beaver34
|
posted on 19/12/14 at 05:35 PM |
|
|
soldering and flux
do people use flux when soldering?
if so what type, i seem to struggle with normal solder with flux in, used some paste stuff before and its made the job alot easier
only issue is i cannot remember what it was called so i can buy some
|
|
|
rash12
|
posted on 19/12/14 at 05:39 PM |
|
|
I use laco flux works for me but there are lots of makes
|
|
AndyW
|
posted on 19/12/14 at 06:25 PM |
|
|
I have always used fluxite and found it perfectly good
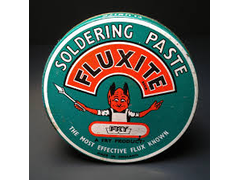 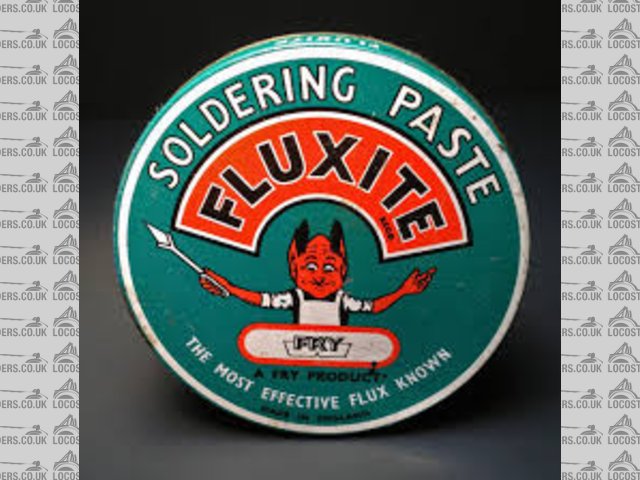 Description
|
|
bi22le
|
posted on 19/12/14 at 06:38 PM |
|
|
I use fluxed solder.
If the pcb pads and cables are clean it will work fine. Its a little more tricky if your doing big stuff as some irons cant pump the heat in enough so
the large wires soak all of the heat away. Is that your issue?
Also make sure you use a suitable sized nib for your iron.
If your talking about soldering copper pipes, i have no idea!!
Track days ARE the best thing since sliced bread, until I get a supercharger that is!
Please read my ring story:
http://www.locostbuilders.co.uk/forum/13/viewthread.php?tid=139152&page=1
Me doing a sub 56sec lap around Brands Indy. I need a geo set up! http://www.youtube.com/watch?v=EHksfvIGB3I
|
|
redturner
|
posted on 19/12/14 at 07:11 PM |
|
|
Fluxite for me but always had good results with Bakers Fluid..............
|
|
rusty nuts
|
posted on 19/12/14 at 07:21 PM |
|
|
Really depends on what you are soldering, for radiator repairs I always use Bakers , for wiring I use fluxes solder wire . As already suggest a decent
iron helps . Have a look at gas powered soldering irons for larger cables (or even a welding torch)
|
|
mark chandler
|
posted on 19/12/14 at 07:27 PM |
|
|
Flux centred solder is for electrical work, the stuff for copper pipes is a different mix, bakers flux for me.
[Edited on 19/12/14 by mark chandler]
|
|
BenB
|
posted on 19/12/14 at 07:28 PM |
|
|
Yes, very much depends on what you're soldering. For electrical stuff it's resin-cored ready-to-go stuff, for plumbing and car bits
(essentially plumbing) it's those tubs of yellow flux that all the DIY superstores sell- works perfectly for me....
|
|
big-vee-twin
|
posted on 19/12/14 at 09:42 PM |
|
|
Lead free solder is poo.
Duratec Engine is fitted, MS2 Extra V3 is assembled and tested, engine running, car now built. IVA passed 26/02/2016
http://www.triangleltd.com
|
|
beaver34
|
posted on 19/12/14 at 10:08 PM |
|
|
sorry its wiring looms for the kit, normally i carnt get the a good enough solder using flux corded stuff
ive got a couple of soldering irons too as i though one was just crap but i seems not to be the case
|
|
redturner
|
posted on 19/12/14 at 10:22 PM |
|
|
With any kind of soldering, cleanliness is next to Godliness, and the correct heat is essential. Tin the wires first, hold together then apply heat
and they should just fuse.....
|
|
Andi
|
posted on 19/12/14 at 10:24 PM |
|
|
quote: Originally posted by beaver34
sorry its wiring looms for the kit, normally i carnt get the a good enough solder using flux corded stuff
ive got a couple of soldering irons too as i though one was just crap but i seems not to be the case
Ditto...
Always been the same for me. Tried various irons/solder stations etc
Andi
|
|
threadbare wallet
|
posted on 20/12/14 at 08:39 AM |
|
|
As above get heat into the wires,most solder is fine but most use a much to small tip thinking they need precision.you need surface area to get heat
into the wire,tin them both before trying attach them,also if trying to do it in the garage(which i presume) the cold or wind will make a difference
at work when (i hand solder pcb boards alday) i have a fan pointing to close to my work it will cool the iron enough to effect things so keep this in
mind.
Hobby irons somtimes dont have the power either so look at the power rating of the iron and the condition of the tip(if replacable try a new one) also
cover the tip with a dap of solder as this helps transfer heat to the work.
Very few things are "really" needed.
|
|
907
|
posted on 20/12/14 at 09:41 AM |
|
|
quote: Originally posted by beaver34
sorry its wiring looms for the kit, normally i carnt get the a good enough solder using flux corded stuff
ive got a couple of soldering irons too as i though one was just crap but i seems not to be the case
Although I don't have trouble using flux cored lead solder if you have loads of connections to do then I would
advise investing in a set of crimp pliers and the terminals & heat shrink that go with them.
 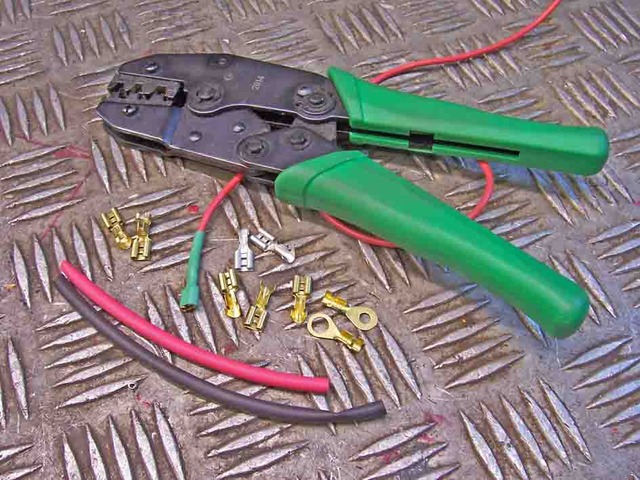 Description
If you must solder then what most people neglect is the irons copper tip.
Clean it with a file before you heat it / switch it on and tin it with flux & solder before you start to solder terminals.
hth
Paul G
|
|
beaver34
|
posted on 20/12/14 at 10:56 AM |
|
|
quote: Originally posted by 907
quote: Originally posted by beaver34
sorry its wiring looms for the kit, normally i carnt get the a good enough solder using flux corded stuff
ive got a couple of soldering irons too as i though one was just crap but i seems not to be the case
Although I don't have trouble using flux cored lead solder if you have loads of connections to do then I would
advise investing in a set of crimp pliers and the terminals & heat shrink that go with them.
 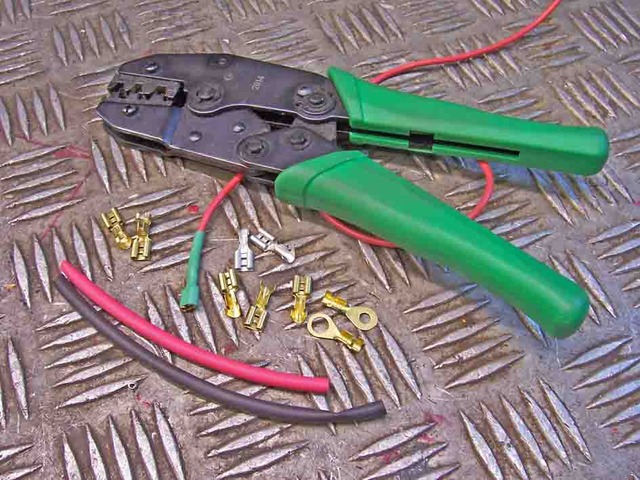 Description
If you must solder then what most people neglect is the irons copper tip.
Clean it with a file before you heat it / switch it on and tin it with flux & solder before you start to solder terminals.
hth
Paul G
thanks paul
ive done the main loom bits with crimps, this is for dash control buttons and other small switches that are fiddle small prongs on the back
|
|
02GF74
|
posted on 20/12/14 at 05:09 PM |
|
|
you trying to solder new or old wires?
the latter may be corroded or oxidised, like the ones in my land rover, splay the filaments out and run them over emery cloth to get a nice shine.
I find that dipping the wire in fluxite helps the folux cored solder flow.
Now I may be treaching you to suck eggs but the way i do it is a follows
- dip wires in fluxite
- put small blob of solder on tip of soldering iron
- place the wires to be soldered in the molten blob of solder
- wait a little bit for the wires to heat up
- introduce the cored solder onto the wires
- if needed run the soldring tip along the wires introducing the solder to the iron tip, it needs to have molten solder on it all the time as the
liquid metal is best for transfering heat
|
|
snowy2
|
posted on 21/12/14 at 09:52 AM |
|
|
if your struggling with the self fluxing solder your technique is no good, you apply a small bubble of solder to the iron to "tin " it...
the heated tip needs to be CLEAN wipe it on a rag the tip should be shiny, then apply the heat to the wire that needs soldering and apply the
soldering wire (the self fluxing type) to the wire and it should flow in to the joint.....easy peasy.
ps....do not heat the joint too much, if the solder forms a spike when you take the solder gun away, it was too hot for to long and the joint could
well be unreliable.
sometimes you are the pigeon, most of the time the statue.
|
|
designer
|
posted on 21/12/14 at 11:00 AM |
|
|
I would never solder anything on a loom. Quality rachet crimpers is the only way.
Soldered joins are unreliable, that's why they are banned for aircraft.
|
|
MikeRJ
|
posted on 21/12/14 at 12:56 PM |
|
|
quote: Originally posted by designer
I would never solder anything on a loom. Quality rachet crimpers is the only way.
Soldered joins are unreliable, that's why they are banned for aircraft.
Correct. Any application that requires high reliability, long life and is subject to vibration should use crimp connections for cable looms. Trains,
aircraft, spacecraft and any modern car will use crimped connections exclusively for cables.
Using aggressive fluxes designed for plumbing or sheet metalwork (e.g. fluxite) is an especially bad idea, the non activated flux that inevitably
remains within the wire and connector will cause corrosion.
|
|