britishtrident
|
posted on 23/2/06 at 08:42 AM |
|
|
The basic premise of the calculations is flawed pedal pressure isn't always applied at 90 degrees to the pedal axis --- I would work with 10kn
applied at an angle of 30 degrees -- do that and I suspect your pedal will buckle like tissue paper. Then of course there are fatigue and stress
concentrations at welds to consider.
With brake pedals always use steel if made from solid material at least 8mm thick -- brake pedals do snap look what happed to Clay Regazzoni in an
F1 Ensign at Long Beach in 1981 ---"In the 1980 Long Beach race a brake pedal snapped and Clay's car went careering down a slip road to
slam into a parked Brabham which had retired earlier in the race. Clay sustained back injuries which invalided him out of the sport. Thereafter,
partially confined to a wheelchair - he can stand, but not walk - he sustains an active presence at most European Grand Prix commentating for Swiss
television."
Quote taken from http://www.gpracing.net192.com/drivers/careers/482.cfm
[Edited on 23/2/06 by britishtrident]
|
|
|
Hammerhead
|
posted on 23/2/06 at 09:24 AM |
|
|
Supplied MK pedals aren't 8mm steel.........do they need beefing up? Flak, how about having two uprights connecting the foot plate and the
pivot?you could weld tube between your machined holes to increase torsional stiffness.......just a thought.
|
|
NS Dev
|
posted on 23/2/06 at 09:34 AM |
|
|
Was going to post a reply and then I read BritishTrident's reply, which said exactly what I was going to say.
Also, in the first fea drawing, the pedal would not fail in compression at that point, as soon as the material started to distort, it would pinch the
clevis pin which would stop further collapse, then the pedal would fail in tension the other side.
Retro RWD is the way forward...........automotive fabrication, car restoration, sheetmetal work, engine conversion
retro car restoration and tuning
|
|
Bob C
|
posted on 23/2/06 at 10:55 AM |
|
|
I found COSMOS less than perfect for this FEA task - it wouldn't model the pivots properly - so I couldn't get what I considered to be a
realistic overall simulation - ended up doing it in bits (and welding lots more steel on....)
It's good to see a consensus of concern about brake pedals and safety, I bet there's a lot of systems on the road that would fail the
panic test. And I'd include the offerings of most of the kit suppliers in that bracket!
re: angle of application of force - this angle is readily and accurately measurable as it is applied exactly from the right buttock. It's
probably more like 10 degrees.
cheers
Bob
|
|
Jumpy Guy
|
posted on 23/2/06 at 12:19 PM |
|
|
First off- I know nothing about materials, stress or any of that malarky!!
But- i design test rigs for a lot of F1 and sports car manufacturers
Recently, we did a test rig for a major F1 player who also make road cars...
The brake test schedule was -
250 Kg *1000 operations
100 kg * 249,000 operations
|
|
flak monkey
|
posted on 23/2/06 at 12:45 PM |
|
|
quote: Originally posted by NS Dev
Was going to post a reply and then I read BritishTrident's reply, which said exactly what I was going to say.
Also, in the first fea drawing, the pedal would not fail in compression at that point, as soon as the material started to distort, it would pinch the
clevis pin which would stop further collapse, then the pedal would fail in tension the other side.
Thats what I thought would happen. I am going to play on the full Cosmos works soon and model it with a pin through etc and see what the results say
then. Should be a lot better I think.
Thanks for the loading info Jumpy Guy. Will work on something similar to those for my final designs.
Oh and thanks to everyone for all the input, always most appreciated
David
Sera
http://www.motosera.com
|
|
silex
|
posted on 23/2/06 at 12:58 PM |
|
|
Out of interest, once upon a long century ago I was working as a test engineer, and testing the brakes system in the vehicle was part of my job.
I could apply a steady force of 500lbs (approx 2200N) to a pedal with my right leg and in a sumulated panic braking sutuation (ABS or not) I could
apply an instantanious 950lbs (approx. 4240N)force to a pedal.
Admitadly I weigh in a tad more than your 80kg, but you would be so suprised how much force you are capable of generating on certain situations.
Murphy's 2 laws
1. If it can go wrong it will
2. In case of emergency - refer to rule 1.
|
|
Liam
|
posted on 23/2/06 at 01:19 PM |
|
|
quote: Originally posted by flak monkey
OK tried that, and yes you get different results. The the pedal fails at the weld between the pivot tube and the pedal arm.
I was modelling the pedal with a force on the pad equal to the force being applied by your foot, then restraining the pivot as it cannot move in the
car, and applying a force of 5x the pad pressure to the pivot (since the pedal ratio is 5:1). Whats wrong with this?
Hi there,
Ok i misinterpreted your description of your first model - i thought you just had a restrained pivot and a big load at the clevis and nothing else.
Still, as has been said, the solidworks bundled cosmos isn't realy capable of accurately modelling this situation. If the full version lets you
use pivots as restraints properly you're in business.
liam
|
|
britishtrident
|
posted on 23/2/06 at 01:22 PM |
|
|
FEA and FDA are tools that should only be applied after a liberal chunk of sceptical engineer common sense back of an envelope engineering.
I have straighten a few brake pedals that had bee bent sideways -- mainly on Minis and Imps but also Transits (istr the Transit used a pedal cut
from 8mm thick plate).
[Edited on 23/2/06 by britishtrident]
|
|
Liam
|
posted on 23/2/06 at 01:38 PM |
|
|
Here's an early shot of my nicely overbuilt steel brake pedal, made by my buddy Mark...
Liam
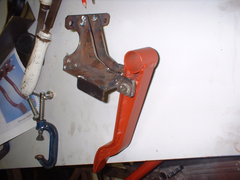  Rescued attachment pedal.jpg
|
|
NS Dev
|
posted on 23/2/06 at 11:30 PM |
|
|
now that ain't gonna bend is it!!!
Who does your lasering?
Retro RWD is the way forward...........automotive fabrication, car restoration, sheetmetal work, engine conversion
retro car restoration and tuning
|
|
Liam
|
posted on 23/2/06 at 11:34 PM |
|
|
quote: Originally posted by NS Dev
now that ain't gonna bend is it!!!
Who does your lasering?
LOL!! He he heee
Hacksaw, files and a bench grinder all the way!
LIam
|
|
NS Dev
|
posted on 23/2/06 at 11:37 PM |
|
|
......now that's patience!! It is funny what designs you can come up with that only use a holesaw and straight lines though! Lots of stuff on my
cars in the past made that way!
Very neat there though around the master cyl mounts, thought it was lasered!
Retro RWD is the way forward...........automotive fabrication, car restoration, sheetmetal work, engine conversion
retro car restoration and tuning
|
|
britishtrident
|
posted on 24/2/06 at 08:48 AM |
|
|
quote: Originally posted by Liam
Here's an early shot of my nicely overbuilt steel brake pedal, made by my buddy Mark...
Liam
Now that would give me confidence :-)
|
|