MikeR
|
posted on 21/9/10 at 04:13 PM |
|
|
how to measure / cut correct length angled tube?
This has bugged me for years and as i've got to cut some roll bar stays soon i thought i'd find out how to do it properly.
I've got a tube that I need to cut that isn't a straight join between two other tubes and the joints on both are different angles. I
struggle to figure out the right length to cut the tube. I usually (hopefully) over cut and spend ages filing it back. Often realising that i've
got one end right and the other wrong, using this as a template for the next bit of steel.
If its straight, its easy, you measure the distance between and cut. If its an inline angle - ie the side diagonals on the chassis its quite easy as
you measure either the smaller or larger length, the angle, mark up the steel with the smaller or larger length, then the angle and cut.
How do i measure the distance when the steel is at a compound angle & also how do you measure up & then mark up the tube when you're
doing round tube?
|
|
|
Fred W B
|
posted on 21/9/10 at 04:39 PM |
|
|
Their are probably more efficient ways bit you could try:
Cut and tack a square cut tube into place that just touches the closest points of the joints you are trying to connect to.
Wrap a 4" wide piece of cardbord into a tube around the steel tube, and fit that up on one end, by cutting it with it scissors to get the right
profile while sliding it into the joint. Once happy, make reference marks on the steel and carbourd template piece.
Repeat for other end.
Now transfer the profiles and register marks to a new, longer piece of steel tube and cut that to fit. Use the seam in the tube as a refrence to
oritate the two end markings
If you see what I mean?
Cheers
Fred W B
You can do it quickly. You can do it cheap. You can do it right. – Pick any two.
|
|
MikeR
|
posted on 21/9/10 at 06:00 PM |
|
|
If i didn't get a better idea i was thinking of doing something similar with wood.
Take a 2" thick square bit of wood, about 6" long. Run a 2" holesaw through the middle to get two bits of 3" wood with a
perfect connection to the roll bar tube.
I'd then stick this to the roll bar tube using a wrap of gaffer tape. Connect the two bits together with another bit of wood to the edge of the
steel. I can then measure the angle and distance. I'll use tube mitre to then tape onto the tubes to do the cut. Thing is, this isn't very
practical for lots of angles, uses lots of wood and I'm hoping their is a better, more reliable, quicker way of doing it.
|
|
pewe
|
posted on 21/9/10 at 06:12 PM |
|
|
There was an article in PPC this month about making a roll-cage which mentioned a down-loadable programme from t'interweb which would give you a
template for a given size of tubing.
Didn't say where it was but might be worth a google to find it.
HTH.
Cheers, Pewe
Looks like this one tube mitre cutting prog
I can't open it as it's Microsoft based and I'm running Linux - note to self - get techie to open it!
[Edited on 21/9/10 by pewe]
[Edited on 21/9/10 by pewe]
|
|
MikeR
|
posted on 21/9/10 at 07:58 PM |
|
|
interesting - been hunting this months ppc for a while..... must try harder.
|
|
StrikerChris
|
posted on 21/9/10 at 08:13 PM |
|
|
I've only ever used 2 methods.the work approach,"its not a f'in piano" technique,get it somewhere near and fill the gaps with
weld,and the one I used on my rollcage,the
"cut it too long,spend hours filing,hide the cockup in the quickly growing 'usefully scrap' mountain,and start again"
technique.
|
|
clairetoo
|
posted on 21/9/10 at 10:00 PM |
|
|
When I was building dragbike frames I used to hold a bit of tube as near to in place as possible , mark the angle on each end in line with the center
of each tube it was going to fit to , then cut those lines with a hacksaw .
Next - with an angry grinder fitted with a coarse flap disc simply shape both ends till they fit
The trick (for me....) was to creep up on the shape , and keep checking both ends after every touch with the grinder .
Its cuz I is blond , innit
Claire xx
Will weld for food......
|
|
907
|
posted on 22/9/10 at 07:46 AM |
|
|
Flexable Templates
Hi Mike,
I would start with two pipes that are too long.
Carefully shape one end with a flap disc (like Claire) until it fits.
Shape the other end of the other pipe to the other angle/shape.
Wrap paper around the shaped end and tap the shaped edge with a small hammer to cut the paper to the shape.
Repeat on the other shaped end.
You should now have two templates that you can slide on the pipe to cut and shape the other ends.
Offer them up and slide and turn them till they look right, maybe a tad long to start with. You can always take a little more off.
For compound curves I use a layer of masking tape, sticky side out, and a layer on top, sticky side in.
A cut with a knife and it can be taken off and stuck on the next one.
I use a spring loaded dot punch to mark the cut line as a row of dots are easy to grind to.
Hope this is of some help.
Cheers,
Paul G
 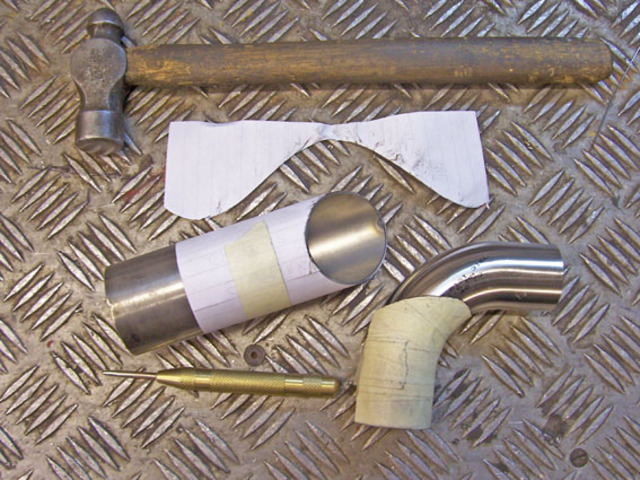 pipe templates
1.5" to 2" tee from the template above.
 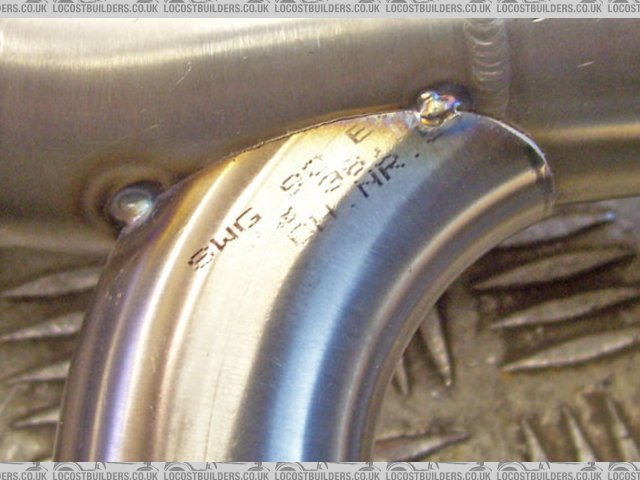 1.5 to 2 tee
[Edited on 22/9/10 by 907]
|
|
Badger_McLetcher
|
posted on 22/9/10 at 04:41 PM |
|
|
I used the same techniques as above- I'm afraid it just seems to be one of those time consuming things if you want to get it done well!
If disfunction is a function, then I must be some kind of genius.
|
|