DIY Si
|
posted on 21/4/06 at 06:04 PM |
|
|
Welding Advice
What's the easiest/best way of welding the inner edge of the V? Only problem is getting into the V with the torch of my mig.
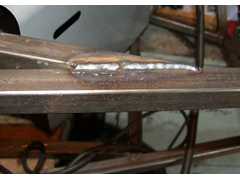 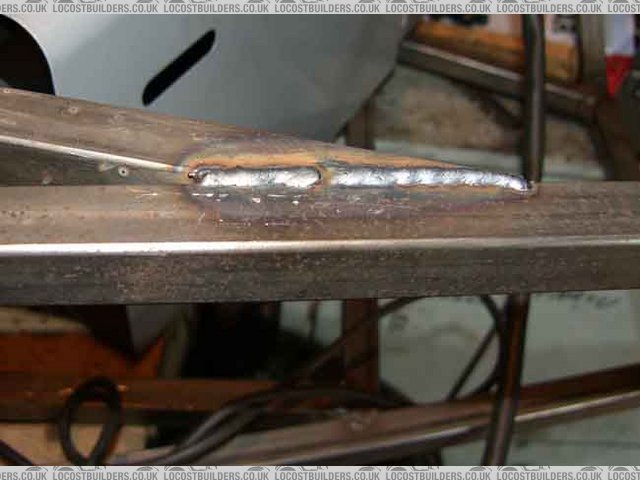 Rescued attachment SH100367.JPG
|
|
|
nitram38
|
posted on 21/4/06 at 06:12 PM |
|
|
Basically you can't !
But it will not hurt if you leave the inside.
If you are really paranoid, then weld some triangle plates across the web.
|
|
DIY Si
|
posted on 21/4/06 at 06:14 PM |
|
|
So putting a beed of weld across/down the gap as close as poss to the V isn't really worth the hassle?
|
|
JoelP
|
posted on 21/4/06 at 06:19 PM |
|
|
you can get a little in from the sides. Trying to fill it from afar isnt ideal as it gets too hot and blobs everywhere. Ive left many parts of my car
unwelded, to no ill effect. Even the bottom of my engine mounts arent welded in. However, if its a crucial part, its well worth cutting a piece of
similar box into a triangle to fill the hole. 
|
|
DIY Si
|
posted on 21/4/06 at 06:21 PM |
|
|
It's one of two Y braces for the enigne bay, as per cymtrik's plans. There are a few other bits like this due to extra triangulation. Or
will be when I put them in.
|
|
JB
|
posted on 21/4/06 at 07:16 PM |
|
|
Welding in Tight Corners
Turn up your gas, wire feed and power. It also helps if you can weld on the horizontal ie the bit your are welding is flat with gravity helping the
weld go into the corner. Then weld from the sides and middle. You will find you can weld into very tight corners which are 25 to 30mm from the
torch.
I would personally weld every joint and corner and it is always possible to get some sort of weld. As mentioned befoe put a gusset or piece in if
required.
John
|
|
mackei23b
|
posted on 21/4/06 at 07:25 PM |
|
|
Hi there
With that amount of weld area / contact patch there should be good strenth without the need to wild the inner V
Cheers
Ian
|
|
DIY Si
|
posted on 21/4/06 at 07:32 PM |
|
|
Must be doing something right. The last time I posted a pic of my welding it was frowned upon! Although I'd be the first to admit it
wasn't the best/neatest. That weld is now what I consider good, but not my best. Am I being hard on myself, or just doing what's right for
the sva man?
Ps cheers NS Dev for your advice.
|
|
tks
|
posted on 21/4/06 at 07:36 PM |
|
|
yeah!
I also would suggest putting the gas higher and the rest accordig to speed..
(the gas alse it would spatter allot!!)
If you don't fill all the gaps, your chasis in the english climate won't last long..
(i mean to say it could caught water)
Bcause it still is mild steel what we are using...
At least kit/silicone the places where you arent able to weld.....
i recommend the gas up trick, every weld is one and will deffo be better as none....
on the other half i say to that the tubes have the moest strenght on the planes
(like in the pic above) sow welding in the non backedup side can cause deforming
altough mig/mag is a very "cold" way of welding...
Just my opinion..
also i think we should look at the manufactures what do they do??
Tks
p.s.
every hole i drilled, before putting something in, i always hat the silicone by hand, every panel has his own silicone gasket...(just let it dry for
3hours..)
i cant sleep well noing/thinking that after a wet day perhaps my chasis tubes have water in them...
The above comments are always meant to be from the above persons perspective.
|
|
DIY Si
|
posted on 21/4/06 at 07:44 PM |
|
|
I'm planning on putting so many coats of paint on it that any little holes I miss get filled up with zinc primer. Or just cover them in
something else waterproof.
|
|
Peteff
|
posted on 21/4/06 at 08:03 PM |
|
|
If you run your top and bottom weld a bit further over the V and then weld into the V downwards welding to one side of the tube then again welding to
the other side you will fill the join with a third run down joining the two together. I keep a shortened squashed shroud for those bits.
yours, Pete
I went into the RSPCA office the other day. It was so small you could hardly swing a cat in there.
|
|
nitram38
|
posted on 21/4/06 at 08:06 PM |
|
|
Another little tip is to buy anti-splatter spray and spray the joints before you weld them. The splatter can just be wiped off. Alternatively, knock
the splatter off with a file. Not by banging it as the file would break, but by sliding it so that the edge of the file, hit the splatter.
Most will knock of this way.
|
|
Mr G
|
posted on 21/4/06 at 08:43 PM |
|
|
'v' ing a shroud and owning an arc welder can help
Normal is getting dressed in clothes that you buy for work and driving through traffic in a
car that you are still paying for - in order to get to the job you need to pay for the clothes
and the car, and the house you leave vacant all day so you can afford to live in it.
|
|
paulf
|
posted on 21/4/06 at 09:15 PM |
|
|
I used both methods on mine , I tend to use 1.5mm arc rods for tight gaps.
Paul.
quote: Originally posted by Mr G
'v' ing a shroud and owning an arc welder can help
|
|
Chippy
|
posted on 21/4/06 at 10:03 PM |
|
|
Don't know if you already have one, but if you get the cone nozzel for your mig, that helps. Using the standard straight one makes it harder to
reach into the tight spots. atb Ray.
|
|
DIY Si
|
posted on 22/4/06 at 12:37 PM |
|
|
Many thanks for the help gents. I think I'll try the flattened shroud thing. Sounds the easiest way for me to do it.
|
|
MikeRJ
|
posted on 22/4/06 at 06:42 PM |
|
|
Definately get a spare shroud and flatten it, helpd greatly. Also the gasless wire (if your MIG supports it) is good for getting into tight corners
as you don't need to wind up gas supply.
|
|
DIY Si
|
posted on 22/4/06 at 07:04 PM |
|
|
Mine's just a bog standard jobbie. If it were to support gasless wire, would it be worth buyin a reel just for tight corners? Seems a bit
excessive. Unless you use it often. Is it any different in use? Apart from the obvious lack of gas.
|
|
907
|
posted on 22/4/06 at 07:47 PM |
|
|
You could cut a wedge and then weld all round.
Paul G
p.s.
sorry about the crap drawing
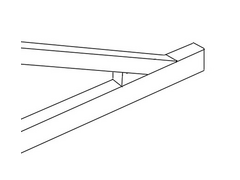 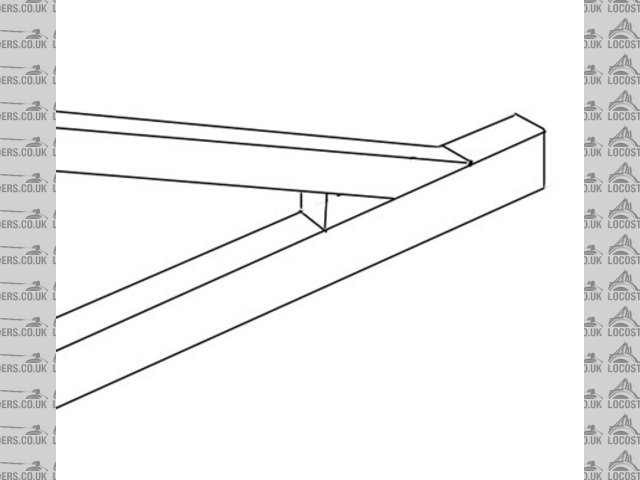 Rescued attachment wedge.jpg
|
|
DIY Si
|
posted on 22/4/06 at 07:53 PM |
|
|
Could do, but to make it easier to get at and worth the effort, it'll have to be damn long. Seems a bit excessive for a little weld. Might look
untidy too, since the rails are visible under the bonnet.
|
|
JoelP
|
posted on 22/4/06 at 08:46 PM |
|
|
it looks very professional if done neatly. I did that on my trailer several times, but that was in 2" section so easier.
|
|
DIY Si
|
posted on 23/4/06 at 12:23 AM |
|
|
That's partly what I mean, for 1" box, is it really worth the effort involved? I'm sure it can look very nice and tidy, but is it
the easiest way?
|
|
JonBowden
|
posted on 23/4/06 at 09:45 AM |
|
|
I'd try to weld it. But if you don't, you could put flexible sealant in to prevent rust.
Jon
|
|
JoelP
|
posted on 23/4/06 at 09:55 AM |
|
|
i dont think it will significantly affect the strength if you miss it, so yes, sealant is fine. Obviously if you were a manufacturer trying to
demonstrate workshop talent it would be a different matter! I wouldnt waste any time thinking about it, just crack on! 
|
|
Simon S
|
posted on 1/5/06 at 09:15 AM |
|
|
Welding inside angle tube joints
It is OK to leave the inside of a tight angle unwelded from a strength perspective, and your weld quality looks good from the pic. What ever you do
don't try too hard to weld inside it by turning up current etc.. Unless you are using something like T45 standard steel tube then every weld
will put the metal thru' a heat cycle that will drop its mechanical performance due to loss of annealing properties. Bottom line is unless the
weld will give you a guarenteed good quality result for minimum heat induced don't bother, as you may do more harm (strength-wise) than good.
|
|