Mr Whippy
|
posted on 31/5/22 at 08:49 PM |
|
|
oh dear
I buy brake pipe from Halfords, its the - Product Type : Pipe Tubing 3/16
I use
Product Type : Pipe Union Male
Size : Male M10 x 1 Pitch
and
Product Type : Pipe Union Female
Size : Female M10 x 1 Pitch
your flaring tool is way fancier than my cheapo joby and it works just fine. I've used these on all my semi modern cars never having a leak and
only had to use imperial on the landrovers.
on brake hose ends they seem to need a double flare (like a cup) and other joints a bubble. If your not sure have a look inside the connection as its
quite obvious by the shape inside. I'd stay away from the SAE single which I think your showing there with the huge countersunk, that's
never going to squeeze down on the pipe hard enough.
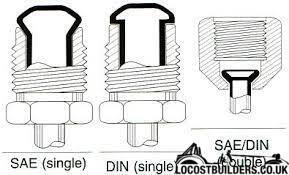
|
|
|
MadMaxx
|
posted on 31/5/22 at 09:16 PM |
|
|
quote: Originally posted by Mr Whippy
oh dear
I buy brake pipe from Halfords, its the - Product Type : Pipe Tubing 3/16
I use
Product Type : Pipe Union Male
Size : Male M10 x 1 Pitch
and
Product Type : Pipe Union Female
Size : Female M10 x 1 Pitch
your flaring tool is way fancier than my cheapo joby and it works just fine. I've used these on all my semi modern cars never having a leak and
only had to use imperial on the landrovers.
on brake hose ends they seem to need a double flare (like a cup) and other joints a bubble. If your not sure have a look inside the connection as its
quite obvious by the shape inside. I'd stay away from the SAE single which I think your showing there with the huge countersunk, that's
never going to squeeze down on the pipe hard enough.
Looking to the shape obtained with my flaring tool by CBS and comparing with your picture I would say mine is SAE standard with double flare, but I
supposed that to use M10 nuts and T piece instead of 3/8" was the same. Looking to results obtained (dripping oil) I understood that I have to
use 3/8" both nuts and T piece to be compatible with the shape of SAE 3/8" flaring. Is it correct my arguing?
I need to use double flare with T piece and single flare to connect straight male bulkhead convex seat 3/8" I have at the end of the flexi pipe
coming from front calipers and rear drums.
My re-building diary:
http://www.llcc.it/YetAnotherForum.NET/default.aspx?g=posts&t=13448
|
|
MadMaxx
|
posted on 31/5/22 at 09:22 PM |
|
|
As flexi pipe I mean this:
[img] [/img]
My re-building diary:
http://www.llcc.it/YetAnotherForum.NET/default.aspx?g=posts&t=13448
|
|
MadMaxx
|
posted on 31/5/22 at 10:43 PM |
|
|
quote: Originally posted by 40inches
The counter-sinking on the nuts looks a bit excessive?
Just checks all my spares and they don't have any counter-sinking!
I have these CBS nuts
Are these nuts for DIN flare?
My re-building diary:
http://www.llcc.it/YetAnotherForum.NET/default.aspx?g=posts&t=13448
|
|
40inches
|
posted on 1/6/22 at 08:25 AM |
|
|
quote: Originally posted by MadMaxx
quote: Originally posted by 40inches
The counter-sinking on the nuts looks a bit excessive?
Just checks all my spares and they don't have any counter-sinking!
I have these CBS nuts
Are these nuts for DIN flare?
They are M10x1, I have used them on SAE and DIN flared joints same as yours with no problem. The copper/Kunifer will
take the shape of the hard fittings.
Just to clarify, the nuts you have are for this fitting.
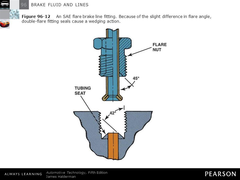 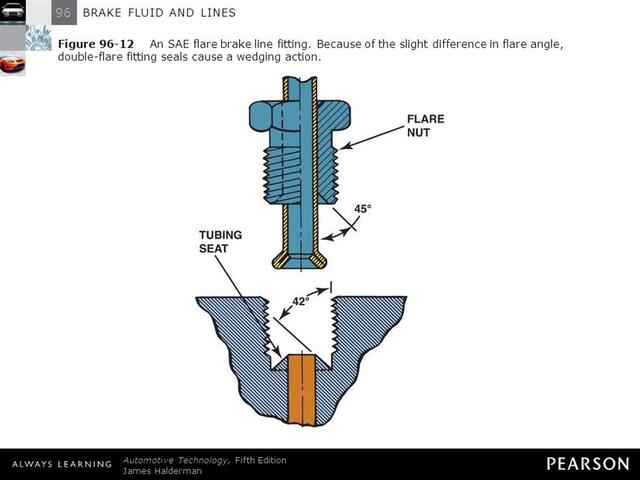 Convex female fitting
[Edited on 1-6-22 by 40inches]
|
|
Mr Whippy
|
posted on 1/6/22 at 11:44 AM |
|
|
quote: Originally posted by 40inches
quote: Originally posted by MadMaxx
quote: Originally posted by 40inches
The counter-sinking on the nuts looks a bit excessive?
Just checks all my spares and they don't have any counter-sinking!
I have these CBS nuts
Are these nuts for DIN flare?
They are M10x1, I have used them on SAE and DIN flared joints same as yours with no problem. The copper/Kunifer will
take the shape of the hard fittings.
Just to clarify, the nuts you have are for this fitting.
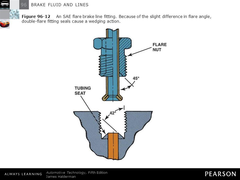 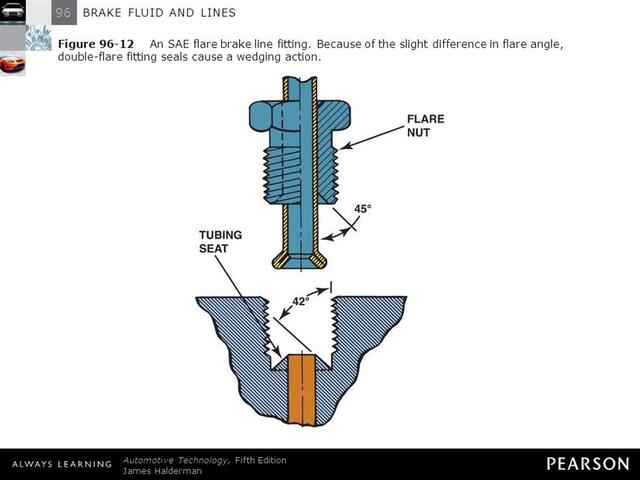 Convex female fitting
[Edited on 1-6-22 by 40inches]
Which is for some types of caliper but not screwing onto the end of your flexi hoses
|
|
MikeR
|
posted on 1/6/22 at 12:24 PM |
|
|
I don't know for sure the different tool will fix your problem. Just saying I had a problem with the tool you currently have.
|
|
MadMaxx
|
posted on 1/6/22 at 01:58 PM |
|
|
Sorry to stress again you all, but still very confused:
Old on left with flat top nut (SAE flare?), new on right with inside chamfered (DIN flare?).
[img] [/img]
Old joint between kunifer pipe and flexible (imperial?) pipe to caliper:
[img] [/img]
Old Imperial (?) T joint above and new metric Tjoint below. It really has different conical shape inside, specific for SAE or DIN flare?
[img] [/img]
My re-building diary:
http://www.llcc.it/YetAnotherForum.NET/default.aspx?g=posts&t=13448
|
|
daviep
|
posted on 1/6/22 at 07:25 PM |
|
|
Wow this is a very confusing story!!
You need to start by identifying what is required at the various connections.
Start by identifying whether you need metric or unf - they are very similar, converted to metric 3/8 x 24tpi (UNF) is 9.5mm x 1.05mm vs 10mm x 1mm for
metric. It's very difficult to tell them apart by measurement, it helps if you have known good components to test with.
Then identify which type of flare is required eg single or double - single would suit your tee piece and double the front flexi bulkhead.
Then identify DIN vs SAE. However my experience of DIN vs SAE is the same as whippy, never had a problem, I'm not even sure what flare my tool
produces.
If you are not confident identifying metric vs imperial, single vs double and & sae vs din, you can always cut the nuts off the old pipe and reuse
them. At least then you can be confident of having matching components.
Hopefully you will get there.
Cheers
Davie
“A truly great library contains something in it to offend everyone.”
|
|
Mr Whippy
|
posted on 1/6/22 at 08:59 PM |
|
|
I often reuse the fittings simply getting them red hot with a blow torch and then dropping them into some old engine oil. come out looking very nice
and stained black. Don't heat the ends of hoses as they explode.
Screw the fittings together by hand with no pipe. They should go together with no play all the way to the bottom of the thread. If they don't
your mixing up threads. You need to take those chamfered unions and hurl them into the bin.
Look here's a pipe and flexi from my car. I only use these two types of fittings for the whole car. These are metric and you'll note there
is no chamfer. These have been split after fitting and you can see that the bubble has clearly been squished smooth and flatter, I can't see that
in your examples of the bubble.
[Edited on 1/6/22 by Mr Whippy]
|
|
Mr Whippy
|
posted on 1/6/22 at 09:12 PM |
|
|
Here's the same pipe end fitted to a metric t-piece, you can't mix metric and imperial as it just won't thread together. I can fit this
hand tight, note the thread has not run out so I know it is squeezing the bubble. Even hand tight I cannot blow air past it.
[Edited on 1/6/22 by Mr Whippy]
|
|
obfripper
|
posted on 2/6/22 at 12:15 AM |
|
|
Just my observations on your pics,
The original on the left is a din type flare with no chamfer on the m10 nut, this is what you need to replicate. The flare on the right is not
fully/correctly formed, and is going inside the chamfer which is making the problem even worse.
It may be worth making some test flared sections that you can thread into place - with the nut fingertight, the pipe should not be loose in the
fitting and there should be enough thread left to allow the nut to be fully tightened ie at least 2mm of thread still exposed.
Once you can see what works, you can make your flares to match.
A generally used standard with brake pipe hardware is metric threaded parts are gold/yellow passivated finish, and unf threaded parts are plain zinc
finish, this only applies to zinc plated steel parts.
This should be a m10 female nut, with a double sae flare to match the end of the hose bulkhead fitting.
This pic from your archive looks fine and correct for this:
 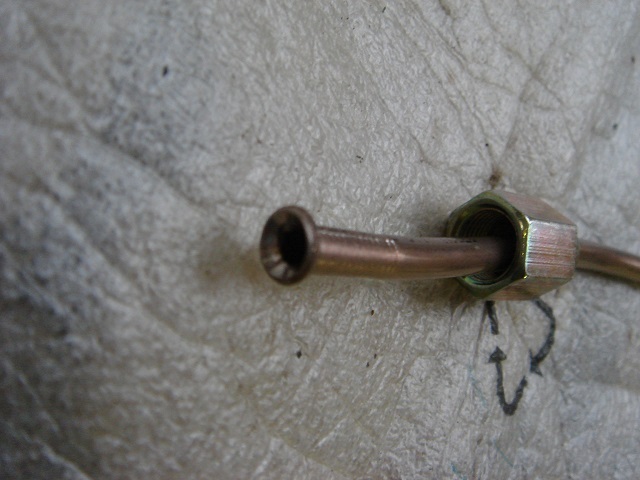 Description
Difficult to see here, technically the din flare has a 115° angle into a 120° seat , the sae flare has a 90° angle into a 96° seat. You could cut a
card template to check, but may be difficult to see this.
At a guess, the old tee union is a din fitting matching your other old fittings, and the new tee union is a sae fitting matching the chamfered brass
nuts you were supplied, both m10 thread.
The new fitting also looks to have machining chatter marks on the seat, this would make it hard to get a good seal even with the correct flares.
Other thoughts
-The flaring tool you have is only for sae flares, as others have mentioned, the copper is soft enough that you can get away with tightening a sae
flare within a din fitting, not best practice but it can work with copper pipe.
The pipes will need more tightening than usual in this case, again a test section is useful to know how much to tighten without damage.
I have seen overtightened unions fail, but only with sae double flares fitted using din nuts, where the square edge has cut off the flare from the
pipe - this is good reason to match correct components wherever possible.
-You need to get some decent din spec male tube nuts, i did look on ebay.it and found only suppliers in the uk, similar on amazon, have you got any
local car part stores who you could actually visit to match tube nuts to your original parts?
Alternatively, if.you have access to a scrapyard, cut off the matching fittings at the abs pump end of a few cars, these are unlikely to be corroded
and will be of good quality and the correct spec from any modern/european car.
-I have had a roll of copper line that would not make good flares due to it not being annealed properly, they always looked uneven and were difficult
to seal, it might be worth heating up a sample to anneal and seeing if it flares any easier/better.
Dave
|
|
chillis
|
posted on 2/6/22 at 08:30 AM |
|
|
quote: Originally posted by MadMaxx
quote: Originally posted by adithorp
Couple of things from those pic's (looking on my phone and a bit blurry zoomed in)...
The flare in pic 3 looks a bit small and in pic one the pipe might need to be further out before flaring to correct. Pic 2 looks like a double/concave
flare and three a single/convex ? Pic 3 also seems to have some damage to the pipe behind the flare.
[img] [/img]
This is the photo of the nut I disconnect. Maybe some dents due to clamping of the flaring tool and a little flat end instead to be domed, so no
chance to be pushed against the case by the nut? Should I have to check and smooth the contact surface, if needed?
My concern is that "all" joints seem suffer of the same problem so it should be some error in some point of the process of flaring or
tightening, so my request of tips about to fix the problem.
Looks like the flare is damaged/malformed - if it isn't perfect shape it will leak.
Never had any success personally with copper - always leaked. Steel pipes never a problem, just harder to work the material. I suspect the softer
material deforms and goes slightly out of shape more easily. You must always de-burr the cut end and make sure its cut square first and ensure it if
straight and square in the die, any slight misalignment will give you a deformed flare and it doesn't need to be deformed by much before it
leaks, don't ask me how I know
Never under estimate the ingenuity of an idiot!
|
|