Chaddy
|
posted on 25/2/11 at 01:17 PM |
|
|
Cycle wings
Does anyone know where I can get cycle wings with the correct radius for 195/50/15 tyres, they all seem to be more for 17 inch.
Cheers
Chaddy
|
|
|
Gordy
|
posted on 25/2/11 at 02:38 PM |
|
|
i got csr style carbon wings from "carbon mods" they will supply to fit radius of your tyre, not cheap but nice quality items 
|
|
2cv
|
posted on 25/2/11 at 04:29 PM |
|
|
Have you thought of making them in aluminium? Not too difficult and the great thing is, they will be exactly the size you want.
This is another part that you can make using just hand tools.
|
|
Chaddy
|
posted on 25/2/11 at 04:37 PM |
|
|
Good idea, what thickness would you use, do you have any pictures of any you have made.
Cheers
Dave
|
|
2cv
|
posted on 25/2/11 at 04:54 PM |
|
|
Hi Dave,
You could use NS3 18 gauge which is about 1.2mm thick. NS3 is quite a tough alloy but reasonably easy to form. Alternatively 1050A pure aluminium in
1.5mm would be okay too. The edges of the finished wing would need wiring but this isn't too difficult and I did cover this with some pictures
here; linky
If you are unsure how to proceed, I'll be very pleased to show you how to form the wing and get rid of the crinkles around the edge. If you let
me know if this is of interest, I'll get some pictures posted next week.
|
|
Chaddy
|
posted on 25/2/11 at 06:53 PM |
|
|
Thanks 2CV, I'll have a look over the weekend.
Cheers
Dave
|
|
slingshot2000
|
posted on 25/2/11 at 07:35 PM |
|
|
I would be very interested in seeing this information, too!
I am planing to try more and more of this sort of thing and appreaciate any knowledge that more experience people are willing to share. I will look
forward to following this, thanks in advance.
Regards
Jon
|
|
2cv
|
posted on 28/2/11 at 09:34 AM |
|
|
There are a number of ways to make a front cycle wing in aluminium and no one way is the right way. It is just a question of finding which way suits
not only the individual's skills but also the tools available.
This is one way using a Hammerform. I've deliberately made the radius 8 inches which is probably 50% smaller than would be needed for a normal
tyre. Here's the start;
[img]
 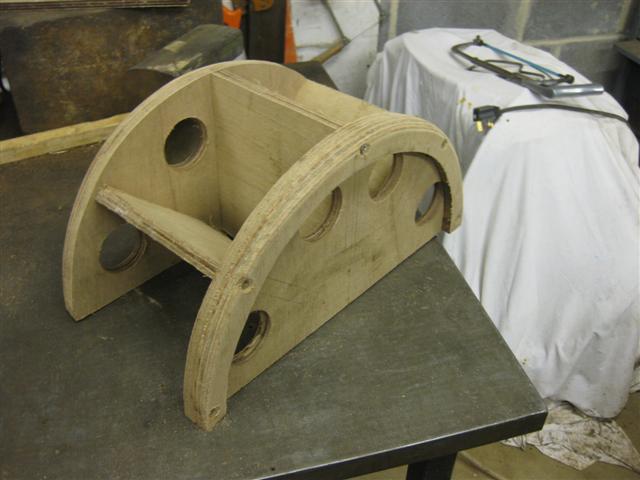 Description
[/img]
[Edited on 28/2/11 by 2cv]
|
|
2cv
|
posted on 28/2/11 at 01:12 PM |
|
|
Here are a few pictures showing how you could go about making your cycle wing. I used 18 gauge 1.2mm 1050A aluminium and I think with anything thicker
you might struggle. With the aluminium clamped firmly in place, the edges are tapped over.
[img]
 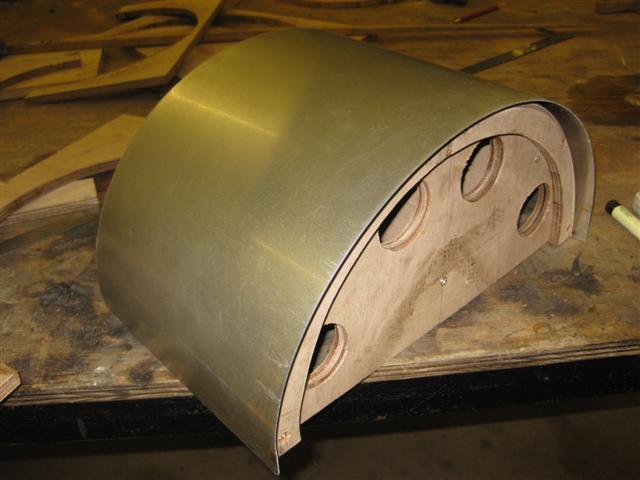 Description
[/img]
[img]
  Description
[/img]
The panel is removed from the hammerform.
The general shape, finish and radius together are improved with a slapper and dolly. (Can do nothing without them!)
[img]
 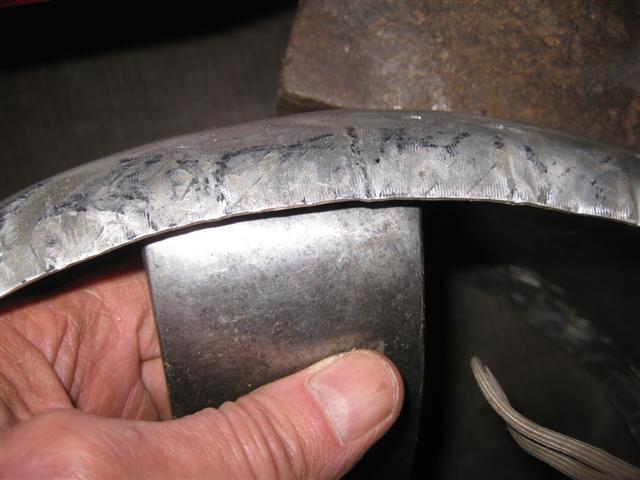 Description
[/img]
Further work was done using a body file to take off the highs and show where the lows were. Further planishing raised the lows followed by more with
the body file.
[img]
 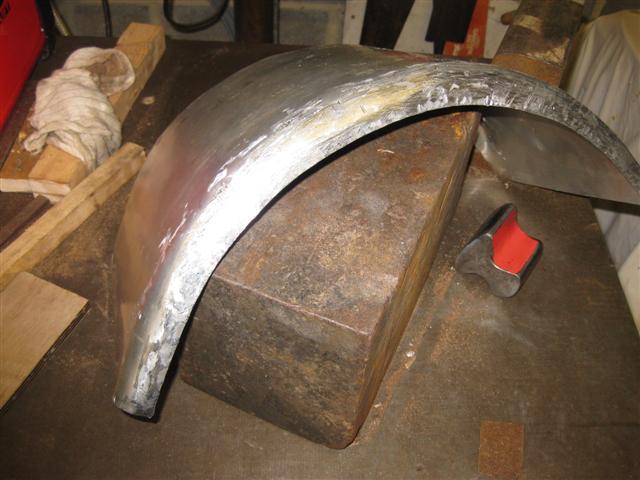 Description
[/img]
[img]
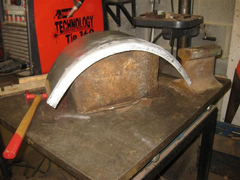 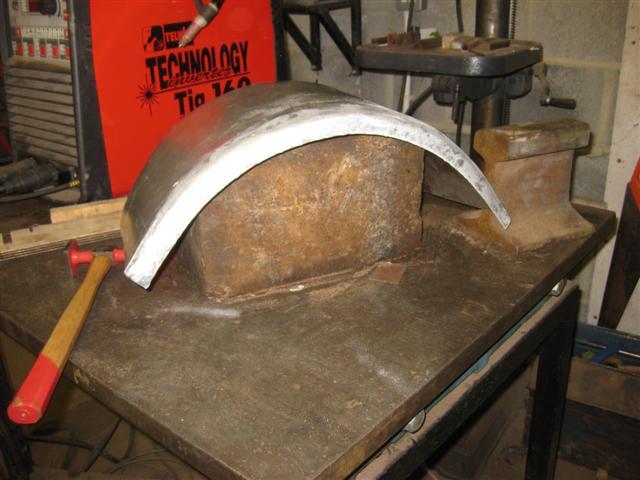 Description
[/img]
Further work is needed to finish followed by trimming and edge wiring. The end result could look similar to a Caterham wing or made to be very
individual.
I hope these pictures show the general idea of achieving the curves and will perhaps encourage people to have a go themselves. I only used the tools
that everone has in their workshop and the cost of the aluminium would be well under a tenner so, truly Locost!
p.s I've just noticed that Westfield sell their plastic wings for £89 each.
[Edited on 28/2/11 by 2cv]
[Edited on 28/2/11 by 2cv]
[Edited on 28/2/11 by 2cv]
|
|
2cv
|
posted on 13/3/11 at 07:23 AM |
|
|
It might make the job easier if the edges of the aluminium are annealed beforehand. I used 1.2mm 1050A which wasn't too bad to work but if a
harder or thicker material is used, anealing would certainly be a good idea. By the time the wiring stage is reached, the edge should be sufficiently
work hardened to allow a nice sharp flange to be thrown.
|
|
2cv
|
posted on 14/3/11 at 12:14 PM |
|
|
Just another thought; instead of using G clamps which do get in the way when hammering down the return, it might be easier to join the two radiused
ply profiles together transversely and then pull them down using a strap around the centre. This will then allow full access to the edges making the
shrinking operation much simpler. The crinkles should be carefully worked out to avoid folding over to make a double thickness. The idea is for the
metal to shrink back into itself.
|
|
:{THC}:YosamiteSam
|
posted on 15/3/11 at 01:12 AM |
|
|
i tried a different approach.
i had 2 fibreglass arches which were getting tired and i felt were too wide slightly.
so i chopped the sides off them leaving a bonding face to bond 1.2mm ally to. used sikaflex type glue stuff. overnight is rock solid.
reason i didnt use ally for the sides is its a right faff on to form it if you havent the time to do it or lack the skill to do it right. suppose it
could of been done like 2cv has done [i applaud you by the way - fantastic job as i know how hard that is for a beginner]
the arch in the pic is just in matt black primer so far to see what it would turn out like. once im happy with what iv created ill do the other one.
|
|
2cv
|
posted on 15/3/11 at 06:55 AM |
|
|
It looks really good, well done. I mentioned right at the beginning that there are many ways to to arrive at the same destination and it is just a
question of finding the way that suits you.
|
|