RazMan
|
posted on 30/8/10 at 08:53 PM |
|
|
Bending box section into a curve?
I'm looking at a door mod which would involve bending some 15mm box into a 60mm radius. Is this even possible to do accurately? The material
needs to be pretty strong and as rigid as possible as it will have the whole weight of the door hinging on the two bends (long hinge welded to them)
maybe stainless is suitable ??
As always, any advice is appreciated
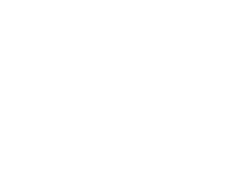 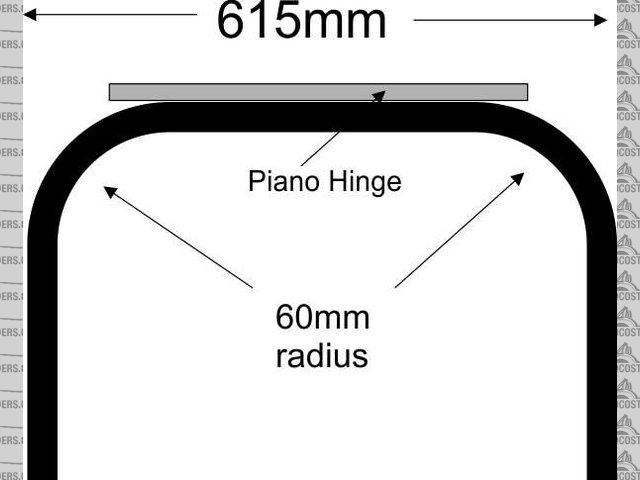 Door Mod2
[Edited on 30-8-10 by RazMan]
Cheers,
Raz
When thinking outside the box doesn't work any more, it's time to build a new box
|
|
|
gavin174
|
posted on 30/8/10 at 09:30 PM |
|
|
yes it is possible..
dont ask me how thou.
a friend has just make hoops for the back of his VW from box....
u2u me some more details and i will get a price for you
http://www.essexkitcarclub.com
|
|
MikeR
|
posted on 30/8/10 at 09:38 PM |
|
|
in theory you can take a hefty bit of wood, cut a square hole in it, open out one side of the wood so one face of the square is enlarged into a curve.
Insert steel, pull down on the steel using the enlarged section to bend the steel. The wood supports the metal stopping it from buckling (in theory).
How you do it accurately, ere, no idea, pay mk to make you two.
Mike
|
|
iank
|
posted on 31/8/10 at 08:15 AM |
|
|
The bit of wood with a hole is called a bending beam. John Bonnett was the man, but he doesn't visit any more and all his pictures are gone.
But FWIW
http://www.locostbuilders.co.uk/viewthread.php?tid=48785
http://www.locostbuilders.co.uk/viewthread.php?tid=76028
--
Never argue with an idiot. They drag you down to their level, then beat you with experience.
Anonymous
|
|
2cv
|
posted on 31/8/10 at 08:50 AM |
|
|
It is true that square tube can be bent without kinking using a bending beam but I think you might struggle with this method bearing in mind the
relatively tight radii that you need.
A better bet might be a tube bender with a mandrel made to suit 15mm square tube similar to that used to form a windscreen frame.
|
|
StrikerChris
|
posted on 31/8/10 at 11:47 AM |
|
|
Pyramid rollers,ive rolled alot bigger box,cant see the small stuff being a problem if the walls thick enough.
|
|
2cv
|
posted on 31/8/10 at 02:19 PM |
|
|
The problem is Chris that pyramid rollers are quite specialised and not something that one normally has in the workshop or can hire locally. Nobody is
doubting that square tube can be bent to the radius required, it's just finding a way that is possible with the tools available.
|
|
RazMan
|
posted on 31/8/10 at 05:19 PM |
|
|
Thanks for the info guys
Just a thought - I have bought many different mandrel bends in the past (for exhausts, intakes etc) so is anything available in box section like that?
Cheers,
Raz
When thinking outside the box doesn't work any more, it's time to build a new box
|
|
2cv
|
posted on 31/8/10 at 05:40 PM |
|
|
Thinking "Out of the box" ouch!!. I've seen some chairs made from square tube with some fairly tight bends.
|
|
2cv
|
posted on 31/8/10 at 06:44 PM |
|
|
Raz, I've had an idea how to do it. I'll have a play tomorrow and get back to you.
|
|
2cv
|
posted on 31/8/10 at 07:40 PM |
|
|
Can you use 15mm steel square bar? This would be very easy to bend. Okay, heavier than tube but its got to be rigid enough.
Raz can you let me know before I get involved with my tube idea.
|
|
RazMan
|
posted on 31/8/10 at 09:11 PM |
|
|
quote: Originally posted by 2cv
Raz can you let me know before I get involved with my tube idea.
I don't think I can use bar as the door would be far too heavy and there are more bends involved lower down in the doors. These are gull wing
doors and due to the limits of the existing design I need to keep everything as light as possible.
I think I may have found a company that can form various sections but I need to phone them to be sure.
Cheers,
Raz
When thinking outside the box doesn't work any more, it's time to build a new box
|
|
TQ_uk
|
posted on 1/9/10 at 10:48 AM |
|
|
Will the bends be visible once door is finished?
Can't you either 'pie-cut' box section or make the bend out of sheet (ie cut the 2x curved 'L' faces and bend the
remaining 2 faces from a 15mm(ish) wide strip?
Or a combination, i.e pie cut and reinforce with side plates cut from sheet?
|
|
RazMan
|
posted on 1/9/10 at 11:02 AM |
|
|
That's a thought - maybe even get the curves laser cut and tig them to the rest of the frame.
p.s. The bends will be in full view so neatness will be the order of the day.
Cheers,
Raz
When thinking outside the box doesn't work any more, it's time to build a new box
|
|
Angel Acevedo
|
posted on 1/9/10 at 04:13 PM |
|
|
Soapy water for Bends
I saw a program where they made trumpets, and they freeze soapy water inside the pipes prior to bending.
You may try this and let us all know how it went?
Beware of what you wish.. for it may come true....
|
|
2cv
|
posted on 1/9/10 at 04:55 PM |
|
|
Raz, do I gather you are still looking for a solution?
|
|
Fred W B
|
posted on 1/9/10 at 05:39 PM |
|
|
quote:
maybe even get the curves laser cut and tig them to the rest of the frame
Thats what i was going to suggest, fabricate the bends. 60 mm is a tight radius and bent square tube always looks lousy.
Cheers
Fred W B
You can do it quickly. You can do it cheap. You can do it right. – Pick any two.
|
|
RazMan
|
posted on 1/9/10 at 08:08 PM |
|
|
quote: Originally posted by 2cv
Raz, do I gather you are still looking for a solution?
I am forming a cunning plan at the moment - hopefully forming steel in due course
Thanks for all the ideas guys - I am going on my hols at the weekend so I will have another look when I get back to Blighty.
Cheers,
Raz
When thinking outside the box doesn't work any more, it's time to build a new box
|
|
2cv
|
posted on 3/9/10 at 05:58 PM |
|
|
I have to say that I'm intrigued by this little problem and while you are on holiday Raz, I've been wasting some hours experimenting with
just simple tools to give a decent result. Indications are that forming curves (L section), stretching on one and shrinking on the other and then TIG
welding them together might work.
|
|
2cv
|
posted on 4/9/10 at 08:43 AM |
|
|
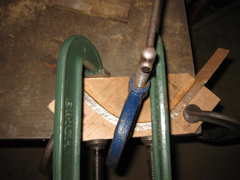 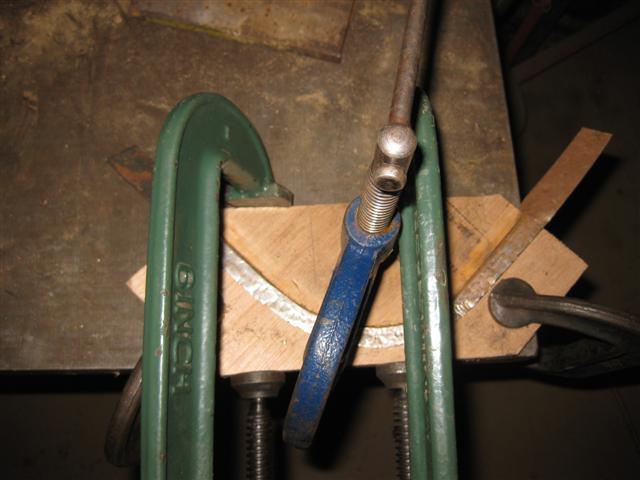 Description
Using marine ply as a hammerform, the first section is formed
[Edited on 4/9/10 by 2cv]
|
|
2cv
|
posted on 4/9/10 at 08:47 AM |
|
|
[img]
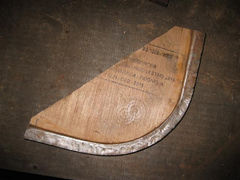 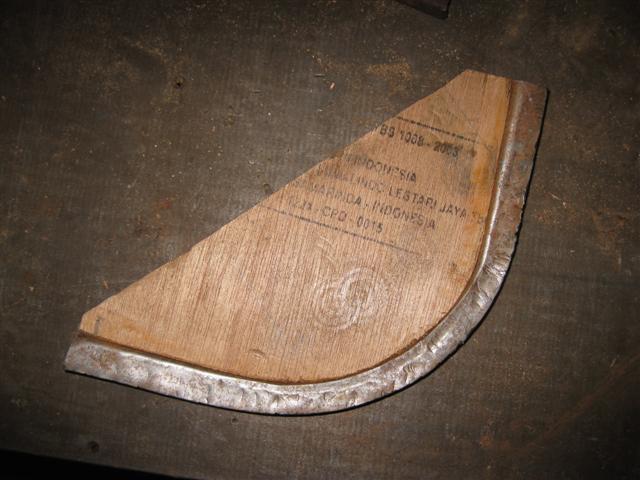 Description
[/img]
Just planishing needed to work out the hammer marks
|
|
2cv
|
posted on 4/9/10 at 08:49 AM |
|
|
[img] Image deleted by owner[/img]
Shrinking started on section 2
|
|
2cv
|
posted on 4/9/10 at 08:51 AM |
|
|
A bit more forming done
[img]Image deleted by owner[/img]
[Edited on 4/9/10 by 2cv]
|
|
2cv
|
posted on 4/9/10 at 08:57 AM |
|
|
[img] Image deleted by owner[/img]
The two pieces with identical radii.
Okay, you say, they won't fit together because one needs to be a larger radius than the other and you'd be absolutely right--- doh!
The next step then is to cut a hammerform to the larger radius to produce a mating piece and weld them together. However, before welding, some
trimming will be necessary where stretching has taken place. The bends can easily be sharpened up by back chasing using a dolly and hammer.
[Edited on 5/9/10 by 2cv]
[Edited on 5/9/10 by 2cv]
|
|
2cv
|
posted on 4/9/10 at 11:20 AM |
|
|
This has got to the point where it should be in the "Tools and Techniques" section
|
|