NS Dev
|
posted on 11/12/05 at 11:36 PM |
|
|
Controllable rear end roll-steer
Wide open question.........
building a new grasser for 2007, so will be building it during 2006.........
I'd like to incorporate something that I think will enhance early corner handling, but maybe I am wrong.
I want a way of countersteering the rear (driving) wheels during corner entry roll movement, but without toeing both rear wheels out during squat.
Strictly speaking rear wheel or 4 wheel steering is illegal in the regs for Autograss racing, but I think it can be incorporated into a
"normal" toe adjustment system.
The tricky bit is getting it to roll steer without altering toe during pitch changes.
I had an idea of using a rocker/bellcrank to mount the inboard end of the rear trailing arms, and operating the bellcranks vis the anti-roll bar, with
adjustable stops to set the min and max movement........but then when the antiroll bar is unladen, the bellcranks will float and the toe will move
around........
any ideas??
(thinking of some sort of clever over centre arrangement where the rollbar can move the rockers but they can't move
themselves......................just can't picture how to do it.....not very good at clever linkages!)
[Edited on 11/12/05 by NS Dev]
[Edited on 11/12/05 by NS Dev]
|
|
|
Volvorsport
|
posted on 12/12/05 at 12:14 AM |
|
|
a weissach axle in reverse ?
www.dbsmotorsport.co.uk
getting dirty under a bus
|
|
NS Dev
|
posted on 12/12/05 at 12:22 AM |
|
|
pardon my ignorance but wossat!?
|
|
NS Dev
|
posted on 12/12/05 at 12:25 AM |
|
|
ahhhhhhh, just googled!!
Yup, exactly a weissach axle in reverse, nicely put!
Any ideas on doing that but without rubber involved and only affecting the geometry in roll and not in pitch???
|
|
Volvorsport
|
posted on 12/12/05 at 12:31 AM |
|
|
hmmm , can only thik of using the movement of a roll bar .
ie a mechanical link that uses the twisting movement to move a toe link outwards .
are u saying your motor doesnt turn in roll because of a locked diff or something .
what about setting up a weissach axle , with extra toe out as std
www.dbsmotorsport.co.uk
getting dirty under a bus
|
|
NS Dev
|
posted on 12/12/05 at 12:37 AM |
|
|
Yes, locked diff.
Initial turn in is ok, but then the requisite oversteer is purely power/track surface governed. If this could be induced after the initial turn-in has
set the roll angle then I think the car would be easier to drive, and the key to autograss, easier to hold the inside line.
Any hint of understeer mid corner and somebody is in the gap.
Oversteer is easy to correct with steering input, but understeer means being animal with the brake and throttle which is never good for track
positioning and controlled progress.
As I say, might be a daft idea but I think it might just work........need any tricks I can think of!!!
|
|
Volvorsport
|
posted on 12/12/05 at 12:54 AM |
|
|
hmm , ill sleep on it !!
www.dbsmotorsport.co.uk
getting dirty under a bus
|
|
Dusty
|
posted on 12/12/05 at 02:06 AM |
|
|
Wonder if you could achieve an effect by using cranks somewhat along the lines of the Dax suspension system which moves suspension pivot points and
thus camber in roll but tied into steering arms instead?
|
|
NS Dev
|
posted on 12/12/05 at 08:46 AM |
|
|
might be possible, but I think I might be pushing my luck with the scrutineers if there is an obvious "steering arm" involved, rather than
something that looks like a toe adjuster.
I am the club chief scrutineer so it'll be ok at my club but at other events I may not be so lucky!!
|
|
tadltd
|
posted on 12/12/05 at 09:39 AM |
|
|
How about using a gas strut (as found in car tailgates) as the toe-link. You can buy these at different 'strengths' I think. RS Components
sell 'em.
At max extension it won't give toe-out, but will compress to give toe-in. You would need to fiddle with the settings and the geometry to get it
to work...
...just an idea, I haven't fully woken up yet!
Best Regards,
Steve.
www.turnerautosport.com
|
|
MikeRJ
|
posted on 12/12/05 at 12:18 PM |
|
|
quote: Originally posted by NS Dev
might be possible, but I think I might be pushing my luck with the scrutineers if there is an obvious "steering arm" involved, rather than
something that looks like a toe adjuster.
You wouldn't have to do anything suspicious with the toe adjuster, you could do the steering by simply moving the top or bottom ball joints in
or out. Moving the balljoint that gives you positive camber as it toes out would give you an oversteer "double whammy". (I.m assuming a
double wishbone system?)
A variation on the Dax arrangement was exactly what sprang into my mind when I read your first post, though of course the idea behind the dax setup is
to maintain perfect camber in roll. I'm fairly sure you will need to cross connect the left and right suspensions if you want no toe change in
squat etc. as one corners suspension by itself can't "see" the difference between squat and roll.
[Edited on 12/12/05 by MikeRJ]
|
|
MikeR
|
posted on 12/12/05 at 12:47 PM |
|
|
Why don't you do something similar to what Rover did on the 200.
Not sure how to describe it but ....
Mount the rear axle on a trailing arm system, then the chassis mounts for the trailing arms aren't mounted to the chassis at all. They are
mounted to "something" that is mounted to the chassis (i think in the middle). Add a element of compliance into this mounting so that when
the car starts to turn in, that flexes on its mounting causing the rear wheels to 'turn'.
|
|
NS Dev
|
posted on 12/12/05 at 12:48 PM |
|
|
Not double wishbone I'm afraid, it's trailing arm.
Old school but very good at keeping the wheel square to the track during huge pitch movement...............perhaps this pic will explain.......:
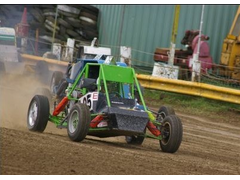 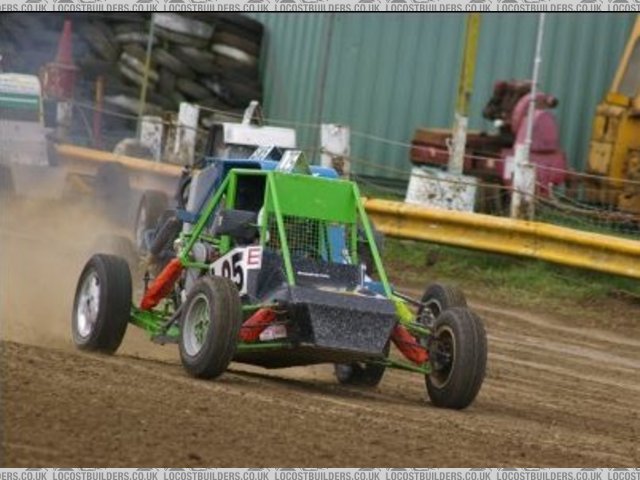 l25startatmap
|
|
MikeR
|
posted on 12/12/05 at 12:57 PM |
|
|
nice to see you infront with the throttle pedel floored
(to those that haven't seen the car race, it really drops at the rear a lot when the power is applied)
|
|
NS Dev
|
posted on 12/12/05 at 01:02 PM |
|
|
thanks Mike!
Was a really good start (especially considering I was the least powerful car there!!) Shame it all went wrong in the first corner eh!!!
[Edited on 12/12/05 by NS Dev]
|
|
MikeR
|
posted on 12/12/05 at 01:13 PM |
|
|
i never mentioned that bit!
see, you're your own worst enemy
Reading up on the weissach axle, it seems a good solution, i'm sure that the s/w i gave you ages ago can model that as well.
Still want you to look into auto camber adjustment as well. The way you shred the one side of the tyre in some races means it would have to be a
benefit.
(plus could help mask some of this as well, but suspect it might be too much to adjust with the zero setup time you have)
have tyou decided on a class yet ? (7?)
|
|
britishtrident
|
posted on 12/12/05 at 02:47 PM |
|
|
I started think of a way to to do it using void bushes and additional control links but then --
thinking out of the box didn't Lotus use a 3 point subframe mounting on the FWD Elan to reduce understeer --- I think 2 of the mountings were
void bushes.
|
|
britishtrident
|
posted on 12/12/05 at 03:53 PM |
|
|
quote: Originally posted by MikeR
Why don't you do something similar to what Rover did on the 200.
Not sure how to describe it but ....
Mount the rear axle on a trailing arm system, then the chassis mounts for the trailing arms aren't mounted to the chassis at all. They are
mounted to "something" that is mounted to the chassis (i think in the middle). Add a element of compliance into this mounting so that when
the car starts to turn in, that flexes on its mounting causing the rear wheels to 'turn'.
ie a torsion beam ? --- yes proven good simple stuff on the rear of fwd car but on the back of a rwd would be bit unkown I think the roll stiffnes
would be too high for good traction of grass.
|
|
MikeR
|
posted on 12/12/05 at 04:13 PM |
|
|
But .... the roll stiffness would be up to how NS Dev designs it.
Also, somethings just occured to me, the max amount of movement we can design in is the max in/out travel in the drave shaft CV joints minus a little
bit to stop the thing going solid.
Any idea how much this is ? How much we're looking for? It might just affect the approach.
|
|
britishtrident
|
posted on 12/12/05 at 05:04 PM |
|
|
Trouble is with a torsion beam the high roll stiffness comes with structure of the beam.
|
|
britishtrident
|
posted on 12/12/05 at 05:09 PM |
|
|
good stuff link
http://www.autozine.org/technical_school/suspension/tech_suspension21.htm
|
|
MikeR
|
posted on 12/12/05 at 05:12 PM |
|
|
but i was thinking of attaching the trailing arms at the end of the beam as attached now to the chassis. The restistance to turn in the beam would be
a factor of friction between the beam and the chassis (and i guess some mounting bush).
In the original setup isn't the beam used as a torsion / anti roll bar, hence the name? (at work, can't really look it up to check).
|
|
NS Dev
|
posted on 12/12/05 at 06:32 PM |
|
|
quote: Originally posted by MikeR
But .... the roll stiffness would be up to how NS Dev designs it.
Also, somethings just occured to me, the max amount of movement we can design in is the max in/out travel in the drave shaft CV joints minus a little
bit to stop the thing going solid.
Any idea how much this is ? How much we're looking for? It might just affect the approach.
Loads of movement in the CV's Mike. The joints themselves are std ford, but the driveshafts have 4 inches of slide travel through the joints as
well as they are "long spline" shafts which plunge through the joint splines as well.
Certainly wouldn't be looking at much movement tho, only talking a few mm, but it needs to be controlled, I am not sure about rubber bushes,
would like an active mechanical control that can be locked out if needs be really.
The whole idea may well be flawed, but I am inquisitive!
Class 7 Mike, deffo now.
Prob Volvo T5 minus turbo but plus eaton supercharger. All stuck on a spaceframe in the smallest shell that will hold it........don't think a
mini is big enough tho, may need to be a pug 205 I reckon!
Checked out and Omex "big" ecu will run the 5cyl coil on plug engine no bother, and run boost control, knock sensor, startline rev limiter
all manner of crap that I don't understand......just need to save the £800 for the ECU ho ho ho!!
|
|
MikeR
|
posted on 12/12/05 at 06:51 PM |
|
|
[cough] megasquirt [cough]
I know, i know it involves some work but its about 500 pounds cheeper!!!
How much is your time worth again?
|
|
NS Dev
|
posted on 13/12/05 at 12:32 AM |
|
|
..........................if somebody can advise me how to run a 5 cyl engine with coil on plug ign on megasquirt then I am open to the idea.......not
sure it's poss tho.
|
|