cloudy
|
posted on 6/1/08 at 06:10 PM |
|
|
All made in 3D studio max - I still can't get my head around solidworks!
|
|
|
Benonymous
|
posted on 7/1/08 at 01:08 AM |
|
|
Solidworks
I'm trained in 3D Studio Max and I found Solidworks quite easy to use. The big difference with SW is that you have to be much more deliberate
in how you do things. Another snag is that Max is designed to let you make absolutely anything whereas SW is an engineering program. When I
was designing my chassis I found that it wouldn't put a weldment profile on a spline. It only wanted to play with arcs so I made my tube an arc
and worked with a regular shape rather than a custom one. Another downside is the rendering in SW. I don't have the 'Photoworks'
package so I'm limited to screen captures as far as I can tell. After using Max and Mental Ray, it's a real let-down! I'm still
learning SW and I no longer use Max but if you can learn Max you can easily learn SW. Hard to put down the familiar tools though 
|
|
Alan B
|
posted on 7/1/08 at 02:10 AM |
|
|
I guess the difference is that 3DS max will let make anything on the screen...whereas the parts in SW you can make in real life (for the most
part)...
How would you detail an extrusion extruded along a spline?...how do you do any detail drawings from 3ds max?...I don't think you can (can you?)
because it is just a visualisation program...as opposed to (as you say) an engineering design tool...
|
|
cloudy
|
posted on 7/1/08 at 12:10 PM |
|
|
I've just assumed the units in 3dmax are millimeters, so I can design to scale. I do have to read off all my dimensions on the fly as I
can't get a good printout, but I just take a laptop outside with me
James
[Edited on 7/1/08 by cloudy]
[Edited on 8/1/08 by cloudy]
|
|
Alan B
|
posted on 7/1/08 at 12:54 PM |
|
|
quote: Originally posted by cloudy
I've just assuming the units in 3dmax are millimeters, so I can design to scale. I do have to read of all my dimensions on the fly as I
can't get a good printout, but I just take a laptop outside with me
James
[Edited on 7/1/08 by cloudy]
Whatever works for you mate..  
Splendid job so far...keep up the good work..
|
|
Benonymous
|
posted on 8/1/08 at 06:13 AM |
|
|
Max vs SW
quote: Originally posted by Alan B
I guess the difference is that 3DS max will let make anything on the screen...whereas the parts in SW you can make in real life (for the most
part)...
How would you detail an extrusion extruded along a spline?...how do you do any detail drawings from 3ds max?...I don't think you can (can you?)
because it is just a visualisation program...as opposed to (as you say) an engineering design tool...
Yes, for me Max is about making fantastic models and animating them. Solidworks forces you to make a proper job of the model and as you say, the
parts made can be birthed into the real world via the magic of CAM and laser cutters (joy!) I always found it nearly impossible to stick to doing
things accurately, it was easier to do them for maximum visual appeal.
SW and Max aren't comparable products in many ways but you can output .DXF files from Max so if you did everything properly I can see no reason
why you couldn't use it to have parts made with CAM processes.
BTW James, I'm very impressed with your design and your progress. So many inspirational people on this forum 
|
|
Gakes
|
posted on 11/1/08 at 05:56 PM |
|
|
Amazing work dude 
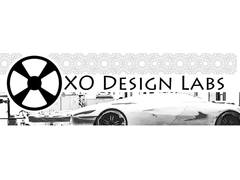 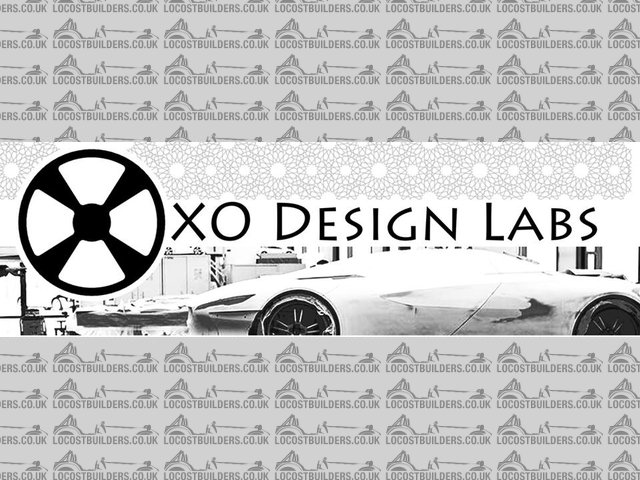 Description
|
|
cloudy
|
posted on 12/1/08 at 05:01 PM |
|
|
Small update, I've turned up my chain tension adjusters and test fitted the chain:

|
|
nitram38
|
posted on 13/1/08 at 06:20 AM |
|
|
My only suggestion for your chain adjusters is that I recommend some top guides for your diff carrier.
From your 3D drawing there is nothing stopping side loads pushing the diff brackets over at the top.
Remember that as your driveshafts are moved up and down, there is a chance that thse will put side loads on your diff carrier.
This is not to criticise your work, but to stop any problems.
|
|
cloudy
|
posted on 13/1/08 at 11:30 AM |
|
|
Good spot - thats something I have thought about but haven't yet designed, I think I'll do it once the adjusters are in...
James
|
|
cloudy
|
posted on 13/1/08 at 08:47 PM |
|
|
Remade the diff plates in ally, with an offset to allow a chassis tube between it and the engine. I also made up some temporary driveshafts from my
sierra ones to get the lengths right....

|
|
nitram38
|
posted on 14/1/08 at 05:45 AM |
|
|
Just got to say, that it looks the Dog's Cahoonas !!!! 
|
|
Benonymous
|
posted on 14/1/08 at 10:52 AM |
|
|
Bending
Hey Cloudy, sorry if I missed it but how did you bend the main tubes for your frame. I have considered CNC bending but I'm aware that I may
suffer from 'sticker shock' after asking the price. If you have used a lower tech method I'd be interested.
Cheers.
Ben.
|
|
cloudy
|
posted on 14/1/08 at 11:55 AM |
|
|
I built myself a tube roller from parts I had lying around see here:
http://www.locostbuilders.co.uk/viewthread.php?tid=54042&page=20&contribmessage=none
It can't bend the tube much tighter than I have for the side tubes, as the tube starts to oval....
James
[Edited on 14/1/08 by cloudy]
|
|
cloudy
|
posted on 20/1/08 at 05:15 PM |
|
|
Span the engine up tonight to check everything so far, here's a little video
Video
Ignore the wobbly driveshafts they are just temporary cut and shuts till I'm happy with the lengths...
[Edited on 20/1/08 by cloudy]
|
|
clanger
|
posted on 23/1/08 at 06:54 PM |
|
|
Hi James,
Project looking cool as ever.
Quickie question:
Rear suspension pick points, they based on the book chassis or your own design ?
What tube & wall thickness are you using for the diff mounting / rear suspension monuting.
keep up the good work !
cheers
|
|
cloudy
|
posted on 23/1/08 at 08:06 PM |
|
|
They are of own design but will inevitably sit fairly close to the book dimensions as it's an MNR rear wishbone setup
James
|
|
neilj37
|
posted on 24/1/08 at 08:05 AM |
|
|
This project is looking really good. I just wish you would hurry up and finish so you can make me one.
Did you ditch the cross over roll bar idea al la MK?
BTW can you make mine a single seater with the seat in the middle of the car
[Edited on 24/1/08 by neilj37]
|
|
COREdevelopments
|
posted on 24/1/08 at 06:29 PM |
|
|
ye this project is amazing! cant wait to see it finished. put me down for one too!!
Rob
|
|
defcon
|
posted on 27/1/08 at 11:18 AM |
|
|
Im amazed by your tube rolling device. Can you tell me the wall thickness you are able to roll?
|
|
cloudy
|
posted on 28/1/08 at 12:59 AM |
|
|
I've only tested it up to 3mm wall tubing, I suspect thats close to it's limit as the screwjack becomes very hard to turn!
Does anyone know a supplier for the foam commonly used for hand shaping moulds intended for glass fibre layup?
I'm going to take a crack at building a CF/GRP composite bonnet!
James
[Edited on 28/1/08 by cloudy]
|
|
Delinquent
|
posted on 28/1/08 at 08:55 AM |
|
|
I go to local building insulation companies (if you have a Sheffield Insulation near you give them a try)
|
|
cloudy
|
posted on 28/1/08 at 10:27 AM |
|
|
Thanks any idea what they call it?
James
|
|
Delinquent
|
posted on 28/1/08 at 11:47 AM |
|
|
Insulation foam
Comes in a variety of densities and block shapes, have a look at Fred's thread re his bodywork, he mentions his preferred density in there
somewhere and I think he'd have a better idea on what's good for a project of this size. I've always just gone for the highest
density offcuts they have as my mouldings have always been relatively small.
|
|
nitram38
|
posted on 28/1/08 at 01:06 PM |
|
|
Just make sure that you go for a non-styrene based foam, otherwise it will melt when you put styrene based filler/fibreglass.
Polyester does not react with styrene, so go for polyester foam or similar
|
|