zilspeed
|
posted on 3/6/04 at 08:23 AM |
|
|
Durable wing stay design.
Looking for suggestions for a durable wing stay design. My current ones start of as round tube which butt welds onto flat bar which is then bent over
the wheel to form the shape under the cycle wing. There is a clear weak point at the point where the flat bar and round tube butt weld together - end
on end.
Any suggestions ?
One has failed and I am going to repair it by replacing the flat bar with a longer piece which I will run down the side of the round tube and give a
much longer contact area between the two.
Really I'm looking for suggestions for a design which has no obvious failure points built in as my current ones, frankly, do.
[Edited on 3/6/04 by zilspeed]
|
|
|
AvonBelgium
|
posted on 3/6/04 at 08:28 AM |
|
|
If you use a tube that you squeze to make it flat neare the tyre.
I think this will be stronger
|
|
Mix
|
posted on 3/6/04 at 08:40 AM |
|
|
I would flatten the ends of the round tubes and insert the flat bars inside them, then weld the two together. There will still be a weak point at the
change of section but the flat bar will better supported and I think will look better than running the bar outside the tubes.
Just my opinion though.
Mick
[Edited on 3/6/04 by Mix]
|
|
mangogroove
|
posted on 3/6/04 at 09:34 AM |
|
|
Perhaps a web welded on the inside would help 8mm bar.
These cycle wings have and will always give trouble to the masses. The other thing is to get some fake carbon ones made of plastic from that lighting
supplier.
Fibreglass ones are heavy unsprung weight. Reduce this and the brackets will not have to work as hard.......
|
|
Hugh Paterson
|
posted on 3/6/04 at 10:51 AM |
|
|
Im with Mangogrove, flat bar but welded with webs spreading the load at the joint between the flat bar/tube. What u using to weld Mig?
Shug.
|
|
zilspeed
|
posted on 3/6/04 at 11:01 AM |
|
|
Mig is all I can do shug.
As someone said to me years ago, "I'm an armature ".
I believe he was an electrician.
I sincerely hope the weather improves or I'll be doing nothing today.
|
|
Hellfire
|
posted on 3/6/04 at 11:41 AM |
|
|
I believe the MK ones are done in the way of...
quote: Originally posted by Mix
I would flatten the ends of the round tubes and insert the flat bars inside them, then weld the two together. There will still be a weak point at the
change of section but the flat bar will better supported and I think will look better than running the bar outside the tubes.
and I am not aware of anyone having problems with them.
Incidentally, the arches themselves... MK now do a cracking bit of GRP (with moulded 'lug type things) that makes them look totally made for the
job!
If anyone has a picture?
[Edited on 3-6-04 by Hellfire]
|
|
craig1410
|
posted on 3/6/04 at 11:49 AM |
|
|
Hi,
I'll be doing my wing stays soon and perhaps I'm being naive but if the edges of the bar and flat are bevelled to permit full weld
penetration (multi pass if required) then shouldn't it be strong enough no matter whether it is a simple butt weld? If not then I'd
suggest cutting a slot in the round bar to allow the flat bar to be inserted for 25mm or so before fully welding.
Cheers,
Craig.
|
|
zilspeed
|
posted on 3/6/04 at 12:13 PM |
|
|
Flat bar up the middle of the tube it is then lads.
Sometimes all it takes is a couple of ideas to help see a better solution
|
|
Markp
|
posted on 3/6/04 at 05:04 PM |
|
|
I had the same problem
in the end I welded them back together, added a small bit of metal around the area where it snapped and added a metal strip joining the two which
makes it more rigid
mark
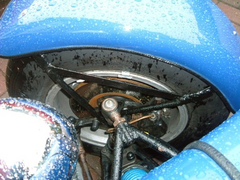 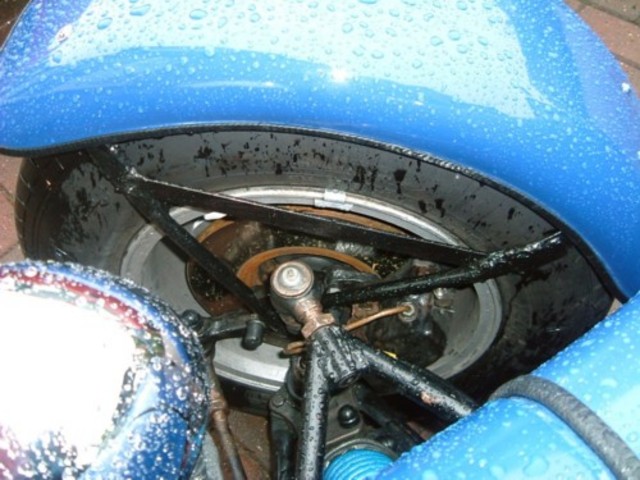 Rescued attachment cycle.JPG
|
|
stressy
|
posted on 3/6/04 at 08:28 PM |
|
|
and now for something completely different.......
I used tube for the whole shebang as follows:
cut a steel plate which has holes to match those on the upright intended to locate the disc covers.
bolt in position using either a spacer if fixed or if you have a mishmash of wheels then go for double nuts.
use a pipe bender to form 90 degree bends in two peices of pipe. one for the front stay, one for the rear.
assemble on sheet with clamps and weld to plate as desired.
trim plate back and tidy up.
when fitting arches bed them down on either a mastic or light filler.
Having had an immediate failure with the original design this has given me 1000,s of miles of happy use. i even managed to damage an arch keeping the
stay intact...
|
|
britishtrident
|
posted on 3/6/04 at 08:58 PM |
|
|
Squeeze the tube -- while red hot then reheat and quench to refine the grain structure
Also don't weld the joint braze it
|
|