jcduroc
|
posted on 14/12/03 at 06:32 PM |
|
|
RC's Chassis mods
MOD’S TO RC’s LOCOST CHASSIS
The chassis is intended to:
• Support the weight of the various organs: Bodywork, engine & gearbox, differential & transmission, steering column & rack, pedal box,
battery, petrol tank and seats & passengers;
• Resist the loads derived from the relative movements of the body & chassis versus the suspensions (roll, pitch and yaw);
• Provide attachement points for the bodywork and several other items such as the seat belts which induce occasional shear loads.
The weight of the several items referred to in a) induces mainly bending loads on the structures supporting them, while the movements of the
suspensions induce all kinds of loads; amongs those suspension movements roll is probably the most important to take care of because if the chassis
has the torsional stiffness to resist the opposing loads created in roll it will resist all other suspension loads equally well.
In the light of the above considerations let’s have a critical look at “the book” chassis design.
1. The front unparallel unequal length double wishbones is a 5-link system (5th is the track rod) demanding the same number of attachement points on
each side, plus one for the coilover/shocks top-eye. In the “book” design the four brackets to which the two wishbones attach are welded to the face
of 1 inch square tubes; being 2 inches wide these brackets leave ½ inch unattached at each side of the tube.
Given that the standard bushes (Spitfire) are 36 mm long I would prefer to use 40 mm square tube to attach the wishbone pivots directly (see Fig. 1).
These tubes would replace LD and E (lower part of chassis) and LC and the joints of S and T with FU1 and FU2 respectively in the upper part of the
chassis.
This means that the front end of the chassis would no longer be in the same plane as D1 and A1 (ride height) but a bit higher; F1 should go up to meet
the “new” E 40 mm tube at its position and so forth (see Fig- 2).
2. In the “book” design the steering rack attaches to a rather “flimsy” (32 x 3 mm) steel strip mount. As there is an obviously missing tube from LB
LC F1 to FU1 J1 S a new 1 inch square tube will support the steering rack, replacing the “book” mount (see Fig 3).
3. The biggest loads induced by the suspensions movements occur at the coilover/shocks top attachements so these should be given equal if not bigger
attention than those referred in 1.; we shall explore its size and position later.
4. At the rear end (live axle as per “the book”) the 4 trailing arms (2 at each side) attach to similar brackets welded to tubes M1 and M2. My
criticism about the front wishbones mounting brackets equally apply here, reinforced by the fact that the trailing arms are bound to twist by the
kynetics of the suspension itself. My thinking is that the trailing arms must have Rose joints in the chassis mountings (as Jim McSorley did) and
bushes in the axle mountings; therefore the brackets at M1 and M2 could be replaced by 40 mm square tube. Note that M1 and M2 tubes are almost always
subject to twisting moments due to the action of the live axle; its size and position, considering K1[2], K3[4], B1[2] and A1[2] and the lack of
triangulation in B1 "e" O3 K3 [B2  f  O3  K4], slould be given a deep thought.
5. Back to the front end it has already been referred (by Cymtrick other than me) that there must be 2 tubes joining the ends of LD to the ends of S
and T at LC.
6. The front lower “bay” LD | F1 | E | F2 must also be conveniently triangulated, either by tubes or by a 16 or 18 SWG welded steel sheet. The choice
might be dependent of the configuration of the lower engine bay tubes (F1[2] and G1[2]).
7. The “book” engine mountings induce bending loads at the (+/-) middle of tubes F1[2] and G1[2]. The weight of the engine could be better spread into
the chassis if it were loaded into a vertical tube, going from where the “book” steel sheet welds into G1[2] to the middle of J1[2]; another tube
would come from here to the middle of F1[2] and a third one from here to the first point (completing a triangle); TR1[2] would then be replaced by two
tubes.
This way G1[2] must no longer be unique and might be joining C where it meets H and “l” (is there any reason not to?).
8. At the top of the engine bay, as I have pointed out in a post and Cymtrick agrees, R may be replaced by two Y braces (one at each side)
conveniently shaped to clear the engine and its ancillaries; if this is not possible one or both can be made removable (bolt attached).
9. Other than supporting the front of the scuttle (how many kgs?) I can see no utility for the P tube; can anyone enlighten me?
10. As far as I can see TR5[6] and H, both from A1[2] | D1[2] to N1[2] | J1[2] are redundant. If B2 is placed accordingly to the intersection of K1[2]
with A1[2] and the tranny tunnel “k” tubes moved what is H doing there?
11. Instead isn’t there a tube missing, joining the tops of TR5 and TR6? Even if it is curved to clear the driver’s (and passenger’s) knees?
12. The tranny tunnel is another very controvertial item in this chassis design. According to Cymtrick it adds little or no stiffness to the chassis.
However, if G1[2] is a straight path to “l”[m] and the tunnel is made of 1 in tube, an extra tube joins lower ends of M1[2] and the foremost “k” tubes
and B1 joins the lower ends of M1[2] and the rearmost “k” tubes (O3 moving forward) what would be the increase in stiffness?
These a few thoughts that occurred to me as I was starting to “finalize” the sketches to start building my first “book” chassis since the tubes were
delivered last Friday and the MDF platform will arrive next week.
Any comment will be welcome and very much appreciated.
JCM
|
|
|
Ben_Copeland
|
posted on 14/12/03 at 10:16 PM |
|
|
Hmmm cant be bothered to read it all... so i'll just nod quietly     
Ben
Locost Map on Google Maps
Z20LET Astra Turbo, into a Haynes
Roadster
Enter Your Details Here
http://www.facebook.com/EquinoxProducts for all your bodywork needs!
|
|
JohnN
|
posted on 15/12/03 at 12:43 AM |
|
|
Hi,
Takes a bit of reading, & cross referencing with the book diagram.
Not sure I agree with point 10. Tr5 & 6 are often beefed up - Luego, for example, so to omit then and H as well....... mmm
Are these ideas based on any frame analysis? I've seen other suggestions, some of which you repeat, but not point 10.
I, personally have doubled up the chassis members here, not the least, for better side impact protection - see picture
JohnN
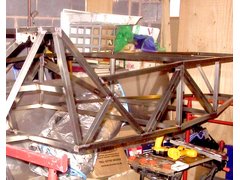  Rescued attachment chassis7.jpg
|
|
jcduroc
|
posted on 15/12/03 at 12:05 PM |
|
|
quote: Originally posted by JohnN
Not sure I agree with point 10. Tr5 & 6 are often beefed up - Luego, for example, so to omit then and H as well....... mmm
JohnN
I think that I was not clear in point 10; I should have written "either TR5 or H, one of them is redundant".
No way I would eliminate both.
Cheers
João Matoso
JCM
|
|
cymtriks
|
posted on 17/12/03 at 01:34 PM |
|
|
My thoughts...
1) There is no reason not to do this but it may be easier to use 1x1.5 inch tube to fit into the existing design better. The 1.5 inch face would be
aligned with tube J1 and J2
2) Yes. Adding this diagonal is in my mods but I did not suggest that it could also replace the rack mounts. A good idea
3) Yes. But the length of J between FU and LA/B is very short so will not bend much.
4) I've never really thought about this but a quich read of your points makes sense.
5)As in my mods, a V brace at the front.
6) I suggest a welded in panel between tubes E and LD. This is very stiff and helps with the aerodynamics of the underside of the car.
7) Yes. A good idea for bigger engines. But engine bell housing and starter motor may prevent tubes G1 and G2 from being moved. The Book does mention
this.
8) Double Y braces are better than two short R tubes as on the Westfld7. The double long R tubes on the Caterhm7 are best but are difficult to fit
around the back of an engine. The double Y brace will clear most engines and is very stiff.
9) P helps to brace J1 and J2 but see my answer to 11.
10) Yes. But change D1 and D2 to match and remember that the bodywork side panels will change if D1 and D2 are changed to meet the new B2 position.
11) A curved tube isn't very stiff but a structural dash board would be a good idea. This could make tube P redundant. Check the Caterhm7 design
which has a structural dash.
12) I didn't say the tunnel was useless! It is very inefficent and the Book tubes do not do much. Turning the tunnel into a fully boxed 18 gauge
welded structure greatly improves it's contribution to stiffness. This does restrict tunnel access though. Access holes may be required for
assembly. A hole will also be required for the gearlever and handbrake.
|
|
pbura
|
posted on 19/12/03 at 06:45 AM |
|
|
My 2 cents
1. Agreed with Cymtriks that 1"X1.5" tube would be the most direct way to have a better mounting surface. As I am not aware of chassis
failures in this area, though, I would not go far out of my way to do it (such as having to buy a 20' length for that purpose only).
2. Yes, I think the rack mounting looks flimsy, too. I would rank the rack position as being more important than bisecting FU1 | J1 | S exactly,
though.
3. In this case I would say that shock position outranks strength considerations. I've seen several cars with shock mounting brackets that
extend far away from J, apparently with no problems.
4. With Rose joints in the chassis mountings (I am doing this, too, to save space), the brackets on M can be narrower, and so better supported. As
for the lack of triangulation noted, I'm considering making O3 diagonal from e | O1 to B1 | K3.
Weren't you going to build IRS?
5. No question about this one.
6. I like Cymtriks' suggestion for a panel here.
7. This is a good idea, if everything will fit.
8. Thanks to Cymtriks for spelling out the preferred order for selecting these.
9. I see P as being fairly important for anchoring the transmission tunnel to the whole structure.
10. Alternatively, K1 could be raised to intersect with H | A1, so that TR5 could be tossed. I'd like to see M1, K1, and N1 all intersect, too.
Would have to draw this up to see how it looks. This is not a big concern, as we're probably only talking about a pound of metal here.
11. FWIW, I'm making my own scuttle and will have a hoop here.
12. I like the boxed tunnel, but want to use aluminum, so will be taping and riveting.
Thanks for posting your questions, João. Many good points covered that I hadn't thought much about.
Best of luck!
Pete
|
|
jcduroc
|
posted on 20/12/03 at 03:48 PM |
|
|
quote: Originally posted by pbura
1. Agreed with Cymtriks that 1"X1.5" tube would be the most direct way to have a better mounting surface. As I am not aware of chassis
failures in this area, though, I would not go far out of my way to do it (such as having to buy a 20' length for that purpose only).
In fact I bought a 6 m length of 40 x 40 x 1.5 but it can be used on the chassis jig as well. Anyway the weight difference between 1 x 1.5 " and
40 x 40 is not much.
quote: Originally posted by pbura
2. Yes, I think the rack mounting looks flimsy, too. I would rank the rack position as being more important than bisecting FU1 | J1 | S exactly,
though.
Agreed
quote: Originally posted by pbura
3. In this case I would say that shock position outranks strength considerations. I've seen several cars with shock mounting brackets that
extend far away from J, apparently with no problems.
So did I; matter for touhght...
quote: Originally posted by pbura
4. With Rose joints in the chassis mountings (I am doing this, too, to save space), the brackets on M can be narrower, and so better supported. As
for the lack of triangulation noted, I'm considering making O3 diagonal from e | O1 to B1 | K3.
There must be a way to birdcage that area of the chassis and yours might well be one; matter for thinking...
quote: Originally posted by pbura
Weren't you going to build IRS?
Yes I am, but using someone else's workshop and tools obliges me to help the owner to build another Locost, live axle in this case (based on a
Mk II Escort)
quote: Originally posted by pbura
6. I like Cymtriks' suggestion for a panel here.
I think we all agree on this.
quote: Originally posted by pbura
7. This is a good idea, if everything will fit.
First issue: good support, spreading the loads along the chassis;
Second: Multi-engine purpose.
Third: get the engine as far back as possible (see Mark Allanson and Wyn Edawards)
quote: Originally posted by pbura
8. Thanks to Cymtriks for spelling out the preferred order for selecting these.
Consensual.
quote: Originally posted by pbura
9. I see P as being fairly important for anchoring the transmission tunnel to the whole structure.
11. FWIW, I'm making my own scuttle and will have a hoop here.
I'll be making a structural dash; the question is (at least for me) wether it will anchor to the tunnel as well as to Q eliminating P.
quote: Originally posted by pbura
10. Alternatively, K1 could be raised to intersect with H | A1, so that TR5 could be tossed. I'd like to see M1, K1, and N1 all intersect, too.
Would have to draw this up to see how it looks. This is not a big concern, as we're probably only talking about a pound of metal here.
Let's share this points' ideas (you too, Cymtrick).
quote: Originally posted by pbura
12. I like the boxed tunnel, but want to use aluminum, so will be taping and riveting.
For the first build I'll be using tube (20 mm OD) bracing; we'll see afterwards.
quote: Originally posted by pbura
Thanks for posting your questions, João. Many good points covered that I hadn't thought much about.
Best of luck!
Pete
Thank you for sharing your ideas.
João
JCM
|
|
Tigers
|
posted on 22/12/03 at 10:20 AM |
|
|
Sorry for stupid question but what do you mean by "structural dash"? Is there any pictures?
|
|
cymtriks
|
posted on 22/12/03 at 12:08 PM |
|
|
structural dash
By "structural dash" I mean a dashboard structure that is designed to carry chassis loads. A single bent tube around the top of the
scuttle/dash will not be very good at this. What you need is a structure as follows.
A top tube around the outer edge of the dash which starts and ends at the chassis side top tubes. A second tube then forms the bottom of the dash and
also starts and ends at or close to the chassis side top tubes. A steel sheet is then welded to join the two tubes all the way across the car. Cut
holes in the sheet for instruments and switches.
I think that Catrham use a structural dash but a better example can be found on the Lotus 23.
|
|
Tigers
|
posted on 22/12/03 at 02:13 PM |
|
|
Thanx, got it now.
|
|
|