robocog
|
posted on 3/12/11 at 07:28 PM |
|
|
end mills
I have a lathe and have started a project
I think I'm going to need to do some milling...which I have never tried before
I know jack about milling tooling so need some pointers before I go blowing money on stuff that will not be suitable
I think there are going to be 2 types of cut I will need to make (and I will try to describe them)
type 1 - where I will be "slotting" some holes that are open at the end (drilled hole elongated)
type 2 - where I will be slotting....but the end of the bit will be into material....bottomed out...flycutting stylee so I have a nice square cut
Would/could the same sytle "tooling" be used for both operations?
Material is quite soft aluminium alloy at the mo but I /may/ change to brass if my prototype works (although see no reason why it wont be suitable in
alloy)
Size wise I need 5mm dia for the slotting tool that will be used for type 1
and 2mm dia for the type 2 (and some of the type1 cuts)
I'm not removing any great depth of material (2mm deep for the flycutting/bottoming operation) so I will be keeing the tooling as physically
short as poss
will try and post pics as re-reading my explaination even has me confused!
Regards
Rob
|
|
|
tegwin
|
posted on 3/12/11 at 07:44 PM |
|
|
I have been having a play with milling cutters today on my lathe and drill press...
The weak link is the morse tapers that hold the chucks in...
I managed to cut a blind 16mm diamter hole 4mm deep into some brass in my drill press, but it didnt like it! Reallllly want a proper mill!
------------------------------------------------------------------------------------------------------------------------
Would the last person who leaves the country please switch off the lights and close the door!
www.verticalhorizonsmedia.tv
|
|
Talon Motorsport
|
posted on 3/12/11 at 07:49 PM |
|
|
End mills need to go into pre drilled holes before you can move them sideways unless you start outside of the material. You will need a 'slot
drill' if drilling into then slotting, besides I'm not sure you can get end mills that small but I stand to be corrected.
|
|
Talon Motorsport
|
posted on 3/12/11 at 07:53 PM |
|
|
quote: Originally posted by tegwin
I have been having a play with milling cutters today on my lathe and drill press...
The weak link is the morse tapers that hold the chucks in...
I managed to cut a blind 16mm diamter hole 4mm deep into some brass in my drill press, but it didnt like it! Reallllly want a proper mill!
I would not advise that you do that with an endmill on a pillar drill too often if you value all your soft fleshy bits!
|
|
robocog
|
posted on 3/12/11 at 07:54 PM |
|
|
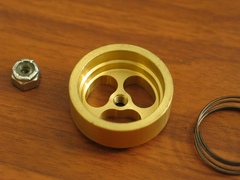  Description
This is what I mean by type 1 ...the three holes in the base, drilled then slotted (5mm, all the way through the material)
and the "castellations" is the type 2 cutting (2mm wide and 2mm deep)
 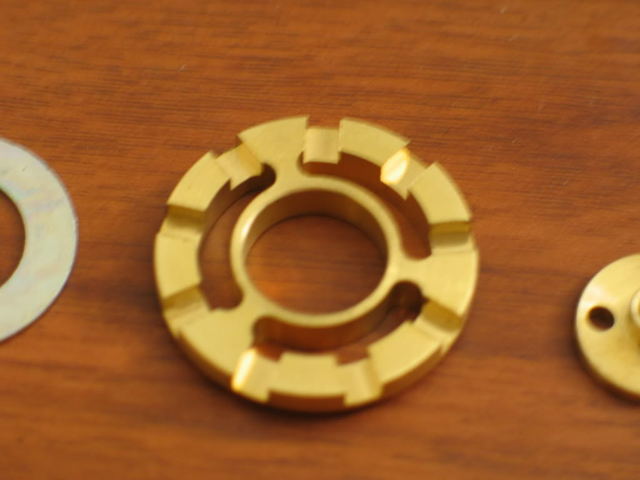 Description
I guess I'm going to have to get inventive on how to arrange it so I can rotate the work for the slotting around the central point (or buy a
rotary vice) and use the chuck to hold the milling tooling
Any pointers appreciated
looking at the following tooling for the job
5mm dia (type 1 )
4 flute End Mill TiN coated - 5mm diameter | eBay
Says suitable for slot milling so I guess that should be OK
the 2mm dia
2 flute End Mill HSS - 2mm diameter | eBay
Is what I describe as type 2 cutting called "pocket cutting"?
(and is that tool suitable for what I want from it?)
Regards
Rob
|
|
robocog
|
posted on 3/12/11 at 07:58 PM |
|
|
OK so I would need to drill pilot holes for each of the slots first ...then slot away
Didn't know that - and has possibly saved me some frustration /broken tooling and another delay waiting for replacements ...so thanks for
that
(glad I asked now)
any advantage / dissavantage as to how many flutes the tooling should have??
Regards
Rob
[Edited on 3/12/11 by robocog]
[Edited on 3/12/11 by robocog]
|
|
Talon Motorsport
|
posted on 3/12/11 at 08:07 PM |
|
|
Unless you spend a fair bit on the rotary vice ie more than £150 you will struggle to get any thing rotates smoothly. You really need a rotary table
to give you a fine enough turning ratio to make a smooth cut. Have you considered posting this on a hobby/live steam engineering forum? I know it will
be a lot safer than using a pillar drill and a vice.
|
|
owelly
|
posted on 3/12/11 at 08:22 PM |
|
|
I've used milling bits in a drill chuck in a pillar drill and as said, it's not ideal! The sideways motion on the bit/chuck causes the
tapers to loosen then the whole lot falls out and munches it's way through your workpiece or whatever else it grabs hold of. In my case, it
destroyed the ally diving lamp I was modifying before making a dash for my sleeve.
I've also (mis-)used my lathe for milling operations either by mounting the milling bit in the chuck and clamping the workpiece to the tool
post, and vice-versa.
For those pieces in the piccies, I agree that to make an accurate job of things, you'll need an indexing table and a proper milling head.
http://www.ppcmag.co.uk
|
|
robocog
|
posted on 3/12/11 at 08:29 PM |
|
|
I have some sketches of "ideas" of how to hold and rotate the work (and a poor mans dividing device so I know when to stop rotating)
I will be using my lathe as I know its well out of the scope for my pillar drill (but it is good at self centering over a punch mark and drilling
ovals!)
Kind of up for the challenge including building the work holding and rotating device so farming it out is not yet being considered
Sure if I make a pigs ear of it I will either be looking at prices for someone else to do it for me (only if it can be done for pocket money prices)
or abandon the project completely
At the moment I need to build 4 of these "thingys" which are not mission critical to my life...just a bit of tinkering fun/learning
curve
I have started the first 2 and at the stage of the making holes and slotting
I have a bit more alloy bar left so a screw up at this stage will be no biggy as I reckon I can reproduce what I have done so far in 1/2 the time its
taken so far (and maybe a tad more accurately)
I have made a lot of swarf so far as the only bar I had was more than double the diameter required...shed is overflowing with the stuff...LOL
Regards
Rob
|
|
robocog
|
posted on 3/12/11 at 08:32 PM |
|
|
How did the milling operations go using the lathe?
I guess it has to be better than a pillar drill?
I'm only going to be taking very light and slow cuts (and theres minimal material to be removed)
Interested to hear how it went
Regards
Rob
|
|
trikerneil
|
posted on 3/12/11 at 08:47 PM |
|
|
Hi
You can get end mill holders to use in a lathe and make a couple of split bushes to hold your slot drills.
LINKY
Remove the chuck and fit the holder with a drawbar. This is a much more rigid setup than holding the cutter in the lathe's chuck.
With a bit of imagination you can do loads of milling in a lathe
Milling tube bender dies.
Boring out a set of yokes.
HTH
Neil
ACE Cafe - Just say No.
|
|
fazerruss
|
posted on 3/12/11 at 10:11 PM |
|
|
For a cheap supply of end mill ect you can use ordinary hss drill bits with the end ground flat rather than pointed. It works very well believe it or
not. A friend of mine who is into hobby engineering uses them when the drill bits are too short from years of sharpening.
"if assholes could fly this place would be an airport"
|
|
trextr7monkey
|
posted on 3/12/11 at 11:44 PM |
|
|
I just ordered a couple of 3mm carbide tipped end mills for a small CNC machine yesterday , they will be in the Trend catalogue somewhere, roundabout
£16 each
atb
Mike
Edited to ad: We have found Chronos to be an excellent supplier of milling accessories- rotary tables, collets etc so worth having a look at their
stuff foir inspiration too
[Edited on 4/12/11 by trextr7monkey]
http://www.flickr.com/photos/14016102@N00/ (cut and paste this dodgey link)
Our most recent pics are here:
http://s129.photobucket.com/albums/p211/trextr7monkey/
|
|
robocog
|
posted on 4/12/11 at 12:02 AM |
|
|
Should I be looking at going up in sizes in steps? (like pilot drilling and slotting before using the final size) rather than taking the 5mm off in 1
go for the bottom half - or should it be OK in one step?
(its not as if I'm taking off shed loads of material)
ditto for the 2mm slots and end milling for the top piece with castellations...
Lathe is an old M type and I /think/ it may have a morse taper under the chucks threaded nose...but will more than likely be MT1
Tailstock is MT1 and is just about usable..though It could well be the tailstocks chuck taper that is not quite right rather than the tailstock
itself
Will take a look next time chuck comes off as I'm now doubting myself and it may be just a straight bore
I know the drawbar (assuming I have a taper of some sort behnd there) would need to be a skinny affair as the through bore is annoyingly narrow
Regards
Rob
|
|
trikerneil
|
posted on 4/12/11 at 06:12 AM |
|
|
I have found that the headstock is usually one size larger morse taper than the tailstock.
Neil
ACE Cafe - Just say No.
|
|
MikeRJ
|
posted on 4/12/11 at 10:56 AM |
|
|
Robocog, have you checked out the Debrix emulators? They are pretty cheap.
|
|
robocog
|
posted on 4/12/11 at 01:19 PM |
|
|
quote: Originally posted by MikeRJ
Robocog, have you checked out the Debrix emulators? They are pretty cheap.
Yep but too chuffing fat for my little tiddler :-(
Max width I could fit would be 29mm (as suggested by "the big company" who retail them) possibly could get 30mm at a push without it
binding ...and looking at the photo's of the copy's I could possibly turn them down...but walls would be left paper thin which would worry
me
Have tried and tried to get to the bottom of who /actually/ makes them, or even a distributer but got nowhere
(I'm pretty sure its somewhere far east and are pretty tied up contract wise with the "big company"
Emailed Debrix and a couple of other Harley places but they were not willing to divulge much and stated that and the bigger one which is just as
sensibly priced were the only sizes /they/ could get them in
so far made the cups and the caps
Have managed to get the upper (compression) springs on order- still looking for the lower rebound one
Have some suitable washers here and the bolts - so just need to make the holes and sort out the lower springs and give em a whirl
Pretty confident I can make something that will be better than what I currently have (after a few tweaks)
It's the dive under breaking I really want to minimise - without having it almost hydrolock on our fantasic british roads
Regards
Rob
[Edited on 4/12/11 by robocog]
|
|
Confused but excited.
|
posted on 4/12/11 at 03:40 PM |
|
|
quote: Originally posted by owelly
I've used milling bits in a drill chuck in a pillar drill and as said, it's not ideal! The sideways motion on the bit/chuck causes the
tapers to loosen then the whole lot falls out and munches it's way through your workpiece or whatever else it grabs hold of. In my case, it
destroyed the ally diving lamp I was modifying before making a dash for my sleeve.
I've also (mis-)used my lathe for milling operations either by mounting the milling bit in the chuck and clamping the workpiece to the tool
post, and vice-versa.
For those pieces in the piccies, I agree that to make an accurate job of things, you'll need an indexing table and a proper milling head.
Clamped to the tool-post? Naughty. There's no reason that you can't clamp work to the cross-slide though.
Tell them about the bent treacle edges!
|
|
trikerneil
|
posted on 4/12/11 at 03:56 PM |
|
|
I have a worm and wheel setup if you fancy a go at making a simple dividing head.
Neil
ACE Cafe - Just say No.
|
|
robocog
|
posted on 4/12/11 at 04:07 PM |
|
|
Seems to have an MT1 (in poor condition) behind the chuck
Both my dead centers and tailstock chuck do go in...and kind of locate but badly
I may try and clean it up with a bottle brush with thinners/wd to see if its just crud causing the nasty fit
Certainly would be better off using the 3 jaw self centering chuck as it stands
the runout using the morse taper as it stands is as good as using a hand drill on a rocky boat
Noted to use the cross slide rather than toolpost
Regards
Rob
|
|
robocog
|
posted on 4/12/11 at 04:57 PM |
|
|
Thanks for the kind offer Niel
Will shout up when it gets to that bit if my first idea fails dismally
Regards
Rob
|
|
trikerneil
|
posted on 4/12/11 at 05:41 PM |
|
|
OK Rob
Neil
ACE Cafe - Just say No.
|
|