MK9R
|
posted on 21/1/10 at 01:36 PM |
|
|
Chopping and rejoining chassis
Any recommendations on how to rejoin the main chassis tubes if i cut the front section off between the engine and suspension pick up points?? Ideally
i want to build the new front end up on the bench, then join it to the existing chassis (which is a completed car). Ideally would have been nice to
slide an insert inside the tubes and push together and weld, but the angles chassis rails stop this option
Cheers Austen
RGB car number 9
www.austengreenway.co.uk
www.automatedtechnologygroup.co.uk
www.trackace.co.uk
|
|
|
blakep82
|
posted on 21/1/10 at 01:42 PM |
|
|
isn't it best to renew whole tubes instead?
cutiing and joining tubes is like cut and shut isn't it?
________________________
IVA manual link http://www.businesslink.gov.uk/bdotg/action/detail?type=RESOURCES&itemId=1081997083
don't write OT on a new thread title, you're creating the topic, everything you write is very much ON topic!
|
|
MK9R
|
posted on 21/1/10 at 01:50 PM |
|
|
quote: Originally posted by blakep82
isn't it best to renew whole tubes instead?
cutiing and joining tubes is like cut and shut isn't it?
yes it would be, but that would be a full strip back to the bulkhead, simply not an option
Cheers Austen
RGB car number 9
www.austengreenway.co.uk
www.automatedtechnologygroup.co.uk
www.trackace.co.uk
|
|
russbost
|
posted on 21/1/10 at 02:02 PM |
|
|
Absolutely no problem with joining tubes providing they are welded properly. Obviously the usual measure twice cut once applies, but due to the fact
that you're workoing in 3 dimensions with (presumably) 4 tubes you will probably need to juggle it all about a bit to get everything aligned. I
would suggest clamping some tubes along the sides of each joint to ensure all is square - you may well find a bit of tweaking of new &/or old
sections is required.
If you are concerned about the strength of the finished item then just add a brace across each joint.
I no longer run Furore Products or Furore Cars Ltd, but would still highly recommend them for Acewell dashes, projector headlights, dominator
headlights, indicators, mirrors etc, best prices in the UK! Take a look at http://www.furoreproducts.co.uk/ or find more parts on Ebay, user names
furoreltd & furoreproducts, discounts available for LCB users.
Don't forget Stainless Steel Braided brake hoses, made to your exact requirements in any of around 16 colours.
http://shop.ebay.co.uk/furoreproducts/m.html?_dmd=1&_ipg=50&_sop=12&_rdc=1
|
NOTE:This user is registered as a LocostBuilders trader and may offer commercial services to other users
|
A1
|
posted on 21/1/10 at 02:18 PM |
|
|
Id maybe be tempted to weld the tubes then add a bit of bracing and weld that up too. got any pics of the bit in question?
|
|
MK9R
|
posted on 21/1/10 at 02:27 PM |
|
|
quote: Originally posted by A1
Id maybe be tempted to weld the tubes then add a bit of bracing and weld that up too. got any pics of the bit in question?
Its the full front end, so main tubes got to be cut and rejoined
Cheers Austen
RGB car number 9
www.austengreenway.co.uk
www.automatedtechnologygroup.co.uk
www.trackace.co.uk
|
|
Agriv8
|
posted on 21/1/10 at 02:27 PM |
|
|
Id be tempted to sleve weld an internal tube then drill through and a spot of puddle weld on existing rails.
regards
Agriv8
Taller than your average Guy !
Management is like a tree of monkeys. - Those at the top look down and see a tree full of smiling faces. BUT Those at the bottom look up and see a
tree full of a*seholes .............
|
|
Daddylonglegs
|
posted on 21/1/10 at 03:34 PM |
|
|
quote: Originally posted by Agriv8
Id be tempted to sleve weld an internal tube then drill through and a spot of puddle weld on existing rails.
regards
Agriv8
My thoughts exactly. Would give it much more strength than just joining/bracing the tubes externally.
It looks like the Midget is winning at the moment......
|
|
MK9R
|
posted on 21/1/10 at 03:51 PM |
|
|
quote: Originally posted by Daddylonglegs
quote: Originally posted by Agriv8
Id be tempted to sleve weld an internal tube then drill through and a spot of puddle weld on existing rails.
regards
Agriv8
My thoughts exactly. Would give it much more strength than just joining/bracing the tubes externally.
Can't do that as chassis rails are angle inwards and want to build the new front end up on the bench so i can get it nice and straight and
welded all round
Cheers Austen
RGB car number 9
www.austengreenway.co.uk
www.automatedtechnologygroup.co.uk
www.trackace.co.uk
|
|
scootz
|
posted on 21/1/10 at 05:33 PM |
|
|
Bizarre!
I was thinking this very thing myself this morning - no need to the ask the question now!
It's Evolution Baby!
|
|
lsdweb
|
posted on 21/1/10 at 06:12 PM |
|
|
There's some photos on what 'we' did to my Westfield
here
Wyn
|
|
craig1410
|
posted on 21/1/10 at 06:15 PM |
|
|
Can't you create some heavy duty plates (eg 6mm steel) and then bolt on the entire front end? Obviously use high tensile (10.9 or 12.9) bolts
like you would with a roll bar.
I would think you would need something like 2 M10 or M12 bolts per plate with perhaps 6 plates. (4 corners plus 1 either side of tunnel). Ideally the
plates would have flanges to carry the shearing loads rather than rely on the bolts themselves.
I would be a bit concerned about cutting and welding in a line right across the car and would prefer to go the bolt-on route. Each section can be made
structurally independent and with a defined interface between the two sections.
Could also prove very convenient when removing the engine and gearbox.
Thoughts?
Craig.
|
|
craig1410
|
posted on 21/1/10 at 06:17 PM |
|
|
quote: Originally posted by lsdweb
There's some photos on what 'we' did to my Westfield
here
Wyn
That looks fine because the upper and lower tubes don't stop at the same longitudinal plane.
|
|
Angel Acevedo
|
posted on 22/1/10 at 05:11 AM |
|
|
Reinforcing Grafts
I would use gussets on the union, with a "U" section made to cover 3 sides, or an "L" for two sides; these with tube or 16 Ga
steel, or make Triangular Gussets from the Pipe size you´re using.
Just cut a 45º onthe end of the pipe, then another 180º apart, Grind to fit on the inside, weld, done..
HTH
AA
Beware of what you wish.. for it may come true....
|
|
907
|
posted on 22/1/10 at 09:07 AM |
|
|
If I wanted to butt weld box section and be 100% sure of the weld strength and penetration I would use the backing strip technique.
As you can't buy it I would make up a length of 22mm box.
Grind through two opposite corners of 25mm box to cut it into angle and weld it back together to form 22mm.
Clean off the welds and cut into short lengths and insert into the 25mm half way and tack.
In the case of your chassis, because these are short you would have no trouble sliding the joints together.
With a 2mm gap and a tad of prep this type of joint could be welded with complete confidence, even with a low powered welder.
Just my 2p
Cheers
Paul G
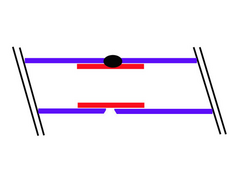  Rescued attachment backing strip.jpg
|
|
Agriv8
|
posted on 23/1/10 at 12:56 PM |
|
|
quote: Originally posted by MK9R
quote: Originally posted by Daddylonglegs
quote: Originally posted by Agriv8
Id be tempted to sleve weld an internal tube then drill through and a spot of puddle weld on existing rails.
regards
Agriv8
My thoughts exactly. Would give it much more strength than just joining/bracing the tubes externally.
Can't do that as chassis rails are angle inwards and want to build the new front end up on the bench so i can get it nice and straight and
welded all round
Dont see wht the angle has anything to do with it ? you would not be able to weld the iner tubes to your new or the existing but nothing to stop you
slidimg the tubes int correct position when lined up
Build as you are planning to do.
cut 4 internal ( you could equally do external but internal would look Pritier ).
put a marker line arround center point of each tube (and note length of tube )
Slide the internal tubes into exisiting chassis leaving a couple of mm exposed position new nose section.
Gently slide the inner tubes foreward into the new ( this should help to hold your new nose square ) keep sliding forwad until your 1/2 wat line is
visable between old and new chassis do samw for the other 3
tack weld ( check measurements )
Weld away.
then as you know the lenght of you inner tube drill and puddle weld
regards
Agriv8
Taller than your average Guy !
Management is like a tree of monkeys. - Those at the top look down and see a tree full of smiling faces. BUT Those at the bottom look up and see a
tree full of a*seholes .............
|
|
skinned knuckles
|
posted on 23/1/10 at 04:01 PM |
|
|
so long as you are a good welder and get good penetration, not just a surface weld then in theory, the join should be as strong as the metal you are
welding, but as a belt and braces approach, i would weld some 2mm angle over the join as well for 50mm either side of the weld. i would use angle so
that it acn be welded to the inside and lower surfaces of your box section so as not to effect the panel fit.
A man isn't complete until he's married, then he's finished
|
|
Peteff
|
posted on 25/1/10 at 07:58 PM |
|
|
I'd just cut the old one off and weld the new one on. Weld is all that holds the rest together anyway. Anything else you do to it is just going
to look bodgey.
yours, Pete
I went into the RSPCA office the other day. It was so small you could hardly swing a cat in there.
|
|