Theshed
|
posted on 13/3/11 at 02:21 PM |
|
|
Finding reasons not to start welding...
I have been making these bits for a year (including a massive lathe mending session)...I am dreading making a mess of the welding

|
|
|
Theshed
|
posted on 13/3/11 at 02:22 PM |
|
|
Arrrg cant do photos.. quick search for instructions
|
|
scudderfish
|
posted on 13/3/11 at 02:24 PM |
|
|
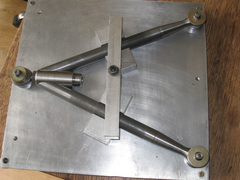  top front jig version I
|
|
Theshed
|
posted on 13/3/11 at 02:24 PM |
|
|
[img]http://locostbuilders.co.uk/upload/3jig.JPG
Phew!
|
|
Theshed
|
posted on 13/3/11 at 02:26 PM |
|
|
Thankyou! Still not worked it out!
|
|
Steve Hignett
|
posted on 13/3/11 at 02:35 PM |
|
|
put [/img] at the end of the statement above...
Basically you've put the html instruction telling "it" this is a photo, but you also have to tell "it" when it stops
being a photo, hence the slash...
|
|
Steve Hignett
|
posted on 13/3/11 at 02:38 PM |
|
|

|
|
Theshed
|
posted on 13/3/11 at 02:47 PM |
|
|
Thanks again -- melted versions in about 3 hours time..
|
|
David Jenkins
|
posted on 13/3/11 at 03:02 PM |
|
|
Can't fault your preparation... everything looks really neat, the fit looks good, and they're nice and clean.
It is worth practising on similar setups until you are reasonably confident that it will work on the 'real' pieces.
|
|
David Jenkins
|
posted on 13/3/11 at 03:04 PM |
|
|
One thing - I hope your rose joints aren't in place when you're welding, else they'll suffer from the heat of welding (it spreads a
long way!)
[Edited on 13/3/11 by David Jenkins]
|
|
PSpirine
|
posted on 13/3/11 at 03:51 PM |
|
|
Surely given that the ends are solid steel, it will be possible to tack them together in the jig, then take the rose joints out and finish the weld? I
doubt 3-4 tacks will put that much heat into them!
|
|
designer
|
posted on 13/3/11 at 07:14 PM |
|
|
Never weld within 3 inches of a rose joint.
That is hell of a jig.
If the rest of the car is made to that standard it will take years!!
[Edited on 13-3-11 by designer]
|
|
steve m
|
posted on 13/3/11 at 07:54 PM |
|
|
The rose joints are facing the wrong direction?
|
|
designer
|
posted on 13/3/11 at 08:05 PM |
|
|
quote:
The rose joints are facing the wrong direction?
Rose joints should be mounted by a vertical bolt.
|
|
Theshed
|
posted on 14/3/11 at 06:55 AM |
|
|
Part welded then ran out of argon.....I must say I find welding round tubes with tig really hard. The welds penetrate but never look pretty...Not
pretty enough to photograph (sulking)
The rose joint in the picture is an old one so was offered up as a sacrifice. It did get very hot!
The car is not a locost so the bearings are the right way around. The vertical bolt orientation plus shims behind the mountings gives room for
adjustment as well as being stronger. I got lazy with the outer joint I was going to make a housing but it was taking forever. The inner housings will
take stake in bearings.
What do you mean "take years to finish"? More than the 8 it has taken to get this far???.......I sometimes wish the shed would burn down
on better days I take the one part at a time approach. Getting the front wheels on will be a huge milestone.
|
|
designer
|
posted on 14/3/11 at 08:00 AM |
|
|
I see you are using the 'old fashioned' panel clamps instead of clecos.
|
|
Mr Whippy
|
posted on 14/3/11 at 08:01 AM |
|
|
tbh after that amount of work and not being happy to weld it, I'd have definitely taken that to a welding shop and got it done professionally
which would have cost what? £20-30 a tiny percentage of the time and money spent so far...
Fame is when your old car is plastered all over the internet
|
|
David Jenkins
|
posted on 14/3/11 at 08:41 AM |
|
|
quote: Originally posted by designer
I see you are using the 'old fashioned' panel clamps instead of clecos.
I have a few of those - not as quick as clecos, but functionally exactly the same. Very useful for tight corners where you can't get the cleco
pliers in!
|
|
Theshed
|
posted on 14/3/11 at 02:18 PM |
|
|
I could have paid somebody else to weld these but that would take the fun out of it. When I started I needed some parts milled. Very straight forward
facing and drilling job. Local engineers said that for cash it would be a mere £1,000. I said no thanks and bought a milling machine. All of the
billet parts in my photo section have been made by me. A CNC lathe followed for much the same reasons. I am a bit annoyed that my welds are not pretty
but very confident that they are strong. I will tidy them up in due course.
The reason I use wind up skin pins is that I bought a biscuit tin full for £10 on ebay! I have around 4000 rivets in my tub each one drilled redrilled
and reamed.....I hate those pins! They rub the skin off your fingers. Too mean to change now. Tub is now 95% complete - those pictures are a little
old.
|
|