Volvorsport
|
posted on 13/12/06 at 06:18 PM |
|
|
are you suggesting we make robin hoods now syd ?
what about these ?
www.darrian.co.uk - 2 motoring news championships and the British GT championship - cant be doing much wrong .
ive seen the aftermath of big accidents , and i think , if i make one , ill live !!!
www.dbsmotorsport.co.uk
getting dirty under a bus
|
|
|
ettore bugatti
|
posted on 13/12/06 at 07:12 PM |
|
|
My advise:
KISS
keep it simple and stupid
|
|
NDC790
|
posted on 13/12/06 at 10:36 PM |
|
|
Is stainless a bit messy to cut (I say this teasing a ss splinter out of my hand between typing) and at 1.2mm thick you would need quite a large
gilateen, to large for my budget.
|
|
kb58
|
posted on 14/12/06 at 12:16 AM |
|
|
I've found that in general, splinters are only a REAL problem when using a die-grinder.
If you use one of those cutters that has the scissor-type cutting head, that works well. It's the diabolically sharp edges that cut like a
knife, you have to watch out for.
Mid-engine Locost - http://www.midlana.com
And the book - http://www.lulu.com/shop/kurt-bilinski/midlana/paperback/product-21330662.html
Kimini - a tube-frame, carbon shell, Honda Prelude VTEC mid-engine Mini: http://www.kimini.com
And its book -
http://www.lulu.com/shop/kurt-bilinski/kimini-how-to-design-and-build-a-mid-engine-sports-car-from-scratch/paperback/product-4858803.html
|
|
Dick Bear
|
posted on 14/12/06 at 04:20 AM |
|
|
Thanks once again,Syd!
I'll U2U with some specific question I have on the mono configuration.
Regarding cutting of Ssteel. I've always had good luck getting a clean edge on Ssteel with my plasma cutter. Doesn't cause any edge
distortion or out-of-straights associated with sissor-types and is ready for body panel tac-'n-stich welding technique.
Some plannishing of the seams will be necessary but other than that being a bit more difficult in Ssteel than it is in aluminum it should be pretty
straight forward, eh?
Dick Bear
www.marketpointproductions.com
|
|
Syd Bridge
|
posted on 14/12/06 at 09:07 AM |
|
|
I regularly cut stainless steel with the 4 1/2"grinder witrh the 1mm cutoff disc. Knife through butter! No mess and splinters. Just clean up the
sharp edges (which you get with any metal cut, not just ss), with a flap disc on the second grinder.
For a guillotine, the 1.2 ss is no more difficult than ms. Maybe I'm lucky having a few places local who have the huge hydraulic things that cut
12mm plate with ease. 
|
|
NDC790
|
posted on 14/12/06 at 10:52 PM |
|
|
I took som pic's of an Elise chassie today at work, it had some temp stickers left on it from where the bonding was baked, temp went up to
175degC, if that sheds any light.
My point about cutting SS is that, unless you have some expencive kit, it's messy to cut, far more messy than ally (that's not that i dont
like mess)
More pics of the elise chassis on my profile, if you intrested!
[Edited on 14/12/06 by NDC790]
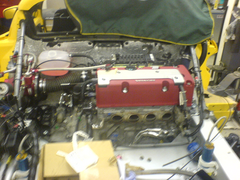  Rescued attachment Picture 043.jpg
|
|
Dick Bear
|
posted on 15/12/06 at 01:12 AM |
|
|
"Messy" in what way?
quote: Originally posted by NDC790 My point about cutting SS is that, unless you have some expencive kit, it's messy to cut, far more
messy than ally
I'm not clear what you mean by the term "messy". In what way do you feel cutting SSteel is "messy"? I want to
understand what yu mean. Is it messy meaning dangerous, difficult, disruptive, costly; i'm not sure what you mean by that term in this case.
In my build there will not be a kit involved as the project will be scratch built based on my own design. So knowing exactly what you mean by
"messy" will aid me I'm sure.
Dick Bear
www.marketpointproductions.com
|
|
kb58
|
posted on 15/12/06 at 03:41 AM |
|
|
Messy to me means it's hard to handle without taking extra care.
If a die-grinder is used, it produces 1000s of stainless splinters which are so small you can't even see them to remove from your hands. They
even go through leather gloves. Cutting the material with shears leaves a very sharp edge, much sharper than steel or aluminum.
I know this because I have a stainless floorpan.
Mid-engine Locost - http://www.midlana.com
And the book - http://www.lulu.com/shop/kurt-bilinski/midlana/paperback/product-21330662.html
Kimini - a tube-frame, carbon shell, Honda Prelude VTEC mid-engine Mini: http://www.kimini.com
And its book -
http://www.lulu.com/shop/kurt-bilinski/kimini-how-to-design-and-build-a-mid-engine-sports-car-from-scratch/paperback/product-4858803.html
|
|
TheGecko
|
posted on 15/12/06 at 05:47 AM |
|
|
quote: Originally posted by NDC790 unless you have some expencive kit
quote: Originally posted by Dick Bear In my build there
will not be a kit involved as the project will be scratch built based on my own design.
Dick, just to clarify that bit of it. When NDC790
used the word "kit" I'm pretty sure he was using it in the common English slang way, meaning tools/equipment - as in "That
3/16" Gripley-Thorton is a nice bit of kit isn't it?" - rather than referring to a kit-car. NDC790, care to confirm (and perhaps
give a real name we can refer to you by)?
Dominic
|
|
Dick Bear
|
posted on 15/12/06 at 06:08 AM |
|
|
Thanks gt58 for sharing your definition of messy with us.
Your mini floor pan must have been a real 'bear', (pardon the pun) to be even partially responsible for formulating a definition for the
word 'messy'. :-)
I agree that extra care is required when handling sheet material!
I wonder what was meant?.... 'messy' is such a generic
word.
Dick Bear
www.marketpointproductions.com
|
|
Dick Bear
|
posted on 15/12/06 at 06:20 AM |
|
|
Dominic,
You snuck one in on me while my typing expertise was showing its' lack of expertise!
Thanks for the clearification... It always interesting to read the different British words on the site. Most times they don't throw me but
there are times when I know a word I've not ever heard before means something very specific to everyone else and I haven't a clue.
Ironically I'm currently trying to find out what is 'messy' when working with Ssteel. I really want to know... been thinking
about it all day. :-)
Thanks again.
Dick Bear
www.marketpointproductions.com
|
|
Syd Bridge
|
posted on 15/12/06 at 09:01 AM |
|
|
SS is no more 'messy' to me than ordinary mild steel. Go near any metal with a die grinder, and depending on the cutter used, you'll
get those splinters. NOT JUST WITH STAINLESS!!!
As I put, I cut it with the 1mm wheel on the 4 1/2" grinder with no probs. The sharp burr you get with a guillotine, again, is something that is
on all metals guillotined.
When you work with metals often(as I do, and obviously Mr.Bear does), you learn to deburr everything as soon as it's cut. And gloves become the
normal everyday workwear.
You lot take fright at the slightest thing. Bunch of pansies!
Some common sense would go a long way. But then again, common sense seems to be a rare commodity these days, from the top of the country's
leaders to the lowest labourer.
Cheers,
Syd.
Oh, and I would hope that the Elise chassis are not cooked at 175c, that's getting into dangerous territory for aluminium, of any sort. Most, if
not all, of the epoxy adhesives used in the auto stuff is below 140c.
[Edited on 15/12/06 by Syd Bridge]
|
|
Peteff
|
posted on 15/12/06 at 11:16 AM |
|
|
I resemble that remark syd
Having worked as a fettler on cast iron, in steel foundries casting stainless and a boiler factory I think I've had my share of metal. Someone
once remarked that everything you do to metal either makes it sharp so it cuts you or hot so it burns. In the boiler factory we had guillotines that
would cut and presses that would punch holes in metal 10mm thick and the thicker you get the less sharp edges you get.
yours, Pete
I went into the RSPCA office the other day. It was so small you could hardly swing a cat in there.
|
|
NDC790
|
posted on 15/12/06 at 10:00 PM |
|
|
Sorry Dick, please forgive me.
By kit I ment - equipment/tools.
& by messy I ment - dust, fileings, sharp edges, time to cut Ect.
As you may have guessed, i'm better with a spanner & welder than I am on com-po-ter!!
And sorry again NDC is me, Nicholas David Carr...........but Nick is fine!
It's very dificalt on here to judge other peoples experience, abilities and facilities, if thay have any, for me, I have some of the first two,
but none of the last. So knowing what I want to do and being able to achive it, are two differant things. I've been spoiled at work in the past,
being able to use any tool or machine when ever needed. As my Dad call's me, Mechanical Tart.
[Edited on 15/12/06 by NDC790]
|
|
crbrlfrost
|
posted on 15/12/06 at 10:45 PM |
|
|
Sorry, had to drop an idea into the pool since this thread got me thinking last night. What about a steel/balsa construction. I did a test piece last
night, a simple 12x12'', 22ga carbon steel and 1/4 balsa core and it is incredibly stiff. and comes in at 3lb/ft^2. I'm doing more
test pieces of 24 and 26ga skins this weekend and the weight should drop roughly 17% between ga. I'll do some puncture and modes of failure
testing next week, as well as machinability. I'm curious about how well routing would work. But these samples are done very grass roots style.
Glass beaded the skins to get rid of rust and contamination, generic 2 part "tuffy" grade epoxy and a couple of weights for pressure. I
did do a 100C post cure, but a lower temp post cure can be done in a standard garage environment with a little imagination. Naturally the core
thickness can be increased for stiffness but I'm keeping them all the same for consistency in testing right now. Anyway, just a thought for
consideration. Cheers!
|
|
Dick Bear
|
posted on 15/12/06 at 10:56 PM |
|
|
Thanks Nick,
That is basicly what gt58 and others thought you had meant but I just didn't want to miss some really messy situation with Ssteel that had been
experienced by you.
Although I don't have everything I might want, I do have most everything in the way of "kit stuff" (did I use that word correctly)
needed for metal fabrication and having what I do I haven't experienced stainless to be any more "messy" than other metal
materials. As Pete said.... it all cuts and burns regardless of its' make-up. It is however great fun to work with!
Thanks again for clearing the mystery!
Dick Bear
www.marketpointproductions.com
|
|
NDC790
|
posted on 15/12/06 at 11:46 PM |
|
|
No problem Dick.
I guess it's a personal thing, myself I like using ally, posibly the motorsport backgrownd, SS too heavy!
But before everyone starts, JUST MHO!
For what it's worth.
Nick.
Dick, like the lugfast!
[Edited on 16/12/06 by NDC790]
|
|
Dick Bear
|
posted on 17/12/06 at 08:46 AM |
|
|
Ref. LugFasts
Hey Nick,
Thanks for your thought on LugFasts.
You must have been checking out my MarketPoint Productions web site. It was on a very hot and humid day at Bristol, TN while I was helping one of my
charges set-up the Winston Cup Scoreboard and communications sytem for the night race that I watched from the press box all the teams, but especially
the Jack Roush team, sweeting out the process of attaching five lug nuts to what seemed to be an acre of wheels. Seeing the 4-men involved over
several hours of time I thought there must be a better way to do this than what they were doing.
That began my experimenting with alternatives until I arrived at the LugFasts solution. I patented it around '95 and now they have become a
mainstay on pit roads across the US and Canada. When the Rolex series began to require green flag pit stops a couple years ago LugFasts were quickly
expanded into that racing environment as well.
If your racing efforts involve pit stops I'd be happy to send you a few gratis tubes to try out.
Cheers,
Dick bear
www.marketpointproductions.com
|
|
Doug68
|
posted on 18/12/06 at 07:12 AM |
|
|
Hi Dick,
How do you intend to get the ground effects to work?
My understanding is that a vehicle needs to be very close to the ground to get a ground effect and preferably sealed at the sides (Going back to the
F1 ground effect era).
I had a conversation once with an ex-automotive aerodynamicist who gave me the impression that he felt very little could be done under a road car to
help with aerodynamic grip.
On the folded and riveted structures I originally wanted to go this way. Having spent a couple of years working in aircraft design it appealed to me
from a manufacturing point of view, though the complexity of the math problem was not one I wanted take on for my first project.
An alternative might be the type of hybrid structure I and Fred W B are doing where the main loads are carried in steel members with alloy structures
being used improve the stiffness of the whole frame. I guess the difference being if the alloy fails in this situation you get a slightly wobbly car
and not a disaster.
One thing I think you should do if you go down the all alloy route is treat the car like an aircraft in terms of inspection for fatigue wear through
the life of the vehicle.
For certified aircraft it’s my understanding that there’s always an example of the type somewhere in a wiffle tree being fatigued to braking point,
hopefully a long time before any flying examples have the same failure.
On the car side of things all the volume manufacturers physically fatigue test all of their vehicles to the design life of the vehicle (~90,000 miles
in most cases these days). And parts still fail during these tests even with all of the engineering, design and computing power available to them.
Obviously no real production car today is riveted together out of ally so fatigue is not confined to that type of structure.
The link has some good pictures of wiffle trees:
http://www.dsto.defence.gov.au/publications/4219/DSTO-TR-1773.pdf
|
|
Dick Bear
|
posted on 19/12/06 at 12:09 AM |
|
|
Doug,
At the risk of being blind sided again by a message from one participant on this forum who is obviously less than enamored with my efforts and felt it
necessary to accuse me of being stubborn, ignorant, unaware, a liar, careless, having a death wish, an endangerment to others, an opportunist,
arrogant, and dangerous within the context of a single private email, I will continue my thoughts along the lines of making a true monocoque. Perhaps
throughout a lifetime I’ve been guilty of most of these but surely I can’t have all those character flaws at once this moment so I’ve pretty much
dismissed his rudely written opinion. Fact is, my wife and kids think I’m kind and, for the most part, responsible so I’m not sure where he is coming
from.
Thanks for the information and link to the Australian structure fatigue test program. Very interesting reading… Wouldn’t it be great to have such a
facility available to us to test each of our designs? Unfortunately we don’t and therefore, as with most state-of-the-art information until the
relevant findings trickle down from the top, we who occupy the lower echelon are forced to advance our knowledge and augment our design and
construction techniques using products and methods after they are developed by individuals and manufacturers occupying positions in the information
chain above us.
There is nothing new about this situation. It has always been that way in art and science. Philosophically I believe we should shun any thoughts and
pressure by others to limit exploration or to accept our ‘last to know’ position as an excuse not to attempt new methods. Using the skills and
knowledge we should press onward. Hopefully, our successes will out number our failures!
You have accepted this challenge as you methodically use your ability in 3D CAD (a skill I wish I possessed) to draw and design what you envision to
be the best solution possible in your build. Capitalizing on each of your abilities while anticipating and creating situations that need to be solved
you will, I’m confident, arrive at solutions that others would not even attempted. Most, if not all, of your solutions will be positive and those
that are found lacking in the final analysis can be addressed further, once more information is gathered. Individuals who limit themselves to or feel
bound by formulas, charts and opinions of those who came before simply disciples. They are forever relegated to achieving only that which has already
been achieved. Rather than originals, they are copiers regardless of attempts to disguise themselves as something more.
GROUND EFFECTS: I agree with you and your aerospace associates that achieving any advantage from ground effects on a road car might be minimal.
Certainly it is impossible to attain the same level achieved by teams at the height of its use in F-1. The fact is no one should want to attain that
level of achievement even if they could for all the same reason that those design practices were ruled illegal by F-1. However, I feel that somewhere
short of the extremes practiced by F-1 teams there is a level at which ground effects can be beneficial and achieved safely resulting in better
handling and cornering of a road car.
I submit that somewhere between dangerous and void, there is an acceptable level of achievement. Helping to hold the nose of a car down and increase
stability simply by attaching a vertically fastened front air dam beneath the nose has been proven effective and is accepted as safe so much so that
that feature is present on nearly every road car manufactured today. The fact that a full seal of air cannot be achieved on a road car is a good
thing because it eliminates the possibility of carrying any design to a dangerous level.
We should, I feel, explore ways in which we can create specific areas of negative pressure beneath the car to enhance stability and increase the
vehicles’ cornering ability. We will have taken a huge step forward once we’re able to increase both stability simply by the effectively using the
constant (usually disruptive) dynamics of air rushing between the car and the roadway.
Doug, your suggestion that I plan for regular inspection on the monocoque if I go down that avenue, is well taken. Because we are all tinkerers at
heart we should include in our tinkering the inspections of all components in the vehicles we design and build. You are right.
Well, this ended up being a longer post than I had envisioned when I started so I will stop for now.
PS. Has anyone heard the results from the metal clad balsa wood experiments? I’d like to see what was discovered.
Dick Bear
www.marketpointproductions.com
|
|
Doug68
|
posted on 19/12/06 at 05:24 AM |
|
|
Hi Dick,
A very thoughtful post.
Because a thing has not been done before is to me very good reason to go and do it, at the very least you’ll find out why nobody else did it!
For my own design I am very focused on getting as stiff a frame as I can come up with and suspension that hopefully will give me good mechanical grip,
weight or lack of it is not a top priority for me.
I’m sure some people on this forum won’t like what I’ve come up with it as it’ll be thought of as too heavy and too complex.
But those are my personal goals, so what they think is up to them.
On the CAD side I don’t think it’s hard to learn and looking at your post you’ve obviously got technical drawing skills and can think in terms of 3D
so I doubt it’d be too much of a problem for you to understand. Thankfully for me when I started learning Solid Edge this year my initial design was
horrible so it wasn’t too much heart ache to start again when I realized I’d done it all wrong from a CAD point of view.
I’m nearly at the point to start fabricating the main frame, my aim to date has been to address the major structural issues in the model before I make
a mistake for real, I’m taking this approach as I’ve stuffed up other projects in the past for lack of planning.
|
|
Syd Bridge
|
posted on 19/12/06 at 11:03 AM |
|
|
There may be some confusion with 'ground effects' and 'undercar aerodynamics'. Two completely different things.
Ground effects relies on a low pressure area being set up under the car, by stopping air getting under and thus creating a partial vacuum.
Undercar aero concedes that it is impossible to seal the underside, so sets out to create a big inverted aero section underneath, to act as a foil to
produce 'lift' downwards. This needs all sorts of splitters, gates, and dams to guide airflow and keep the flow organised.
Cheers,
Syd. 
|
|
kb58
|
posted on 19/12/06 at 02:10 PM |
|
|
quote: Originally posted by Doug68
Because a thing has not been done before is to me very good reason to go and do it, at the very least you’ll find out why nobody else did it!
However, this thread involves creating an aluminum monocoque , which has been done before. The limitations are very well known, specifically
metal fatigue. There's no shame in reading and learning what happened to those who did try something new. The British airliner, the Comet,
killed many people because of metal fatigue, which wasn't well understood at the time. It is now, so why ignore the lessons?
While building a car isn't the same as a plane, the metal fatigue issue certainly is, even more so, due to the increased vibration and pounding
it takes. Having a suspension mount become unstuck, is as life threatening to the driver as to those around him.
I'm very impressed by those here who can calculate the stresses, and therefore the life, of an aluminum monocoque. I have no idea how it's
done, but if I set out to build one, I'd certainly do my research. But building one, without doing your homework, and thinking,
"It'll be fine", is far worse than what happened with the Comet. Those engineers didn't know what would happen - we do. We
have the advantage of hindsight - why pretend it doesn't exist? It's irresponsible to endanger other people's lives by not
researching the topic; not implementing what's already known and understood.
Imagine having to choose the size of tubing, for fabricating A-arms. What's the sensable way to pick the right size? Ask others what they use,
calculate the force, and use a Strength of Columns table in a Material Science textbook.
Or, do you pick, say, 1/2" diameter, because no one else does it, and to be different. There may be a very good reason why it isn't
done; researching to find out why is the right thing to do. Why not use the collective wisdom of those who have gone before us? It's all there
in the books.
[Edited on 12/19/06 by kb58]
Mid-engine Locost - http://www.midlana.com
And the book - http://www.lulu.com/shop/kurt-bilinski/midlana/paperback/product-21330662.html
Kimini - a tube-frame, carbon shell, Honda Prelude VTEC mid-engine Mini: http://www.kimini.com
And its book -
http://www.lulu.com/shop/kurt-bilinski/kimini-how-to-design-and-build-a-mid-engine-sports-car-from-scratch/paperback/product-4858803.html
|
|
Dick Bear
|
posted on 19/12/06 at 05:22 PM |
|
|
Very interesting but of questionable value:
"However, this thread involves creating an aluminum monocoque, which has been done before."
…And I might add… done very successfully starting with the Can-Am’s and hundreds of racers and production vehicles since then.
"The limitations are very well known, specifically metal fatigue. There's no shame in reading and learning what happened to those who did
try something new."
....If you believe that the Comet’s airframe construction was something new you have a lot of research to do. The something new that is associated
with the Comet program was the fact that it was the first jet passenger plane. Certainly not that it was the first monocoque type airframe.
"The British airliner, the Comet, killed many people because of metal fatigue, which wasn't well understood at the time. It is now, so why
ignore the lessons?"
...My reading of the Comet disaster (early 1950’s) is somewhat different than yours. I conclude from my reading that metal fatigue was the issue but
rather than draw the generalized conclusion that all such construction is doomed to failure, I find that it was fatigue of a specific area of the
plane (the square corners the engineers designed for the plane’s windows). If you read further about the planes extended life, rounding the corners
corrected the problem. That’s the lesson to be learned from the Comet rather than what you conclude and inappropriately assign to all monocoque
design. I suggest that you re-read the articles regarding the Comet!
"While building a car isn't the same as a plane,"
....Well you get one point right but lose everything with your next questionable conclusions.
"the metal fatigue issue certainly is, even more so, due to the increased vibration and pounding it takes."
....I take it you’ve never witnessed or viewed video of a naval aircraft landing on aircraft carrier. The violent and nearly instant transfer of
weight from the wings in flight to the landing gear is far greater than the relatively slow weight transfers taking place in a vehicle frame.
"Having a suspension mount become unstuck is as life threatening to the driver as to those around him."
....No one is talking about ‘sticking’ something to anything? I prefer the phrase, ‘securely attach’ with universally accepted methods such as welds
and bolts.
"I'm impressed at those here who can calculate the stresses, and therefore the life, in an aluminum monocoque."
....Calculating the stresses doesn’t necessarily result in the ability to predict the life of anything. I would assume the engineers had calculated
the stresses factors on the Comet but their error in window design resulted in a shortened lifespan for at least two of their planes.
"I have no idea how it's done, but if I set out to build one, I'd certainly do my research. But building one, with no research,
thinking, "It'll be fine", is far worse than what happened with the Comet. Those engineers didn't know what would happen - we
do. We have the advantage of hindsight - why pretend it doesn't exist?"
....I don’t think anyone is contemplating building a monocoque without research. Certainly not without thought and no one here seems to take the
attitude that “it’ll be fine”. And once again, the only hindsight advantage anyone can legitimately draw from the Comet tragedy you present is the
understanding that sharp, square corners of cutouts are not appropriate.
Quite frankly gt58, your prediction of certain doom is based upon a less-than-careful reading of two plane crashes that happened nearly 50-years ago.
You seem bent on comparing apples to oranges and are guilty of making broad generalized statements that are neither substantiated nor defamed by your
one case study. You are ignoring the fact that monocoque design has been successfully for years both in the air and on the ground.
And finally, your less then professional assumption that anyone contemplating such a project universally lacks the ability to conduct research, is
unable to think, is ignorant of history or is guilty of ignoring facts speaks more to the delusions of grandeur you have for yourself than it does to
any weaknesses that may exist in those you are attempting to convince or impress.
Cheers,
Dick Bear
www.marketpointproductions.com
|
|