Pavel
|
posted on 29/1/05 at 10:17 AM |
|
|
DeDion Tube Construction?
I'm consideering building a dedion set up for a sierra rear end.
Most Dedion tubes are just that tubes.
Do they have to be ?
Can they be made out of RHS? something like 2" square?
regards
Pavel
|
|
|
dozracing
|
posted on 29/1/05 at 11:15 AM |
|
|
Yes they can be, in fact i believe that Tiger do just that on one of theirs.
Kind regards,
Darren
|
PLEASE NOTE: This user is a trader who has not signed up for the LocostBuilders registration scheme. If this post is advertising a commercial product or service, please report it by clicking here.
|
Kissy
|
posted on 29/1/05 at 12:07 PM |
|
|
Try to use round tube, it not only looks better it is far stronger torsionally pound-for-pound
|
|
Cita
|
posted on 29/1/05 at 12:23 PM |
|
|
Here we go again:tube versus RHS 
|
|
undecided
|
posted on 29/1/05 at 12:30 PM |
|
|
well moon cheese is a non starter so round tube much safer
|
|
JoelP
|
posted on 29/1/05 at 12:57 PM |
|
|
i think kissy has worded it correctly here though, stating pound for pound rather than by size!
i would use 2inch square myself to make it easier to line up square.
|
|
mangogrooveworkshop
|
posted on 29/1/05 at 03:57 PM |
|
|
round is the way
[img][/img]
|
|
andylancaster3000
|
posted on 29/1/05 at 10:17 PM |
|
|
By how much are the standard sierra drive shafts too long for the book chassis. Is it possible to use the sierra drive shafts (as they come off the
sierra) on a book chassis, if so how much wider is the rear end.
(Sorry if i have hi-jacked this thread!)
Andy
|
|
chunkielad
|
posted on 29/1/05 at 10:36 PM |
|
|
If you use a 4" wider chassis then you can use them full size so it looks like 4" wider track!!
I would consider the square tubing as it's going to beasier to make yourself rather than trying to bend tube!
|
|
craig1410
|
posted on 30/1/05 at 01:10 AM |
|
|
You don't have to bend the tube. Look at the GTS Tuning design at www.gtstuning.co.uk. They just weld the two halves of the round tube together.
Personally I prefer the design that mangrove shows above as this is the same design as my own but maybe I'm biased...
Cheers,
Craig.
|
|
NS Dev
|
posted on 30/1/05 at 11:24 PM |
|
|
Round tube is no harder to accurately line up than square tube. It may give the illusion of being easier, but in either case you could do with (as a
minimum) a bit of a cobbled up jig of some sort to hold everything still while you weld it up, in which case, the round is as easy as square. (and as
was said above, if nothing else, round looks much better!!)
On the driveshafts subject, remember that custom made (not shortened and welded but custom made from scratch!!) shafts are only £70 each! (from GB
engineering in Nantwich, for those that have missed my previous plugs for this excellent company!!....no connection!!)
|
|
Rorty
|
posted on 31/1/05 at 04:10 AM |
|
|
New billet axles are lovely and simple; you hand over your cash and you have new axles.
Welded tubular axles are fine too. Lobro (probably the largest CV and axle manufacturer in the world) sell weld axles specifically for inserting into
thin wall tube.
Afterall, what's a drive shaft if not a welded tubular structure.
Granted, the torque through the axles is multiplied by the diff, but tubular axles are perfectly acceptable.
 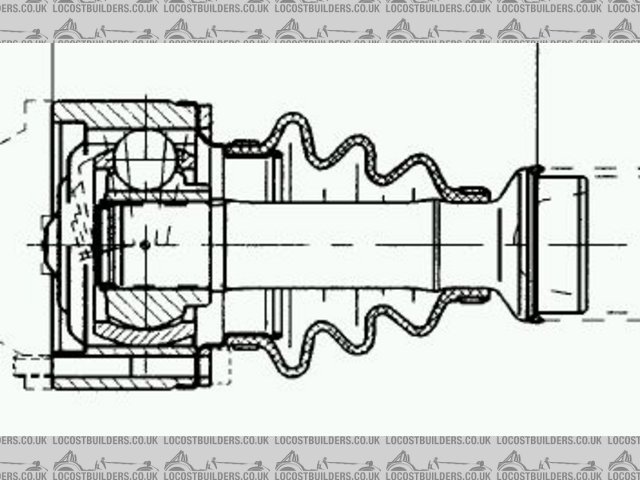 Rescued attachment Lobro_weld_axle.jpg
Cheers, Rorty.
"Faster than a speeding Pullet".
PLEASE DON'T U2U ME IF YOU WANT A QUICK RESPONSE. TRY EMAILING ME INSTEAD!
|
|
britishtrident
|
posted on 31/1/05 at 09:16 AM |
|
|
Caterham also don't bend the tube -- I don't why the general layout of the Caterham tube set up isn't more widely used (litigation
worries ?)
Square section is a bad idea apart from the very minor factor that by weight it isn't as efficient as round at carrying torsional loads--
the strain deformation at the end welds with square section under torsion isn't nice.
|
|
andkilde
|
posted on 31/1/05 at 02:12 PM |
|
|
quote: Originally posted by Rorty
Lobro (probably the largest CV and axle manufacturer in the world) sell weld axles specifically for inserting into thin wall tube.
Ooh!
Those are snazzy. Do you know of any suppliers that stocks these Rorty? Or are they only available to the auto manufacturers in quantity?
Cheers, Ted
|
|
Bob C
|
posted on 31/1/05 at 03:41 PM |
|
|
>>Square section is a bad idea apart from the very minor factor that by weight it isn't as efficient as round at carrying torsional
loads-- the strain deformation at the end welds with square section under torsion isn't nice.
Ah but the only torsional load down the dedion tube is brake imbalance.
Square on the other hand is better at resisting bending, so should perhaps be preferred??? (I might be wrong here.....)
I agree make the damn thing straight if you can - MUST be better!
Cheers
Bob
PS in a recent thread on the round v square subject, someone posted that same wall thickness square had same bending strength as round IIRC - that
feels wrong to me. I'll test some 3/4 by 16g next chance I get.
|
|
flak monkey
|
posted on 31/1/05 at 03:48 PM |
|
|
'Ere we go again...Square is stiffer in both bending and torsion than round as it has a higher second moment of area (polar second moment of
area for tortion) (more material further from the neutral axis).
But when/if square fails it will do so suddenly due to the corners being stress raisers. So it will also fail earlier (at a lower load) than round,
but the deflection up to that load will be much less.
You can make a dedion tube from RHS. For the same failure strength it will be heavier, but a lot stiffer.
Think that makes sense,
David
Sera
http://www.motosera.com
|
|
cymtriks
|
posted on 31/1/05 at 08:08 PM |
|
|
If your car is light weight then you could try 2.25-14gauge which someone reported (was it Rorty?) as being used on a light weight home made seven
clone.
The original Escort axle is about 2.5 inches and again I recall someone stating that it was less than 10 gauge in wall thickness.
I think Caterham use a 2.5 inch tube. I think La Bala uses a 3 inch 16 gauge tube.
If I was doing it I'd use a 2.5 inch 14 gauge tube. This will be very slightly heavier than the 2.25 inch tube but is much stronger and it is
easier to weld than 16 gauge.
Tube strength and stiffness has more to do with tube size than with wall thickness so don't kid yourself that a thick walled small tube will be
as strong as a bigger tube with a thinner wall.
Regarding links I'll suggest a Satchell link with the top links as in the book but with lower links running from the lower rear corners of the
transmission tunnel to the outer ends of the Deon tube. The lower link mounts on the tube should allow a link angle of 30 degrees minimum to the axle
line. So if the link goes out from the tunnel corner by 20 inches it'll need to go back by about 11.5 inches minimum.
Satchell links are simpler, lighter and cheaper than five link designs and do not require a welded wishbone as in the Caterham design. They can also
handle a lot of power.
|
|
Rorty
|
posted on 31/1/05 at 09:08 PM |
|
|
quote: Originally posted by andkilde
Those are snazzy. Do you know of any suppliers that stocks these Rorty? Or are they only available to the auto manufacturers in quantity?
Cheers, Ted
They are a standard catalogue item for all sizes of CVs and should be available through any Lobro retailer. The part # will start with 0616 and then
the relevant joint size after that.
I've used them for some fairly high horsepower cars, but frankly, with all the torque a BEC puts out, a cut-and-shut tubular axle made from a
standard solid axle is fine.
I have cut the ends of solid axles off so I could drill the centres out to 10mm (from both ends), and then welded them into some tube. Nice and light
(also marginally helps spin up for better throttle response) and plenty strong enough if done properly.
Even though axles don't spin as quickly as a prop shaft, it's important to ensure they're reasonably well balanced if they're
welded. I normally check them for run out after they've been welded, and if they're visibly out, I'll nudge them in a press a couple
of times to straighten them. It's not very scientific, but it's all that's required.
I've never had an axle fail since I crudely welded some Imp axles with an arc welder in my early teens.
Cheers, Rorty.
"Faster than a speeding Pullet".
PLEASE DON'T U2U ME IF YOU WANT A QUICK RESPONSE. TRY EMAILING ME INSTEAD!
|
|