AdrianH
|
posted on 3/6/11 at 09:14 PM |
|
|
Anyone got a magic way of mounting flywheel in lathe?
I would like to remove the slight pit marks from the front face of a 1.8 CVH flywheel, needs approx 5 thou taking off the two faces.
Lathe chuck is not big enough to hold the flywheel around the edge, my inside jaws will not go small enough to go in the central hole,
so wonder if anyone has another technique or a flange that would mount the flywheel on then stick in the chuck?
On another note for the same end. Lost one of the clutch dowels so turned one down from an old valve stem.
Must be more careful and stop loosing bits.
Adrian
Why do I have to make the tools to finish the job? More time then money.
|
|
|
HowardB
|
posted on 3/6/11 at 09:20 PM |
|
|
stub shaft that fits the hole, or, faceplate?
:-)
Howard
Fisher Fury was 2000 Zetec - now a 1600 (it Lives again and goes zoom)
|
|
clairetoo
|
posted on 3/6/11 at 09:24 PM |
|
|
For skimming flywheels I use a dummy shaft , four tapped holes to hold the flywheel , and just skim the mounting face each time I use it .
For any major machining , I am lucky to have a lathe with a big enough four jaw chuck to hold just about any car flywheel
Its cuz I is blond , innit
Claire xx
Will weld for food......
|
|
austin man
|
posted on 3/6/11 at 09:27 PM |
|
|
loctitw glue if it can stick a man to a ceiling a flywheel shouldnt be a problem lol
Life is like a bowl of fruit, funny how all the weird looking ones are left alone
|
|
David Jenkins
|
posted on 3/6/11 at 09:55 PM |
|
|
quote: Originally posted by austin man
loctitw glue if it can stick a man to a ceiling a flywheel shouldnt be a problem lol
Oooh - that's just too scary a concept...
[Edited on 4/6/11 by David Jenkins]
|
|
steve m
|
posted on 3/6/11 at 10:09 PM |
|
|
What about leaving it on the engine and start it up on the garage floor, and take the tool to the offending bit?
|
|
madteg
|
posted on 3/6/11 at 10:31 PM |
|
|
Could allways cut the end of an old crank.
|
|
AdrianH
|
posted on 3/6/11 at 11:18 PM |
|
|
Think I will go for the dummy shaft idea and not the Loctite. I'll see what is left in my bar stock tomorrow.
Adrian
Why do I have to make the tools to finish the job? More time then money.
|
|
omega 24 v6
|
posted on 4/6/11 at 11:24 AM |
|
|
Clairetoo's idea would be the prefferred method by most engineers given this set of circumstances.
If it looks wrong it probably is wrong.
|
|
coozer
|
posted on 4/6/11 at 12:19 PM |
|
|
Must be a MASSIVE lathe for the swing.....
1972 V8 Jago
1980 Z750
|
|
clairetoo
|
posted on 4/6/11 at 01:50 PM |
|
|
quote: Originally posted by coozer
Must be a MASSIVE lathe for the swing.....
Well , I machined part of the MDF tool for a molding I was doing at work on it - it needed to be tapered and round , so this was the easy option . To
give an idea of scale , the part is 14 inches in diameter
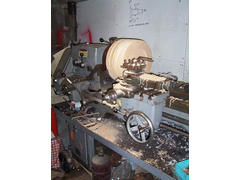  Lathe.....
Its cuz I is blond , innit
Claire xx
Will weld for food......
|
|
AdrianH
|
posted on 4/6/11 at 02:42 PM |
|
|
Job done, must take more care where I put the holes in the mandrel but done it, just waiting for ARP bolts to arrive next week and one job down on the
Silvertop.
Just finished some injector bosses for the ongoing project.
I am having fun with the lathe today, just got to clean up!
Adrian
[Edited on 4-6-11 by AdrianH]
Why do I have to make the tools to finish the job? More time then money.
|
|
flak monkey
|
posted on 4/6/11 at 05:09 PM |
|
|
I do....
Not telling how I did it though 
Duratec flywheel and clutch with enough room for the saddle to clear the ring gear too.
Sera
http://www.motosera.com
|
|
Badger_McLetcher
|
posted on 7/6/11 at 09:36 PM |
|
|
Magnets! Giant magnets!
If disfunction is a function, then I must be some kind of genius.
|
|