MikeR
|
posted on 18/9/23 at 08:16 PM |
|
|
https://www.amazon.co.uk/Extension-Cable-Female-Supply-Optiplex/dp/B09NBK3Z4M
Would that work as a pigtail (if you cut the atx end of and stick with the mini atx end)
|
|
|
robocog
|
posted on 18/9/23 at 08:58 PM |
|
|
Traces are nice and wide (about 2mm??, not sure how thick ) for the stuff that is controlled from the transistors on the NO2C, but only got the
option of single output pins per bank
Was only when I compared to the DB37 plug pin sizes and realising that they are also using 2 pins for each inj bank to spread the load that I started
to get a bit twitchy
Looking at the Molex pages, and finding something similar... if not the same - I see they rate those at 8.5A per pin..and I am fused at 5A per pair of
injectors and have never blown one....so I am very likely worrying about nothing, but when comparing surface contact area , it just LOOKS wrong before
even talking about splitting the load across a couple of pins on the DB37 connector
I possibly went overboard on the size of connectors and wires to the injectors needlessly in the rest of the loom...big ugly white square connectors
with 6.3mm spades...
Normal to want to over engineer and overthink these things I guess...
Am torn now....
|
|
MikeR
|
posted on 19/9/23 at 08:51 AM |
|
|
https://www.google.com/url?q=https://m.youtube.com/watch%3Fv%3DTin42HBdE-Y&sa=U&ved=2ahUKEwjI5JnbpbaBAxU4XEEAHfZXA4AQtwJ6BAgDEAE&usg=AOvVa
w1bgzo5Q33o669E88M7cbb2
May or may not reassure you.
|
|
robocog
|
posted on 24/9/23 at 07:04 PM |
|
|
Still haven't decided, so have soldered in wires for now (easier to remove and go with the multiplug if I change my mind)
Hooked it up to a megastim - checked O2, TPS, CLT, IAT and that I had fuel pump output
All working great (but input voltage is showing as quite out of whack reading about 4v higher than a bench PSU - verified with a multimeter as well
...not sure if I need to deal with this or if it is a non issue, get an annoying red warning about input voltage when it sees a real 13 volts..and it
shows closer to 17v on TS)
Hooked it up to the car - calibrated the TPS, and I am getting sane readings from the other "real" sensors as well..
wired the VR up and did a tooth log and reversed the VR pins so I could see which way it was happiest... as advised.... (no filter applied)
  tooth log 1
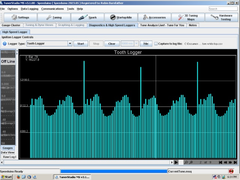 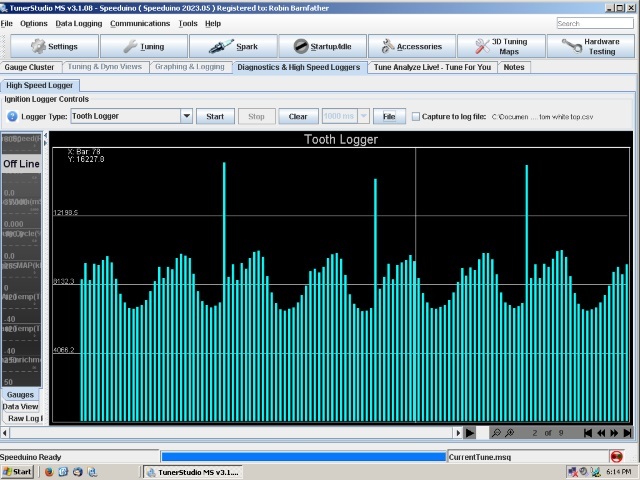 tooth log 2
I guess the bottom one gives the best signal ...and is the one with the positive wire from the VR on the bottom terminal on my sensor...cannot
remember which way they are wired
and I guess the dips are where the engine is pushing over compression in the cylinders whilst cranking over
Just awaiting a coilpack plug (forgot to order one) and I can get the ignition side loom sorted
Dug out a strobe light and verified it works (fired car up with the old MS unit)
Not got a timing mark as I changed the sump to an ERA one - so will have to find TDC and make a pointer and suitable set of marks and use that
All systems go, hopefully not too far off it starting with the speeduino...if all goes to plan
(and then the hard work of getting it running nicely)
I guess I can sort of transpose the 8X8 I have in MS and a kind of make new tables from the tables I have
I am guessing no easy way of "exporting and importing" due to the table size differences
As and when I get it running I am happy to share the msq...but I guess unless someone else is running the same TB's/injectors/regulator and pump
etc it will only be something to refer to rather than a plug and play setup
[Edited on 24-9-2023 by robocog]
|
|
MikeR
|
posted on 25/9/23 at 10:23 AM |
|
|
The second tooth log is what you're looking for HOWEVER its dependent on your VR sensor. You set your trigger edge to your VR sensor and then
adjust the wiring to look like the second picture. (this is a mantra for me as people get it wrong, then get issues with high rpm timing drift or bad
sparks and say "speeduino's rubbish" .
|
|
coyoteboy
|
posted on 25/9/23 at 10:43 AM |
|
|
quote: Originally posted by MikeR
https://www.google.com/url?q=https://m.youtube.com/watch%3Fv%3DTin42HBdE-Y&sa=U&ved=2ahUKEwjI5JnbpbaBAxU4XEEAHfZXA4AQtwJ6BAgDEAE&usg=AOvVa
w1bgzo5Q33o669E88M7cbb2
May or may not reassure you.
Not really, voltage drop is key, not so much heating. Injectors need a low impedance path and dinky little wires don't help. Nor do unnecessary
connectors which each have a few tens of miliohms across them and potential for variation in performance. Someone in the comments points out that you
need a predictable low voltage drop to accurately control them, if the voltage drop in the harness changes with time, temperature or current, it makes
tuning tricky. But everything is a compromise.
|
|
scudderfish
|
posted on 25/9/23 at 07:46 PM |
|
|
quote: Originally posted by robocog
I guess I can sort of transpose the 8X8 I have in MS and a kind of make new tables from the tables I have
I am guessing no easy way of "exporting and importing" due to the table size differences
[Edited on 24-9-2023 by robocog]
You can export specific tables in TS, and then import them. It will interpolate the data to the new size
|
|
robocog
|
posted on 28/9/23 at 03:19 PM |
|
|
Awesome!
I have kind of interpolated the ignition and fuel map, and bunched the TPS loads up where I feel I needed more cells than relying on interpolation
gave with MS (again could be barking up the wrong tree as to the sole reason for going with speeduino over MS)
majority of the axis is taken up with 0% to 50% load, then bigger jumps to 100% load...
Bit more progress today
- got the loom made up for the ignition driver, hooked it all up and tested I have spark
Marked the front pulley and confirmed it was firing in roughly the same place as the edis was...
(swapped between MS and Speeduino whilst it is still trivial to do that)
Hoping tomorrow is OK weather wise and I can get the injectors wired in and see if I can make it "run" and get tuning
I need to make proper marks at TDC and 10 degrees to confirm it is advancing etc and get it dialled in properly, but much easier if it is actually
running
Not got a case for it yet, so its a bit precarious/sketchy and just dangling from the loom plug, so unlikely I will be taking it out for a test drive
with speeduino just yet
getting closer though.....
|
|
MikeR
|
posted on 28/9/23 at 04:21 PM |
|
|
I should be certain of this but I'm only 95% sure.
Cranking timing over rides locked ignition. So if you're spinning the engine slower than the cranking limit the advance won't be the
ignition fixed advance.
Hopefully that will stop you chasing your tail trying to figure out the timing.
|
|
robocog
|
posted on 28/9/23 at 07:27 PM |
|
|
Yes, cranking was quite slow, so not that easy to see, but looked to be in the ballpark(ish)
(I set to fixed 10 degrees...but as you point out it could have been at the cranking advance angle of 5...and I bet I am still a few degrees out on
the pickup, It sure looked close enough to the 10 degrees I was getting from the EDIS to at lest try and start it)
Have wired up the injector pins to the connector tonight, so hopefully if the weather is OK tomorrow I may get to attempt to start the car and double
check the timing
Will 3d print a case shortly, so /if/ I get that far tomorrow and am tempted to take it for a drive round the block it will be less sketchy
Should I be concerned about the misreporting of input voltage?
Only things I can see it affecting off the top of my head are the deadtime compensations and dwell compensation...but maybe there is more "behind
the scenes"
On a bench PSU (verified with a multimeter as well)
10v is showing as 12.4v in TS
11v = 13.9v
12v = 15.3v
13v = 16.7v
14v = 18.2v
This is after using the calibrate voltage offset reading in TS and reducing it to the max -2v...
|
|
robocog
|
posted on 28/9/23 at 11:04 PM |
|
|
and that was short lived
Just couldn't live with the wrong voltages being displayed...so got the firmware, modified the sensors ini and compiled using VS code
TS whined that versions didn't match, tried with arduino IDE...same issue...
downloaded another version of the firmware, used arduino studio, got the voltage almost dead nuts on...went back in and made a minor tweak and slowly
swept from 10v to 13v making note of the reported voltages (same as I had been doing when dialing in to get the reported voltages close...the
speeduino stopped responding,....loud pop - and C4 exploded and has stunk the room out
was only seeing 13v...so kind of glad it didn't do this after fitting to the car
Bit gutted TBH...not sure what to do now...
|
|
MikeR
|
posted on 29/9/23 at 06:37 AM |
|
|
I let the magic smoke out my first one that I soldered up. I then bought one pre made. Had no issues with that one. Go on the forum or Facebook or
discord and ask questions. Worst case send it to Richard bell on Facebook or eBay and he'll repair it.
|
|
robocog
|
posted on 29/9/23 at 08:07 AM |
|
|
Maybe all is not lost
It still seems to work / respond this morning, tested using stim on the bench....
Dug into the schematic, looked the board and arduino over for any "reasons" or witness marks etc...nothing found
The C4 cap is part of the inlet side for the 5v regulator
(I am guessing for suppression/smoothing)
Have desoldered it out of circuit and will carry on regardless for now
I just don't know why it decided it had had enough at 13v...it will potentially see more than that when installed in the vehicle!
Hoping just a bad component - as it was on a decent lab PSU and unlikely it would have put out anything other than what I told it to...
(looks at PSU suspiciously....)
Case has printed, voltages are now being reported accurately for everything between 10 and 14v after a recompile with new offset in sensors ini
Mine needed 254 to be changed to 170 to get it reading right...not sure why such a variation..but it is what it needed to be to read right
------------------------------------------------------------------------------------------------------------------------------------------------------
------------------------------
void readBat()
{
int tempReading;
#if defined(ANALOG_ISR)
tempReading = fastMap1023toX(AnChannel[pinBat-A0], 170); //Get the current raw Battery value. Permissible values are from 0v to 24.5v (245)
#else
tempReading = analogRead(pinBat);
tempReading = fastMap1023toX(analogRead(pinBat), 170); //Get the current raw Battery value. Permissible values are from 0v to 24.5v (245)
#endif
------------------------------------------------------------------------------------------------------------------------------------------------------
--------------------------------
I am running with speeduino-202207-fixes firmware as it was the only one that I could get TS to work with nicely after compiling
I tried with what I thought was the master, but ran into signiature issues as it was adding -dev to the name....
How do I change it? (can it be explained in a way that I would be able to understand?) TS's error message was not that helpful despite it
offering me to click a button to try and fix the conflict...the only 2 buttons that seemed to get me out of the loop was cancel or carry on but
ignoring the issue, which would repeat next power cycle
sky is grey but not yet raining...today is the day I guess... unless anything else goes wrong!
Will hopefully report back with good news!
|
|
MikeR
|
posted on 29/9/23 at 08:16 AM |
|
|
If you use the Dev firmware you need to tell tuner studio is on Dev. The name check is to ensure the mapping of fields in Tibet studio matches what is
on the arduino.
If you press ctrl-p in tuner studio (you can get there from a menu but I can't recall which one or during new project setup) and browse for the
ini file. it's in the folder listed before the speeduino folder with the source code. It's called speeduino.ini.
Doing this from phone at work so can't check actual locations.
|
|
robocog
|
posted on 29/9/23 at 11:44 AM |
|
|
Car starts and runs fine
Sun has come out in full force so I cannot see the laptop screen without sitting under the tonneu cover, so have come in to cool down
Too bright out there to see the strobe light, so will have to wait for another day...or to get an opportunity to take it indoors somewhere
I have confirmed the timing is moving and is very much in the same ballpark as EDIS was giving when locked to 10 degrees
Car revs up OK and seems to behave - but does still need a load of tuning
Car still "wants" to run quite rich at idle - seems "happiest" and smoothest in the 12's, if I lean it out from there it
gets a bit lumpy and revs start dying
Still have a lean patch with very slow throttle tip in from idle (same as I had with MS)
(not sure how to combat this - other than don't do that...)
maybe I can shuffle the fuel table a bit more and keep tuning that area...
But - major success I'd say
Still got to do a load of routing and tidying up of wires
also need a proper case as my 3d printed one is a bit chonky and doesn't have a lid yet and make some kind of decision whether to fully replace
the MS - or try and have it so they can be swapped out with little to no fuss till I have it fully under control
I will try and link to the msq for anyone else wanting a nosey at a mostly working but not tuned zetec speeduino looks like
(2l silvertop, R1/R6 throttle bodies, Bosch200 series igniter, zetec coil)
http://www.robocog.co.uk/speeduino/Zetec_silvertop_speeduino_starts_and_runs.msq
[Edited on 29-9-2023 by robocog]
[Edited on 29-9-2023 by robocog]
|
|
MikeR
|
posted on 29/9/23 at 12:58 PM |
|
|
Post your tune and a log on the speeduino log location and then ask for help on the forum / facebook. People will have a look and offer advice.
I'm nervous by your voltage the more i think about it - you shouldn't need to edit the code. Can you double check the battery voltage
circuits as it should 'just work'. I'm worried it has side effects.
|
|
robocog
|
posted on 29/9/23 at 03:22 PM |
|
|
Yes, it bothered me - to the extent I wanted to make changes to the code to make it "right" (computers doing calcs - BS in = BS out)
I know the voltages going in were clean (lab PSU, verified with multimeter)
Not much in the circuit on the NO2C for VCC power coming in
3 resistors, 2 capacitors then going off to ADC clamping and pin A1
I guess I /could/ have played with the voltage divider resistors to get the arduino to recognise closer to the actual input voltage, but the software
route seemed less likely to lift pads, plus was more of a learning curve
The cap (tantalum?) that blew is on the batt power input going to the 5v reg, I have a good steady 5v from it, so I don't think that the reg
caused it - or got harmed
Have messaged diy-efi where I got it - and asked about me having to recompile for input voltage to be right
(and to see if he is willing to chuck me another cap to try...and to let him know this has happened in case there is a correlation with something)
Will see what he says...he has got back to me on other queries after a few days
My guess is that not all mega's are equal and it /could/ vary - based on internal reference voltages etc...and I possibly got one that was a
"bit more off" than the 2v +/- adjustment available that TS allows...
I think I am pretty confident that it must have just been a bad cap that had a premature death...
A google search brought me to doing the firmware recompile as a workaround, so I am not the first that has needed to do that
(but was a bit surprised it was so far out)
Will do some more tuning when I get chance (need a dull overcast day) before posting anything to the speeduino site/facebook
Would be happier sharing the tune once I have run it through autotune a few times at least
Have decided I will try and add the extra wires to the DB37 that I will need for speeduino...that MS doesn't use - so swapping ECU's is
fairly trivial
(confident I have enough extra "spare" pins in there that are not connected or used in the MS unit)
1, 2, 27, 29 and 31 for VR+, VR-, Ign1, Ign2 and Tach out...
Will dig out the old MS board schematics and double check first
|
|
robocog
|
posted on 29/9/23 at 06:07 PM |
|
|
Just a theory (on why my cap may have gone pop...)
I was using USB /AND/ a lab power supply at the time
I wonder if that could have been a cause?
I had run it up this way quite a few times already (stimulator also supplies VCC) whilst playing with it on the bench and I didn't consider that
powering from USB and the VCC simultaneously may be an issue..mind you same issue when I was playing with it on the car ...
Do I need to make a special USB that does not supply power? (data only)
|
|
MikeR
|
posted on 29/9/23 at 06:38 PM |
|
|
Nope. It's happy with both. That is the norm. However, every time it detects power on USB it triggers a reset on the Arduino so it can(if needed)
update. If you have a cable or something to block post it means your can connect without causing a reset.
|
|
robocog
|
posted on 29/9/23 at 08:30 PM |
|
|
Bang goes that theory then....
Was hoping it may give a reason for the cap exploding and give me something to avoid for next time...
|
|
robocog
|
posted on 30/9/23 at 10:42 PM |
|
|
It lives...
A few hiccups along the way, but I drove it about for a good couple of hours today doing some tuning
Old mapping seemed OK on the driveway without load... but was obviously not perfect as soon as I hit the road..LOL
Had a few moments where it fell flat on its face from low revs, have got it so it doesn't do that (manually) and locked those bins out from
autotune...again it seems to be initial tip in from low RPM...it likes to run rich at idle and I have not really reflected that in the AFR bins, so
autotune kept leaning it out making the tip in issue worse
I think I have been a bit stingy with my AFR bins around cruise, so will richen them up a bit, so all the issues have been of my doing
Have got it to the point where it is pretty much usable and is perfectly happy with a hot start
(yet to see how it takes to a cold start)
Tuning not quite as refined as I had MS ...yet, but not bad for a couple of hours of playtime
Autotune has been pulling fuel out mainly, so am satisfied it should be OK to hit some of the higher RPM/load sites gradually
(was trying to hit a bin and hold it there, till it had worked its magic, then move to another bin..as well as just normal pootling along in
traffic)
Might get chance to try and hit a few more bins tomorrow with more autotune runs
(quiet dual carriageway run is on my list so I can perhaps hit some of the higher RPM sites)
Will keep prodding at it and post up a new msq on here when I am closer to being happy with it...
All in all - am dead happy I have gone this route
MS is still in the car and I have it so I only need to swap VR sensor and coil plug and a power wire and the vacc tubing and I can swap over the
ECU's
(just whilst I am experimenting)
|
|
MikeR
|
posted on 1/10/23 at 06:21 AM |
|
|
Fabulous news. This is great to hear.
If I'm correct, the tip in has had a few grumbles for not being great and their is a revision.. not sure if it's in the current firmware of
the next release.
|
|
robocog
|
posted on 4/10/23 at 02:20 PM |
|
|
Not heard back from diy-efi, so have just ordered 5x replacements from an online retailer (not that I have spotted any issues with running without C4
for now)
Did the timing today - printed a timing wheel, cut it out, laminated it, bluetacked to the front pulley, bent wire around a bolt as a pointer
Cam cover off to check the cams are right (and that I had the "right" TDC), dial gauge down the plug hole
I was miles out
Took my time and got it absolutely spot on for the ECU, did some autotuning...world of difference
Engine has never run so well
I have replaced that MSQ I shared earlier, as the trigger angle was NOT right
For my silvertop engine running a NO2C speeduino - the trigger angle is 287degrees
(but always check for yourself ;p)
[Edited on 4-10-2023 by robocog]
|
|