/3/06 by NS Dev]
Retro RWD is the way forward...........automotive fabrication, car restoration, sheetmetal work, engine conversion
retro car restoration and tuning
|
|
britishtrident
|
posted on 29/3/06 at 01:42 PM |
|
|
At times like these I feel like getting the old Weegie out and calling up the spirit of Fred Lanchester.
To quote Newton "We stand of the shoulders of giants"
|
|
JonBowden
|
posted on 29/3/06 at 02:01 PM |
|
|
Ok, just modelled it with string and short lengths of 1" x 2" wood.
My first result was upsetting - it binded!!
However, this was found to be due to my string catching on the edge of the wood, making two of the "arms" shorter.
Once this was fixed, then the system was free (ie the string remained taught when the pieces of wood were twisted), even when taken to extremes.
anyone care to knock one up using rigid links?
If this is not convincing, then I could make a bigger example with wider bits of wood. I could even try videoing the experiment if someone would llet
me post it somewhere
[Edited on 29/3/06 by JonBowden]
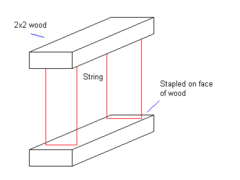  Rescued attachment test.gif
Jon
|
|
NS Dev
|
posted on 29/3/06 at 02:28 PM |
|
|
Yep, needs trying with solid links, the bind (if indeed it exists, as I say I am totally confused now!) will be VERY small in magnitude on a small
model (as it would on the car) but nonetheless a problem with solid links.
Just running through it with a colleague here who I usually turn to with geometry stuff, and he's musing over it too.
Conclusion at the moment is that if the roll centre is dead centred within the 4 link brackets on both the axle and the chassis then it will roll
perfectly with no binding............
however, as soon as any roll actually occurs, with a panhard rod, the roll centre migrates and the links no longer share a common centre and will then
tend to bind up. On the other hand this makes no sense to me as the links are all the same length and spherically mounted so as Syd said, should be
fine, but as I see it, one link needs to be able to change length for the system to work????
With a watts linkage, the roll centre remains in the axle centre, so in pure roll the linkage will not bind, but roll will almost certainly be
combined with pitch in the real world, or more often just be single wheel bump, in which case again the system will bind up???
God I am confused.
Found a great quote which I have decided sums it up great, by one Colin Chapman which roughly stated any suspension system works fine until it
moves!!!
about right here!!
Retro RWD is the way forward...........automotive fabrication, car restoration, sheetmetal work, engine conversion
retro car restoration and tuning
|
|
JonBowden
|
posted on 29/3/06 at 02:47 PM |
|
|
I can move the bits of wood all over the place (simulating moving the roll centre) but there is always a way to keep the string taught.
Jon
|
|
JonBowden
|
posted on 29/3/06 at 02:59 PM |
|
|
Thinking about it some more, I am convinced that 4 equal length parallel trailing arms will not bind. But :
- Non parallel arms will bind.
- Non equal length arms will bind (or at least constrain the roll centre).
Thus such arms if using rose joints must be adjusted to exactly the same length and the mounting points must be such that the arms are exactly
parallel.
Further, any chassis or axle flex will lead to "dynamic" binding.
Since any binding due to the above causes would place large loads on the bearings, I think it would be best to allow some compliance in the system.
Jon
|
|
NS Dev
|
posted on 29/3/06 at 03:26 PM |
|
|
I think that must be the answer John, as you say a system with no elasticity in the links will only need a very small movement of a mounting point to
cause a binding situation.
I'm going to have to forget this one now or it will drive me insane!!
Retro RWD is the way forward...........automotive fabrication, car restoration, sheetmetal work, engine conversion
retro car restoration and tuning
|
|
Syd Bridge
|
posted on 29/3/06 at 05:12 PM |
|
|
Matt.
There is no 'fence'. You made a blanket statement that is blatantly wrong, and you do not appear to be able to admit it. I will gladly
take up your offer, should I ever be in the position to do so. However, I'll more than likely be spannering my youngster racing against you
before that happens.
quote: Originally posted by MikeRJ
US racers use something called a birdcage to eliminate binding in their rear suspension setups, ever heard of these Syd?
[Edited on 29/3/06 by MikeRJ]
Mike
I am well aware of the 'birdcage' things, and as you should now realise, I am not a proponent. They are used to stop, (surprise surprise)
binding, when arms of grossly differing lengths are fitted. They need careful fitting to eliminate movement, and need constant attention and checking.
More trouble than they are worth. However, some still find the need for them. ( And no need for the smartarse attitude.)
Now, Mr.Trident.....SilentBloc bushes are another name for Metallastic. Same as the QH Y419's. Just the thing that polyurethane is put in place
of, and is a vast improvement on.
Cheers,
Syd 
|
|
procomp
|
posted on 29/3/06 at 05:34 PM |
|
|
Hi syd i did say that my first post was probably worded wrong but i will stand by a compliant set up on a locost will be better than one with rod
ends.
after that we will have to agree to disagree ime affraid.
i have never met you but i would still shake your hand if we met one day
cheers matt
|
|
cymtriks
|
posted on 29/3/06 at 09:44 PM |
|
|
It works like this...
Equal lenght and parallel trailing arms will not bind. Using a Panhard rod or Watts linkage won't change that statement.
Unequal length OR non parallel OR unequal and non parallel will bind. Something must twist or bend somewhere.
The Fury kitcar in live axle form uses a Watts link on each side to locate the axle fore-aft and a penard rod to locate sideways. It will bind BUT it
is rumoured that this is deliberate as it allows the rubber bushes to function as a progressive anti roll feature. Either that or it's a design
mistake that's been made to work well in the real world.
Other linkages are possible. Satchel links won't bind, can handle big power, and need four links as opposed to five. A three link and Panhard or
Watts will also work but strangely no one uses that either. Two links and an A frame, as used on the Caterham Deon, will also work perfectly with rod
ends without binding.
So I'm with Syd on this.
|
|
MikeR
|
posted on 29/3/06 at 10:13 PM |
|
|
Ok, I'll admit to not reading this thread (too late at night i'm afraid) but i've got one question.
In the real world perfectly equal length is near enough impossible to do, so what is an acceptable amount of difference between your trailing arms.
1mm, 2, 5 ?
|
|
NS Dev
|
posted on 29/3/06 at 10:54 PM |
|
|
No idea Mike, my brain has reduced itself to porridge with too much thinking about bloody links!!!!
Happy now that I was wrong though, but also happy that Matt was right but for various reasons other than the ones that I thought!
Ah well, just as well my 7 isn't live axle!!
Retro RWD is the way forward...........automotive fabrication, car restoration, sheetmetal work, engine conversion
retro car restoration and tuning
|
|
MikeR
|
posted on 29/3/06 at 11:26 PM |
|
|
yeah but mine is and one of my trailing links is a smidgen out!
(2mm as i recall)

|
|
C10CoryM
|
posted on 30/3/06 at 03:28 AM |
|
|
You would be suprised at how many vehicles have "bind" in their suspension and it is considered acceptable. Pretty well all OEM bushings
are rubber which is the great compensator for binding. The rubber will deflect enough to deal with it. For example, on a fox body mustang if you
install solid or poly bushings you will only get about 1/2 the wheel travel. Lots of older 3link GM cars are the same.
Ideally you will be able to remove the coilover on one side, and jack the diff up into the bump stop w/o compressing the other coilover. This is how
you check for bind. If it compresses the other sides spring, or lifts the vehicle, its bound up.
IMO, for a fun street car you need at least 3" of bump and 3" of rebound to avoid the dreaded bumpsteer. That means you can have up to
6" of difference between the 2 rear wheels. Do you see that in normal driving with a solid axle? Id bet never.
Long story short, the rubber bushings will deflect enough to deal with minor binding at the extreme ends of travel. If built right you will tear the
rubber before fatiguing the steel. Rose joints can not, I repeat NOT bind. They will come apart if they do. You must check for bind if you are
using a rose joint. I think most only have about 20degrees of rotation in the radial plane before binding.
Also, From my experience poly is totally unacceptable for use as a bushing unless it is greasable and you grease it often. Poly is a sticky materiel
and will bind when loaded. It also cold creeps. Stick to rubber, or solid bushings (ideally lined with delrin or similar)
The sprint car bidcages are used because there are no axle tubes. They ride directly on the spinning axles .
For the 4 links using a panhard bar you have to remember that the panhard moves in an arc. Since its attached to the axle, that means the axle is
moving sideways while moving up/down. This is where a lot of 4links end up with bind. This is where the rose joints come in handy.
I am no expert, but I do tinker with suspension on a regular basis .
Hope I have helped a little.
Cheers.
"Our watchword evermore shall be: The Maple Leaf Forever!"
|
|
Syd Bridge
|
posted on 30/3/06 at 08:37 AM |
|
|
quote: Originally posted by procomp
i have never met you but i would still shake your hand if we met one day
cheers matt
And I yours.
Cheers,
Syd.
|
|
Broadside Motorsport
|
posted on 30/3/06 at 08:20 PM |
|
|
Now shoot me and leave me for dead if I have got completely the wrong end of the stick, but I'm trying to think how it could bind and try to
word it and get a picture up so as to show it from procomp's point of veiw. Now after much head bending and convincing myself that it is
impossible for it to bind being equal lengths etc as everyone has already said i resorted to paint as simplicity sometimes overcomes complexities such
as autoCAD.
Now, the only way I can see that it can is as shown in the diagram i provide. I think everyone is thinking too much on the big scale of torsion and
its quite simply the fact that if you look at the rear axle as if looking down the prop shaft you will see the axle and spherical joints as shown on
the axle. Now when one side is up and the other down, the rod part of the joint will rotate, until it gets to the bolt that goes through the spherical
part, at which point it will stop rotating. Now assuming this is happening at both sides of the car at once, "binding" will occur. This is
assuming it is also happening at the other end of the rod aswell, and that there isn't a rotational bearing halfway down the rod aswell, or the
nuts will just undo and free rotation will occur resulting in the bar falling off.
Does that make ANY sense or have I just grabbed the shitty end of the stick that no one was talking about? Been a good think for me though because
I've always thought "this is how it's done, it works, it's not broken, don't fix it!"
Mark
|
|
JoelP
|
posted on 30/3/06 at 08:30 PM |
|
|
thats the mechanical binding that led to the 11 degree figure popping up. Matt thinks it will bind sooner for a geometric reason. 
|
|
Broadside Motorsport
|
posted on 30/3/06 at 08:32 PM |
|
|
Fair enough, so I was on the right trail to his thinking. Think a 3D model with spherical joints included is the only answer to this conundrum.
|
|
MikeR
|
posted on 30/3/06 at 11:45 PM |
|
|
i'm getting sorely tempted to get my technical lego out and see what happens.
If i go i'll take some pictures and post them.
(but not tonight)
|
|
Mix
|
posted on 31/3/06 at 01:16 AM |
|
|
Confession Time
This had been playing on my mind for too long...I decided to re-model the setup.
I made a mistake in my first model, (basically I didn't allow for the fact that vertical separation of the trailing link attachments at the axle
effectivly reduces). When this was taken into consideration the torsion in the axle dissapeared.
So.........I appologise for my previous, (misleading) post.
Mick
The moral of the story................my spatial awareness and ability to use CAD are adversly affected by lager... 
|
|
Syd Bridge
|
posted on 31/3/06 at 07:56 AM |
|
|
You've got it right, Mark.
The system will only bind at the limit of rodend rotation, as I said earlier. At this point, the system will 'lock' abruptly.
A poly bush setup will be putting torsion into the arms, and bushes, with the first movement.( The rodends won't, until the lockup point.) This
torsional load is there constantly, but varies, obviously, with normal car movement. The poly bush setup will be softer and progressive (just as Matt
says), but WILL lock up, just as rodends will. Simple geometry.
Cheers,
Syd.
|
|
craig1410
|
posted on 2/4/06 at 07:57 PM |
|
|
Hi,
I resisted the temptation to post before reading the whole thread and I'm glad I did since it seems to have been resolved more or less.
I have a full size working de-dion axle setup on my car with equal length parallel links and a panhard rod and I can confirm that it does not bind
throughout the limts of travel at both sides. I did take great care when building it to get the links exactly parallel and exactly the same length and
having read this thread I'm glad I did!!
Out of interest, my links are adjustable and have a left hand threaded rod end at one end and a right hand threaded rod end at the other (with
locknuts both ends). This means I can adjust the length in situ by loosening the locknuts and turning the arm itself. To get them all the same length
I just made a jig from a piece of square tubing with two 1/2" bolts welded to it the desired distance apart. It is then just a case of adjusting
the length of each link until they slide on to the jig. Any subsequent adjustment is done on a 1/2 turn at a time basis equally on each link.
Cheers,
Craig.
|
|
Cheffy
|
posted on 4/4/06 at 11:55 AM |
|
|
Hi Craig,
Thanks for the info. What size/thread rod ends did you use?
Thanks in advance ,
Martin
Farts are like Rock'n'Roll. You love your own but you hate everybody else's. Lemmy, Motorhead.
|
|