Jonte
|
posted on 4/3/04 at 05:05 PM |
|
|
Fastening the rollbar ?
How do you mount the rollbar for best result? Have a look at my attached pic.
Do you use rivnuts, rivets or something else
  Rescued attachment rollbar.GIF
Click it
|
|
|
Staple balls
|
posted on 4/3/04 at 05:30 PM |
|
|
i'm gonna go for option 1, using m12 bolts/nuts (and crush tubes in the chassis tubes if i can)
rivnuts really arn't up to the job. remember the rollbar is there to save your life, not pull out when you need it
|
|
James
|
posted on 4/3/04 at 05:56 PM |
|
|
Jonte,
Can you even get the blts in these positions?
I wish I good. Mine were going to have to be all over the place. Now I've modified my shock brackt (so the shock actually fits!) and
there's only room for 3 bolts!
Guess I'm gonna *have* to brace the bugger!
Cheers,
James
|
|
MikeR
|
posted on 4/3/04 at 06:09 PM |
|
|
I think most people end up using three bolts and if you mean brace as in rearward bars - don't think about it, just do it. Roll bars (by all
accounts) aren't worth much without them.
|
|
James
|
posted on 4/3/04 at 06:14 PM |
|
|
Problem with the bracing is it completely messes up having a simple boot lid with an easily accessable boot!
|
|
Staple balls
|
posted on 4/3/04 at 06:15 PM |
|
|
i'd go for a more
 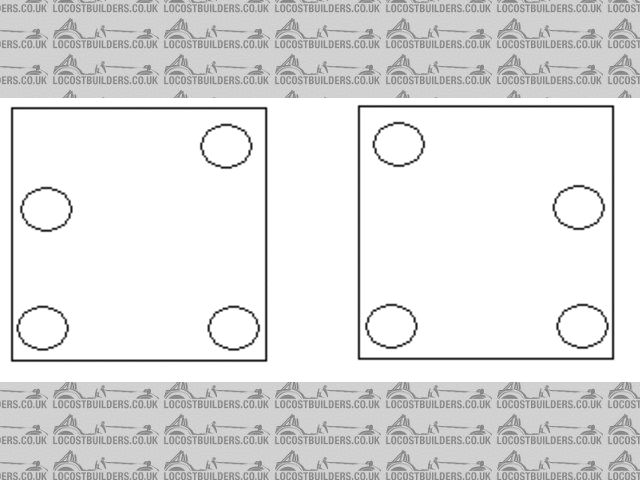 Description
style bolting pattern btw, should allow more space, away from home now, so can't check
|
|
Jasper
|
posted on 4/3/04 at 07:49 PM |
|
|
Used 4 x M12 and fully welded bracing bars to the bottom corners of the chassis.
Agree there as useful as a chocolate teapot if they're not braced.
|
|
Peteff
|
posted on 4/3/04 at 08:16 PM |
|
|
Weld it on. You don't have a problem with the bolts then.
yours, Pete.
yours, Pete
I went into the RSPCA office the other day. It was so small you could hardly swing a cat in there.
|
|
Kitlooney1000
|
posted on 4/3/04 at 08:28 PM |
|
|
my roll bar, albeit too short for me, is made from 3mm 2 1/4 inch steel, bit heavy but thought it would be stronger.
|
|
craig1410
|
posted on 6/3/04 at 12:39 AM |
|
|
I agree with Peteff, just weld it on. In my opinion it should be a standard fitment to any Locost chassis anyway.
Cheers,
Craig.
|
|
Jonte
|
posted on 6/3/04 at 08:01 AM |
|
|
quote: Originally posted by craig1410
I agree with Peteff, just weld it on. In my opinion it should be a standard fitment to any Locost chassis anyway.
Cheers,
Craig.
That would be great if it wasn´t for that I´m gonna get the rollbar chromed.
Click it
|
|
Peteff
|
posted on 6/3/04 at 04:13 PM |
|
|
Moving the goalposts now eh ?
Can't you have it chromed so far down then weld it on and paint over the weld and where the chrome finishes. I don't know if this is
feasible but then again I don't like chromework so it won't affect me.
yours, Pete.
yours, Pete
I went into the RSPCA office the other day. It was so small you could hardly swing a cat in there.
|
|
craig1410
|
posted on 6/3/04 at 07:54 PM |
|
|
Jonte,
Can't you get it chromed then just grind off enough chrome to enable you to weld it on to the chassis? I expect that you will want to cover up
the bit where the rollbar meets the chassis anyway for aesthetic reasons.
I considered bolting my rollbar on but couldn't find an elegant method of bolting it on hence I ended up welding it. Once I've dressed the
welds a little bit I think it will look a lot neater than if it had 3 or 4 bolts in non-uniform places.
If I had gone with the bolted method then I would have drilled through my chassis tube "O" and installed crush tubes with a 2 or 3mm wall
thickness (fully welded into the tube). I would have done the same with the little 4 inch long piece of square section at the back of the suspension
turret. I would then have used four M10, 12.9 ton Socket Cap Head screws nicely spaced around the perimeter, passing through the four crush tubes. I
would probably have welded the nuts on the underside to make them captive to avoid fiddling about at a later date once all the bodywork was in
place.
Cheers,
Craig.
|
|
Nick Davison
|
posted on 6/3/04 at 11:23 PM |
|
|
Why chrome, cant you use stainless. I bought some 50mm X 2mm cds from a stockist £36 for 6m of the stuff and had it bent to a patern made from some
15mm copper water pipe covered in lagging.
|
|
JoelP
|
posted on 7/3/04 at 12:28 AM |
|
|
and if anyone does end up welding near chrome, remember the crap about chromates or whatever they're called, no point poisoning yourself for a
hobby...
|
|
Mark Allanson
|
posted on 7/3/04 at 12:30 AM |
|
|
hobby - HOBBY - It's a bloody lifestyle!!!
If you can keep you head, whilst all others around you are losing theirs, you are not fully aware of the situation
|
|
Mark Allanson
|
posted on 7/3/04 at 12:35 AM |
|
|
I originally was going to bolt mine down, but welded it in the end.
I used the bolt holes as 'welders rivets'. I put the bolts thougth the holes the wrong way up and then plug welded them up on the upper
face. You end up with 10mm structural rivets. the contraction of the weld pool as it cools draws up the bolt to make it stronger than any torque
setting.
If you can keep you head, whilst all others around you are losing theirs, you are not fully aware of the situation
|
|
JoelP
|
posted on 7/3/04 at 12:44 AM |
|
|
i just need to find an easy way to get the tubes bent... was gonna use inch square but theres not much point in making it from that...
good plan to weld the bolts though.
|
|
craig1410
|
posted on 7/3/04 at 01:24 PM |
|
|
The point about chromates also applies to stainless steel as it has chromium content too. In fact it may even have a higher chromium content than
chrome plated mild steel...
Cheers,
Craig.
|
|
flak monkey
|
posted on 7/3/04 at 01:28 PM |
|
|
Stainless steel is usually between 15 and 20% chromium IIRC and 2-3% nickel. Dont know what the content for chrome plated steel is though.
David
Sera
http://www.motosera.com
|
|
craig1410
|
posted on 7/3/04 at 01:41 PM |
|
|
David,
I'm not sure how thick a typical chrome plate is but I'd guess about 0.1mm or so (thickness of paper). On a rollbar with a 3mm wall, the
20% chromium content would equal the equivalent thickness of (3mmx20%) = 0.6mm so unless the chrome plate is 0.6mm or more then welding stainless is
probably more hazardous than chrome plated steel, especially if, as I said earlier, the chrome is ground away from the weld site (1/2inch or so).
In any event precautions should be taken against breathing this stuff in or ingesting dust and debris.
Cheers,
Craig.
|
|
derf
|
posted on 7/3/04 at 03:14 PM |
|
|
I used two 4" long cuts of 16gauge 1x1" tube on each side of the 4x4 squares, when I do fit the roll bar I will drill 4 holes, 1 in each
corner through the 1" steel tube, then fit in some small hollow tube, weld that in on top and bottom, grind the top flat, then thread-tap the 4
small tubes, then I will bolt the top plate to the lower plate, then weld the roll bar to the top plate. If you put it in the corners it will be
stronger. This will allow you to chrome the roll bar.
Image deleted by owner
[Edited on 7/3/04 by derf]
|
|
Mark Allanson
|
posted on 7/3/04 at 07:31 PM |
|
|
Chrome plate is very thin, the work is first nickel plated (0.05mm?) and the chrome plated, this is only a few microns thick
If you can keep you head, whilst all others around you are losing theirs, you are not fully aware of the situation
|
|
derf
|
posted on 8/3/04 at 01:20 PM |
|
|
Correct chrome plate us uber thin, that is why it is nickle plated first, then sanded to look for imperfections, then nickle plated again, then
chromed, and buffed to look for imperfections, then chromed again and buffed again (there's alot more to it than just that, but thats the
important stuff) Chrome is also alot of maintenance to keep clean and shiny, and it weighs alot.
|
|