MikeR
|
posted on 22/11/23 at 01:18 PM |
|
|
Rough guide to machining cost
I'm looking at converting my weber DGV into fuel injection (a bit like retroject) but for a lot less cost.
I've 3d printed one of the parts that replaces part aux venturi with a mounting for an injector. The part i've 3d printed fits perfectly.
I'd like to now get it made in metal. Before I dig out the welder and swear lots I wondered about a rough cost for someone else making it.
Its 44mm long, 16mm high, and 8mm wide except for a circular section in the middle thats 18mm 0d and 14mm id. So potentially needs to come from a
piece of metal 44x18x16.
Link below to a picture of the part i'm replacing. The replacement is the same outside shape but the hole size is bigger and i don't need
anything making inside the hole. This also has nice radiused edges, i'd probably want that but iteration 1 is currently just square for
testing.
https://www.webcon.co.uk/products/5723-dgvdgav-3236-dgv-auxilliary-venturi-35/
If i supply the cad file what am i looking at it costing, £10 or £100 or ????
|
|
|
MikeR
|
posted on 22/11/23 at 01:30 PM |
|
|
if i can work the damned photo side of this site with a modern phone i'll photograph what i've made - currently i can't!
|
|
gremlin1234
|
posted on 22/11/23 at 01:38 PM |
|
|
what metal do you want to use? ali, brass, ...
|
|
MikeR
|
posted on 22/11/23 at 01:48 PM |
|
|
Ali or Brass or plutonium - anything that's reasonable cost and relatively strong.
Picture of what I mean
 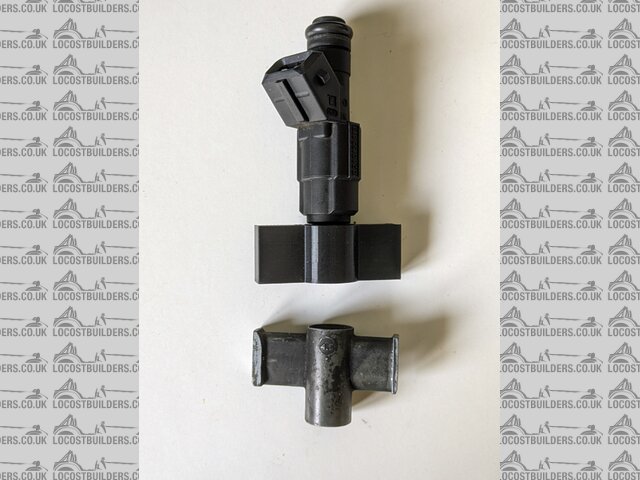 dgvinjector
|
|
nick205
|
posted on 22/11/23 at 02:45 PM |
|
|
I'd say to have that machined as a single part would be fairly complex and pricey.
Probably cheaper to have it made as 3 parts and work out how to accurately join them into a single part.
When I built an MK Indy I fitted a 2.0 Pinto with Weber DGV and it ran fine. I didn't get into fuel injection. Have to ask though, are there not
easier and more cost effective ways of changing to fuel injection than your planned method?
|
|
tegwin
|
posted on 22/11/23 at 04:22 PM |
|
|
The price of DMLS (metal 3d printing) has come down a lot over the last few years. If you have an STL file I would send it to a few of the
companies that offer that service and see what they would charge?! Id guess somewhere around £100 per part... Parity with having something like that
machined probably!
------------------------------------------------------------------------------------------------------------------------
Would the last person who leaves the country please switch off the lights and close the door!
www.verticalhorizonsmedia.tv
|
|
MikeR
|
posted on 22/11/23 at 04:41 PM |
|
|
Right, guess I'm welding it then. I can get the steel for a few quid.
I'm expecting the total cost to be in the 20 to 30 quid range. (Ok it will be more but I'll have steel left over & I've already got
lots of other parts. The 20 to 30 is the cost for the steel used).
Why am I doing it, cause I want to & cause I'm involved in speeduino so I think I should & it's another excuse not to finish the car
for a year
If I was confident I could reliably mount the injector fuel rail without it having to be compressed into into the inlet side then I'd use the
plastic part but printed in nylon.
|
|
Schrodinger
|
posted on 22/11/23 at 09:51 PM |
|
|
why not mount the injector/s in the manifold ?
this is what I did when converting twin webers to injection.
Keith
Aviemore
|
|
MikeR
|
posted on 22/11/23 at 10:21 PM |
|
|
I've had a plan to do this, but making my own manifold out of steel. Made the manifold after lots and lots of heat scratching, mounted it and
realised the carbs didn't fit under the bonnet. Got annoyed and cut it up.
Saw a scrap Weber dgv and thought "wait a minute, this might be quite easy".
(Would rather have the DCOEs - but can't face making the manifold again and can't weld Ali.)
Will post a picture later when the 3d printer had finished how easy this conversion will be.
|
|
Schrodinger
|
posted on 22/11/23 at 11:10 PM |
|
|
this was my setup
 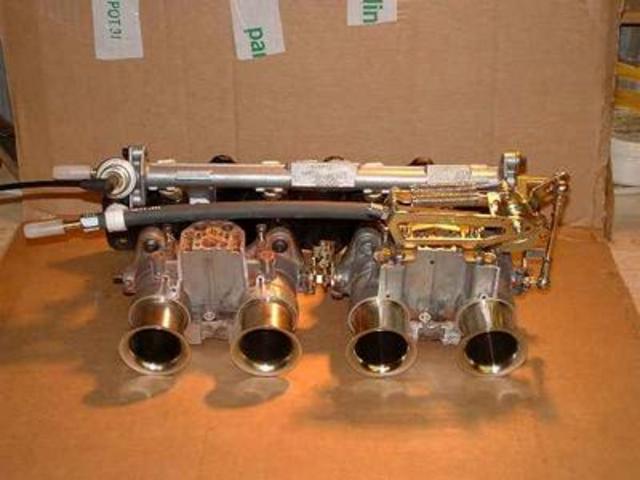 Dressed manifold
Just a thought but won't the injector fire onto the butterfly?
If so I think you will get some erratic running especially when the engine is cold at low revs.
You ideally want to be injecting onto the back on the valves or into the manifold.
Keith
Aviemore
|
|
MikeR
|
posted on 22/11/23 at 11:47 PM |
|
|
You've done almost exactly what I was thinking of - however i was going to mount the injectors under the manifold. This would allow them to fire
straight into the head towards the valve (its a crossflow so the inlet isn't shaped for injection) and it allowed me to potentially hide what I
was doing a bit to retain the DCOE look.
Regarding the DGV approach - yep, it would be firing towards the butterfly. This is exactly what retroject does & what the DGV does when sucking
fuel for 'normal' running. Its also how the single point injectors or yesteryear worked (although they had lower pressure and better
atomisation). Not perfect but as its going to the manifold first before the pistons sucking the fuel/air mixture i don't think it will be too
bad.
I'll have some 3d printed pictures of the bits I need to make by the morning so i'll share a picture of two..... you never know by the
weekend I may have reverted back to the DCOE's (as thats what i really want).
|
|
coyoteboy
|
posted on 23/11/23 at 09:22 AM |
|
|
quote: Originally posted by tegwin
The price of DMLS (metal 3d printing) has come down a lot over the last few years. If you have an STL file I would send it to a few of the
companies that offer that service and see what they would charge?! Id guess somewhere around £100 per part... Parity with having something like that
machined probably!
Last time I checked (2 years ago) a part 35x6x6mm was priced at 2500.
The price of metal for subtractive machining is almost irrelevant unless you're asking for unobtanium, the machining costs are far more important
and for that alu will make your life easier - it's faster and easier to machine.
Negatively machined I'd expect a part like that to be a few hundred as a one-off, and I wouldn't expect many places to want to do it -
one-offs are expensive - there's a lot of set-up, fixturing and programming time to absorb into the cost.
If you can CAD it yourself, you could fire it into shapeways or similar to get a metal printed price (but be aware that with metal printing you need
post-machining!) and into somewhere like fractory or similar to get online one-off prices for negative machining. These places usually come out 30%
higher than if you went to a jobbing shop round the corner and fought with them for 30 minutes to get the price down.
Paying someone to make you a thing is an expensive luxury
[Edited on 23/11/2023 by coyoteboy]
|
|
Theshed
|
posted on 23/11/23 at 10:36 AM |
|
|
Much of the cost of CNC is the initial set up and fixturing. I do not think that would be very hard to machine manually.
If I have understood the picture it is a 2d shape. If that is right then it is a simple case of drilling or boring (depending on tolerance) the centre
hole. Using a rotary table to cut the outside profile. The only difficult bit is the radius between the arms and the centre circle (outside). There is
no radius in your plastic part. Using an endmill would result in a radius. You could always file it down but I do not see it getting the way of the
air stream as the injector us biggish. If you weld it you will have created a natural radius in the same spot.
It would be even quicker to have a square in the centre. Four flats and one hole. You could file the outside to your hearts content..... Or use a
radius cutter come to think of it.
If you are not in any great rush (and I see your build has taken as long as mine....). I will make these for you. Probably take me a few weeks to find
the time. I would need a drawing and an idea on tolerance for the arms and centre hole.
An alternative is to get them water jet cut. Some finishing would be required. This assumes that the 2d profile is as I have said above.
|
|
coyoteboy
|
posted on 23/11/23 at 11:29 AM |
|
|
That's an offer you can't refuse - most places outright refuse to manually machine things these days.
|
|
Dingz
|
posted on 23/11/23 at 12:56 PM |
|
|
Sorry be be a bore but what’s wrong with using a pinto injection manifold? Assuming it’s a pinto of course.
Phoned the local ramblers club today, but the bloke who answered just
went on and on.
|
|
MikeR
|
posted on 23/11/23 at 01:53 PM |
|
|
Unfortunately Its for a crossflow engine - otherwise i'd have used the pinto manifold in a heartbeat.
@TheShed - i'll pm you. The key points are the width of the arms & total size to fit in the slot in the weber carb, along with the size of
the big hole for the injector to fit into (~13.8mm / 35/64 / .440 to .450)
|
|
Theshed
|
posted on 23/11/23 at 07:14 PM |
|
|
OK - make sure you allow sufficient clearance for the injector. An exact fit will mean pressing the injector in and it will not come out easily. The o
rings need some space to work as well.
If you can accurately measure the choke you took out I can follow those dimensions. I can make these in 7075T6 Aluminium which is plenty strong.
I will keep an eye out for a PM
|
|
Dingz
|
posted on 23/11/23 at 08:06 PM |
|
|
Sorry for assuming it is a pinto, have you considered the single port injection units that were fitted to some of the Metros with K series engines?
probably other makers to.
Phoned the local ramblers club today, but the bloke who answered just
went on and on.
|
|
paulf
|
posted on 26/11/23 at 10:39 PM |
|
|
Could it be 3 d printed in a higher grade plastic rather than metal ?,the injector is plastic after all.Other wise it could be fabricated from brass
and silver soldered or machined from ally relatively easily,i think it would even be possible to make from a bit of round bar with a hole drilled and
maybe reamed on a pillar drill to suit the injector and then hacksawed and filed to shape.
|
|
coyoteboy
|
posted on 27/11/23 at 11:09 AM |
|
|
quote: Originally posted by paulf
Could it be 3 d printed in a higher grade plastic rather than metal ?,the injector is plastic after all.Other wise it could be fabricated from brass
and silver soldered or machined from ally relatively easily,i think it would even be possible to make from a bit of round bar with a hole drilled and
maybe reamed on a pillar drill to suit the injector and then hacksawed and filed to shape.
I guess you could use PEEK, but personally I wouldn't trust a non-metal part downstream of the throttle, having had carbon manifolds crack and
basically go WOT with no control, I wouldn't advise that for the average member of the public - if you can prove the lack of porosity and do some
strength/fatigue checks, maybe. Of course everyone's risk strategy varies and it *is* possible to use PEEK in the engine bay, depending on the
right strength and stiffness in the design.
[Edited on 27/11/2023 by coyoteboy]
|
|