andrew-theasby
|
posted on 5/9/12 at 04:19 PM |
|
|
homemade sheet metal rollers, suggestions please
I have acquired some steel tubing which im hoping will be suitable for making myself some sheet metal rollers suitable for stainless and alloy sheet
but i have a fewquestions which im hoping other peoples experience can answer.
-Firstly i have 3 tubes around 1m long, 50mm OD with 10-11mm walls (the ID is slightly hexagonal). Will this be rigid enough for its length?
-Secondly what is the best design for the roller positions? I was thinking with picture 2 that only one would need to be adjustable, but maybe the
width would be better to be adjustable too? Anybody have any plans that require minimal fabrication?
-And third, the bearings, what do they normally use? Ball bearings, roller bearings or brass bushes? Suitable sizes?
Oh and one last one, will it be best with a shaft welded in to the end of the tube for the bearing, or a bearing inserted in the tube with a full
length shaft, bearing in mind that will need 3x 1m 25mm round bar.
Any suggestions would be appreciated please, keeping to the locostbuilders theme with cheap bearings, minimal machining re using scrap etc.
I wont be able to get back on line tonight as im at work btw so will check for replies tomorrow. Thanks

|
|
|
Ivan
|
posted on 5/9/12 at 04:51 PM |
|
|
This was done with bushes
http://www.mytractorforum.com/showthread.php?t=122172
|
|
myke pocock
|
posted on 5/9/12 at 06:37 PM |
|
|
Only comment I would make is that the tube that you have needs to be extremely rigid. I have seen solid rollers on a pucka rolling machine of the same
length you are thinking of actually flexing slightly. I think that is why the attached link showing a home made roller has such massive rollers.
|
|
907
|
posted on 5/9/12 at 08:32 PM |
|
|
Hi Andrew,
Your "pic1" diagram shows pre-set rolls, sometimes called initial pinch rolls.
The upside of this type of rolls is that they start to roll from the edge of the sheet.
Your red line depicting the sheet is the wrong way round btw.
The sheet would be inserted from the right and the curve would be to the left.
The two left hand rollers would have a gear on the end so that they would drive each other,
and rotate in oposite directions.
The downside of this design is that for a given diameter and length they will roll thiner sheet.
"Pic2" are pyramid rolls.
In your diagram the two bottom rollers need to be much closer together (the ? dim)
and need to be linked by either a chain or have gears with an idler gear between so that they
both rotate the same way.
The upside is that, for a given diameter and length, they will roll thicker sheet.
The downside is that the edge of the sheet has to be pre-set in some other way.
With all rolls the rollers flex, and this results in the ends of the cylinder that you are rolling
being a tighter rad than the centre, i.e. the ends meet and the middle doesn't.
For this reason I don't advise using pipe to make the rollers.
I have three sets of slip rolls. A set of Edwards pre-set that are 4ft x 3"dia rated at 16g mild steel, (1mm s/s)
a set of 1020mm x 3" pyramid rolls that I cut down from 5ft, now rated at 4mm m/s,
and a set of home made 500mm x 40mm pyramid rated at 16g that I use to roll small stuff.
Hope this helps.
Cheers,
Paul G
Edit to add pics of my 500mm set.
The rollers are made from LAS
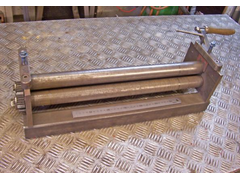 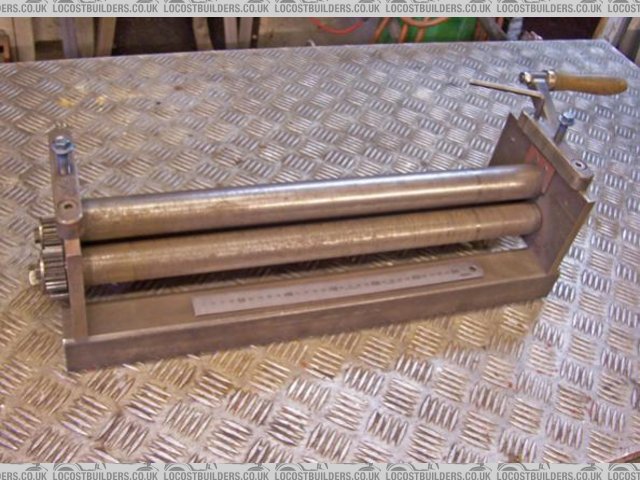 home made rolls
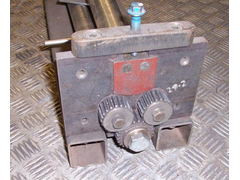 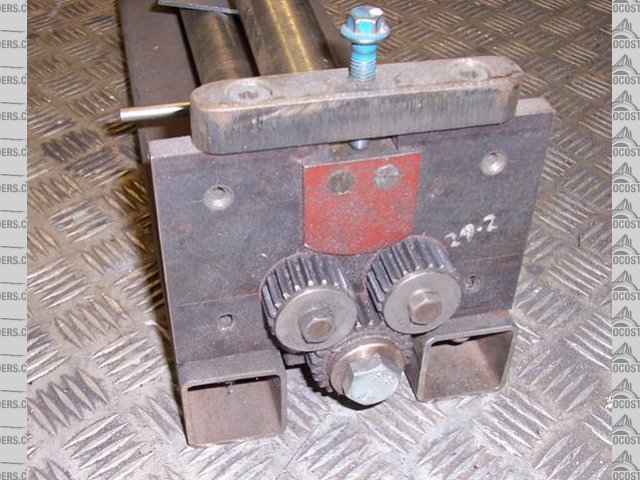 Description
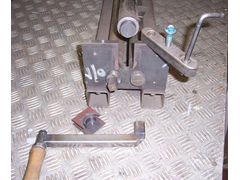 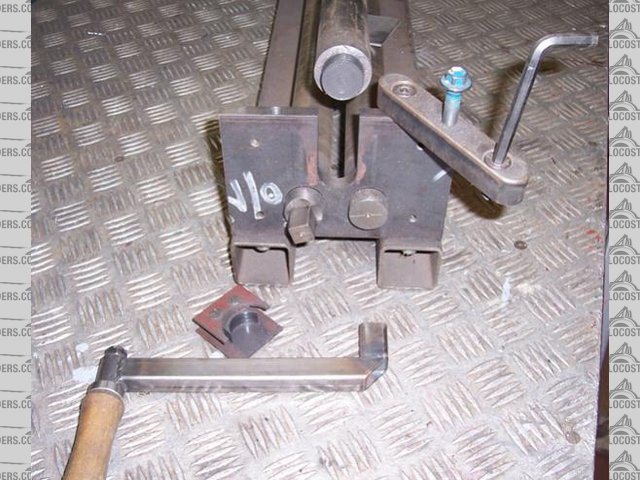 Description
[Edited on 6/9/12 by 907]
|
|
hillbillyracer
|
posted on 5/9/12 at 10:55 PM |
|
|
I've got a set of old pinch rolls about 1m wide, the rollers are about 75mm or so & solid steel. The old fabrication engineer I bought them
from reckoned it was possible to roll 3mm sheet at full width but you'd have to work bloody hard (they're manual operation!). I've
never taken them that far & dont know that they'll do it but have rolled 2mm sheet around 600mm wide & would say it'd be giving
you a fair big workout as he said!
I've seen them flex a touch rolling 3mm mabye 300mm wide.
If you just want to roll thin sheet it'll likely be ok but based on how mine works you'd have to be carefull how thick you went with the
material.
As said the pinch rolls work right from the edge of the sheet (but only one edge, you need to turn the work round to do both edges)
I like your 2nd bearing idea better, you could turn the inside of the tube out just enough to make it true so you'd lose less strength, make it
an interference fit & the weld would have less work to do.
I cant remember what mine uses for bearing, I think it's just plain bushes.
|
|
andrew-theasby
|
posted on 6/9/12 at 01:10 PM |
|
|
Ok thanks for the comments, you've got me wondering now whether it would be worth cutting them down to 2ft to increase the rigidity or whether
3ft with limited thickness would be more versatile? I think it will be mainly alloy I use them for, but still nice to have the option for steel.
|
|
907
|
posted on 6/9/12 at 10:09 PM |
|
|
The pic shows my 4ft Edwards preset rolls.
The rollers are 3" solid hardened steel and even these flex a bit when rolling the full width.
Cheers,
Paul G
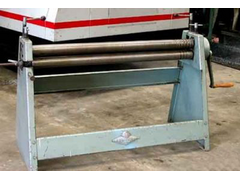 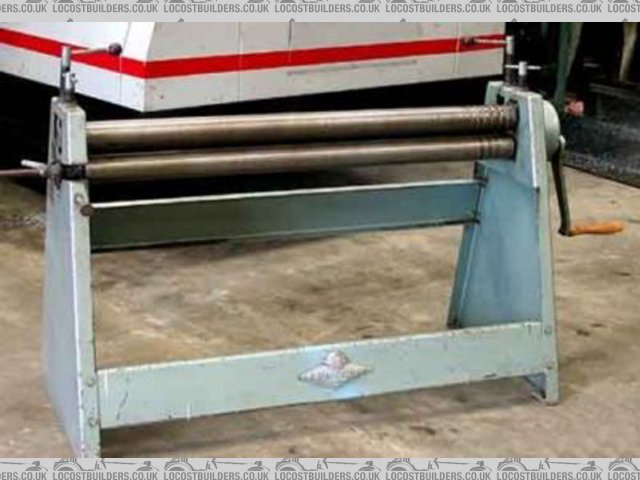 4ft pre set rolls
|
|
andrew-theasby
|
posted on 7/9/12 at 01:40 AM |
|
|
Can i ask where you sourced the gears from, im not having much luck finding any at the moment? And is it not necessary to use bearings, i notice your
small set just sit in holes in the end plates. Are bushes more suitable than bearings, as i have ball bearings readily available.
|
|
907
|
posted on 7/9/12 at 07:06 AM |
|
|
quote: Originally posted by andrew-theasby
Can i ask where you sourced the gears from, im not having much luck finding any at the moment? And is it not necessary to use bearings, i notice your
small set just sit in holes in the end plates. Are bushes more suitable than bearings, as i have ball bearings readily available.
Hi Andrew,
The gears are change wheels from my Harrison lathe. Search the bay for "change gear".
Yes, mine have no bearings, just keep them well greased. The best way would be to use bronze bushes.
You will notice that there are 4 tapped (m6) holes in the ends. These were to bolt the 2 ends together
while I machined the holes. The two bottom rollers must be parallel or it will roll more at one end than the other.
I'm not trying to tell you how to make yours, just trying to pass on my experience with various rolls I've used
and owned so I will just say that I would have reservations about using pipe as the rollers.
Hope this helps.
Cheers,
Paul G
|
|
MikeRJ
|
posted on 7/9/12 at 09:15 AM |
|
|
quote: Originally posted by 907
I'm not trying to tell you how to make yours, just trying to pass on my experience with various rolls I've used
and owned so I will just say that I would have reservations about using pipe as the rollers.
Bsides the stiffness, I wonder if pipe would be concentirc enough? I suspect you wouldn't need much eccentricity to stop rollers working
properly.
|
|
907
|
posted on 7/9/12 at 09:28 AM |
|
|
quote: Originally posted by MikeRJ
quote: Originally posted by 907
I'm not trying to tell you how to make yours, just trying to pass on my experience with various rolls I've used
and owned so I will just say that I would have reservations about using pipe as the rollers.
Bsides the stiffness, I wonder if pipe would be concentirc enough? I suspect you wouldn't need much eccentricity to stop rollers working
properly.
I don't know how old you are Mike but do you remember the old 3d bit? I do.
( Not sure if that's thruppenny or threepenny bit.)
Cheers,
Paul G
|
|