nitram38
|
posted on 6/4/10 at 08:14 AM |
|
|
MotaLeira Coilover Springs What rating?
Right I'm going to change my air suspension to coilovers with hydraulic rams. My reason is that the car needs to be more predictable than a
variable spring rate that I have now. That also coupled with the ability to dial in shock rates too.
Anyhow, I need to calculate what spring rate I need to start off with.
I have a corner weight guage to check each wheel, but the complications are the pushrod angles and the cam ratio's for the inboard shocks.
I need a formula to work out a starting point, because I'll probably end up changing them a few times, but I don't want to be a long way
off to start with.
The car weighs 480kg so with two people I guess about 680kg.
So if anyone can give me a simple starting point to work out my springs, I'd be grateful
|
|
|
nitram38
|
posted on 6/4/10 at 09:33 AM |
|
|
To be honest I haven't measured them yet but I know they are un-equal cams. Shocks will be normal way up but more horizontal.
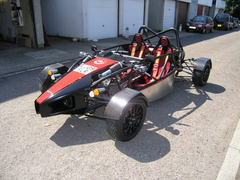 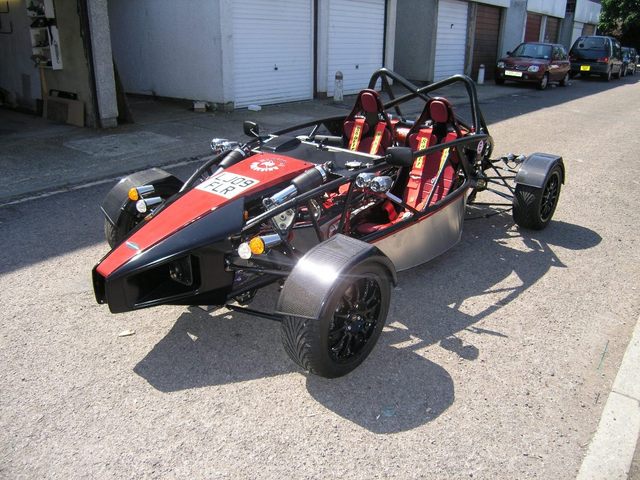 Description
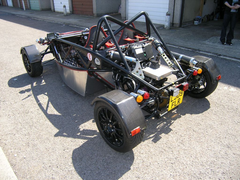  Description
|
|
Frosty
|
posted on 6/4/10 at 10:11 AM |
|
|
You need the SPRUNG weight of the corner, and also the suspension leverage. It's a geometrical nightmare to work out on paper when dealing with
inboard suspension, so my advice to you would be to work out the motion ratio by doing the following:
1) Decide on a base ride height.
2) Jack the car up, remove the damper, and then jack a wheel up so that it sits at base ride height in relation to the chassis (perhaps mark the
pushrod and the body when car is on the ground, and when they line up in the air, you know you are at target ride height).
3) Put a ruler next to the wheel, and a dial gauge on the end of the bell-crank where the damper bolt connects..
4) Jack the wheel up by exactly 10mm, and see what 10mm equates to on the dial gauge (be as accurate as you can).
From this you will know what a 10mm movement at the wheel equates to at the damper, and from here you can calculate the suspension leverage ratio.
(Be warned that this ratio is not constant throughout the suspension compression, but ignore that for now).
Now you can work out a suitable spring to use. The calculations for spring rates in Allan Staniforth's Competition Car Suspension is extremely
helpful. You need the corner weight, and the suspension leverage which you will now have.
You will be able to get very close to an ideal spring based on the above.
|
|
nitram38
|
posted on 6/4/10 at 11:36 AM |
|
|
Right some measurements!
Front suspension no driver passenger. Corner weight gauge is 220 lbs
Rear Suspension
Corner weight gauge 300 lbs
Ratios:
Front: Rod movement 10mm Shock moves 7mm
Rear: Rod movement 10mm Shock moves 5mm
Weights are about right 480Kg is roughly 1060 lbs
need to add 200kg taking weight to 1500 lbs total
On an approx 60/40 split
Front should be 600 lb (300 lb per side)
Rear should be 900 lb (450 lb per side)
Now the ratios need to be taken into account
Am I right in thinking the rear ratio is
450 X 0.5 = 225 Lb
Front is 300 X 0.7= 210 lb?
Should I add some lbs to allow for errors?
Front would have to be minimum of 225 lb but go for 250 lb rears?
[Edited on 6/4/2010 by nitram38]
|
|
Bluemoon
|
posted on 6/4/10 at 12:12 PM |
|
|
quote: Originally posted by nitram38
Right some measurements!
Front suspension no driver passenger. Corner weight gauge is 220 lbs
Rear Suspension
Corner weight gauge 300 lbs
Ratios:
Front: Rod movement 10mm Shock moves 7mm
Rear: Rod movement 10mm Shock moves 5mm
Weights are about right 480Kg is roughly 1060 lbs
need to add 200kg taking weight to 1500 lbs total
On an approx 60/40 split
Front should be 600 lb (300 lb per side)
Rear should be 900 lb (450 lb per side)
Now the ratios need to be taken into account
Am I right in thinking the rear ratio is
450 X 0.5 = 225 Lb
Front is 300 X 0.7= 210 lb?
Should I add some lbs to allow for errors?
Front would have to be minimum of 225 lb but go for 250 lb rears?
[Edited on 6/4/2010 by nitram38]
I think you should have:
450/0.5
450/0.7
.. As the springs need to be a higher rate as you have less movement than at the wheels...
Not an expert! Please check!!!
Dan
|
|
nitram38
|
posted on 6/4/10 at 12:24 PM |
|
|
Originally when I had a 1:1 ratio on my rear springs, the air shocks could not lift the car. I changed it to a 2:1 ratio in favor of the air shocks
and now it works. Therefore the shocks require less effort to lift the car not more.
I am assuming the same for the springs.
Less lbs on the spring side.
|
|
hughpinder
|
posted on 6/4/10 at 12:42 PM |
|
|
I think that, taking the rear suspension, you need 450lbs 'pressure' from lever arm. If 10 mm of movement at the wheel = 5mm at the spring
then you have a lever with a 2:1 mechanical advantage - e.g the spring 'sees' 900lbs. If you want a spring to support this with 1 inch
compression you need a 900lb/inch spring. If you only want to compress the spring 3/4 of an inch the spring rate will be 1200lb/inch, etc.
Then you work out the 'wheel rate' for a 900lb spring and find out that you're going to loose your teeth pretty quick!
IRRC, Wheel rate = (((motion ratio)^2)*spring rate)*sin(spring inclination))
=0.25*900*1 (assume spring at 90 deg to lever) = 225
Also IRRC Staniforth says F1 cars have a wheel rate 400+, soft road cars 60-70, sports cars up to 120, So it sounds like that would be pretty hard
suspension!
There was something about front wheel rate should be higher than rear as well, or maybe the other way round - I can't remember - must do some
homework tonight.
I hope that I remembered all that right!
Regards
Hugh
|
|
Frosty
|
posted on 6/4/10 at 12:48 PM |
|
|
That was quick
I assume with a corner weight gauge you are measuring just the total corner weight and not just the sprung weight. You need just the sprung weight.
Let's assume for a moment that 220lbs is the spring weight (excludes wheel and tyre etc).
First we'll work out the suspension leverage based on your measurements.
If the front rod moves 10mm and gives 7mm at the damper, 10 / 7 = 1.43, so your front dampers have a leverage ratio of 1.43 (so force on the damper is
1.43 times greater than it is on the wheel).
Allan Staniforth recommends that a track based car should start at 130CPM and you might adjust a little from there.
The calculation to work out suspension CPM is 187.8 x sqrt( (spring rate / suspension leverage squared) / corner weight)
So your calculation based on a 200lb spring will be 187.8 x sqrt( (200 / 2.05) / 100 )
This gives a frequency of 125CPM, so looking at a 225lb spring, that will give 133CPM so I'd go with this on the front.
You need to work out how how much weight the car will be carrying when it needs to be at its best and factor this into the total weight of the car,
then to the calculations again. Best to use corner weight scales with driver (or driver and passenger) to get the total weights at each corner.
a 225lb spring will not give 133CPM when carrying two 100kg passengers you see - it will be less.
As for the rear, because of the massive leverage (2:1 ratio), you would need a 600lb spring to give you 133CPM. Again, this is with no weight in the
car, so doing these calculations again with driver and passenger would show the need for even heavier springs.
|
|
Frosty
|
posted on 6/4/10 at 12:51 PM |
|
|
Well done Hugh that's the right way to think about it. It took me a while to type out my post but basically the same conclusion.
Run a super-strong rear spring, or alter the leverage.
I think it's far better to change the leverage since the bell crank mounts will be under some serious strain with that ratio and a high spring
rate.
|
|
daviep
|
posted on 6/4/10 at 01:36 PM |
|
|
quote: Originally posted by hughpinder
I think that, taking the rear suspension, you need 450lbs 'pressure' from lever arm. If 10 mm of movement at the wheel = 5mm at the spring
then you have a lever with a 2:1 mechanical advantage - e.g the spring 'sees' 900lbs. If you want a spring to support this with 1 inch
compression you need a 900lb/inch spring. If you only want to compress the spring 3/4 of an inch the spring rate will be 1200lb/inch, etc.
Regards
Hugh
Nah that's definately backwards, I can say this without any calculation at all, look at the pictures, the shock is on the long arm of the
pivot.
Davie
|
|
nitram38
|
posted on 6/4/10 at 01:36 PM |
|
|
quote: Originally posted by nitram38
Originally when I had a 1:1 ratio on my rear springs, the air shocks could not lift the car. I changed it to a 2:1 ratio in favor of the air shocks
and now it works. Therefore the shocks require less effort to lift the car not more.
I am assuming the same for the springs.
Less lbs on the spring side.
I'm a bit confused, so why did this work?
The air spring was the same before and after the cam change, except it worked under the 2:1 ratio.
Surely the load on the air spring was reduced not increased, therefore required less effort from the air spring?
|
|
daviep
|
posted on 6/4/10 at 01:40 PM |
|
|
quote: Originally posted by nitram38
quote: Originally posted by nitram38
Originally when I had a 1:1 ratio on my rear springs, the air shocks could not lift the car. I changed it to a 2:1 ratio in favor of the air shocks
and now it works. Therefore the shocks require less effort to lift the car not more.
I am assuming the same for the springs.
Less lbs on the spring side.
I'm a bit confused, so why did this work?
The air spring was the same before and after the cam change, except it worked under the 2:1 ratio.
Surely the load on the air spring was reduced not increased, therefore required less effort from the air spring?
I agree.
|
|
nitram38
|
posted on 6/4/10 at 01:43 PM |
|
|
Cheers, I didn't think I was going mad!
|
|
matt_gsxr
|
posted on 6/4/10 at 01:50 PM |
|
|
Isn't it the wheel movement that is important, not the rod movement.
The ratio of wheel motion to spring compression is the important thing. Then you need to remember to square this before determining the spring as
described above.
Regarding the Staniforth recommendations, i.e. ~100cycle per minute, most people run stiffer than this. It isn't clear why Staniforth is too
soft (his numbers are based on successful hillclimb cars), but it might be that we have higher unsprung mass, which is another nasty free variable.
Matt
|
|
Frosty
|
posted on 6/4/10 at 02:06 PM |
|
|
quote: Originally posted by matt_gsxr
Isn't it the wheel movement that is important, not the rod movement.
The ratio of wheel motion to spring compression is the important thing. Then you need to remember to square this before determining the spring as
described above.
Regarding the Staniforth recommendations, i.e. ~100cycle per minute, most people run stiffer than this. It isn't clear why Staniforth is too
soft (his numbers are based on successful hillclimb cars), but it might be that we have higher unsprung mass, which is another nasty free variable.
Matt
Yes.
When I suggested that the motion ratio was measured, it should be measured by moving the wheel 10mm upwards and seeing what comes out at the other end
so to speak.
Looking at the bell cranks, it doesn't look like a 2:1 ratio to me, even with the push-rod angle being what it is.
|
|
nitram38
|
posted on 6/4/10 at 02:17 PM |
|
|
Springs on my car will hardly move a great deal because the car is so low. My whole reason I'm changing from the airspring to spring is to give
me a constant spring rate, irrespective of my ride height and to give me an adjustable damper because I get a very slight oscellation on motorways
without a passenger.
Im going to fit hydraulic cylinder rams under the spring to raise the car over obstacles. The spring rate will stay the same as it is only the shock
getting extended and they will only be used at low speed over speed humps etc.
Surely my air springs are working at the correct rate to lift the car off the deck and drive perfectly well without ripping my mounts off therefore
the replacement steel spring must be the same rate as my airspring to lift the car so should not pose any more of problem?
[Edited on 6/4/2010 by nitram38]
|
|
nitram38
|
posted on 6/4/10 at 02:22 PM |
|
|
quote: Originally posted by Frosty
quote: Originally posted by matt_gsxr
Isn't it the wheel movement that is important, not the rod movement.
The ratio of wheel motion to spring compression is the important thing. Then you need to remember to square this before determining the spring as
described above.
Regarding the Staniforth recommendations, i.e. ~100cycle per minute, most people run stiffer than this. It isn't clear why Staniforth is too
soft (his numbers are based on successful hillclimb cars), but it might be that we have higher unsprung mass, which is another nasty free variable.
Matt
Yes.
When I suggested that the motion ratio was measured, it should be measured by moving the wheel 10mm upwards and seeing what comes out at the other end
so to speak.
Looking at the bell cranks, it doesn't look like a 2:1 ratio to me, even with the push-rod angle being what it is.
I can only go by what my measurement told me.
I measured both points of the cam arm, lowered my car so that the pushrod moved 10mm and then measured the shock mount and that moved 5mm.
That is 2:1?
|
|
hughpinder
|
posted on 6/4/10 at 02:28 PM |
|
|
Don't forget that what was asked was the movement at the spring end for 10mm movement of the wheel - the mount for the rod that pushes the bell
crank will be part way down the arm and may account for some of the overall ratio seen. The bell crank itself may have a 1:1, but if the push
rod is half way down the suspension arm.....
Regards
Hugh
|
|
hughpinder
|
posted on 6/4/10 at 02:31 PM |
|
|
Sorry, I misread that,
I see you measured 10mm of rod movement - so probably 15+mm of wheel movement, is that right?
Hugh
|
|
nitram38
|
posted on 6/4/10 at 02:35 PM |
|
|
My pushrod fixes just behind the bottom wheel hub and within the wheel it'self.
I cant see the ratio being greatly altered.
|
|
Frosty
|
posted on 6/4/10 at 02:44 PM |
|
|
quote: Originally posted by nitram38
My pushrod fixes just behind the bottom wheel hub and within the wheel it'self.
I cant see the ratio being greatly altered.
Yes but the pushrod is not vertical, so the angle of it reduces movement.
Pushrods are usually about 45 degrees on a car, but just to make the point, imagine if it were at 90 degrees (horizontal). The wheels moves, but you
would have zero movement on the bell-crank.
|
|
nitram38
|
posted on 6/4/10 at 02:44 PM |
|
|
As for spring rates and talk of osscillation etc, I need a spring that supports the car plus passengers, not too soft that the car hits the deck or
rolls excessively, not to hard that there is no give.
Surely my choice of spring is limited by whats available and the closest best guess?
I bet after all the calcs I end up changing them again!
Why hasn't some bright spark come up with a pressure type gauge that you fit in place of the coilover that tells you the actual weight
required?
That would erase all this need for calcs!!
[Edited on 6/4/2010 by nitram38]
|
|
hughpinder
|
posted on 6/4/10 at 03:00 PM |
|
|
'Why hasn't some bright spark come up with a pressure type gauge that you fit in place of the coilover that tells you the actual weight
required?
That would erase all this need for calcs!! '
I like that idea - its just that calculations are free and can be done before you build the car, wheras measuring needs the car to already exist, (and
you'd probably want to set all 4 wheels at once). This wold give you the actual force needed to support the car. You would still need to decide
how much compression of the spring is going to be used to hold the weight of the car, and also decide what wheel rate you want to use.
Regarding an earlier comment on Staniforths wheel rates being on the low side - could this be because he suggests using an ARB which allows the use of
softer springs?
Hugh
|
|
MikeRJ
|
posted on 6/4/10 at 04:11 PM |
|
|
quote: Originally posted by nitram38
Surely my choice of spring is limited by whats available
If you are using standard size coil overs with 1.9" or 2.25" springs then your choice is absolutely
massive, both in spring rate and free length.
People have mentioned the frequency of the suspension simply because it's a very simple way of working out what spring rate is suitable for the
weight of your car and a given application (road, track etc.).
As for the ratio between wheel and spring, why not measure it empirically, i.e. jack the car up and raise and lower the wheel whilst measuring damper
movement. Presumably you have designed the system to give a rising rate anyway, and combined with your variable height control this is going to make
your calculations somewhat more complex.
|
|
nitram38
|
posted on 6/4/10 at 04:28 PM |
|
|
The new set up will be at a fixed height with the ability to raise the car without compressing the spring. So I need a spring calculated for the
intial fixed height. When the car is raised it will not matter as it will be used for low speed obstacles. The car will be set up on this intial low
height.
My springs are going to be limited to, the weight required to be carried, the length of spring by the length of my shock and hydraulic ram (meaning
shorter springs) and the shock diameter.
The shock diameter is fixed, the length I need is fixed, only the rate I need to work out.
Maybe there is a massive range of springs, but there will only be one set at the given diameter and length I need available.
So therefore only one spring will do.
Allowing for set poundages available, I'm limited to the poundages available
[Edited on 6/4/2010 by nitram38]
|
|