macbrew
|
posted on 21/5/03 at 08:29 PM |
|
|
Mig Welder
1st time in 8 months that I've spit the dummy - short story ... mig 90 packed up.
Went to machine mart and was about to buy one of the new clarke 135 (Red), was told by assistant that the blue ones are better because they still have
copper transformers and the new one's are Ali. The only other difference is cosmetic (and about £30).
Ended up with a 150 amp for the same price.
Just a thought if your looking for a Mig.
I beleived him anyway !!! or am I just a mug?
|
|
|
stephen_gusterson
|
posted on 21/5/03 at 09:44 PM |
|
|
cant see how the transformers would be different - all the ones I have ever seen are copper.
I have a 'red' welder. They are a tad better built and have hinged access for the wire reel rather than screwed on cover. I would have
thought if anythign the red one would have a 'better' transformer.
atb
steve
PS
my 100a welder can work 100% duty cos I fitted a fan inside it. If yours has no fan, its well worth fitting one - mine has never cut out thro heat.
|
|
MikeRJ
|
posted on 22/5/03 at 07:19 AM |
|
|
I bought a "Blue" welder from MM a few years ago, and some of them had copper windings and some aluminium (or so I was told).
The most usefull feature on mine is the ability to reverse the polarity to use gassless wire which makes welding outside far easier.
[EDIT] The assistant also told me that the "Red" welders were pretty much identical internaly, and that they were replacing the Blue
range which were to be discontinued. However, that was several years ago and they still sell both.
[Edited on 22/5/03 by MikeRJ]
|
|
macbrew
|
posted on 22/5/03 at 08:56 AM |
|
|
Yep got a fan, wheels, whistles & bells. Very happy with it.
100% duty, even with a fan, would be asking a lot especially at full power. Bad economics to make things that give 100% all the time, try running your
engine at full revs and see how long it lasts.
I would imagine that copper gives a higher duty cycle than Ali. cos of its higher temp. tolerance and I'm sure that temp. affects the
performance of the transformer (Eddy currents an all that ... Ahhh ... college days) otherwise why fit fans.
|
|
stephen_gusterson
|
posted on 22/5/03 at 09:25 AM |
|
|
If you take a look in your welder, you will see a rectifier assembly. This is on a heatsink plate. As I recall, this is the bit that gets hot. Fitting
a fan allows this to remain cooler, stopping the heat switch from tripping.
Its very common in electronics to blow air past heat sinks - it does not mean that the device is being over driven - jus that there is a 'heat
sump' effect that will cause failure if too much heat builds up. Using a fan keeps the device below the critical point of silicon failure. Any
power device needs a heat sink - fitting a fan raises the effectiveness of the heatsink.
Running a fan cooled welder for longer by keeping it cool wont break it - its the heat build up that threatens to do that!
atb
steve
|
|
MikeRJ
|
posted on 22/5/03 at 12:17 PM |
|
|
quote: Originally posted by stephen_gustersonRunning a fan cooled welder for longer by keeping it cool wont break it - its the heat build up
that threatens to do that!
I think macbrew was refering to the P=I^2R loss (copper loss) within the transformer windings. Blowing air past a transformer unfortunately
won't help cool the internal windings very much.
If properly designed, an aluminium transformer will have very little difference in efficiency over a copper one, the main difference being a cost
advantage and a size penalty for aluminium.
Irrespective, either type would be fine for home use.
|
|
stephen_gusterson
|
posted on 22/5/03 at 02:19 PM |
|
|
whatever losses there may be, my 15% duty rated unit has welded my car without on cutting out - even when I continuously welded the whole floor!
atb
steve
|
|
Danozeman
|
posted on 22/5/03 at 04:13 PM |
|
|
Ive got a sip 130 turbo mig with a fan in it. Dont know what the duty is. It had never cut out on me due to heat until the other day when i was
doing some quite heavy duty welding for about 45mins and it stopped just as i finished.
Its got the reverse polarity thing to for gasless welding..
What gas bottles u chaps using?? Pub bottles?? the little chuck away rip off ones?
|
|
Peteff
|
posted on 22/5/03 at 04:38 PM |
|
|
Product endorsement time.
I had a sip 130 for years. Put a few cars back on the road with that one. It started cutting out and feed problems so I bought a 170 erfi (german
make). It's been brilliant for the last 6 years and still going strong. Rotary controls on it much better for fine tuning. I use .8 wire and
energas big bottle 5% mix. Welds 20g right up to RSJ's. It has a proper Euro torch as well with bigger tips and shield, not the toy ones and
from the local supplier the parts are cheaper than MM and Draper. Also it takes a full size reel of wire which costs £10, not the sewing machine size
things you get from MM. The polarity reverses by swapping earth lead to another socket to run gasless but I've never used any. It has a duty
cycle of 65% on full power but I've never been able to test that on it. I've put foot long runs on girders and it never flinched so I
don't think I will ever tax it to its limit.
yours, Pete
yours, Pete
I went into the RSPCA office the other day. It was so small you could hardly swing a cat in there.
|
|
John
|
posted on 23/5/03 at 09:54 PM |
|
|
German Welder erfi
Pete,
I am looking for a decent welder myself. Can you advise where to get hold of the erfi models. Will the 170 connect to a 240v 13A socket.
John.
Working on a CVH 1.8 engined Locost. Hoping to use as much as possible of Sierra donor. £210 left.
|
|
stephen_gusterson
|
posted on 23/5/03 at 10:02 PM |
|
|
I bought some argon / co2 mix the other day to see how much better it was than co2 on its own.
ITS A HELL OF A LOT BETTER.!!!!!!!!
Less spatter, looks prettier and 'strikes' better.
Shame I did everything with co2 and put up with the crap for so long...
atb
steve
|
|
stephen_gusterson
|
posted on 23/5/03 at 10:04 PM |
|
|
if you want to buy a welder try
http://www.ebay.co.uk
and search on mig welder.
there are lots of new ones at decent prices.....stay away from the 80 quid 80 amp ones tho.......
|
|
Trev Borg
|
posted on 23/5/03 at 11:30 PM |
|
|
Mine's bigger than yours
I got a 185 turbo mig. Runs fron a 13 amp socket no probs.
The larger the welder, the better it seems to weld. Smoother wire flow ?.
The only difference i can think of, why an aluminium wound transformer would be inferior to a copper wound transformer, is that the copper has greater
current carrying capacity and a higher melting point. But saying that. I'm an electrical engineer working for a power supply company, and have
never heard of an aluminium wound transformer !
|
|
Peteff
|
posted on 24/5/03 at 10:15 AM |
|
|
I've searched for a UK Erfi dealer but I can't find a listing. Mine was from a local supplier called 3 Shires. They are good for
consumables, especially if you don't want a receipt . Steve, you live and learn. CO2 is good for thick stuff but 5% Argon mix is better for
the material we use. 10% for thin steel and pure argon for aluminium if your welder will do it. You might get away with a lower setting with the argon
mix as well.
yours, Pete.
yours, Pete
I went into the RSPCA office the other day. It was so small you could hardly swing a cat in there.
|
|
craig1410
|
posted on 24/5/03 at 04:22 PM |
|
|
Guys,
Interested in the comment about Argon-mix giving better results than CO2. I have found the exact opposite and I don't know why. I have tried the
Argon/CO2 mix bottles from Halfords and the pure CO2 from Halfords and the CO2 give nice shiny, smooth penetrated welds with just a hint of brown slag
in some of the corners. The argon mix was a nightmare and seems to run out really quick compared to the CO2.
I was using the same power and feed settings with both which may be wrong. Also, I found that the Argon-mix gas was producing a sort of
"plasma" glowing gas effect between the gas cup and weld site and it seemed to make the weld pool drop off the weld site a lot showering
the floor with sparks. Could my polarity be wrong or something? It makes a wierd noise like blowing over an open bottle top when using Argon mix but a
nice crackle when using CO2. Really weird!
My welder is a Clarke 120Amp with feed set at about 6 (max 10) and with power switches set to A, 3, Max or somethimes A, 2, Max. I'm welding 2mm
SHS tubing of the industrial contruction steel type (black coating) but I am running a file or grinder over the weld sites to get clean steel before
welding.
Any ideas?
Cheers,
Craig.
|
|
macbrew
|
posted on 24/5/03 at 06:03 PM |
|
|
I agree, I've tried the 5% Argon mix. Although it did not spit as much I was not happy with it and also found that it ran out much quicker than
CO2.
Must be using it wrong but I tried lots of settings with no joy.
I'll put up with a few burns using CO2 cos it's cheaper.
|
|
craig1410
|
posted on 24/5/03 at 06:13 PM |
|
|
Glad it's not just me...
One thing I did notice at one stage was that my gas cup had become "Live" which really screwed up the weld quality big time. This happened
because I had replaced the gas cup with one which was too short and had to pack it forward with washers. I didn't notice that my washers were
bridging the insulation between the gas cup thread and the cup itself. I realised something was very wrong when I kept fusing my gas cup to the
chassis when I was tack welding acute angles. I even blew the circuit breaker in my garage at one point which left me stumbling around in the dark
trying to find the door...
Anyway, watch out for that one!
Cheers,
Craig.
|
|
Peteff
|
posted on 24/5/03 at 06:36 PM |
|
|
Live shroud.
The gas shroud can fill up with spatter and arc across to the weld tip if you don't ream it out with a screwdriver or similar occasionally. This
can cause the tip to melt in extreme cases welding it to the wire or fusing it into the gun. I used to get this using pub gas in my old welder so I
invested in some 5% argon and would only use the pub gas in emergencies now. The euro connector type has a push on tip with a built in insulated
sleeve and is much easier to maintain. The only way you can use the gas quicker is by turning the regulator up on my welder.
yours, Pete
I went into the RSPCA office the other day. It was so small you could hardly swing a cat in there.
|
|
David Jenkins
|
posted on 24/5/03 at 08:23 PM |
|
|
re: argon + co2 mix
This mix is all I've ever used - but I get mine from BOC, not Halfords!
I work on the principle that I need everything in my favour to make a good weld - good gas, electronic insert in my welding helmet, making
really sure that the metal I'm welding is totally grease & oil free, and so on.
Paranoid, moi?
DJ
|
|
craig1410
|
posted on 24/5/03 at 10:02 PM |
|
|
Peteff,
Yes I know what you mean but in my case it was actually the steel washers that I'd packed the shroud out with. I replaced the last one with a
fibre washer and it's fine now. I do ream out the shroud regularly when welding although I find that a gentle tap against the workpiece or a rub
with a wire brush is all that's required most times.
David,
I agree that BOC gas is most likely far superior to the Halfords stuff, mainly due to the better quality regulator. I may well hire a bottle when
I'm ready to seam weld the chassis and put in the floor. However, I'd be well annoyed if I hired a bottle only to find that I got the same
poor results that I get with Halfords Argomix.
Hopefully someone can suggest a reason why I was getting the poor results as described in my earlier post.
Cheers both,
Craig.
|
|
Peteff
|
posted on 27/5/03 at 05:51 PM |
|
|
This was done with the power set to about 1/3, wire speed 2 (goes to 10) and gas at about 10cu ft per hour. Settings vary for different welders and
people may weld faster or slower than me. The tube is 20g and the plate is 3mm. The gas is 5% argon co2 mix, energas supplier.
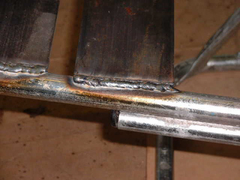 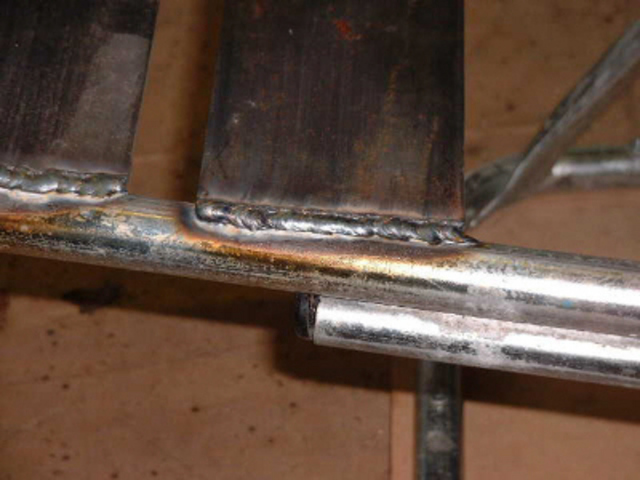 Rescued attachment weld.JPG
yours, Pete
I went into the RSPCA office the other day. It was so small you could hardly swing a cat in there.
|
|
Danozeman
|
posted on 27/5/03 at 05:58 PM |
|
|
Gas bottles
What gas bottles does every one use??
|
|
craig1410
|
posted on 27/5/03 at 08:59 PM |
|
|
Peteff,
Here is a sample of a weld done using Halfords pure CO2 with 2mm steel gearbox bracket being welded to a 2mm (not 16swg) steel 25x25mm tube. Note that
this weld was done very quickly without any great care taken and I used full power (120A Clarke) with 5/10 wire feed and gas flow on full. I've
no idea how much flow you get from one of these Halfords type regulators...
Notice the little spatter particles. This is the only problem I find with using CO2 but given that I have a welder which isn't really big enough
the extra penetration I get with the CO2 works better IMHO. Note, I am by no means a good welder but I am happy with the strength of my welding
process even if it's not the prettiest. I just can't get any joy with Argon mix for reasons discussed in another thread on the subject.
Cheers,
Craig.

|
|
billy
|
posted on 28/5/03 at 09:49 PM |
|
|
wow, looks like bird shite to me.....lol....
luego-lo-cost finished,vauxhall 16v 2.0,twin 45s de-dion rear set up
|
|
craig1410
|
posted on 28/5/03 at 09:53 PM |
|
|
Billy,
I know it's not the best but you must have some wierd birds down your neck of the woods!
Cheers,
Craig.
|
|