JoelP
|
posted on 17/2/06 at 08:06 PM |
|
|
threads on a track rodend.
having finally put the new rack in the locost, i find that, even with a touch of toe in, i only have 5 threads holding the TREs on. Definately
borderline, but with the locknuts they seem snug. Question is, is that too few turns? They arent short enough to fit extensions, which rather
annoyingly, i have lying around...
any thoughts?
|
|
|
flak monkey
|
posted on 17/2/06 at 08:09 PM |
|
|
If you have 5 turns you have about 9mm of thread in the track rod. Which i would say isnt enough, but i am happy to be proven wrong!
david
Sera
http://www.motosera.com
|
|
Nick Skidmore
|
posted on 17/2/06 at 08:11 PM |
|
|
I would say that's not enough. 1.5 x diameter is comfortable.
How about cutting the trackrod at a suitable place and welding a sleeve made out of tube / drilled bar over the gap?
I've seen single seater drive shafts shotened / lengthened by this method.
|
NOTE:This user is registered as a LocostBuilders trader and may offer commercial services to other users
|
JoelP
|
posted on 17/2/06 at 08:19 PM |
|
|
well, i just did that with the column, and i suppose the rack sees different but smaller forces than the column.
Are the arms normal steel?
|
|
andyb64
|
posted on 17/2/06 at 08:40 PM |
|
|
Joel, if you need anything machining you can use my lathe if you want
Andy...
|
|
JoelP
|
posted on 17/2/06 at 08:59 PM |
|
|
cheers andy - not sure what im going to make to sort this one. Having just been for a blast round the block, the toe in is excessive - rolling out of
the drive saw the tyres jumping every few metres.
I have some 19mm round bar, but it seems a little thin and wouldnt be a tight fit. Maybe a 4 inch sleeve with regular holes drilled for spot welds.
Any tips anyone? It needs sorting tomorrow, as its trackday sunday, hence i cant buy any parts.
That said, the quick rack makes an amazing difference! Unbelieveable Just need some new top bones and some new shocks now 
|
|
Jon Ison
|
posted on 17/2/06 at 09:35 PM |
|
|
Dunno if this will make any sense ?
If you have some round bar, cut your track rods in half ish, drill n tap up the middle, (lathe is best) drill n tap up the middle of your extension
piece (the round bar) prob around M8 for all of them, use some threaded bar (studding) or cut some bolt heads off if you have none, put a weld prep on
all the bits your gonna screw together and screw the lot together then fill the weld preps with weld and too make it really neat back in lathe too
smooth it all off.
Hope this makes some kinda sense, if anyone is wondering if this will hold I have made input shafts this way too mate different engine/gearbox
combinations together driving thru a locked diff so seeing lots of load and never broke one........ touch wood.
Edit too add,
Nothing wrong with the sleeve idea above, ive done drive shafts that way too, just think the idea I mentioned looks much neater especially if done in
a lathes
[Edited on 17/2/06 by Jon Ison]
|
|
gazza285
|
posted on 17/2/06 at 10:16 PM |
|
|
Why not cut the ends off your track rod to allow you to put the extensions on? Or will you cut off too much thread to leave you with not enough in the
extension then.
DO NOT PUT ON KNOB OR BOLLOCKS!
|
|
JoelP
|
posted on 17/2/06 at 10:28 PM |
|
|
hi guys. Lots of good ideas, but heres my best attempt, hot from the welder. No time to spare! I must confess, i held it at the most photogenic angle!
I found some 15mm tube, chopped 20mms of it, chopped the arms, welded the 15mm into the gap, then ground back and sleeved it with the 19mm round,
which turned out to be a tight fit.
Thoughts?
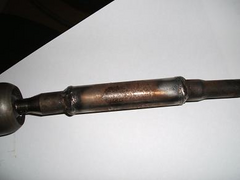 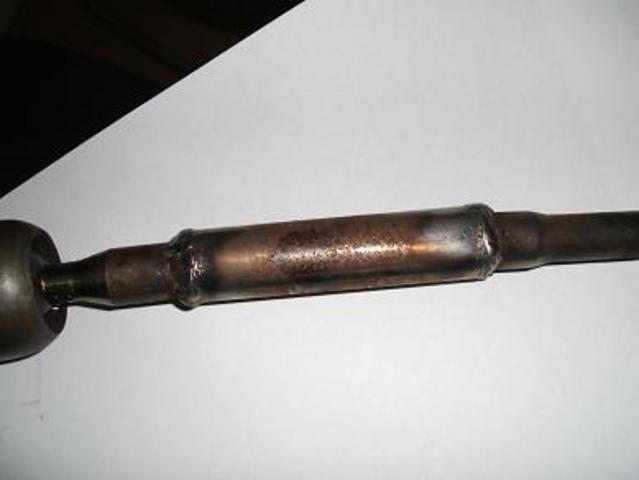 Rescued attachment rackend1.JPG
|
|
JoelP
|
posted on 17/2/06 at 10:30 PM |
|
|
a slightly lighter photo, so the welds actually show up...
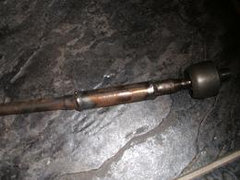  Rescued attachment racklight.JPG
|
|
JoelP
|
posted on 17/2/06 at 10:32 PM |
|
|
balls that no better.
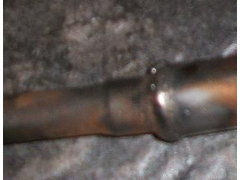  Rescued attachment racklight.JPG
|
|
02GF74
|
posted on 18/2/06 at 10:50 AM |
|
|
Christ almighty!!! Have you not been paying attentions? I have this problem; quick search would reveal all.
To answer some questions;
The track rods are hardened steel (rally design) so it would be next to impossible to cut threads using a die; you need a lathe.
Ford rack, if my old one is one. has 12 mm rods and the threads on the ends are rolled to make them 14 mm. You could put 12 mm thread on but thatwont
match the track rod ends.
In my case, I have about 3 threads engaging in the track rod end.
My solution is to have a set of short extensions made up, about 8 mm.
I have worked out that I would need to cur the track rods and they will screw into the extensions by about 27 mm.
Note that Rally design do similar ones to my design, for £20, in ali, DAR 006, diemensions (from memory) are
thredead end: 20 mm
solid end 5 mm
threaded hole: 40 mm (?)
As for what you have done,
From being on Land Rover forums, strengthening track rods comes up quite often and MOT man does not like any welding stuff on them; like what you have
done, hmmmm....
|
|
JoelP
|
posted on 18/2/06 at 11:38 AM |
|
|
im not cutting threads, i welded a simple extension in. Its solid as f*ck, and steering arms arent that stressed anyway. Talk about paranoid...
|
|
JoelP
|
posted on 18/2/06 at 11:42 AM |
|
|
just to clarify my statement that they arent very stressed - i can steer the wheel by hand no problems, without the car being jacked up. I can also
rotate it by hand, again, not jacked up. So if its that easy with dry steering, how much easier is it when the wheel is spinning? Centrifugal forces
and bumps arent much greater.
Do you think you could even bend an arm by hand, nevermind stretch or compress it?
|
|
chrisg
|
posted on 18/2/06 at 11:49 AM |
|
|
Aren't welded trackrods an automatic MOT fail?
I always thought they were.
cheers
Chris
|
|
02GF74
|
posted on 18/2/06 at 12:15 PM |
|
|
quote: Originally posted by chrisg
Aren't welded trackrods an automatic MOT fail?
I always thought they were.
cheers
Chris
Did you read the second part of my post? ^^^^^ This what I thought as well.
|
|
chrisg
|
posted on 18/2/06 at 12:44 PM |
|
|
I didn't see that mate!
Anybody know for sure?
Cheers
Chris
|
|
rusty nuts
|
posted on 18/2/06 at 12:58 PM |
|
|
Sure welded track rods are an M.O.T AND S.V.A failure . Don't matter how strong you think they are . This problem seems to crop up now and then,
anyone know of any company that can make extended track rods for not too much money ?
|
|
chrisg
|
posted on 18/2/06 at 01:23 PM |
|
|
Anyone with a decent lathe should be able to make them, tapped hole one end, thread turned on the other.
Cheers
Chris
|
|
JoelP
|
posted on 18/2/06 at 01:34 PM |
|
|
the welded part is under the rubber gaitor/boot thingy, plus its probably track only from now on anyway.
First shakedown is fine...
|
|
rusty nuts
|
posted on 18/2/06 at 01:35 PM |
|
|
Chris , I meant the complete track rod, not just the extensions . trouble is the ball on the inner end would need to be hardened?
|
|
chrisg
|
posted on 18/2/06 at 01:41 PM |
|
|
Yes it would.
I've found the bit from the mot test manual.
MOT Testers manual
Section C > d.
Cheers
Chris
|
|
flak monkey
|
posted on 18/2/06 at 01:43 PM |
|
|
Yep the balls are hardened. If you made them out of the right grade of steel (so you could heat treat the ball) and made a form tool to cut the ball
accurately then you could make them at home... Not worth the hassle though really.
Easier to take the track rod off, cut it to shorten it, then put it in a lathe and turn the OD to a decent sizes so a nice accurate thread can be cut
on it. Then make up some threaded extensions. IMO
David
Sera
http://www.motosera.com
|
|
britishtrident
|
posted on 18/2/06 at 01:46 PM |
|
|
Strikes me there is a big market for track rod extension with with 14 mm male thread and either untapped or 1/2" unf thread at the female
end.
Sierra track rods ends are slightly longer but also because of the swan neck design alow the rack track rods to runs straighter --- which should
allow them to screw on a few more threads.
|
|
britishtrident
|
posted on 18/2/06 at 01:48 PM |
|
|
I wonder if it would be possible to machine an Escort rackt to accept Sierra style track rods -
|
|