bart
|
posted on 11/2/15 at 11:16 PM |
|
|
ps: also the moulding ( optimold ) resin goes off after 6 weeks so have to plan quite carefully so I don't waste loads of material
pps is it MOLD or MOULD seams to be spelt to ways depending where you look ?
BE ALERT > BRITAIN NEEDS LERTS
|
|
|
cloudy
|
posted on 12/2/15 at 09:35 AM |
|
|
Not sure about optimould - but easycomposites' Uni Mould (very similar) is good to go after 24 hours. It's an exotherm reaction that gets
mould temps over 50c that actually does the intial cure (after about an hour). I then post cure ramp up to 90c for epoxy infusion work..
James
www.warnercars.com
|
|
bart
|
posted on 12/2/15 at 10:32 AM |
|
|
re opti and uni mould
hi cloudy like you have done extensive research into both systems , it would appear its probably the same stuff with different labels on. ( expect
angry reply's ! )
the biggest problem seams to be getting all the styrene out after layup. force cure being the ultimate solution.
I spoke at length to the tech guy at east coast and he said that you don't have to use ie: 90 deg but if you half the temp you need to double or
triple the time , hence there web site saying leave at ambient for 2 weeks , this applies to there high temp styrene based resins for parts as well .
was considering making a big temp box oven from 100mm thick insulated roof board. and running it up to say 50-60 deg
for parts I may use epoxy resin in some instances due to the much higher heat property's ie side pods and rear panels
it would be wet lay , don't think I have the inclination to do pre preg but I could be talked into it
what due you use , epoxy , styrene based , pre preg ????
and do you use pva release or one of these more fancy chemicals
totally worried about these words that several people have said
"no matter what you do , you will get a mould that sticks to the buck and wont release , it happens to every one at least once"
BE ALERT > BRITAIN NEEDS LERTS
|
|
cloudy
|
posted on 12/2/15 at 11:43 AM |
|
|
18mm MDF box sized to your largest part, a PID temp controller & SSR relay kit from ebay £10, a £10 argos fan heater and lined with some foil
faced 20mm loft insulation boards will get you to 90c (the safety cutout on the fan heater prevents it getting much hotter) all in cost £60.
I use vacuum assisted resin infusion with epoxy resins (carbon/kevlar fibres) The infusion process is quite capable of better parts than prepeg and
much cheaper materials.
PVA + chemical release on all moulds (chemical can let you down on less than perfect surfaces) With PVA if the mould sticks, just get enough of a gap
to get a water supply in there, 30mins of soaking will get pretty much anything off a buck assuming you haven't miscalculated your draft
angles
If you want to do any epoxy you'll need to post cure your moulds - In my experience an ambient cure isn't sufficient no matter how long
you leave it.
Check out the easycomposites video tutorials - they're pretty good
James
www.warnercars.com
|
|
bart
|
posted on 12/2/15 at 11:58 AM |
|
|
thanks cloudy
BE ALERT > BRITAIN NEEDS LERTS
|
|
tegwin
|
posted on 12/2/15 at 02:20 PM |
|
|
If cnc machining is out of the question due to cost have you thought about slicing your solid model into 10mm sections and having them all
routed/waterjet cut out of a suitable foam... A lot lower tech so should not cost silly money... stick them together and then sand/fill etc to the
finished size?
[Edited on 12/2/15 by tegwin]
------------------------------------------------------------------------------------------------------------------------
Would the last person who leaves the country please switch off the lights and close the door!
www.verticalhorizonsmedia.tv
|
|
Fred W B
|
posted on 12/2/15 at 04:31 PM |
|
|
Hi Bart
I don't know if you have seen my log already
here
but if not you might find some of my experience usefull
Cheers
Fred W B
You can do it quickly. You can do it cheap. You can do it right. – Pick any two.
|
|
bart
|
posted on 20/2/15 at 02:53 PM |
|
|
some slow progress, but progress none the less
hi all
have not posted for a while , been very busy paying the bills.
managed to get several hours late last night designing the front buck for fibre glass fixture ( 2:30 am finish ! )
its not quite finished but close
hope to do the back over the weekend
 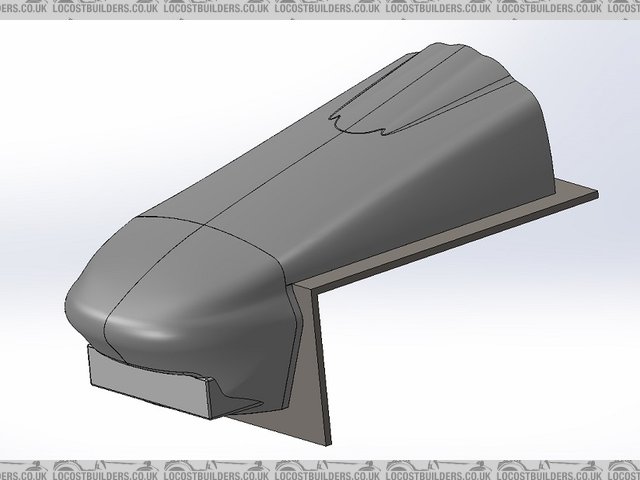 Description
 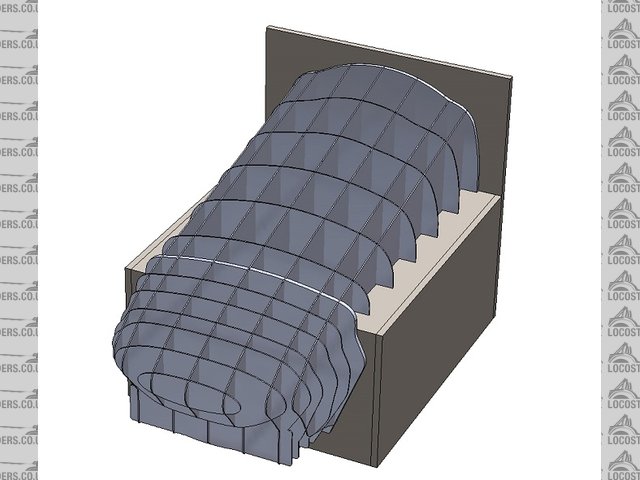 Description
BE ALERT > BRITAIN NEEDS LERTS
|
|
cloudy
|
posted on 20/2/15 at 06:37 PM |
|
|
Nice - lots of cut with surface? Are you going to "jigsaw" the formers to slot together?
[Edited on 20/2/15 by cloudy]
www.warnercars.com
|
|
bart
|
posted on 20/2/15 at 07:29 PM |
|
|
hi cloudy
yep going to use 3mm Foamex sign board , 2 ways to proceed
1) get the parts printed out on A0 paper and the stick down and cut out with model knife
2) get the parts cnc routed ( I would like to do this but need to get quote first )
as for slotting yes it all needs slotting was going to sit here tonight and try figure the best way to slot it all together.
its a bit of a problem as the model is top and bottom if that makes sense , still nothing a big brew , and a penguin wont solve !
( I bet that has the non uk visitors guessing what how a "penguin" helps ) ( and what a big brew is ) .
miss bart ( no not lisa ,that would be incest ! ) is watching happy enders so that gives me some free time .
[Edited on 20/2/15 by bart]
BE ALERT > BRITAIN NEEDS LERTS
|
|
bart
|
posted on 25/2/15 at 02:48 AM |
|
|
rear foam skeleton
HI all
still busy in work so brew / penguin and another very late night early morning
made a good start at the rear foam mould
should finish tomorrow night.
decided to plot the drawing out and cut the foam by hand
just brought a terrific bargain off eBay 3 year old hp 510 plotter for £310 with little use ( was listed in the wrong place ! )
says its working we will see when I pic it up
I needed one for work anyway , so two birds with one stone
 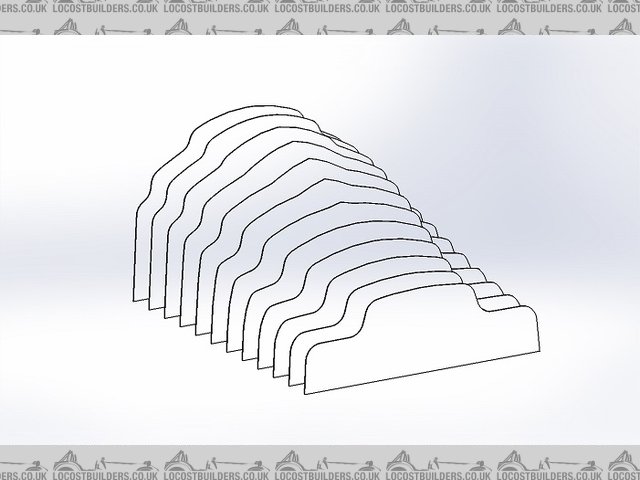 Description
BE ALERT > BRITAIN NEEDS LERTS
|
|
bart
|
posted on 25/2/15 at 07:22 PM |
|
|
new plotter arrived
hi all
went to Chester today to pick up my new 42" plotter
well well well pleased ,what a barging , got £150 of new cartridges with it , there's not a scratch on it looks like new.
first true bargain I have had of flea bay.
ps: it enormous the wife is so pleased that its in the dinning room / office.
can do up to 42" wide by any length you want , so I can print out all the foam former parts to scale to cut out.
ordered some rolls of paper for tomorrow , tried A3 the biggest I had and it works a treat
 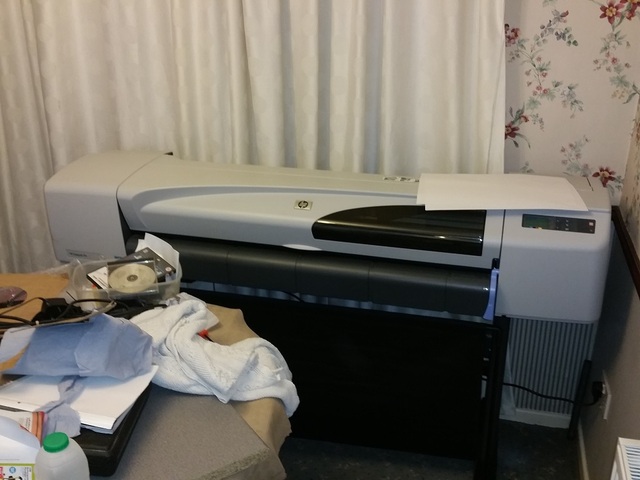 Description
    
BE ALERT > BRITAIN NEEDS LERTS
|
|
cloudy
|
posted on 25/2/15 at 08:56 PM |
|
|
result
www.warnercars.com
|
|
bart
|
posted on 26/2/15 at 12:02 AM |
|
|
lots of slots , and more slots , and more slots
hi again all
finished playing with my new toy back to design !
finished the rear top part
just the rear lower panel to do
then I have to out put all the files so I can print them out
I will order the foam tomorrow and some spray mount glue recon I need 4 off 8*4ft sheets
not cheap but I recon safer than working with mdf especially with all the sanding .
posting all the detail pics so people can see how I am attempting to complete my build , I'm sure its not the only way but that's the way
I have chosen.
 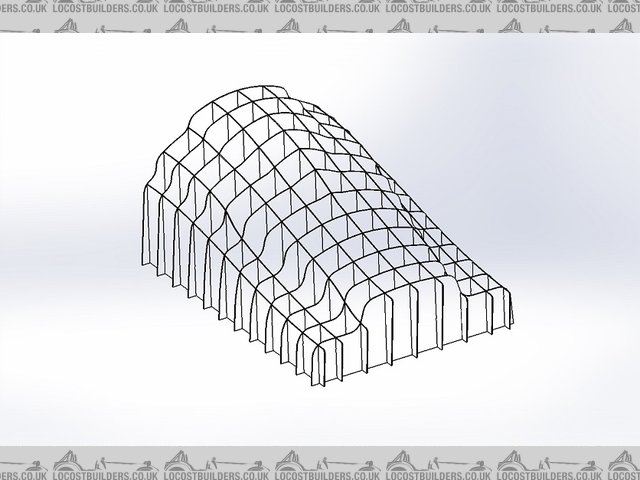 Description
 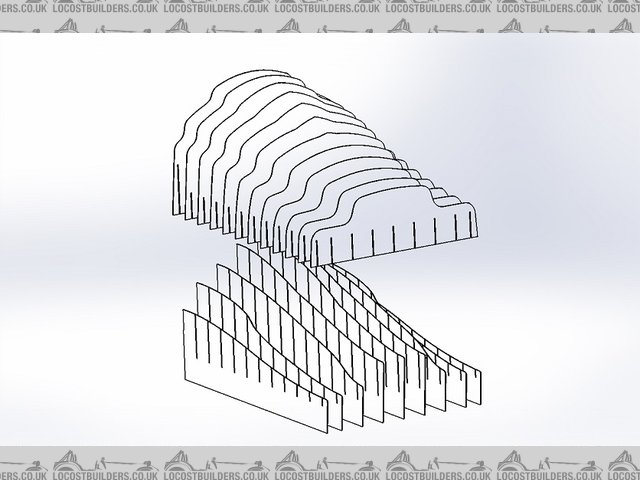 Description
BE ALERT > BRITAIN NEEDS LERTS
|
|
bart
|
posted on 2/3/15 at 10:05 PM |
|
|
mould materials arrive
hi all some progress
went to Preston today to pick up some polyurethane roof insulation
got a whole Citroen Picasso full ( with all seats out ) could not have got a mouse in extra !
cost me £60 cash , worked out the same amount from some of the glass fibre places would have been £400
did some trials last week works a treat , easy to sand ,light weight , resin proof ,
also the pvc sheets arrived for the skeleton.
got most of the formers printed out , some more to do and I need to get some mdf for base's.
lots of work to do but getting there. slowly
 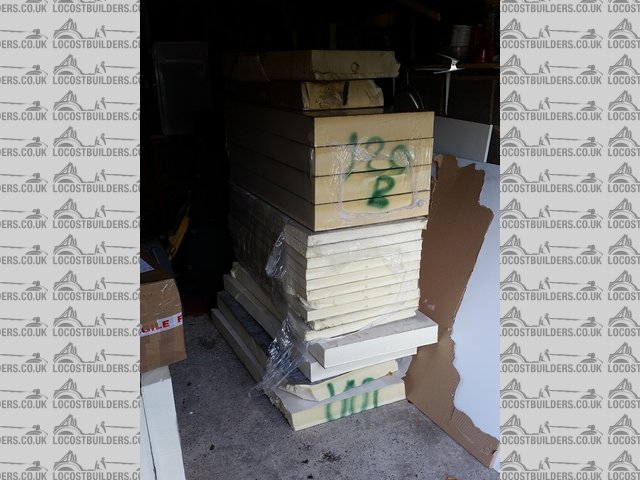 Description
 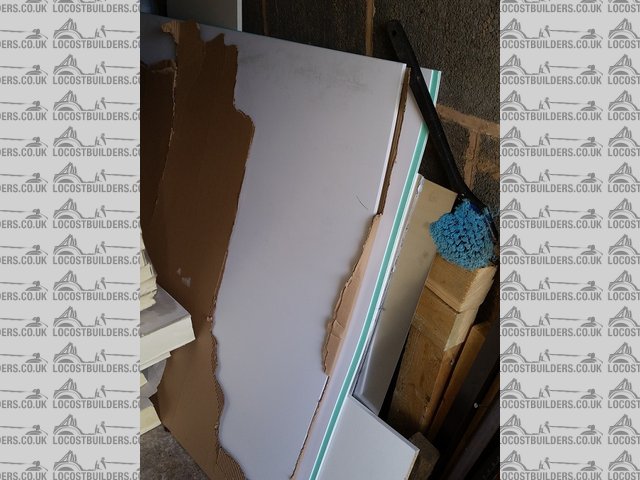 Description
BE ALERT > BRITAIN NEEDS LERTS
|
|
bart
|
posted on 7/3/15 at 09:13 PM |
|
|
body work progress
hi all body work progress
1) finished design of rear and front body work
2) printed out full scale templates on my new plotter
3) stuck the templates to Foamex plastic sheet
4) cut the mould buck formers out with a Stanley knife ( on the lounge floor ! )
5) made the mdf support structure
6) assembled and glued the formers to the support structure
hard work but progress
random selection of pics during build
inserting foam starts tomorrow
 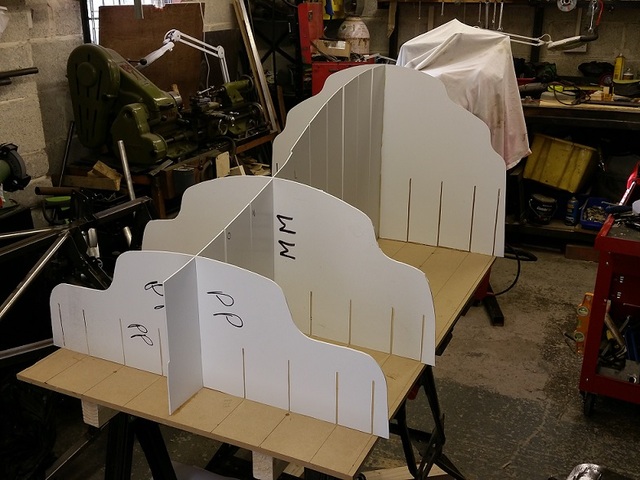 Description
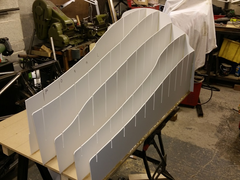 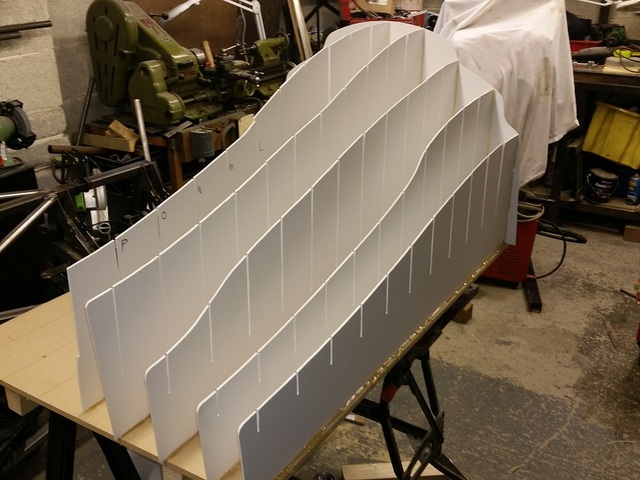 Description
 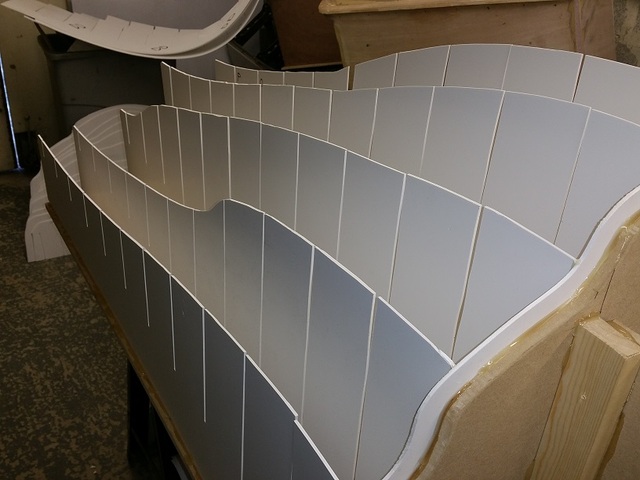 Description
 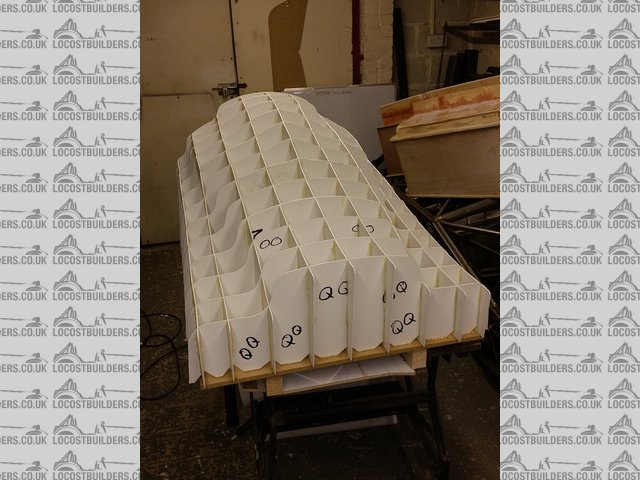 Description
 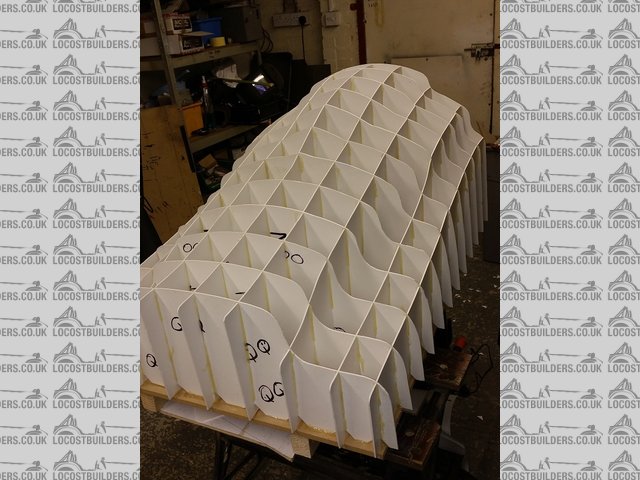 Description
 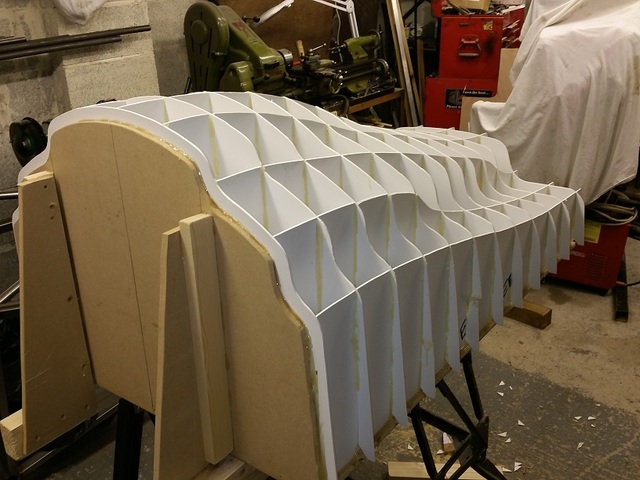 Description
ps: hot glue does a very good job of removing finger prints and any other skin !!!!
[Edited on 7/3/15 by bart]
BE ALERT > BRITAIN NEEDS LERTS
|
|
bart
|
posted on 7/3/15 at 09:20 PM |
|
|
further information
the skeleton is surprisingly rigid and strong , and will improve when I put the foam in tomorrow .
its hard work but far cheaper than cnc milling , will just have to see what results I get .
next week if I get time ill sand it down to shape and also I have to design the wheel arches and rear suspension covers.
will have to see if I can get the time in-between work .
BE ALERT > BRITAIN NEEDS LERTS
|
|
bart
|
posted on 8/3/15 at 10:15 PM |
|
|
update of foaming
this is going to take ages !
5 hours to do about 20% of the foam infill's
and using hot glue sticks at an alarming and costly rate
well I have started so I suppose ill have to finish
next job tonight order more glue sticks
 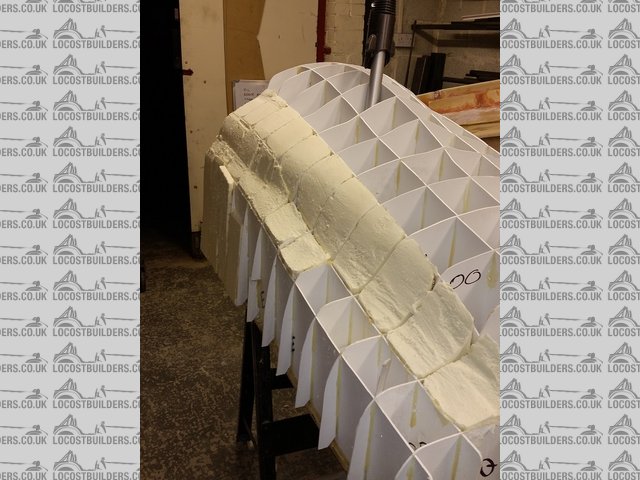 Description
BE ALERT > BRITAIN NEEDS LERTS
|
|
bart
|
posted on 10/3/15 at 10:19 PM |
|
|
cant believe how long this takes 40% done
 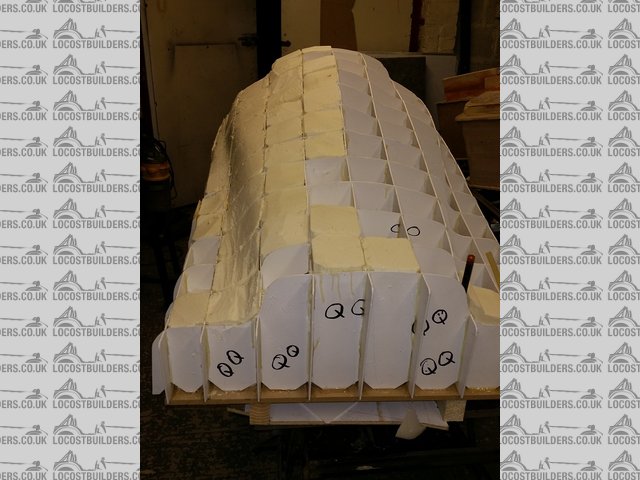 Description
BE ALERT > BRITAIN NEEDS LERTS
|
|
Rosco86
|
posted on 10/3/15 at 10:29 PM |
|
|
Coming on nicely mate
|
|
Fred W B
|
posted on 11/3/15 at 11:34 AM |
|
|
Coming on.. If you think that takes along time just wait untill you get to the surfacing
I cheated and had my blocks cut by a foam supplier.
Get all the foam in before you try to shape it. Try creep up to the profile by sanding the foam rather than cutting chunks off. It looks like you
already a bit low in some places. To do the negative curves maks some sanding blocks out of round wood stock or something
Cheers
Fred W B
[Edited on 11/3/15 by Fred W B]
[Edited on 11/3/15 by Fred W B]
[Edited on 11/3/15 by Fred W B]
You can do it quickly. You can do it cheap. You can do it right. – Pick any two.
|
|
bart
|
posted on 16/3/15 at 06:49 PM |
|
|
body rear update
hi all
hard work , boring , hard work , boring , body work oh body work
starting to make progress with the rear engine cover
all foamed up and starting to sand to shape
and YES I know some of the parts are below where they should be , well spotted !
" that's what body filler is for LOL"
been a bit over enthusiastic in some places .
problem's to report for those thinking of doing something similar.
1) don't get hot melt glue on the outside faces , cant be sanded
2) try to avoid negative radii especially with compound curves
3) take your time don't rush like I did !
4) if I did this again ( which I wont !) then I would pay the extra and get it cnc machines , will work out cheaper in the long run.
5) top tip . if possible get someone else to do it !!!
 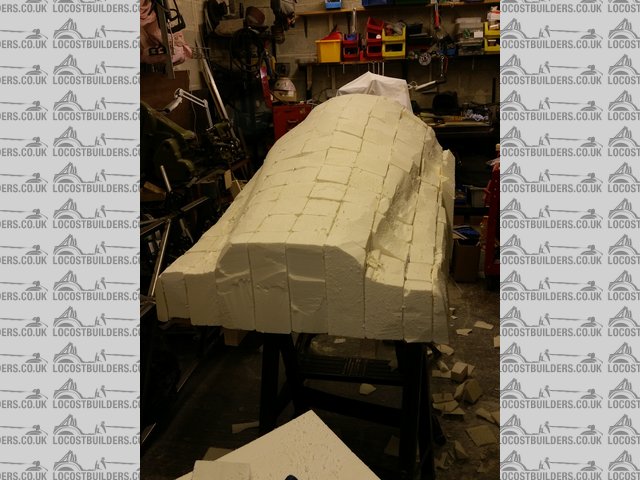 Description
 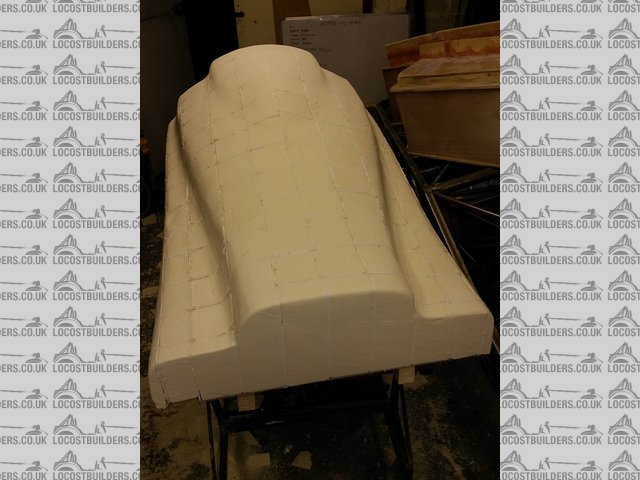 Description
all comment's taken , and read , with a smile
BE ALERT > BRITAIN NEEDS LERTS
|
|
bart
|
posted on 24/3/15 at 11:59 PM |
|
|
getting there slowly due to cold weather and work load
bit more body filler and sanding to go
 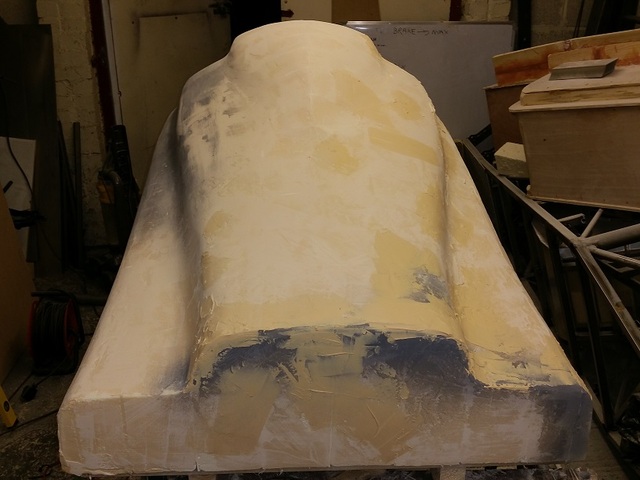 Description
BE ALERT > BRITAIN NEEDS LERTS
|
|
ceebmoj
|
posted on 25/3/15 at 07:36 AM |
|
|
Coming along nicely.
|
|
wylliezx9r
|
posted on 25/3/15 at 10:33 AM |
|
|
Good work - keep going
I spent a lot of money on booze, birds and fast cars. The rest I just squandered.
George Best
|
|