Gakes
|
posted on 7/4/08 at 08:13 PM |
|
|
Carbon fibre and GRP chassis
Hi guys and gals
I have been doing tons and tons of research on the ultimate middy road-going sports car for a while now and only recently have I thought of using
carbon and glass fibre in my chassis. Maybe a front tubulalar section for suspension that bolts onto a carbon/glass fibre mid/passenger section (kind
of like a reinforced bucket) that bolts onto a rear section that houses the engine and rear suspension.
Has anyone here ever attempted one of these possibilities or am I a bit off track again?
I want to make my car as modern as I can, and try to incorporate different materials. If theres anyone looking to go this route, I'd love to
chat and exchange info.
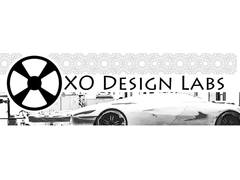 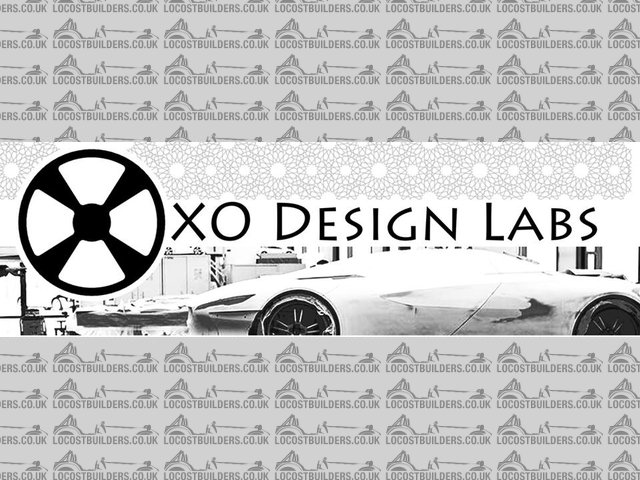 Description
|
|
|
Paul TigerB6
|
posted on 7/4/08 at 08:21 PM |
|
|
Very advanced for many on here but there are a few others doing similar to what you plan.
You might like to have a good read here for inspiration.
|
|
Volvorsport
|
posted on 7/4/08 at 08:31 PM |
|
|
certainly possible .
i was going to do that until i got side tracked .
www.dbsmotorsport.co.uk
getting dirty under a bus
|
|
Gakes
|
posted on 7/4/08 at 08:33 PM |
|
|
Cheers Paul. I have come across the DP1 already. very well refined design he has there. Still uses a tubular frame throughout though with a carbone
fibre shell. What I am looking for is info on how strong the carbon/glass fibre chassis are and if anyone has tried it, is it costly? Recently, carbon
fibres' popularity and newly found manufacturing processes has brought down the price a bit, so its kinda in reach. This is from a South African
context
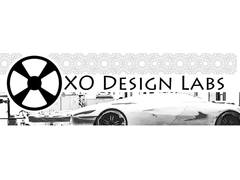 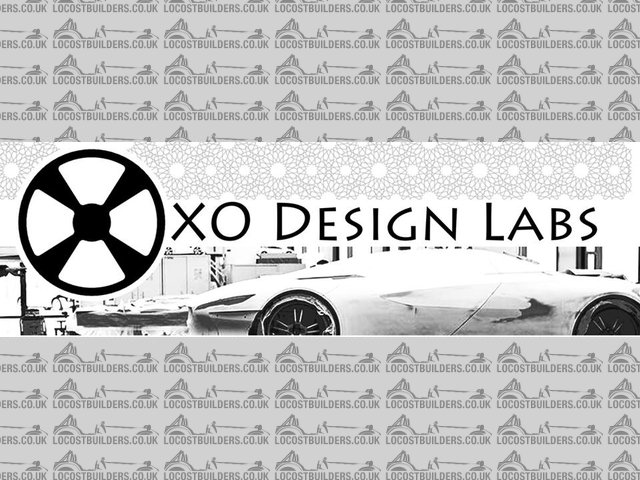 Description
|
|
Gakes
|
posted on 7/4/08 at 08:37 PM |
|
|
Volvo sport
Have worked out anything in the process? ...design, costs, strengths???
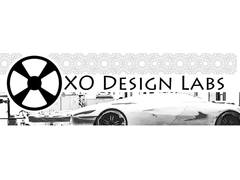 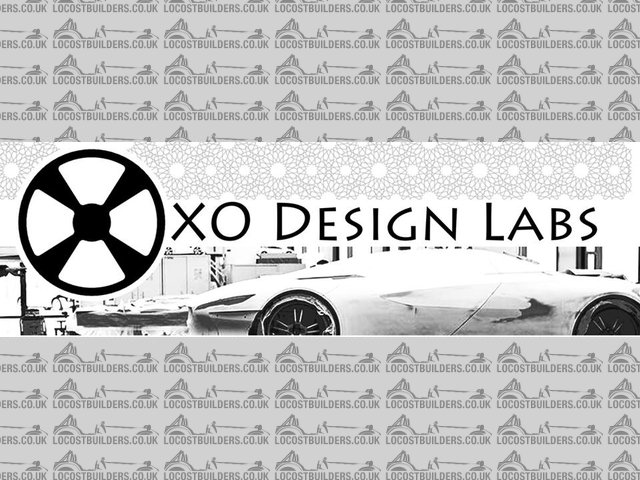 Description
|
|
nitram38
|
posted on 7/4/08 at 08:41 PM |
|
|
I hate to burst your bubble, but carbon fibre is a bit more complicated to make good strong bulkheads and the like.
The technology that goes into them to make them strong means using other fibres, weave patterns and an autoclave big enough to remove all of the
air.
Unless you have a bottomless wallet or your dad owns Maclaren, I think you should give it a miss. (at least for structural componants)
[Edited on 7/4/2008 by nitram38]
|
|
Richard Quinn
|
posted on 7/4/08 at 08:43 PM |
|
|
Unless you have significant experience of this type of construction I would advise against it. I tinker with carbon fibre/epoxy moulding and have done
for many years. Carbon fibre can provide impressive stiffness for a given weight but the impact resistance is less than impressive.
Most exotic composite race cars are built using aluminium (or similar) honeycomb materials faced with carbon fibre and any moulded parts are generally
made from pre-preg which helps achieve the optimum resin content with a panel containing 4 or 5 layers of carbon fibre measuring less than 1mm in
thickness. This type of moulding requires the use of an autoclave to cure under elevated temperature and pressure. It is possible to cure in an just
in a programmable oven but my one attempt at moulding pre-preg ended up with me achieving my strongest bond ever. Unfortunately it was the bond
between the part and the mould (even using proper chemical release agents)! Oh yes, and pre-preg usually needs to be stored frozen.
|
|
Gakes
|
posted on 7/4/08 at 08:50 PM |
|
|
Nitram38,
thanks for the comment. I have worked and designed for a fibreglass mould and plug manufacturing company. Guys that worked in the factory told me that
carbon fibre is worked in the same way that GRP is. I know that Huge car companies use ovens to cure them and machines to extract air from them. But,
the same basics apply to GRP and carbon fibre.... Apply resin, then the mat, roll out air bubbles then repeats these steps for another layer. I have
come across a site of a kayak manufacturer. He uses carbon fibre in that same way
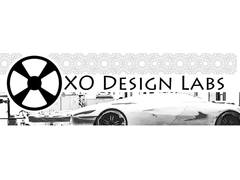 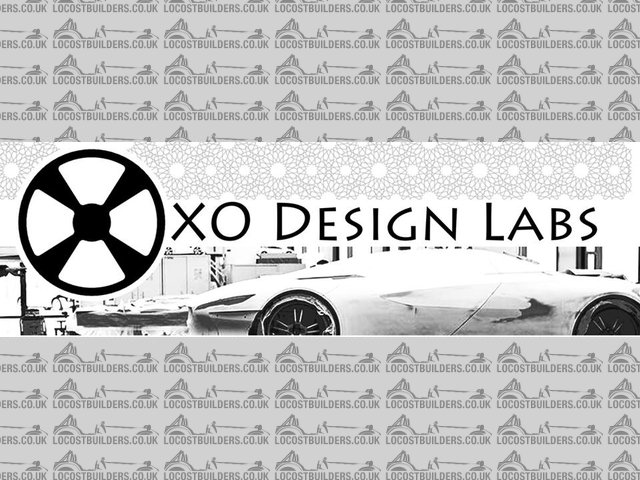 Description
|
|
Gakes
|
posted on 7/4/08 at 08:54 PM |
|
|
quote:
Richard Quinn
Unless you have significant experience of this type of construction I would advise against it. I tinker with carbon fibre/epoxy moulding and have done
for many years. Carbon fibre can provide impressive stiffness for a given weight but the impact resistance is less than impressive.
Most exotic composite race cars are built using aluminium (or similar) honeycomb materials faced with carbon fibre and any moulded parts are generally
made from pre-preg which helps achieve the optimum resin content with a panel containing 4 or 5 layers of carbon fibre measuring less than 1mm in
thickness. This type of moulding requires the use of an autoclave to cure under elevated temperature and pressure. It is possible to cure in an just
in a programmable oven but my one attempt at moulding pre-preg ended up with me achieving my strongest bond ever. Unfortunately it was the bond
between the part and the mould (even using proper chemical release agents)! Oh yes, and pre-preg usually needs to be stored frozen.
OOOOh. so it looks like im pissing in the wind again.
How about glass fibre chassis anyone?
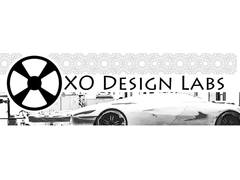 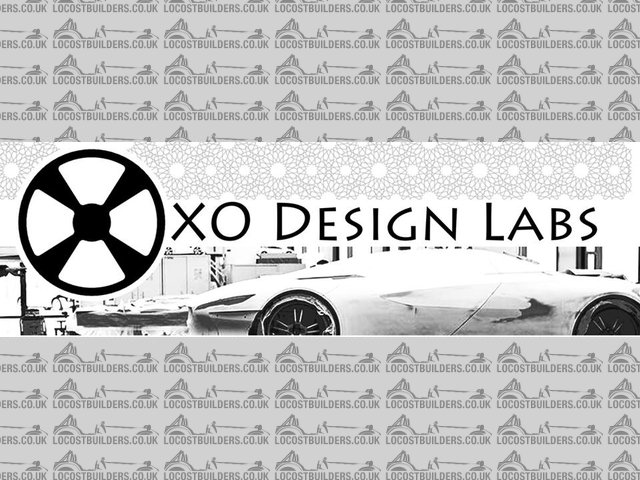 Description
|
|
Triton
|
posted on 7/4/08 at 09:03 PM |
|
|
oooo glass fibre chassis....you been peeping
My Daughter has taken over production of the damn fine Triton race seats and her contact email is emmatrs@live.co.uk.
www.tritonraceseats.com
www.hairyhedgehog.com
|
|
Griffo
|
posted on 7/4/08 at 09:04 PM |
|
|
fo9r the cost associated with it you may be better looking at aircraft grade ali? then again maybe not. im sure someone will know more than me
|
|
Richard Quinn
|
posted on 7/4/08 at 09:05 PM |
|
|
I'm not wanting to p*ss on anyone's chips but even something like a fairly standard West epoxy laminate really needs to be vacuum bagged
to get a decent strength to weight. It also needs to be cured and post-cured at a higher temperature than a polyester resin to achieve full
strength.
It isn't a black art (well, I suppose it is black and does look nice!) but if you are looking at a basic wet lay up then I certainly
wouldn't do it for anything structural/safety critical
|
|
Triton
|
posted on 7/4/08 at 09:09 PM |
|
|
I'm using fibreglass to make mine but using something groovy in the ingredients to add stiffness yet weighs nowt...
My Daughter has taken over production of the damn fine Triton race seats and her contact email is emmatrs@live.co.uk.
www.tritonraceseats.com
www.hairyhedgehog.com
|
|
Gakes
|
posted on 7/4/08 at 09:18 PM |
|
|
quote:
Triton
I'm using fibreglass to make mine but using something groovy in the ingredients to add stiffness yet weighs nowt...
C'mon....let me in on that secret pls.
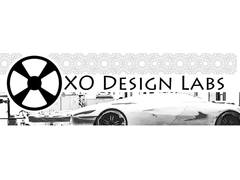 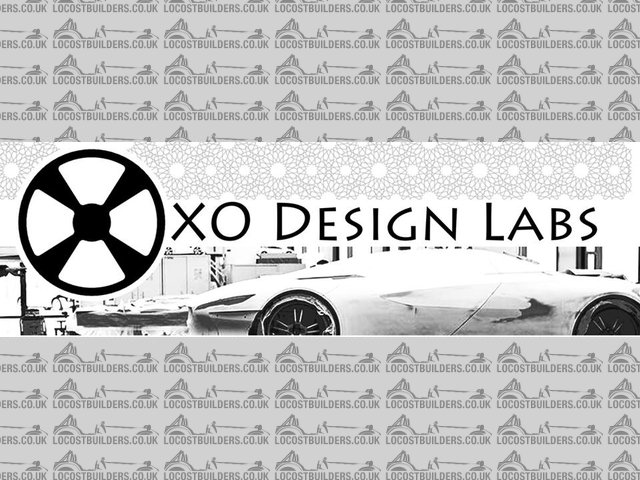 Description
|
|
Triton
|
posted on 7/4/08 at 09:27 PM |
|
|
Loads of blue smarties, hardest bit is eating all the other ones first..and doesn't matter then if car isn't any good as will be too fat
to get in it anyway..
Seriously it's not that new but it is for a car so if i write it here do you promise not to let anyone else read it?....
My Daughter has taken over production of the damn fine Triton race seats and her contact email is emmatrs@live.co.uk.
www.tritonraceseats.com
www.hairyhedgehog.com
|
|
Triton
|
posted on 7/4/08 at 09:33 PM |
|
|
Gakes,
u2u'd you meduck
Mark
My Daughter has taken over production of the damn fine Triton race seats and her contact email is emmatrs@live.co.uk.
www.tritonraceseats.com
www.hairyhedgehog.com
|
|
RK
|
posted on 7/4/08 at 09:41 PM |
|
|
Doesn't anyone build a car for 250 anymore?
|
|
Volvorsport
|
posted on 7/4/08 at 09:43 PM |
|
|
www.darrian.co.uk
www.dbsmotorsport.co.uk
getting dirty under a bus
|
|
Gakes
|
posted on 7/4/08 at 10:03 PM |
|
|
thanks guys.
Triton, I U2U'd u 2 mate. This must be one of the greatest forums if not the best ever. So much knowledge floating around.
Has anyone made any progress on the 3D model hosting or something? I have a few models I dont mind sharing
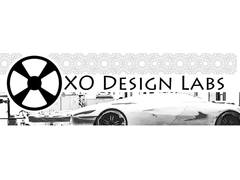 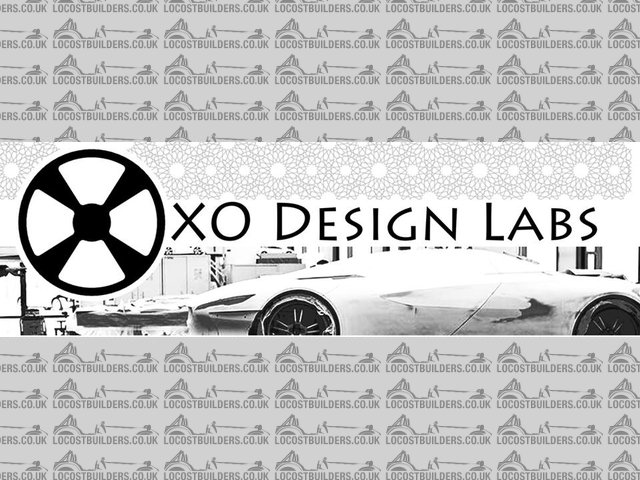 Description
|
|
worX
|
posted on 7/4/08 at 10:05 PM |
|
|
Is it a layer of sandwiched foam?
quote: Originally posted by Triton
Loads of blue smarties, hardest bit is eating all the other ones first..and doesn't matter then if car isn't any good as will be too fat
to get in it anyway..
Seriously it's not that new but it is for a car so if i write it here do you promise not to let anyone else read it?....
|
|
Volvorsport
|
posted on 7/4/08 at 10:13 PM |
|
|
the other thing you can use is parabeam .
its used in grp pressure vessels , and can be used with normal resin .
or a couple of sheets of teklam to get you going .
do a google .
www.dbsmotorsport.co.uk
getting dirty under a bus
|
|
Triton
|
posted on 7/4/08 at 10:28 PM |
|
|
The new smartie tubes are just right as nice shape and glue together easily. Like i said before the down side is the amount of munching to get said
tubes is a pain but needs to be done.
Place the odd blue one for right affect and bingo....only smarties have the answer!
But that might be all a load of gobbledygook for all I know...it may well be the yellow ones needed...
My Daughter has taken over production of the damn fine Triton race seats and her contact email is emmatrs@live.co.uk.
www.tritonraceseats.com
www.hairyhedgehog.com
|
|
twybrow
|
posted on 7/4/08 at 10:46 PM |
|
|
From the sound of it, what you would like to build is the same basic design as the Mclaren SLR (our sister company builds them and the Koenigsegg -
damn they look fine in bare carbon!). The design that goes into the tub is vast. When you think of using composites, then you need to consider so much
more than just the material choice. CFRP is a wonderful material, assuming it is processed well, and used correctly in a well engineered design. The
geometry, the material, the thickness, the process etc etc etc can all play a massive role in determining the final strength/stiffness properties.
It is by no means impossible for an amateur builder to design and manufacture something really effective (I think Syd Bridge has done something
similar in the past?). But personally, I wouldn't. As you cant design, test and redesign, you would need/want to over engineer it to be on the
safe side, then you may find other materials would have been better to work with.
|
|
jono_misfit
|
posted on 7/4/08 at 11:08 PM |
|
|
There are a number of hillclimb cars made of pre preg carbon fibre that were designed and manufactured at home. A lot are done using vaccume bagging
and elevated cure, not under pressure in an autoclave.
There are a lot of them that have survived being attacked by moving tree's / crash barriers without significant injuries to the drivers.
Personally i think one of the biggest problems will be getting decent quality carbon, at a sensible price, in a sensible time frame. Its too popular.
|
|
Benonymous
|
posted on 8/4/08 at 05:06 AM |
|
|
Years ago I read an article in a motoring magazine about how Morris 1100's were made in GRP for sale in Spain (I think). I've Googled it
but there doesn't seem to be any references to it anywhere. It wasn't an April fools joke, the article was supported by a number of
pictures showing the mould making process. As I recall, the whole car was made of regular fibreglass and polyester resin. There were a few kits in
the 70's with fibreglass tubs too I think. There's no reason why a fibreglass tub wouldn't work. Special attention would have to
be paid to areas of high stress but it'd be perfectly feasible. The main difficulty you'll have with it is getting it past the
regulations. A tubular space frame has much more easily calculated strength. As otheres have pointed out, the way a structure is made with
composites and the techniques used will have just as big an effect on the final strength of the finished part as the design itself.
Don't forget, you're the crash test dummy in the equation.
|
|