David Jenkins
|
posted on 14/10/08 at 05:48 PM |
|
|
A few thoughts about wing stays
Once again I have had to repair my nearside front cycle wing, which started me thinking again about ways to stop it breaking...
As I see it, there is one fundamental problem with these cycle wings - each is a large mass flapping about on the end of a number of steel stays.
There are many designs for stays, some of which last longer than others, but chances are that they will all break eventually. Usually there is a
stress concentration point somewhere in the design where the vibration will eventually do its worst.
There appear to be 4 solutions (to me, anyway):
1. Make the stays as strong and as rigid as possible
People have tried this with some measure of success, but the end result can be very heavy - and the vibration often finds somewhere to break it in the
end. Ultimately (IMHO) this is not a great engineering solution and unlikely to be 100% successful.
2. Devise some way of sharing the flexing along the whole length of the stays so that no one point gets stressed too much
I don't know of anyone who's tried this yet, but I believe that this is a possibility - I considered several layers of steel, bound together
loosely like a leaf spring. Alternatively some clever person could make them out of carbon fibre, with a tapering section to distribute the flexing. I
dread to think how much that would cost...
3. Stop the wing flapping in the first place, by bracing it on the outside of the wheel
I have seen this done very neatly on LocoR1's car - it looked very tidy and apparently is very effective, but there are some issues for my car.
This option seems to be the best way to address the root cause of the problem, by stopping the wing flapping in the first place. This means that the
main stays to be just strong enough to hold the weight (and a lot easier to design). LocoR1's design seems to be the way to go, but then I got
thinking - I have very little space to fit anything inside the hole in the wheel, as the bearing cap takes up most of the room. Whatever I fit is
going to have to have a very thin rim, and I can't yet see how to fix it in place. If that could be solved then the rest of the fixing is fairly
easy to sort out.
As I was staring at the front hub trying to solve this problem, I had a thought - sticking through the wheel is the end of the stub axle, which is
stationary in relation to the upright and does not rotate with the wheel. If some way could be found to fix a support to the end of the stub axle then
it wouldn't be necessary to add extra items to the outside of the wheel. This would reduce complexity and risk of failure (imagine what would
happen if the bearing seized up).
There appear to be two methods available for fixing something to the end of the stub axle: using the hub nut thread, or drilling and tapping into the
end of the axle. The axle doesn't have a lot of spare thread once the hub nut is fitted, but there should be sufficient to hold a light bracket
(I don't see that the outer wing support would have a lot of force on it). I suspect that drilling into the end of the stub axle might be a
'challenge', as I am sure that it is made of hardened steel - it wouldn't be possible to go very far as the cotter pin hole is only
about 10mm - 15mm from the end. Either method would require some way of replacing the hub's grease cap.
I can see one significant risk with this solution, which is the damage that may be done to the stub axle if there was a glancing blow on the stub axle
extension. This could be expensive, but could be minimised if the extension was made of something 'expendable' like aluminium or plastic.
4. Get rid of the cycle wings and fit clamshells
Not to everyone's taste, their aerodynamics can cause a light front end at very high speeds, and they are very hard to buy new (I've been
looking, but I haven't found a stockist yet). However, they do have the advantage of not breaking off every few thousand miles, and they offer
pedestrians some measure of protection from the front part of the hot exhaust pipe. I haven't abandoned this option, if all else fails, as
aerodynamics don't play a big part in the sort of driving I do (and I think that they look OK).
So there you have it - some random thoughts on sorting out the wing stay problem - anyone got any thoughts?
|
|
|
locoR1
|
posted on 14/10/08 at 06:06 PM |
|
|
Looking at your picture I don't see why you couldn't drill and tap into the end of the stub axle then use a stud with some kind of seal
through the stub axle cover, as you say no need for the added complexity for a bearing,
As for the wing stays mine are just standard book design so you wouldn't of expected them to of lasted over 6 years if it wasn't for the
stays.
Looking forward to seeing your solution.
Dave........
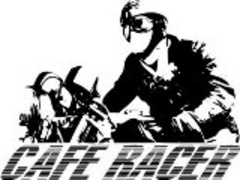 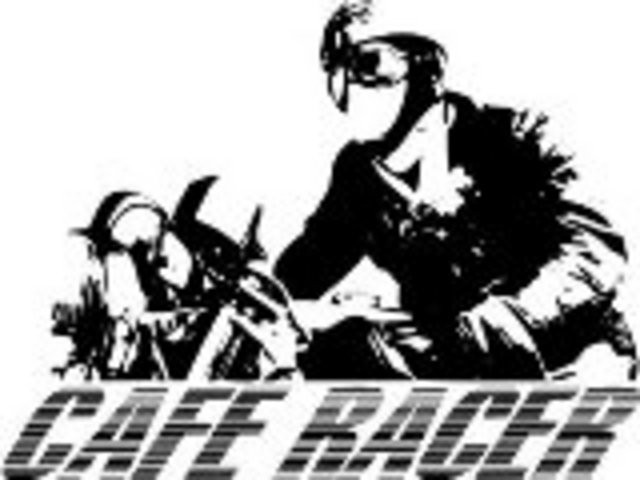 Description
Check out my CB500T Cafe Racer build diary
|
|
Mark Allanson
|
posted on 14/10/08 at 06:16 PM |
|
|
Just don't have the stays. I supported mine down the inner edge, not have any problems in 3 1/2 years on the road
If you can keep you head, whilst all others around you are losing theirs, you are not fully aware of the situation
|
|
COREdevelopments
|
posted on 14/10/08 at 06:19 PM |
|
|
you can scrap idea 4 for a start!! clam shells are hideous. and only belong on the original lotus 7s.
i have done just over 1000 miles and so far (touch wood) no signs of cracking. think its down to design and constuction of the stays. the design in
your picture is a good idea but personally i think it doesnt fit in with the looks of overall car and would stick out like a sore thumb.
try looking at CLOUDY (a member on here) he had a good design and claimed his didnt shake.
atb
Rob
|
|
panichat
|
posted on 14/10/08 at 06:21 PM |
|
|
Interesting...
Is there any way that the cycle wings themeselves could be re-designed so that they don't vibrate so much? Perhaps an aerodynamically minded
person could analyse what forces are being produced and suggest ways to give less drag and more stability.
Is there any way that the wing stays could be designed with a cheap and easy to replace "weak section" that could be checked and renewed
at regular intervals?
Dave
|
|
eznfrank
|
posted on 14/10/08 at 06:45 PM |
|
|
Looking at the photo of yours in your archive (and assuming they're the same??) they look quite small and sat quite far back on the wheel.
How about trying some slightly bigger ones rolled forward a bit to stop all the air going up and under?
|
|
David Jenkins
|
posted on 14/10/08 at 06:54 PM |
|
|
I don't think that it's an aerodynamic problem - it's simply the wing boinging up and down as the wheel goes over the Essex &
Suffolk ruts. The evidence for this is the fact that the other wing on the driver's side has never broken (I shouldn't say things like
that...), it's the nearside that gets the pounding.
Rob - I used to boast that my wing stays never broke - until I got to 3,000 - 4,000 miles, at which point I stopped boasting! Also, I've seen
Dave's car in real life, and the extra stays are very discrete and do fit in with the car's design, as you can see here.
[img][/img]
|
|
Mark Allanson
|
posted on 14/10/08 at 07:17 PM |
|
|
just do away with them completely
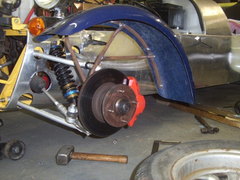  Rescued attachment ModCycleWings.jpg
If you can keep you head, whilst all others around you are losing theirs, you are not fully aware of the situation
|
|
Humbug
|
posted on 14/10/08 at 07:43 PM |
|
|
Option 5: cycle type wings permanently attached to the bodywork like some Duttons. Cycle wing look without the flexing problem.
I would have a more rounded sevenesque nose rather than the squared-off one here.

|
|
TOO BADD
|
posted on 14/10/08 at 07:57 PM |
|
|
A pair of gull wings on ebay £40 start no bids 22hrs to go !
|
|
rusty nuts
|
posted on 14/10/08 at 08:27 PM |
|
|
David , there is no reason you couldn't turn up an extension piece to screw onto the stub axle replacing the hub nut . Aligning the split pin
holes may need a bit of thought, possibly shims between the extension and the washer? . Have you thought about the weight of the cycle wings? as it
could be a contributing factor of the stays breaking. I intend making some stronger stays and replacing the wings with lightweight items .
|
|
David Jenkins
|
posted on 14/10/08 at 08:40 PM |
|
|
Mel,
That's pretty much what I was thinking of doing - making an extension piece that would act as a lock nut for the hub nut. I'd guess that
drilling the extension across all the flats would make lining up the split pin fairly easy.
The wing itself is quite light - it's 'minimum size' so probably as light as it's possible to get a GRP wing.
|
|
rusty nuts
|
posted on 14/10/08 at 08:47 PM |
|
|
Carbon fibre is very light although it has the effect of lightening the wallet as well
|
|
02GF74
|
posted on 15/10/08 at 07:54 AM |
|
|
I had to get my head round the mounting point for the wire stays until it dawned the stub axle was not rotating....
Effective solution but I personally don't like it.
I've had one stay go and it was at the point where the flat metal with the bolt hole meets the 10 mm square tube for the stays.
From what I have seen, the stays almost always break neer the mouning point since this is the point where the moving stay meets a stationary
bracket.
Like what has been said, reduce the mass of the cycle wing; reduce the mass of the stay near the wing but beef it up near the mounting points.
Also to stop movement of the stays/wings, add a support from the top ball joint - in effect reduces the length of the levers (stays).
At some point I will beefen up the the mounting brackets and add the additional support.
|
|
David Jenkins
|
posted on 15/10/08 at 07:58 AM |
|
|
quote: Originally posted by 02GF74
I had to get my head round the mounting point for the wire stays until it dawned the stub axle was not rotating....
.
Dave's solution isn't fixed to the stub axle - it's a plastic plug fixed securely into the wheel hole, with a bearing fixed in. The
stays are fixed to the inner of the bearing.
|
|