deneo
|
posted on 19/2/03 at 08:39 PM |
|
|
ali chassis
ali chassis with floor in place
cost so far £150.00
[Edited on 19/2/03 by deneo]
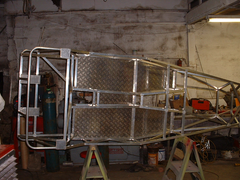  Rescued attachment 00000010.JPG
|
|
|
PaulBuz
|
posted on 19/2/03 at 08:48 PM |
|
|
looks ok so far, any idea on weight?
And wot about chassis flex?
|
|
Rorty
|
posted on 20/2/03 at 12:06 AM |
|
|
What are the dimensions and grade of the square tube?
If you grind any of the welds flat for the purpose of flush fitting panels etc, the welds are bound to crack.
Cheers, Rorty.
"Faster than a speeding Pullet".
PLEASE DON'T U2U ME IF YOU WANT A QUICK RESPONSE. TRY EMAILING ME INSTEAD!
|
|
kingr
|
posted on 20/2/03 at 12:34 PM |
|
|
Looks very nice. Have you got any ideas as to the service life of it?
Rorty - What is it that cause it to crack? Does grinding welds on mild steel have this effect too (obviously to a lesser degree) or is it specific to
ali? I always assumed that welds on ali were left unground because they look so good, they almost add to the look (especially that double fish scale
type effect you've got on the tubes in your gallery!!).
Kingr
|
|
kingr
|
posted on 20/2/03 at 12:37 PM |
|
|
Just to clarifiy, I probably ought to say tig welds look great rather than just ali tig welds, since the one in rorty's gallery looks to be on
steel.
Kingr
|
|
philgregson
|
posted on 20/2/03 at 12:46 PM |
|
|
I'm not sure about this bit aren't ali welds more prone to being brittle and cracking anyway.
I know ali work hardens as it flexes which would make it more brittle over time.
I also know that anealing ali makes it easier to bend.
I don't know what either of these facts has to do with the first statement if it is true but I supose that an ali space frame that was subject to any
degree of flex would be prone to cracking anyway regardless of the welds.
Help - I'm confusing myself.
Anyone enlighten me?
Phil.
|
|
philgregson
|
posted on 20/2/03 at 12:46 PM |
|
|
I'm not sure about this bit aren't ali welds more prone to being brittle and cracking anyway.
I know ali work hardens as it flexes which would make it more brittle over time.
I also know that anealing ali makes it easier to bend.
I don't know what either of these facts has to do with the first statement if it is true but I supose that an ali space frame that was subject to any
degree of flex would be prone to cracking anyway regardless of the welds.
Help - I'm confusing myself.
Anyone enlighten me?
Phil.
|
|
kingr
|
posted on 20/2/03 at 02:26 PM |
|
|
Phil - Although I make no representations to have any depth of knowledge about these things, my understanding was that Ali will fatigue if subjected
to flexing no matter how little, it will take longer with smaller movements, but it will happen. Steel on the other hand you could bend back and forth
within certain parameters (not massive admittedly, but significantly larger than you would want your chassis to have) indefinately, it's only when
you move outside of those parameters that it will fatigue. Hence the reason that, as far as I know, you can use a steel chassis for pretty much as
long as you wish (corrosion and wear aside) whereas using an ali chassis for an indefinite ammount of time would be inadviseable.
On the other hand I could be talking complete and total crap!
Please feel free to enlighten me.
Kingr
|
|
philgregson
|
posted on 20/2/03 at 03:15 PM |
|
|
I concur with your opinion entirely - What I'm not sure about is how the welds affect all this and why they should be subject to a particular
cracking problem (if indeed thay are).
Phil
|
|
philgregson
|
posted on 20/2/03 at 03:17 PM |
|
|
Just to throw another point into the ring - What about the aluminium monocoques that Audi and the like build - why don't they have a limited life?
Is it beacuse they are so stiff that they have been able to eliminate any significant chassis flex?
Is it perhaps only a problem on LOCOST style cars that are, by all acounts, somewhat lacking in the stiffness area?
Phil.
|
|
Simon
|
posted on 20/2/03 at 03:40 PM |
|
|
Phil,
I think that they (Audi) use metal that's so thick that whilst the cars are made from ally, they don't actually save much weight.
ATB
Simon
|
|
Wadders
|
posted on 20/2/03 at 05:58 PM |
|
|
Can't remember for sure, cos it's kinda lost in a fog of old age and alcohol sodden brain cells, but most alloys need heat treating (stress
relieving) after welding, to avoid stress and fatigue fractures occuring at the welded joints, however some alloys don't need to be heat treated
(can't remember which grade without looking it up). As said unless the structure is very rigid i.e like the beam frames on superbikes, you will
eventually have problems with cracking. Early Hyabusas had a rear subframe made of ally which was prone to snapping off and dumping the pillion onto
the rear wheel. Ally is lovely stuff and very strong if used in the correct applications/grade/and size, but beware it can be tricky to spec correctly
for the job.
Al
|
|
johnston
|
posted on 20/2/03 at 06:35 PM |
|
|
i have a bk on chassis design knockin about somewhere i think it said only porsche made a successfull spaceframe chassis outta ali as the fatigue
always got to them
but mayb be gd for sum1 doin the odd hill climb or sprints or such
|
|
Rorty
|
posted on 21/2/03 at 02:38 AM |
|
|
Kingr:
quote:
What is it that cause it to crack? Does grinding welds on mild steel have this effect too (obviously to a lesser degree) or is it specific to ali?
AL is fantastic stuff, but often causes more problems than it solves. Look closely at any welded AL structure that's more than a few weeks old, and
you'll often see a hairline crack at the start and end of each weld. It's frequently these cracks that spread due to loadings/resonance. They are
caused by poor start/finish welding technique/welder control.
Even if these hairline cracks aren't apparent, MIG and TIG welds can fail if the weld bead is interfered with post welding. AL differs from mild
steel in one really tricky aspect: it age hardens. That is to say, AL will get harder just sitting on the bench doing absolutely nothing. You can take
a billet of say, 6061-T3, machine it and weld it, and within a few weeks, it'll be T6!
In the case of a welded AL tube structure, if the welds are ground back, the in-built stress are altered, and the material can go beserk...more so
than with FE.
Like FE, some AL can be heat/solution treated, but treatment depends on what you're trying to achieve. Fine if you're after normalisation, but in
many cases, the AL will age harden anyway. Obviously some situations can't allow for components to naturally age, and so they are treated too.
A really good AL welder is worth their weight in gold. I can weld AL with both MIG and TIG, fairly satisfactorily, but wouldn't class myself a
welder. It's one of those lovely skills that's more art than science.
You'd probably find AL manufacturers R&D departments are larger and take longer per product than their FE counterparts. Just a guess.
There isn't a problem with AL in general, I don't want to get people worried, but you have to be aware of its benefits and drawbacks.
Grinding back FE welds isn't such a problem, but you'd still better be sure the parent metal is deeply "V"ed before welding. The object is to have
full penetration, and a thicker weld than the parent metal where possible. That's why arc/MIG welding is so aptly suited to handymen...it's very
easy to get good penetration and a uniform, raised bead.
philgregson:
quote:
What about the aluminium monocoques that Audi and the like build - why don't they have a limited life?
Well, actually they do. You'll find Audi et al pour millions of tokens into metal bonding research, so it would be nice if they did get it right!
I don't know about Audi, but I know a lot of automotive manufacturers rely almost exclusively on adhesives for bonding AL bodies now.
I'm sick of listening to myself, so I'm sure you all are!
Cheers, Rorty.
"Faster than a speeding Pullet".
PLEASE DON'T U2U ME IF YOU WANT A QUICK RESPONSE. TRY EMAILING ME INSTEAD!
|
|
Alan B
|
posted on 23/2/03 at 05:24 PM |
|
|
quote: Originally posted by kingr
Phil - Although I make no representations to have any depth of knowledge about these things, my understanding was that Ali will fatigue if subjected
to flexing no matter how little, it will take longer with smaller movements, but it will happen. Steel on the other hand you could bend back and forth
within certain parameters (not massive admittedly, but significantly larger than you would want your chassis to have) indefinately, it's only when
you move outside of those parameters that it will fatigue. Hence the reason that, as far as I know, you can use a steel chassis for pretty much as
long as you wish (corrosion and wear aside) whereas using an ali chassis for an indefinite ammount of time would be inadviseable.
On the other hand I could be talking complete and total crap!
Please feel free to enlighten me.
Kingr
No, you are correct.
Fatigue is basically cycles of changing stress level as opposed to constant stress.
Steel has a level of stress (the fatigue limit) at which it will tolerate unlimited cycles. Ali, does not, and therefore has to be "lifed"
accordingly.
|
|