Neville Jones
|
posted on 20/7/10 at 04:40 PM |
|
|
I recall that this design flaw was pointed out some time ago, and the pointer got a right slagging off from the mfrs for it.......
Anyone with the welded steering arms similar to the older RD items and the other sellers, should rid themselves pronto. It's only a matter of
time....
Cheers,
nev.
|
|
|
PuppiesBalls
|
posted on 30/7/10 at 05:36 PM |
|
|
quote: Originally posted by ghostrain
Seems the right moment to advise that Rally Design has advised a possible welding failure on the Raceleda/RMD style of ally upright. Rally Design have
recently changed the steering arm away from the original fabricated arm(welded) to a drop forged design,although the failure has only occured on 2
vehicles with no damage they have made the offer to issue free of charge replacement arms,this offer applies irrespective of whether the upright
assembly was purchased from RD or another retailer. All purchasers will be advised by post but as a discussion thread about uprights was started it
seemed a good moment to advise the problem on this forum.This applies to all gold plated fabricated arms,black painted drop forged arms are to the
latest spec and are not a problem.If you know of anybody who has this front upright assembly perhaps you could let them know. The problem appears to
have occured on only 2 vehicles out of 178 uprights sold but as we have the replacement arms it seems sensible to make the change.
I have recently made quite a purchased from rally design 2 x alloy hubs, 2 bearing sets and also a set of cortina aluminium uprights,
I called MNR today hoping to be able to get hold of some adaptors (pic below) & was advised that the rally design ones are chinese copies and wont
be up for the job!..
Im quite worried now as im planning to use the car on the road and track, its being powered by a 1.8l turbo which will make around 350 bph and I dont
want it to let go.
Can you tell me if these uprights are safe to use?
Here is the adaptors im trying to get hold of so I can use rod ends on my uprights if anyone can help...

|
|
ghostrain
|
posted on 31/7/10 at 12:08 PM |
|
|
Using rod ends at top of uprights
Am I correct that the purpose of the above adaptors is to be able to fit rod ends,fitted at right angles to the upright assembly. If that is the case
I personally have not been happy about the use of rod ends in this mode of use,the failure load of the rod end is considerably reduced and rod ends
were never designed to take load in this plane,for that reason we would always recommend the proven route of transit drag link joints. I was involved
in the design of the front suspension by the leading club race car constructor in th uk and on the prototype both front rod ends failed at the point
where the stub joins the housing. Rod Ends have a relatively low angle of misalingnment,about 11 degrees on average,it is easy to lock out the
bearing. Ironically the cheaper pressed construction joints have a higher angle of misalignment than the normal expensive joints,there are hi-angle
joints available. If employing a rod end in this mode it is most important to loci the movement of the suspension on max bump and droop without
shocker attached to make sure no lock out occurs. I am surprised MNR would say that Rally Design uprights are not up to the job,under what test
results can they make that statement?Are you sure you did not misunderstand their comments. As for the comment about chinese parts then stop using
your VW,Honda,TRW or ZF parts because RD use the same OEM supplier as they do,sorry but that is a fact of life that most of the parts we now use come
from China and it is sad to say that quality and reliability is the better for it...these asian manufacturers have quality control
procedures,equipment and personnel that is the envy of most uk small manufacturers and the bigger uk suppliers are just not interested in this
work.
The latest RD uprights now use drop forged steering arms,the preferable method of manufacture.
Hope that helps
|
PLEASE NOTE: This user is a trader who has not signed up for the LocostBuilders registration scheme. If this post is advertising a commercial product or service, please report it by clicking here.
|
ghostrain
|
posted on 31/7/10 at 09:33 PM |
|
|
Axial Loading of Rod Ends
I did some further research on my own posting and found that the max axial load is according to the respected aurora website 10% of the radial load ie
for a 12000 lb radial rod end the maximum axial load is 1200 lb...aurora state that this load should be considered failure load with no safety
factor....my recommendation is that you use rod ends of minimum 18mm(like the transit joint) or 3/4 unf and with the max angle of misalignment
available.
|
PLEASE NOTE: This user is a trader who has not signed up for the LocostBuilders registration scheme. If this post is advertising a commercial product or service, please report it by clicking here.
|
PuppiesBalls
|
posted on 31/7/10 at 10:24 PM |
|
|
The 10% axial load if for a 3 piece rod end, its 15% allowable for the 2 peice rod end which Is what im using.
Also you reccomend the 3/4" rod end which according to the aurora website is rated to 10900lbs of force, The rod ends I have chosen are £42 EACH
& are rated to over 31,000 lbs force even though there only half inch bore & 5/8 unf thread.
A friend of mine is running the same spec, however slightly smaller rod ends (1/2" bore & 1/2" unf) which are rated to just over
20,000 lbs force and they even though he races it competitively & has even managed to crash into a tree before which destroyed the rhs suspension
& wishbone, the top rod end was still fine, He has also had an aluminium upright 'let go' on him.
Thanks for you concearn however I'm pretty confidient that the rod ends will be up for the job, I am however still concearned with the uprights
as you havent answered the question-
Will they be safe to use or not ?
[Edited on 31/7/10 by PuppiesBalls]
|
|
ghostrain
|
posted on 1/8/10 at 11:58 AM |
|
|
I assume you have the RMD ally uprights,please confirm?You obviously are keen to have a black-white decision on use of these uprights. If the car has
only 750kg weight there must be many vehicles out there using RD uprights who are heavier than that,150 pairs in use and no upright failures says all
but the 350 hp is more powerful than the average that these guys will be using,that's all about how hard you intend to drive the
vehicle,especially on bad surfaces.
Out of interest if you decide against the RD uprights what are your alternatives?
With regard to the safety question have you asked your rod end supplier with the same parameters and clearly explaining the mode you are using those
rod ends whether he considers the rod end to be safe? On the race car I spoke of earlier we ended up using 1" rod ends with lock in ball,real
agricultural joints but with lots of metal at the point where the stem joins the housing...my preference is for 2 piece rod ends,using low carbon
steel rather than chrome moly steel ....the former tends to bend the latter just fails with no warning.
|
PLEASE NOTE: This user is a trader who has not signed up for the LocostBuilders registration scheme. If this post is advertising a commercial product or service, please report it by clicking here.
|
PuppiesBalls
|
posted on 1/8/10 at 01:53 PM |
|
|
Yep I am using the RMD Aluminium uprights (which I purchased from you guys about 2 weeks ago)
Yes I was hoping to get a yes or no
Regarding how hard I am going to drive it, I take car of all my belongings as so if its a crap road surface I will slow down, I dodge & swerve as
many pot holes as possible but its not possible to miss them all, all the time
Alternative to RD uprights are Stiltec Racing Billit uprights, or a set or westfeild ally uprights.
|
|
ghostrain
|
posted on 2/8/10 at 11:43 AM |
|
|
Looking at the F.E.A.
Tensile strength of 6082-T6 billet aluminium is 310 MPa. Tensile strength for heat treated (important) LM25 cast aluminium is 315MPa. So in theory
the billet version is slightly weaker.
MNR is giving a figure of 340MPA, not sure how they acheive that because I thought their uprights were cast heat treated LM25 same as Rally Design.
I looked up the F.E.A. testing of the RMD upright. A 600Kg car with 50/50 weight distribution, 3G bump load and 2G lateral load. Peak load on the
upright was revealed as 105MPa.
All of the failures of aluminium uprights that we know of were from the original batch of Raceleda castings. We rejected most of these castings for
sale at Rally Design on visual appearance (they were very poor quality with cavities).
I must say that some of the ideas that Raceleda had were to my eyes positively dangerous, he drilled steering arms to lighten them and removed much of
the side of cast brake disc bells to reduce weight. All without any form of testing, no wonder he ceased trading!
2g Lateral
3g Bump
3g Bump2

|
PLEASE NOTE: This user is a trader who has not signed up for the LocostBuilders registration scheme. If this post is advertising a commercial product or service, please report it by clicking here.
|
PuppiesBalls
|
posted on 2/8/10 at 12:02 PM |
|
|
Thanks for that re-assurance, I was speaking Micheal Coombs(the bloke who done this FEA) aswell and im confidient that these uprights are top notch
now, My apologies for the questioning, Just got worried after speaking to MNR!

|
|
Doctor Derek Doctors
|
posted on 15/11/10 at 07:02 PM |
|
|
If you have a blank sheet and can have anything you want why on earth are you considering scabby old Ford/Mazda/Triumph bits?
Upright design is pretty easy, you set your geometry, choose your bearing, position your caliper and then join the dots.
Its not the withcraft that people make it out to be... if anything its easier than trying to make existing OEM uprights fit new suspension.
|
NOTE:This user is registered as a LocostBuilders trader and may offer commercial services to other users
|
moss
|
posted on 4/12/10 at 04:54 PM |
|
|
Would vw beetle be any good
http://www.machine7.com/product.php?xProd=877&xSec=475
|
|
GRRR
|
posted on 9/2/11 at 09:35 AM |
|
|
Peugeot 306 uprights look ok, they would take a mushroom adaptor similar to sierra ones thus allowing you to change the height between top and bottom
pivot points to suit application, and the lower ball joint is bolt on rather than part of the 306's lower wishbone. Cheap on ebay too.
In terms of designing your own, the MK MIDI ones look good but maybe the cost of having the parts laser cut and professionally welded together could
be prohibitive.
|
|
ChrisLeary
|
posted on 23/2/11 at 09:50 PM |
|
|
I've got a set of restored Cortina mk3 uprights and calipers for sale.
Chris.
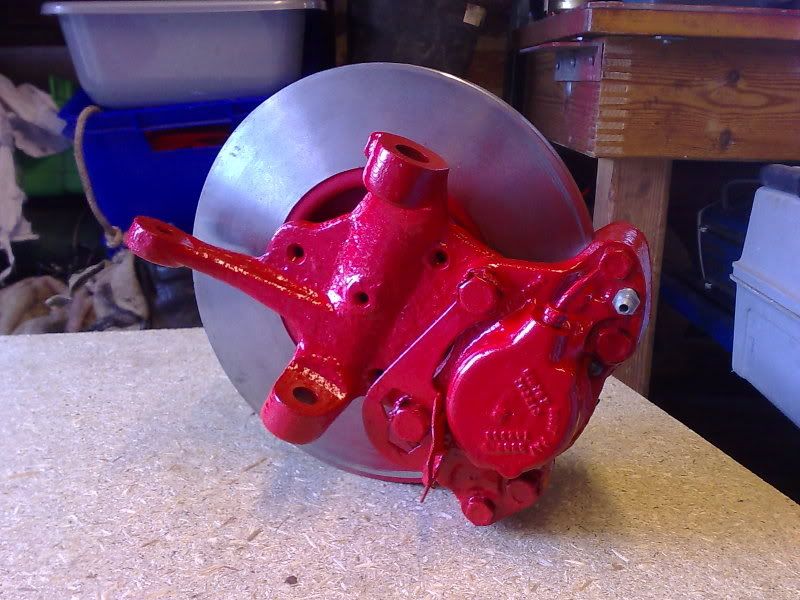
|
|
Bare
|
posted on 26/2/11 at 04:34 PM |
|
|
nice.. except for the paint :-)
|
|
ChrisLeary
|
posted on 26/2/11 at 05:55 PM |
|
|
Cheers, personally I think they look awesome, the picture doesn't really do them justice...
|
|
alfas
|
posted on 26/2/11 at 06:41 PM |
|
|
i understand as "restored" that the caliper has been seperated from the upright, both painted singulary, calipers flushed and new seals
fitted and than bolted back to the upright using new, galvanized bolts, or even better the caliper disassembled (both halfs split) and assembled with
using new, galvanized bolts.
|
|
ChrisLeary
|
posted on 27/2/11 at 11:07 AM |
|
|
quote: Originally posted by alfas
i understand as "restored" that the caliper has been seperated from the upright, both painted singulary, calipers flushed and new seals
fitted and than bolted back to the upright using new, galvanized bolts, or even better the caliper disassembled (both halfs split) and assembled with
using new, galvanized bolts.
Yes both calipers have been 'Fully Restored.' And yes, both calipers were fully dissabled (both halfs split), cleaned, re-assembled,
fitted with new seals, flushed through, filled with transit (or corrosion preventative oil if you don't know) and then they were painted. Once
the paint had cured they were fitted back to the already painted uprights...
To be fair, I thought this was a reasonably friendly forum, but I get the impression that some people think they are better than others.
Alfas, before you assume that people don't complete work to your, obviously very high, standards, maybe get to know them first. I'm an
aircraft technician in the RAF. On a daily basis I disassemble and re-assemble components for the most modern aircraft platform in the RAF. And in all
honesty, I feel this fully qualifies me to 'Restore' a set of Mk3 Cortina Calipers. If you've done this job youself, Alfas,
you'll know just how simple a job this is.
Chris
|
|
scootz
|
posted on 27/2/11 at 11:10 AM |
|
|
You tell 'em Chris!
It's Evolution Baby!
|
|
alfas
|
posted on 27/2/11 at 06:44 PM |
|
|
i´ve seen RAF engineers choosing a RobinHood kit (which already indicates a lot for me) and the result was a even more worse than the typical
robin-hood....so working with RAF does not automaticaly mean a high level of skills or whatever. its a job like any other job.
overpainting bolts which could be easily replaced by new ones says also a lot (to me).
anyway...each to his own!!!
i´m not here to critisize your skills or explain my high level of demands. i´m telling my opinion...very often not in a diplomatic way, otherwise i
would have gone into politics. my opinions come out straight away, therefore often sound a bit harsh. but opinion is opinion.
now to Rallydesign:
"...was advised that the rally design ones are chinese copies and wont be up for the job"
you are wondering why RD´s parts are so cheap and often crap? the answer could be found above.
save once, buy twice!!!
[Edited on 27/2/11 by alfas]
|
|
ChrisLeary
|
posted on 28/2/11 at 09:10 AM |
|
|
quote: Originally posted by alfas
i´ve seen RAF engineers choosing a RobinHood kit (which already indicates a lot for me) and the result was a even more worse than the typical
robin-hood....so working with RAF does not automaticaly mean a high level of skills or whatever. its a job like any other job.
overpainting bolts which could be easily replaced by new ones says also a lot (to me).
anyway...each to his own!!!
i´m not here to critisize your skills or explain my high level of demands. i´m telling my opinion...very often not in a diplomatic way, otherwise i
would have gone into politics. my opinions come out straight away, therefore often sound a bit harsh. but opinion is opinion.
I completely agree that being in the RAF does not automatically indicate a high level of workmanship, but like I said in my last post, you don't
even know me, you know nothing about my job or the work I do.
Well done to you, you know one example of an RAF engineer doing a bad job on a kit, which lets be honest, was probably his first kit. If you think
that this is a fair opinion of enginnering in the RAF you are very much mistaken... To be honest, your opinion about fitting new bolts is very much
your opinion and not an engineering need, if you knew anything about engineering, you'd understand that not all bolts that are removed need to
be replaced. Just because you may think (in your opinion) fitting new bolts looks better, they will not do the job any better if the old bolts are not
damaged.
|
|
alfas
|
posted on 28/2/11 at 11:19 AM |
|
|
ok...lets agree that new (galvanized) bolts with correct strength would have upgraded the complete refurb-job
|
|
ChrisLeary
|
posted on 28/2/11 at 11:44 AM |
|
|
quote: Originally posted by alfas
ok...lets agree that new (galvanized) bolts with correct strength would have upgraded the complete refurb-job
Yes I agree completely with that. But they didn't need replacing, so I didn't bother. I didn't think painting the bolts after
assembly to stop corrosion would cause such a huge problem with people...
|
|
Nisseven
|
posted on 2/5/11 at 10:54 AM |
|
|
Alfas,
I am struggling with your insistance on new "galvanised" bolts in a set of calipers? It may be that what you are calling galvanised
differs from what I know as galvanised, but the only galvanised bolts in this country are used by builders and have a really thick coating of zinc and
definately not what you would use in a car. If you are talking about zinc plating as in electroplating then maybe, but if you are worried about the
strength of the bolt then electroplating, I am told, is not to be recomended either. I personally do not see why the use of new bolts is neccessary,
zinc plated or not, if the old ones were OK. Your opinion is your own as is mine but I think you being a little unfriendly in the way you gave it.
Just my opinion, don't take offence, you are probably a very nice person.
Bruce
|
|
PSpirine
|
posted on 2/5/11 at 11:03 AM |
|
|
Kind of misunderstanding why there's any sort of argument against Chris here - since when is it wrong to paint things (in my mind both making
them looking pretty and preventing corrosion are equally valid reasons).
I certainly can't recall the last time I saw any galvanised fasteners that were high-tensile!
|
|
aeromanboeing
|
posted on 1/6/11 at 05:19 PM |
|
|
After reading the posts on this forum I now know why the SVA is so tough.
|
|