matt_gsxr
|
posted on 8/7/10 at 08:31 PM |
|
|
Anti-roll bar quick how to please
So, I have an ARB on the front of my Phoenix and it seems a bit stiff, I have run the calcs and it is too stiff. So I need to make up another.
My question is how?
I have inboard suspension and all the mountings, so I know the dimensions. It is going to be 400mm long, and needs 5inch arms at 90deg to the bar.
Material wise 1/2 CDS with a 3.25mm wall thickness seems to make sense.
But, how do I fit the arms to the bar?
Weld them? Use a longer bar and bend it with a bit of heat.
I could make it from 1/2inch solid if that would help.
Thanks,
Matt
|
|
|
smart51
|
posted on 8/7/10 at 09:13 PM |
|
|
Could you add extensions to the arms of the current bar? The extra leverage would make it seem softer.
Have a look at the caterham website. They sell ARBs in a variety of thicknesses. One of them might fit.
|
|
hicost
|
posted on 8/7/10 at 09:32 PM |
|
|
Drop Links
Use Drop Links
"I cant do that without accidentally grabbing hold of the work of the divine potter"

|
|
loggyboy
|
posted on 8/7/10 at 09:33 PM |
|
|
Machine/grind/file an area of the bar to make narrower and flex more?
|
|
Steve Hignett
|
posted on 8/7/10 at 09:48 PM |
|
|
ARB shizzle...
http://www.merlinmotorsport.co.uk/SUSPENSION-Associated-Suspension-Parts-Roll-Bar/c31_32_33/index.html
|
|
matt_gsxr
|
posted on 8/7/10 at 09:48 PM |
|
|
All the Caterham ones are too long, as I am running my drop links from the top of the rockers. Actually I am not sure about the front CSR ones, these
are shorter, but still look a bit too long. So I need a bar of around 400mm long.
If I make the arms longer, you are correct it would have the same effect. Unfortunately the arms are already long. As they get longer the front-back
forces on the rocker get nasty. So I am at the limit of the arm length.
I already have drop-links.
Good thought on grinding down the existing bar. The only problem with that route is that it is a bit irreversible! It is something that I am
considering though.
I have read some stuff on this, and generally welding the ARB is considered a bad idea. I might get some 1/2inch rod and put some bends in it
(cold).
Here is an interesting link from a US locost site:
Linky
Matt
|
|
CNHSS1
|
posted on 9/7/10 at 09:52 AM |
|
|
The Allan Stanniforthe books, Race & rally Car Data Source book, and competition car suspension, show the calculations from mike Pilbeam and David
Gould respectively on designing ARBs.
Luckily you already have one, so using the calcs it'll be relatively simple to find the diameter and/or length required to give the results you
need.
As for making one up its not rocket science, CDS tube can be used (bit lighter than solid bar) and can be mandrel bent cold. if you cant get CDS tube
in the sizes required, use hydraulic tube (essentially the same stuff) availaible from most commercial hose suppliers (used to repair plant machines
and JCBs).
Ive used the merlin style plastci clamps and they work great although MUCH cheaper from the hydraulic suppliers
"Racing is life, everything else, before or after, is just waiting"---Steve McQueen
|
|
CNHSS1
|
posted on 9/7/10 at 12:43 PM |
|
|
ooops, engaged brain and re-read your first post properly
welding arms to the tube is easily done and ive had a few done like that with no ill effects, although theory dictates its not ideal. Normally use 4mm
flat plate for the 'arms' and drill a few holes either side of the normal mounting position to give some adjustment. with 5" arms,
possibly only one hole either side of the ideal would give quite a variance in stiffness.
alternatively have the tube mandrel bent as i prev mentioned, and then teh Merlin red ally sliders will give you finer adjustments sliding along the
5" lever arms
HTH
CNH
"Racing is life, everything else, before or after, is just waiting"---Steve McQueen
|
|
matt_gsxr
|
posted on 10/7/10 at 09:47 PM |
|
|
I might remanufacture a bar/tube using the bending method.
Excellent advice there mr CNH.
In the mean time I decided that the easiest thing was to take my 16mm bar and "trim" it down a bit.
I started with this,
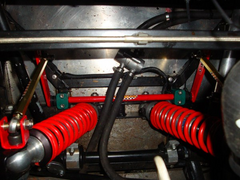  ARB1
and [after 2hours of grinding, filing, sanding] ended with this;
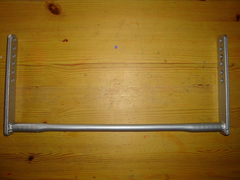  doctored_ARB
16mm diameter, down to a bit less than 13mm. Which reduces the stiffness by a factor of 2 or so.
For what its worth, making a bar in this way might be a good method (especially if you had a lathe) as the weld are on a thick section (limited flex,
and hence chance of failure at the welds which won't flex so well) but you can tune the bar to the required stiffness.
Thanks for all the help on this
Matt
[Edited on 10/7/10 by matt_gsxr]
|
|