cjtheman
|
posted on 28/1/07 at 01:13 PM |
|
|
wishbones
i know it has been covered thousands of times i have done search on it and gone through pages and pages of posts but has anybody come up with a good
design on upper and lower wishbones i know that upper wishbones need 22 mm off set instead of 11 mm that the book states
but cant find any thing on the lower wishbones other than there have been failures due to position of the brace plate ( weld in the center of the tube
than on top of the tube) any help please before i make them wrong as i have already done so on the bottom bones ( made to book spec ) many thanx
colin
|
|
|
ecosse
|
posted on 28/1/07 at 05:27 PM |
|
|
i don't know whether you are using tina or maxi bj's but this is what I did for maxi ones, additional weld points are marked in red.
Hope this helps
Cheers
Alex
 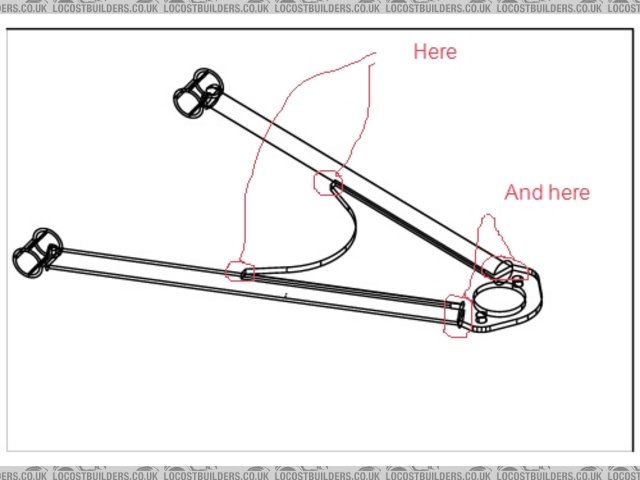 Rescued attachment bottomwishbonetest.jpg
|
|
DIY Si
|
posted on 28/1/07 at 05:34 PM |
|
|
Also, try to move the shock mount as far out as possible, as this is one of the main weaknesses, as it puts a large bending load on the bone.
“Let your plans be dark and as impenetratable as night, and when you move, fall like a thunderbolt.”
Sun Tzu, The Art of War
My new blog: http://spritecave.blogspot.co.uk/
|
|
907
|
posted on 28/1/07 at 06:50 PM |
|
|
Hi.
There has been so much discussion on bottom bones that I think that people are reluctant to post there designs, for fear of criticism.
Because mine are stainless I tend to think that maybe my design is non applicable for most of you.
If s/s is constantly flexed it will work harden and crack so I have increased material thickness to combat this.
Tubes are 22mm od x 2mm thick, and plate is 4mm, as are all the brackets.
The Cortina b/j has had the bent edge cut off and additional holes drilled. This enables it to be mounted under the plate rather than above.
IMHO this is stronger as it doesn't rely on the bolts supporting the weight of the car.
Having said this, if I made steel bones I think that I would still stick with the same material thicknesses.
It is my opinion that 3/4" x 16swg tube is not quite man enough. I stress this is just my opinion.
There's a pic in my photo archive but it has been posted on caster threads so you have probably seen it.
Bottom one is to the book, top has the 22mm offset.
Hope this helps.
Paul G
p.s.
Basicly, the design is the same as Alex's above for the Maxi bj's. Nice that.
[Edited on 28/1/07 by 907]
|
|
cjtheman
|
posted on 28/1/07 at 09:27 PM |
|
|
thanks all for your input this is a great site for information
cheers
colin
|
|
MikeRJ
|
posted on 29/1/07 at 08:31 AM |
|
|
quote: Originally posted by cjthemanthere have been failures due to position of the brace plate ( weld in the center of the tube than on top of
the tube)
That is not the main design flaw. The problem with many wishbones is the straight edge at the back of the shock mounting plate which is a bad stress
raiser. Putting a generous radius on this edge to minimise this is a good idea (as shown in the design ecosse posted).
|
|
ecosse
|
posted on 29/1/07 at 11:12 AM |
|
|
Should have added (and as per Paul's advice) I went bigger on the tubes 25mmOD x 2mm which is overkill probably, but as the bones are a fair
bit wider than standard and as the bottom shock mount will have to be further out than is considered optimal, I went the safe rather than the Chapman
route
Cheers
Alex
|
|
blueshift
|
posted on 30/1/07 at 01:40 PM |
|
|
I went for 25mm x 1.6mm wall and a similar design to that shown above. with little fillets where the end of the arms meets the base plate
happily I had a friend who worked with a laser sheet cutter at the time.. he quit since though 
|
|