dickie b
|
posted on 25/5/11 at 07:57 PM |
|
|
Subaru flat six?
Hi all
I have been following the factory five 'design the car' thread on Pistonheads..
The concept sounds great and the result should be very interesting to see - but did I read somewhere that the guys behind the Murtaya were working on
a similar layout (i.e inline rear mounted with the box converted to 2WD), but using the flat six unit from a Subaru Legacy?
I love the idea of the subaru running gear being used in this way, but the only cars are the Saker (£££) or the SDR storm.. which isnt really my cup
tea in an exo kind of way..
|
|
|
James
|
posted on 26/5/11 at 12:57 AM |
|
|
quote: Originally posted by dickie b
Hi all
I have been following the factory five 'design the car' thread on Pistonheads..
.
Thanks for sharing!
------------------------------------------------------------------------------------------------------------
"The fight is won or lost far away from witnesses, behind the lines, in the gym and out there on the road, long before I dance under those lights."
- Muhammad Ali
|
|
RazMan
|
posted on 26/5/11 at 07:02 AM |
|
|
The Murtaya is a brilliant design IMO and one which I would love to get my hands on.
http://www.murtayasportscars.co.uk/design.html
Cheers,
Raz
When thinking outside the box doesn't work any more, it's time to build a new box
|
|
loggyboy
|
posted on 26/5/11 at 09:33 AM |
|
|
Spotted one of those in Basingstoke at the weekend - looked mean.
There was a tatty one at an Autosolo a few years a go too.
|
|
coyoteboy
|
posted on 31/5/11 at 09:28 AM |
|
|
Murtaya just seems, essentially, like a light subaru? Still got the lump up front between the wheels, so effectively just a re-body?
I'm not sure I'd like to use the 4wd driveline as a 2WD - I did consider it and there's kits to lock the centre diff for just that
reason (about 250 quid IIRC), but I'm not sure it'd cope with all the torque through half the shafts.
|
|
Strontium Dog
|
posted on 31/5/11 at 10:53 AM |
|
|
I agree with Mr Coyote as to the torque issues especially as I've heard of a few gearbox issues in Scoobies. (Not sure about that as not had
much to do with them, just something I've heard). On the upside, with so much less weight the shafts should have a easier time than they would
in a saloon car!
|
|
coyoteboy
|
posted on 31/5/11 at 11:08 AM |
|
|
quote:
On the upside, with so much less weight the shafts should have a easier time than they would in a saloon car!
Actually no, the peak torque felt in the shafts is the same as in the saloon car and is limited only by the engine output, not the body weight. The
only difference is the same torque accelerates the lighter car faster.
|
|
JoelP
|
posted on 31/5/11 at 11:25 AM |
|
|
quote: Originally posted by coyoteboy
quote:
On the upside, with so much less weight the shafts should have a easier time than they would in a saloon car!
Actually no, the peak torque felt in the shafts is the same as in the saloon car and is limited only by the engine output, not the body weight. The
only difference is the same torque accelerates the lighter car faster.
not so! Because the car is freer to accelerate, the shafts dont see the peak torque! This is the same concept as big wheels breaking halfshafts on
offroaders, even when the engine output is unchanged.
Basically, the half shaft only sees maximum torque (ie whatever is passed through the clutch multiplied by the gear ratio) if the wheel is held
still.
Similar also to the fact you cannot snap a spanner on a nut that is loose, the nut would need to be tight to apply the torque that would break the
spanner.
|
|
coyoteboy
|
posted on 31/5/11 at 12:11 PM |
|
|
Imagine the simplest possible system; ignore the gearbox and diffs/shafts apart from the last half shaft (we're assuming they're all the
same anyway). Now use a 1m spanner to turn one end of the shaft using a 100kg weight at the end of it and lock the wheel to the ground (providing
infinite resistance, such as driving a rangerover wheel might ). What's the peak torque in the shaft? It's 1000Nm (give or take).
Change the wheel size to one with half the diameter but keep the wheel locked. What's your shaft torque now? 1000Nm. The change of wheel size
means the force at the tyre contact patch (and so the force on the locking mechanism) is twice as large, but the torque in the shaft is the same and
is limited by the spanner/weight arrangement. The force at the contact patch (or our locking mechanism) is what accelerates your cars mass, but it
doesn't determine peak shaft torque. If the cars mass is higher the same torque in the shaft will produce a slower acceleration, but it
can't produce a higher torque in the shaft.
If you're breaking shafts due to changing wheel sizes it's because your shaft was under-sized to start with for the gearing and engine
driving it, probably on the basis of probable use (i.e. we know the car will start to accelerate and not reach peak torque so we can lose a little
meat off those shafts to save weight and cost).
As I say, adding a flywheel massively increases the torque that can be seen for a fraction of a second using stored energy, but assuming you're
not stepping off the clutch at peak torque with ultra-grippy tyres that won't break free, you'll not see it in the shaft.
Without wanting to labour the point, if you followed your analogy and peak torque was related to wheel size or vehicle weight, if you had an
infinitely heavy car and a 50cc scooter engine you'd be snapping infinite diameter driveshafts still, rather than stalling the engine....
[Edited on 31/5/11 by coyoteboy]
|
|
JoelP
|
posted on 31/5/11 at 12:34 PM |
|
|
i'll agree that we are labouring the point somewhat, but i'll keep on for now
quote: Originally posted by coyoteboy
Imagine the simplest possible system; ignore the gearbox and diffs/shafts apart from the last half shaft (we're assuming they're all the
same anyway). Now use a 1m spanner to turn one end of the shaft using a 100kg weight at the end of it and lock the wheel to the ground (providing
infinite resistance, such as driving a rangerover wheel might ). What's the peak torque in the shaft? It's 1000Nm (give or take).
Change the wheel size to one with half the diameter but keep the wheel locked. What's your shaft torque now? 1000Nm. The change of wheel size
means the force at the tyre contact patch (and so the force on the locking mechanism) is twice as large, but the torque in the shaft is the same and
is limited by the spanner/weight arrangement. The force at the contact patch (or our locking mechanism) is what accelerates your cars mass, but it
doesn't determine peak shaft torque. If the cars mass is higher the same torque in the shaft will produce a slower acceleration, but it
can't produce a higher torque in the shaft.
the flaw here is that you are overlooking what size force is required to hold the wheel still - by definition, for the force at the contact patch to
be negated, the forces in either direction must be equal. It harder to hold the small wheel still - hence why screwdrivers have large handles.
quote:
If you're breaking shafts due to changing wheel sizes it's because your shaft was under-sized to start with for the gearing and engine
driving it, probably on the basis of probable use (i.e. we know the car will start to accelerate and not reach peak torque so we can lose a little
meat off those shafts to save weight and cost).
well, its an agreed principle in 4wd forums that large wheels break halfshafts, because it is harder to turn the wheel.
quote:
As I say, adding a flywheel massively increases the torque that can be seen for a fraction of a second using stored energy, but assuming you're
not stepping off the clutch at peak torque with ultra-grippy tyres that won't break free, you'll not see it in the shaft.
Without wanting to labour the point, if you followed your analogy and peak torque was related to wheel size or vehicle weight, if you had an
infinitely heavy car and a 50cc scooter engine you'd be snapping infinite diameter driveshafts still, rather than stalling the engine....
assuming the car had infinite mass, youd need infinitely low gearing to move it, and unless your halfshafts also had infinite diameter, they would
also snap!
I feel this may go on unless one of us gives up
|
|
coyoteboy
|
posted on 31/5/11 at 01:08 PM |
|
|
quote:
the flaw here is that you are overlooking what size force is required to hold the wheel still - by definition, for the force at the contact patch to
be negated, the forces in either direction must be equal. It harder to hold the small wheel still - hence why screwdrivers have large handles.
No im not, im ignoring the force required to hold it as it's not important here. If I'm holding it still I'm holding it still, with
a smaller wheel of course the force will be larger at the contact patch (i.e. the lever radius presented by the wheel diam) but that's not
important, it's just a reaction force, it can't be higher than the force applied by definition.
quote:
well, its an agreed principle in 4wd forums that large wheels break halfshafts, because it is harder to turn the wheel.
I know a few forums where it's agreed in principle that painted bicycle spokes break easier than unpainted ones despite evidence to the
contrary!
quote:
assuming the car had infinite mass, youd need infinitely low gearing to move it, and unless your halfshafts also had infinite diameter, they would
also snap!
And if you had infinitely low gearing you'd have infinitely slow motion. We're ignoring gearing and assuming it is constant to prove this
point, if you start varying multiple variables you confuse the issues and come to the wrong conclusion. Take an engine and gearbox that are the same,
hell remove the gearbox and bolt an engine right up to your 1ft diam solid output shaft. Now attempt to accelerate that million ton car at 1g
horizontal - what do you think will happen - stall the engine or snap the shaft? Simple, you stall the engine.
Torque is constant along a shaft. Grab a baseball bat and simulate your infinitely heavy car by jamming it in a door. Turn the other side with all
your might, that's the maximum torque the shaft will see, the torque your hands can apply on the handle. Sure if you let the shaft slip
it's going to see lower torque, but that's only because the shaft has minimal rotational inertia and contact friction is dominant,
it's a different situation.
A different analogy would be to take a very large mass, say a planet, and try to spin it with your baseball bat. The force you can put in is limited
by you, and by definition the torque in the shaft. the rate of acceleration of the planet is limited by your hands. Now attach your baseball bat to a
moon instead. You put in the same force, same torque on the shaft only now your moon accelerates faster.
I'm here all day! 
|
|
JoelP
|
posted on 31/5/11 at 01:16 PM |
|
|
quote: Originally posted by coyoteboy
Sure if you let the shaft slip it's going to see lower torque....
I'm here all day!
no need for all day, you've just agreed with me.
Slipping reduces the torque.
Ps, google about big wheels on offroaders, i think you'd find it eye opening just how many people you are arguing with.
|
|
coyoteboy
|
posted on 31/5/11 at 01:29 PM |
|
|
quote: no need for all day, you've just agreed with me.
Slipping reduces the torque.
No I didn't, you're confusing friction with inertia. That's why we specified non-slipping tyres/fixing the wheels in place so we are
talkign about max torque possible with any given arrangement, and working backwards.
quote:
Ps, google about big wheels on offroaders, i think you'd find it eye opening just how many people you are arguing with.
This point means nothing, a) people are often confused by the real causes of breakage and b)...
If your shaft were designed to work with a smaller wheel it would be assumed to slip earlier due to higher contact patch force, reducing reaction
force and so torque in the shaft before it breaks. With a larger tyre you'll see lower reaction forces (which is why they accelerate slower with
big wheels) and therefore the contact patch won't slip as easily (plus the wheels will have more contact patch to grip with) and so the torque
in the shaft can rise to one great enough to snap the shaft IF, and only IF the shaft were designed to handle lower torque than the engine and
box/diffs can generate at that point. Make the shaft large enough to cope with the torque the engine and box can put out and you're never going
to snap it, regardless of vehicle weight or wheel size. In the case of a 4x4 there's teh added complication of a massive flywheel and gearbox
rotational inertia which can provide a sudden spike of torque higher than the engine alone could put out (if you assume the engine isn't the
flywheel), and the fact that you're likely to be stopping and starting wheel motion abruptly (similar to dropping the clutch and using the
flywheel) but the fact still stands - the torque can't rise above that provided by the engine (be it through normal use or b using the flywheel
stored energy). However this operating regime is somewhat distant from road use, i.e. it makes the point harder to see through the mud, but the point
still stands. Google "god" and see how many people a logical view of evolution is arguing with, are you a creationist or do you apply
logic when analysing something?
Feel free to answer the moon/planet/baseball bat analogy? According to your way of looking at it I'd be able to apply more torque to the larger
planet and so snap the bat. In reality I'd just accelerate the planet slower with the same torque and the bat would be fine as I'm fairly
weak
[Edited on 31/5/11 by coyoteboy]
|
|
JoelP
|
posted on 31/5/11 at 05:12 PM |
|
|
quote: Originally posted by coyoteboy
Feel free to answer the moon/planet/baseball bat analogy? According to your way of looking at it I'd be able to apply more torque to the larger
planet and so snap the bat. In reality I'd just accelerate the planet slower with the same torque and the bat would be fine as I'm fairly
weak
Its a poor analogy because firstly, you cannot break a bat by hand, and secondly, both masses are ridiculously heavy.
If we replace the lighter one with say a beach ball, then yes, i can reason you out of it, provided that you are actually strong enough to break the
bat when there is a planet on the end of it.
So, assume you have a long bat with jupiter on it, and you are phenominally strong. You twist hard, the planet barely moves, and you crack the handle
off.
Now, replace with a beach ball; you turn as hard as you can, and before you manage to break it, the whole ball is turning. So you get your equally
strong mate to hold the ball still, and smash it between you.
And you cannot call that friction in this scenario, as its clearly inertia!
If we're going back to analogies, how about the one i mentioned, about trying to snap a spanner with a loose nut?
Also, regarding the wheels on 4wds, i believe it is speciafically because large wheels are more likely to get into a situation where they cannot be
turned, because the resistance at the contact patch has more distance from the centre, so torque is greater on the shaft.
As an example, imagine you have a wheel being turned by a shaft, and the shaft will break at say 100nm of torque. With a 1m radius wheel, that
basically means a resistance to motion at the contact patch of 100 newtons will break it. If the wheel was only 50cms radius, then the force required
at the contact patch to break the shaft would be 200 newtons. So, the larger wheel has caused the shaft to break with a lower force, because the extra
radius as increased leverage.
Now in normal driving in a 4wd, it doesnt matter; you give it full beans, that is translated to a thrust via all 4 contact patches, and the vehicle
accelerates accordingly. If you are in low ratio going up a hill though, you have lots more torque going into the wheels. If you assume that the
contact patch on a given surface will slip if more than 150 newtons is applied, then with the small wheels the tyre will slip, with large wheels the
shaft wil break.
|
|
Alan B
|
posted on 31/5/11 at 05:56 PM |
|
|
Cracking debate
Utterly OT, but I'm loving it...    
|
|
coyoteboy
|
posted on 31/5/11 at 05:58 PM |
|
|
quote:
Its a poor analogy because firstly, you cannot break a bat by hand, and secondly, both masses are ridiculously heavy.
It's not a poor analogy at all, it just doesn't show what you want it to show so you don't like it! Both masses have to be heavy
otherwise it's hard to visualise the forces involved, which is why your nut/spanner analogy seems right until examined in detail.
quote:
If we replace the lighter one with say a beach ball, then yes, i can reason you out of it, provided that you are actually strong enough to break the
bat when there is a planet on the end of it.
No you can't. Replace the ligher one with a fly if you like, all you have to do is turn the ball fast enough that the rotational inertia loads
the engine sufficiently, the problem with that is you wouldn't be able to accelerate a fly (or beach ball) fast enough without it becoming
several parts and flying off before the bat broke. Your analogy, again, seeks to limit it to accelerations/masses that seem to describe what you want,
not reality.
quote:
So, assume you have a long bat with jupiter on it, and you are phenominally strong. You twist hard, the planet barely moves, and you crack the handle
off. Now, replace with a beach ball; you turn as hard as you can, and before you manage to break it, the whole ball is turning. So you get your
equally strong mate to hold the ball still, and smash it between you.
Turning as hard as you can wouldn't doesn't matter here, you'd never be able to turn as *hard as* you can because you're not
able to move fast enough to get the ball to accelerate fast enough to load your arms to the max and thus snap the bat. In theory, if you had the bat
turning fast enough (probably hundreds of thousands of RPM, but with the same max torque as your arms can produce) and then connected it to the beach
ball it WOULD snap the bat.
quote: And you cannot call that friction in this scenario, as its clearly inertia!
Yes but you've moved the masses to a point where it's hard to put the loads and speeds into a normal frame of reference, that's all.
I could do the maths for you if you like, it's all fairly simple engineering calculations.
quote:
If we're going back to analogies, how about the one i mentioned, about trying to snap a spanner with a loose nut?
Again, possible if you were able to get the spanner to accelerate fast enough, however you start coming into the region of the self-inertia of the
spanner being similar larger than that of the item being spun so they become the dominant force in breaking the spanner.
quote:
As an example, imagine you have a wheel being turned by a shaft, and the shaft will break at say 100nm of torque. With a 1m radius wheel, that
basically means a resistance to motion at the contact patch of 100 newtons will break it. If the wheel was only 50cms radius, then the force required
at the contact patch to break the shaft would be 200 newtons. So, the larger wheel has caused the shaft to break with a lower force, because the extra
radius as increased leverage.
You've just repeated back to me almost exactly what I said, only you've missed the point, with respect. Yes, if the inboard end of the
shaft is attached to a rigid mount point, the weight of the car on a slope becomes the "driver" and the shaft would shear. But it's
not, it's attached to an engine and gearbox which are the torque producer, which can only provide a certain torque before stalling, hence the
torque seen by the shaft is limited to what the engine can produce (and is resisted by the wheels), after which point the engine will stall and the
shaft torque becomes zero.
Again, an analogy to clear it up (or make it muddier!) - you have a half inch ratchet on a 1/4 drive extension. We both know you (a nice V8) can shear
that bar with the ratchet if you meet a stuck nut, but your child (a honda scooter engine) isn't strong enough.Which do you think matters -
what size the stuck nut (wheel size) is, or whether it's you or your 3 year old child trying to move the spanner? Do you really think your child
could shear the bar if the nut was an M40 hex head? Of course not, because the torque PRODUCER isn't capable of creating that torque.
The same situation applies when accelerating the car using the same driveline/wheel sizes etc - the torque in the shaft is limited by the torque of
the power and drivetrain multipliers, the mass of the vehicle simply determines how fast the car accelerates for the same force (torque). Don't
make me start drawing free body diagrams!!
[Edited on 31/5/11 by coyoteboy]
|
|
coyoteboy
|
posted on 31/5/11 at 06:40 PM |
|
|
One question to ask yourself- if, in the heavier car, there's more torque in the shaft - what's producing the torque that snaps it? If
the wheel is magically producing torque in the opposite direction to the engine at an amount larger than the engine can, the engine would stall and go
backwards. Wheels don't produce torque, they only react what comes from the engine - nothing from the engine, no force at the wheel contact
patch. Max torque from the engine = max force at the contact patch (assuming no slip). All that changing the mass of the car does is adjust the
acceleration rate required to load the shaft with the max torque, if the shaft is designed large enough to withstand the max torque of the engine
there's nothing you can do with that engine/transmission combo to snap the shaft, whether you're accelerating a moon or a mouse. As I
said, max torque from the engine should technically include the anglular momentum of the flywheel and rotating parts which would produce a much larger
torque than that specified as the engine's nominal torque output, but only for a fraction of a second. Same applies though, design for that
torque instead and you'll never break the shaft regardless of car mass.
In an effort to keep this thread at least partly on track I'm going to bow out now, but feel free to continue the discussion over U2U or MSN, I
need practice explaining stuff like this!
[Edited on 31/5/11 by coyoteboy]
|
|
JoelP
|
posted on 31/5/11 at 08:23 PM |
|
|
this is getting silly, we might have to agree to disagree
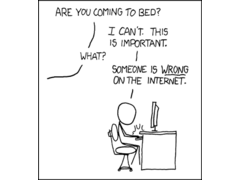 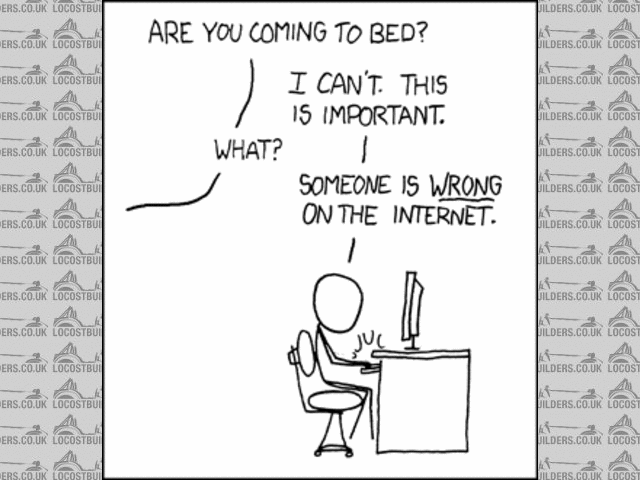 Description
|
|
JoelP
|
posted on 31/5/11 at 08:33 PM |
|
|
on the subject of the offroaders though, i suspect it is the low ratio box that causes the problem - on my jeep, first gear in low is about a 20x
reduction in gearing so 20x more torque, so somewhere about 4000lbft at max throttle. Im guessing they cannot realistically make it take this, and
rely on the user not booting it when the wheels cannot turn. Big wheels are easier to stop turning (in a similar way to how you can stop a cordless
drill by grabbing the chuck, but not by grabbing the driver bit shaft), so make it more likely that the shaft will see the full whack.
Sadly that is also linked to the idea that the shafts see less torque when the wheels are free to turn.
|
|
coyoteboy
|
posted on 31/5/11 at 09:58 PM |
|
|
No no, you're on the right lines with that one - the high ratio box attempts to spin the engine (when moving faster than RPM would make you) and
as you say puts massive torque through the box (assuming the wheel doesnt slip) when hitting the throttle. Probably much more than you could design
the shafts to withstand! That's fine, torque multipliers do pose a danger! 
|
|
|