907
|
posted on 17/7/06 at 09:10 PM |
|
|
Getting the hang of Ally Welding
My rad expansion pot.
It's not finished yet, but it is the first thing I've ever made (welded) from sheet ally.
I think I'll hide it under the nose cone.
Paul G
 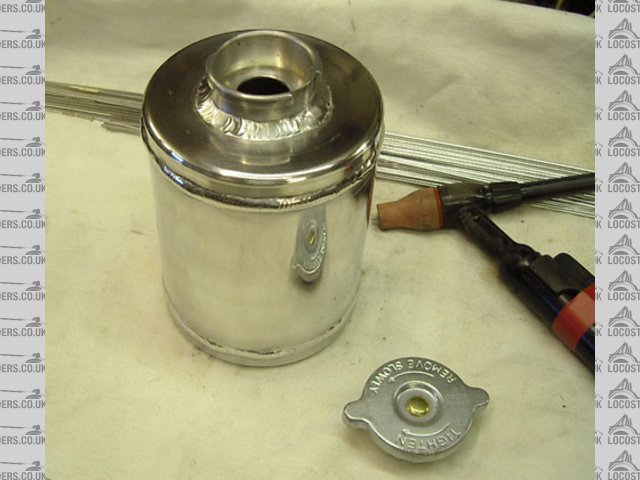 Rescued attachment water-tank-002s.jpg
|
|
|
NigeEss
|
posted on 17/7/06 at 09:36 PM |
|
|
I think it looks fine 
|
|
mark chandler
|
posted on 17/7/06 at 09:39 PM |
|
|
Looks great to me, I,d cut a hole so people can admire it 
Where did you get the filler, its one of my next tasks.
Regards Mark
|
|
tim windmill
|
posted on 17/7/06 at 09:55 PM |
|
|
are you gonna start knocking oil catch tanks out? looks spot on to me.
|
|
tim windmill
|
posted on 17/7/06 at 09:55 PM |
|
|
are you gonna start knocking oil catch tanks out? looks spot on to me.
|
|
tim windmill
|
posted on 17/7/06 at 09:56 PM |
|
|
looked soooooooh good posted twice
|
|
907
|
posted on 17/7/06 at 10:23 PM |
|
|
O Mark. Mark, Mark, Mark.
O ye of little faith.
   
It's a piece of sheet, 152 mm long.
G clamp over an edge of plate, with a plate on top, 3 mm protruding, and knock it down with a nylon mallet.
Remove clamps and knock to 180 deg safe edge.
Same again with 4.5 sticking out.
You end up with a double bend, three thicknesses of material, 5.5 deep.
Roll round a piece of bar or pipe, weld seam, and file out two slots.
Cut tube to length, to fit rad cap, in this case 19 mm, and you have a filler neck.
Scratch building to the extreme me thinks.
atb
Paul G
|
|
dl_peabody
|
posted on 17/7/06 at 11:38 PM |
|
|
Nice Job...What type of welder are you using? MIG, TIG, Gas?
Do you mind giving out the model mumber?
|
|
zetec7
|
posted on 18/7/06 at 03:13 AM |
|
|
If I'd made a piece that nice, I'd put it on display in my living room!! Lovely piece of kit, be proud of it!! Wish I knew how to
TIG  
|
|
DaveFJ
|
posted on 18/7/06 at 07:55 AM |
|
|
Good to see your 'practicing' in anticipation of my request for swirl pot
looking good, yet again your hand skills put us mere mortals to shame!
Dave
"In Support of Help the Heroes" - Always
|
|
John Bonnett
|
posted on 18/7/06 at 06:54 PM |
|
|
Hi Paul
I know in some circles it is considered bad form to ask a cook for a recipe and I hope you will not be offended if I could ask you for a bit more
information on how you made the very nice header tank. I am particularly interested in how you rolled the aluminium neck for the radiator cap. A
superb piece of work that will really enhance your car.
Best wishes
John
|
|
rusty nuts
|
posted on 18/7/06 at 07:04 PM |
|
|
Nice one Paul but you will have to polish it before it gets anywhere near your car . Can I ask how the gas welding is going?
|
|
Trev D
|
posted on 18/7/06 at 09:02 PM |
|
|
Hi Paul good to see some nice work going on cant wait to see your nose cone. regards Trev.
|
|
907
|
posted on 18/7/06 at 10:51 PM |
|
|
Hi All,
Thanks for the replies.
In answer to your questions......
dl-peabody, used a miller dynasty tig welder.
Tim & Dave, What's a catch tank or a swirl pot?
Is it like a keep net or a guzunder?
John, see post 7, back a page.
Rusty, I think an inlet pipe would be handy. I just knew I'd forget something,
and NO, you may not ask about my gas welding.
Trev, the nose is an August job, (and Sept, Oct, Nov, Dec, etc, etc)
atb
Paul G
|
|
johnjulie
|
posted on 19/7/06 at 10:11 PM |
|
|
HIDE IT UNDER THE BONNET!!!!!!!!!!!
Come on 907, you know it's a good job.
Just fishing for praise eh?
Nice one!
Cheers John
|
|
907
|
posted on 20/7/06 at 12:21 AM |
|
|
quote: Originally posted by johnjulie
HIDE IT UNDER THE BONNET!!!!!!!!!!!
Come on 907, you know it's a good job.
Just fishing for praise eh?
Nice one!
Cheers John
It's a shame you think that John.
Not my intention at all.
I bought my ac tig so I could "have a go" at something I'd never done before, i.e. aluminium sheet metal work.
I've put in many hours just getting the hang of what to me is a new skill.
It's far from perfect, had to grind off the first attempt as I failed to clean it properly.
Welding over the top came out a lot better, a lesson learned I think.
I hope a post like this shows that with a will to learn, and a bit of time, a reasonable level of success can be achieved.
When I started my build my level of knowledge was limited to fitting a recon in a tin top, and welding a few patches to pass an MOT.
I build vessels at work, but that's worlds apart from all the aspects of car building.
I thought a roll centre was somewhere you bought sandwiches.
I hope my posts spur people on to have a go at making stuff, not just sign a cheque and wait for the postie, not that there's anything wrong
with that anyway.
So go on, have a go. It may not turn out top notch, but you can say....
I made that
Paul G
|
|
John Bonnett
|
posted on 20/7/06 at 07:48 AM |
|
|
I bought my ac tig so I could "have a go" at something I'd never done before, i.e. aluminium sheet metal work.
Hi Paul
Ignoring the above, it really is a fine piece of work and anyone who can TIG weld aluminium will agree. A T weld (to me anyway) is the hardest weld to
achieve. It is so easy to burn through the edge of the vertical.
The maxim I try to apply is, if it is the best that I can do, irrespective of what others can do, it is ok. If it is not my best, then I bite the
bullet and remake it. I can then look at the job and know that it was the best I could do. There, thought for the day!!
John
|
|
johnjulie
|
posted on 25/7/06 at 07:23 AM |
|
|
Only joking Paul, I've just completed two years of the ABC welding courses, so I know how difficult it is to weld ally. It looks bloody good to
me!
When I said 'NICE ONE', I meant it!
Keep up the good work!!!
Cheers John
[Edited on 25/7/06 by johnjulie]
JFDI
"Just F*****G Do It"
|
|
907
|
posted on 25/7/06 at 06:15 PM |
|
|
quote: Originally posted by johnjulie
Only joking Paul, I've just completed two years of the ABC welding courses, so I know how difficult it is to weld ally. It looks bloody good to
me!
When I said 'NICE ONE', I meant it!
Keep up the good work!!!
Cheers John
[Edited on 25/7/06 by johnjulie]
Look at the welds carefully.
I welded it from 2 o/clock to 12 o/clock, then turned it, 2 to 12 again etc.
The tank is round, but the weld is 50p shape.
Paul G
|
|
John Bonnett
|
posted on 25/7/06 at 06:31 PM |
|
|
Paul what gauge aluminium did you use?
John
|
|
907
|
posted on 25/7/06 at 09:36 PM |
|
|
It's 16g John.
The ends I "pushed" round a former in the lathe.
It's been mounted now, , on a cross brace just in front of the thermostat housing.
Although it's far from perfect, it will be nice to look back and say, "that was the first bit of ally I made".
atb
Paul G
|
|