luke
|
posted on 15/4/09 at 10:03 PM |
|
|
teaching myself to weld and failing!
hey all,
Today i have spent the whole day trying to teach myself to weld and failing miserably!
kit - Im using a clarke 100EN MIG welder running 0.8mm wire and CO2 from a pub bottle. The welder is currently set to max and ive tried a variety of
wire speeds and gas pressures.
now im currently practising on a piece of steel about 2mm thick, nearest i could get to the chassis steel, and im just not getting any penetration at
all.
the welder runs max of 100A and according to the book will weld 3mm but from reading websites these thicknesses are aparently over rated and i should
expect 2mm, but i cant even get penetration on 2mm.
currently my welds look like piles of bird poo and are easily knocked off with a hammer.
an ex collegue says i should be running about 160A at least? am i underpowered or just doing something totally wrong?
cheers for any help at all
luke
|
|
|
blakep82
|
posted on 15/4/09 at 10:07 PM |
|
|
first things first, don't rush yourself. rome wasn't built in a day
it'll take more than a day to get it right
next, i don't know what you're doing wrong, but if you post some photos up, it'll be a lot easier for us to see what to suggest
[Edited on 15/4/09 by blakep82]
________________________
IVA manual link http://www.businesslink.gov.uk/bdotg/action/detail?type=RESOURCES&itemId=1081997083
don't write OT on a new thread title, you're creating the topic, everything you write is very much ON topic!
|
|
tegwin
|
posted on 15/4/09 at 10:08 PM |
|
|
You should be able to get your welds to stick pretty well with a 100A...... Not sure you would get FULL penetration... but they should stick non the
less...
Do you have your polarity the right way round for the earth clamp/weld tip?
you might want to slow the wire feed down quite a bit.... if you are running max power and you are pidgeno shitting.... could be your feed is to fast
of your earth is bad...
Put a location in your profile and someone might be able to help!!
------------------------------------------------------------------------------------------------------------------------
Would the last person who leaves the country please switch off the lights and close the door!
www.verticalhorizonsmedia.tv
|
|
UncleFista
|
posted on 15/4/09 at 10:11 PM |
|
|
Is the EN the one that's set up for gasless (although you can use gas) ?
If it is, you'll need to reverse the polarity on the torch for using gas, otherwise you'll get no penetration
With gas, the torch should be +, the earth clamp -
[Edited on 15/4/09 by UncleFista]
Tony Bond / UncleFista
Love is like a snowmobile, speeding across the frozen tundra.
Which suddenly flips, pinning you underneath.
At night the ice-weasels come...
|
|
handyandy
|
posted on 15/4/09 at 10:14 PM |
|
|
Hi Luke,
i,m not a trained welder but my advice is just keep at it, vary your power/wire speed/gas pressure & your speed of the weld(your movement rate),
not sure where you are located but i,ve just finished an 11 week course at my local tech college, it was great & free, 12 weeks ago i,d never even
seen a mig up close, with the power that your mig is it might be that you are rushing the weld, may i suggest slow down & when you reach the point
of blow thru you know thats the point you want to avoid, if that makes sense?
cheers
andy
|
|
luke
|
posted on 15/4/09 at 10:15 PM |
|
|
cheers for replies,
yer the EN can run gasless, i have it set up the right way and they have kindly put a huge picture on the front of the welder to demonstrate.
ill run outside now and take a pic for you to have a look at.
two ticks
|
|
RichardK
|
posted on 15/4/09 at 10:18 PM |
|
|
Make sure you grind off or file the protective black coating that steel sometimes has so you are welding nice shiny steel, make sure the earth clamp
is good, I welded a pair of mole grips onto the end of my earth cable to make sure, also make sure the the point that you're earthing to is
shiny if possible just to try a rule out stuff.
Turn your gas on so you just hear it hissing then up a tiny bit more as a rough guide.
Put the wire speed somewhere in between a quarter and half with everything on full power.
Don't move the nozzle too fast away from you but do work in a slow figure of eight movement working away from yourself, so get yourself comfy
first.
If you have a blow torch try putting some heat into the metal first may also help.
I'm am no where near a pro welder but these few things seem to work for me.
Cheers
Rich
Gallery updated 11/01/2011
|
|
luke
|
posted on 15/4/09 at 10:25 PM |
|
|
pic for you guys, sorry its a bit out of focus, camera didnt like the light of the flourescent.
|
|
austin man
|
posted on 15/4/09 at 10:27 PM |
|
|
try 6mm wire, and as previous post says clean up area grinder etc prior to welding you may also be moving the torch too fast. Persevere and all will
come naturally start off with lower settings and work your way up, wire speed wiil be a major factor. Someone once told me youve got it right when it
sounds like bacon sizling in a pan.
Life is like a bowl of fruit, funny how all the weird looking ones are left alone
|
|
luke
|
posted on 15/4/09 at 10:37 PM |
|
|
hmmm pic wont seem to work, wont let me put it in the gallery either, are JPEGs not supported?
mine doesnt sound like bacon, its too pulsey, like pop pop pop pop pop.
ive cleaned up both the working area and the clamp area with a grinder.
could it be the power is too high and its melting the wire before it gets the metal hot?
|
|
handyandy
|
posted on 15/4/09 at 10:41 PM |
|
|
what wire speed are you set at & what pressure is your gas output?
andy
|
|
luke
|
posted on 15/4/09 at 10:44 PM |
|
|
ive tried a variety of wire speeds from about 3 up to about 8 (out of 10)
as for gas, the gauge is before the valve on the regulator, the gauge shows about 800PSI IIRC and ive again tried the regulator at about 1/4 up to 3/4
open.
|
|
blakep82
|
posted on 15/4/09 at 10:46 PM |
|
|
quote: Originally posted by luke
hmmm pic wont seem to work, wont let me put it in the gallery either, are JPEGs not supported?
mine doesnt sound like bacon, its too pulsey, like pop pop pop pop pop.
ive cleaned up both the working area and the clamp area with a grinder.
could it be the power is too high and its melting the wire before it gets the metal hot?
hmm, by that it sounds like the wire speeds too slow?
jpg's are supported, but needs to be a unique file name (from every other file name on everyone elses archive, i learned this week )
________________________
IVA manual link http://www.businesslink.gov.uk/bdotg/action/detail?type=RESOURCES&itemId=1081997083
don't write OT on a new thread title, you're creating the topic, everything you write is very much ON topic!
|
|
luke
|
posted on 15/4/09 at 10:49 PM |
|
|
quote: Originally posted by blakep82
hmm, by that it sounds like the wire speeds too slow?
jpg's are supported, but needs to be a unique file name (from every other file name on everyone elses archive, i learned this week )
i thought that but its worse when the wire speed is high, its like it throws a load of wire out and melts too quick to me. but i dont know!
|
|
handyandy
|
posted on 15/4/09 at 10:52 PM |
|
|
ok, i,m using a Clarke 151en set to run on gas, i use wire speed 5 or 6 but gas pressure is quite low, when setting the gas a tip i got from welding
course at college was this....
the gas coming out of the torch should be like someone just gently blowing on your face, not a force ten hurricane,
try this.. set your wire speed in middle of available speed, your amps on full & gas set low & weld one spot, see how long it takes to burn
thru & then you have a reference point to work from, thats how they taught us at college to get the feel for the settings/torch, tho remember it
changes when you weld thicker metals.
andy
|
|
blakep82
|
posted on 15/4/09 at 10:56 PM |
|
|
i was welding a bit today with a clarke 151te, generally my wire speed is set at 5, it needs slight adjusting at different powers. mine has 6 power
settings, not sure about yours, is it 4?
i'd start at lowest power, and set the wire speed to 5 and see how you go. once you work out whats right for the lowest power, then work your
way up.
edit: or try what andy says above. that'll give you a feel for how quick to move the torch, but i think you'll need to get the right wire
speed first, in which case try mine
[Edited on 15/4/09 by blakep82]
________________________
IVA manual link http://www.businesslink.gov.uk/bdotg/action/detail?type=RESOURCES&itemId=1081997083
don't write OT on a new thread title, you're creating the topic, everything you write is very much ON topic!
|
|
handyandy
|
posted on 15/4/09 at 11:20 PM |
|
|
quote: Originally posted by blakep82
i was welding a bit today with a clarke 151te, generally my wire speed is set at 5, it needs slight adjusting at different powers. mine has 6 power
settings, not sure about yours, is it 4?
i'd start at lowest power, and set the wire speed to 5 and see how you go. once you work out whats right for the lowest power, then work your
way up.
edit: or try what andy says above. that'll give you a feel for how quick to move the torch, but i think you'll need to get the right wire
speed first, in which case try mine
[Edited on 15/4/09 by blakep82]
i agree with above, all i,m suggesting is to try and find a maximum burn thru point & work backwards from that, if that doesn,t work try what he
^^^^^ says & work upwards from the minimum 
andy
|
|
MikeR
|
posted on 15/4/09 at 11:23 PM |
|
|
The clarke 150 range are designed (in theory) to have the correct wire speed at setting 5. You then adjust as necessary.
(note this is a concept - but it will get you started if the 100 is the same setup.
Defo clean the steel.
Defo make sure the earth is on clean steel.
Weld next to the edge of the steel - with it being next to the edge there is less metal to take the heat away and it should all go glowing hot and
make you feel better.
The sound you want is a combination of sizzling bacon and ripping silk / cotton.
start off moving the gun at between .5 and 1cm a second (i've guessed the speed before someone tells me its wrong)
Keep the torch about tip about 1cm from the metal and at a 60 degree angle - pulling the torch (ie 60 degrees from where the weld is going to be 120
degrees from where the weld is).
errm.... errr.... its late, i've got a cold and can't sleep - have a go with that lot & sorry for the mistakes 
|
|
luke
|
posted on 15/4/09 at 11:31 PM |
|
|
thanks for all the tips, im going to give another crack at it tomorrow.
think the old saying of bad workman always blames his tools is present here 
|
|
blakep82
|
posted on 15/4/09 at 11:35 PM |
|
|
tell you what, get a photo emailed to me, i'll put it on here for you
blakeperkins82@hotmail.com
________________________
IVA manual link http://www.businesslink.gov.uk/bdotg/action/detail?type=RESOURCES&itemId=1081997083
don't write OT on a new thread title, you're creating the topic, everything you write is very much ON topic!
|
|
craig1410
|
posted on 15/4/09 at 11:38 PM |
|
|
Have you set enough tension on the feed roller? It should be set so that if you point the torch at the concrete floor and press the trigger you should
feel a reasonable "kick" from the wire feeding through but it should still slip without causing a birds nest between feed roller and
torch. Also, is your wire clean and not rusted up like most welding wire tends to be when not used for a few months. If it's rusted up then
remove wire from the spool until you reach clean wire.
Also, check that your electrode is not set too far inside the gas cup. I usually have mine about 5mm inside the gas cup so that I can weld with around
10 - 15 mm of wire between torch and weld pool.
HTH,
Craig.
|
|
luke
|
posted on 16/4/09 at 12:00 AM |
|
|
blake,
email sent, thank you!
|
|
blakep82
|
posted on 16/4/09 at 12:09 AM |
|
|
ok, here we go guys,
 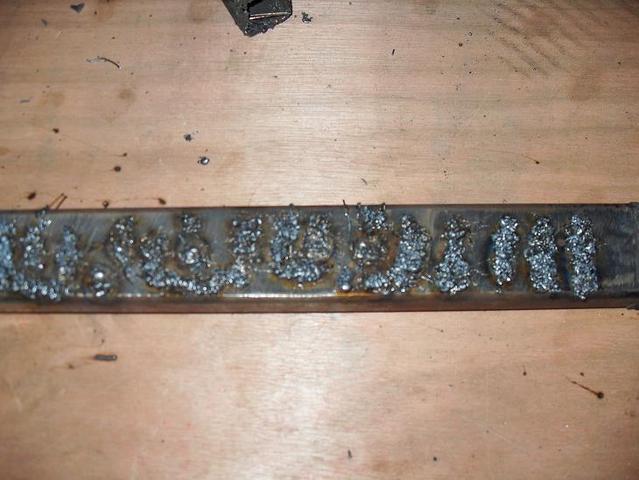 luke
looks like not enough gas actually, because that can have a sort of crystaline effect, but i'm not sure about this now
________________________
IVA manual link http://www.businesslink.gov.uk/bdotg/action/detail?type=RESOURCES&itemId=1081997083
don't write OT on a new thread title, you're creating the topic, everything you write is very much ON topic!
|
|
craig1410
|
posted on 16/4/09 at 12:12 AM |
|
|
WTF is going on there - never seen anything like that before!
Are you sure it is CO2 in your cylinder? Having said that I would expect better results than that with no gas!
Is the welder broken? I have a Sealey 100A turbo and it can easily weld 2mm mild steel.
|
|
handyandy
|
posted on 16/4/09 at 12:22 AM |
|
|
i might be totally wrong but to me it looks like both wire speed & gas is set too high, looking at the bits of wire left beside the metal.
just my opinion.
andy
|
|