heyzee
|
posted on 1/1/04 at 07:28 PM |
|
|
the floor
is it best to weld a steel floor in and have you guys all used 1.6mm whitch i imagine will have to be cut with the grinder or have you used thinner
plate.allso if i were to use alloy what is the recomended thickness will 2 mm be o.k.
|
|
|
Mark Allanson
|
posted on 1/1/04 at 07:53 PM |
|
|
I used 18g mild steel with 13mm ERW strengtheners set at angles so there would be no harmonics from the engine vibration
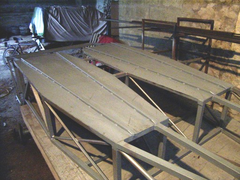  Rescued attachment Floor2.jpg
If you can keep you head, whilst all others around you are losing theirs, you are not fully aware of the situation
|
|
JoelP
|
posted on 1/1/04 at 09:23 PM |
|
|
doing it marks way is a good way to avoid the 'boing' effect, where the floor boings when you stand on it. i used 16g welded, with a few
bars across it for the seat runners, and it boings loads.
|
|
Mark Allanson
|
posted on 1/1/04 at 09:38 PM |
|
|
Its not so much the 'boing' effect, but the zinging rasp as thin steel gets in sympathy with the engine rpm's that I wanted to avoid
If you can keep you head, whilst all others around you are losing theirs, you are not fully aware of the situation
|
|
eddymcclements
|
posted on 2/1/04 at 09:34 AM |
|
|
I took a different approach - 2mm aluminium, bonded with Sikaflex 252 and rivetted every inch. Very little "boing" when you step into the
car. Of course I may find myself sitting on the tarmac if all the rivets pop out, but I personally believe that the Sikaflex alone would hold the
floor on.

|
|
suparuss
|
posted on 2/1/04 at 09:59 AM |
|
|
you did all those rivets with one of those annoying little things?!?!?! id have invested in an air riveter, or at least lazy tong. but then, i am
lazy!
RUss.
|
|
eddymcclements
|
posted on 2/1/04 at 11:36 AM |
|
|
Ahh....but you haven't seen my forearms, have you?
Eddy
|
|
stephen_gusterson
|
posted on 2/1/04 at 01:00 PM |
|
|
eddy - that looks a nice job......do you think you neeeded ALL those rivets!
I think they use less on ships and aircraft!
atb
steve
[Edited on 2/1/04 by stephen_gusterson]
|
|
Mix
|
posted on 2/1/04 at 04:58 PM |
|
|
Actually Steve that's about the right pitch for aircraft 
Mick
|
|
DaveFJ
|
posted on 2/1/04 at 05:09 PM |
|
|
Actually not so sure if it is the right pitch for aircraft - looks a lot more than 2.5D to me (2.5 x the diameter of the rivet)
personally I have gone for a staggered line but with 3.2mm rivets with a spacing of 20mm (contersunk along edges to allow easier body fitment)
I approximate I have used 650 rivets on the floor panels alone - and yes all with a small hand riveter. - I have used 'decent' aircraft
standard blind rivets though....
[Edited on 2/1/04 by protofj]
Dave
"In Support of Help the Heroes" - Always
|
|
Mark Allanson
|
posted on 2/1/04 at 05:34 PM |
|
|
If we ever meet, remind me not to shake hands!!!
If you can keep you head, whilst all others around you are losing theirs, you are not fully aware of the situation
|
|
stephen_gusterson
|
posted on 2/1/04 at 08:27 PM |
|
|
why do aircraft need so many rivets?
atb
steve
have I started summat here ?
|
|
Mix
|
posted on 3/1/04 at 10:02 AM |
|
|
Why do aircraft need so many rivets??
To fill up all the holes 
Mick
|
|
Rorty
|
posted on 6/1/04 at 04:04 AM |
|
|
To keep people in jobs.
Cheers, Rorty.
"Faster than a speeding Pullet".
PLEASE DON'T U2U ME IF YOU WANT A QUICK RESPONSE. TRY EMAILING ME INSTEAD!
|
|
suparuss
|
posted on 6/1/04 at 06:31 AM |
|
|
lol, they are stressed skin construction so th skin needs connecting very well to the frame.
where do you get good rivets from? can i ask me local trade counter for aircraft ones? that chassis does look very nice an proffesional btw
Cheers,
Russ.
|
|
Mix
|
posted on 6/1/04 at 09:01 AM |
|
|
Aircraft rivets
To be honest, the last thing you need are aircraft quality rivets, (especially if you intend to buy them).
Standard (aircraft) pop rivets look exactly the same as those you buy at motor factors but will cost many times the price, (all to do with
'quality control and traceability).
Other blind fasteners used on aircraft, (eg. Cherry rivets) are really designed to be fitted using powered tooling. You can fit them by hand but I
wouldn't advise it in the quantities we are talking about. Again cost will be a big issue.
As for recommended rivet spacing, (pitch).
About 8 times the diameter of the rivet is the norm for stressed skin in aircraft, but this is partly because the materials used tend to be fairly
thin, (.8mm - 1.2mm).
For a 2-3mm floor attached to a steel chassis the pitch can be increased, (I will go for about 16 times diameter).
Steve
Main reason for all those rivets is the thin gauge of the materials used in aircraft construction to save weight.
Mick
|
|
eddymcclements
|
posted on 6/1/04 at 10:36 AM |
|
|
I used 4mm sealed-end aluminium rivets from RSK Supplies, Halifax (I was working over that side of the country at the time).
I didn't know about the 8 x diameter figure - this obviously gives 32mm spacing, but I don't think that 25mm is unreasonable. I used
Clecos to hold the floor in alignment while working - it was a couple of years ago now, but I don't recall it being too much of a chore.
Suparuss - no wonder it looks like a professional chassis...it came from ST Motorsport and has a really good powder-coat finish.
Cheers,
Eddy
|
|