JC
|
posted on 23/2/06 at 09:44 PM |
|
|
Opinions on welding
Wasn't sure where to put this post! Made a rear wishbone for my midi tonight. some welding went really well, other bits less neat - as shown
here. Penetration appeared good. Any clues to what is happening? Cheers!
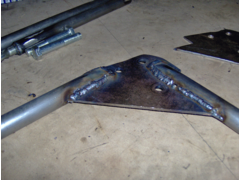 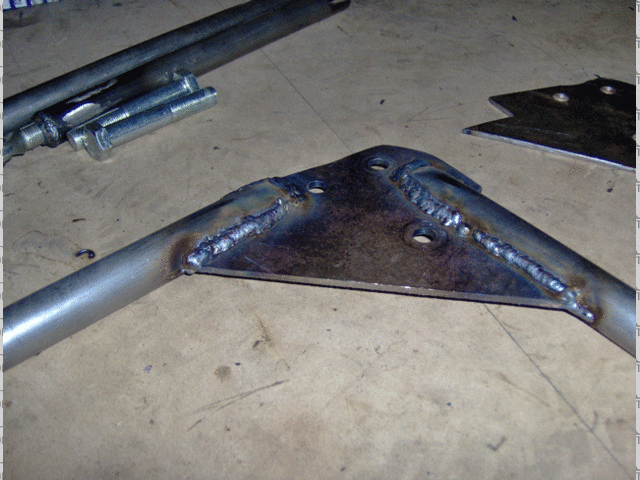 Rescued attachment HPIM0235.gif
|
|
|
flak monkey
|
posted on 23/2/06 at 09:46 PM |
|
|
Too fast, not enough amps or an unsteady hand, possibly a combination of all 3.
Do some more practice on some scrap if I was you...IMO
David
Sera
http://www.motosera.com
|
|
JoelP
|
posted on 23/2/06 at 09:50 PM |
|
|
looks similar to some of my welding. More amps is often the solution, i have trouble setting current on my welder due to a lack of finesse in the
machine (i know, a poor workman who blames his tools ).
there are several professional welders on the forum, one will soon come along with full details and tips 
|
|
mark chandler
|
posted on 23/2/06 at 10:03 PM |
|
|
Less wire speed, it looks like you afraid of burning holes in the thinner tube and hurrying, which equates to lots of weld on top of the job.
Try and work the molten pool from the thicker plate across, slow down and weave the torch more evenly.
Its just practice. burning a hole merely indicates full penetration !
|
|
Jon Ison
|
posted on 23/2/06 at 10:10 PM |
|
|
I'm left handed so if your right handed try the opposite, I hold the gun in my left hand and steady it by resting it on my right hand bit like a
sign writer would do, make any sense ? I find it much easier too "weave" the torch like this.
|
|
emsfactory
|
posted on 23/2/06 at 10:42 PM |
|
|
More amps less feed speed.
|
|
Gav
|
posted on 23/2/06 at 10:47 PM |
|
|
Ill second (or third? ) the too much wire speed opinion.
id try just going a little slower with less wire rather than adjusting wire and ampage at the same time, just try changing one at a time that way
youll get a better feel for how the two settings interact and in the end you'll be able to feel exactly setting is which is to high or too low.
|
|
Wadders
|
posted on 23/2/06 at 10:54 PM |
|
|
You wont be on your own Joel, many hobby type welders are almost impossible to coax a decent weld out of, erratic arc being a big problem, even with a
pro holding the torch, for once you can blame the tool.
Originally posted by JoelP
looks similar to some of my welding. More amps is often the solution, i have trouble setting current on my welder due to a lack of finesse in the
machine (i know, a poor workman who blames his tools ).
there are several professional welders on the forum, one will soon come along with full details and tips
|
|
NS Dev
|
posted on 23/2/06 at 11:18 PM |
|
|
Yep yep yep yep and yep!
all good advice so far!
Wadders you are dead right, that's why my Clarke 150 TE went and the big machine that I have now got bought.
Slow it all down. Practice on some scrap and just keep trying to go slower and slower until you're welding takes perhaps 7 or 8 secs per inch
(as a guesstimate)
This is very slow for mig, but when you have perfected a setup that will give a smooth weld at that slow rate, it's dead easy to speed the wire
up and knock the amps up a setting then to speed things up.
As everybody else said, you have too much wire and not enough heat to melt it at the moment.
Keep welding scrap until you can get it right consistently with all types of weld (corner fillet, butt weld etc) as welding round tube to things
neatly is not the easiest task (as uncle Ron showed with some of the pics in "the book"!! )
I (trumpet out!) am a pretty accomplished welder, but I will never start a weld on something I am making until I have verified the setup of the welder
on a piece of scrap first, so don't think you're the only one who needs to! It's just good practice.
Lastly, with a lot of hobby machines you will find that they spend most of their time on one setting. My Clarke 150 amp used to spend nearly all
it's time on setting 5 (actually "2-High" ) which was 1 setting down from full power. I used this on everything from 1mm through to
2.5mm, which was most of what I welded at the time (still is probably) and just varied the torch speed and wire feed to adjust the weld.
Keep practising, that's the key!
[Edited on 23/2/06 by NS Dev]
Retro RWD is the way forward...........automotive fabrication, car restoration, sheetmetal work, engine conversion
retro car restoration and tuning
|
|
clbarclay
|
posted on 23/2/06 at 11:30 PM |
|
|
quote: Originally posted by Wadders
You wont be on your own Joel, many hobby type welders are almost impossible to coax a decent weld out of, erratic arc being a big problem, even with a
pro holding the torch, for once you can blame the tool.
Originally posted by JoelP
looks similar to some of my welding. More amps is often the solution, i have trouble setting current on my welder due to a lack of finesse in the
machine (i know, a poor workman who blames his tools ).
there are several professional welders on the forum, one will soon come along with full details and tips
A good workman would still not blame the tool, they would just do like NS Dev and get the right/better tool instead.
Unfortunatelt financeal constraints mean i'm stuck being a bad workman most of the time.
To get a bad/inapropriate tool to work better I find cursing it a time or 2 (3, 4, 5, ....) helps.
Fortunatly my workshop is a good distance from our house and any neighbours.
[Edited on 23/2/06 by clbarclay]
|
|
Wadders
|
posted on 23/2/06 at 11:39 PM |
|
|
But thats the point i was trying to emphasize. Most people on here wont be "good workmen'"when it comes to welding, they are only
novice learners, and as such will blame themselves if the results are poor, never suspecting the machine they are using is pants and that even a pro
would struggle to lay down a nice weld with it.
A good workman would still not blame the tool, they would just do like NS Dev and get the right/better tool instead. [/quot
|
|
NS Dev
|
posted on 23/2/06 at 11:50 PM |
|
|
Very true. It was only working in a prototype fabrication shop for a while with "proper tools" that put my hobby stuff in perspective.
Retro RWD is the way forward...........automotive fabrication, car restoration, sheetmetal work, engine conversion
retro car restoration and tuning
|
|
Peteff
|
posted on 24/2/06 at 12:27 AM |
|
|
Are you working towards yourself or away. Turn the power up and push the gun away from you.
yours, Pete
I went into the RSPCA office the other day. It was so small you could hardly swing a cat in there.
|
|
Kodiak
|
posted on 24/2/06 at 03:52 AM |
|
|
Not enough heat (amps), too fast on the wire...would suspect that the penetration is not too good from the shape of the bead.
|
|
Marcus
|
posted on 24/2/06 at 09:23 AM |
|
|
I'm laft handed like Jon and am a two handed welder. Makes those hand held masks a waste of time. I'd reccommend an auto darkening mask,
helps you start in the right place. It took me ages to 'see' the weld pool, thought it was just something gas people talked about, turned
out I was moving too fast. Slow right down look for the melt pool (darker ring around weld) and move this along the workpiece. I've never had
better welds!!
Marcus
Marcus
Because kits are for girls!!
|
|
JonBowden
|
posted on 24/2/06 at 10:48 AM |
|
|
A cheap MIG I used many years ago tended to overheat after a few inches of weld. I couldn't get it to work properly until it cooled down. When
overheated, the power dropped and the wire feed speed became eratic.
This made learning to weld very dificult - I kept blaming myself for the weld quality - I could produce two or three inches of nice weld - then bird
droppings.
Jon
|
|
NS Dev
|
posted on 24/2/06 at 12:25 PM |
|
|
quote: Originally posted by Marcus
I'm laft handed like Jon and am a two handed welder. Makes those hand held masks a waste of time. I'd reccommend an auto darkening mask,
helps you start in the right place. It took me ages to 'see' the weld pool, thought it was just something gas people talked about, turned
out I was moving too fast. Slow right down look for the melt pool (darker ring around weld) and move this along the workpiece. I've never had
better welds!!
Marcus
dead right, meant to mention that you always really need two hands when mig welding. I'm right handed so right hand does the trigger and left
guides the shroud.
With me it doesn't help that I shake like I have permanent DT's so two hands are a necessity.
head mounted mask as a minimum, automatic very preferable (tho mine has just broken so I'm back to basics at the mo!)
[Edited on 24/2/06 by NS Dev]
Retro RWD is the way forward...........automotive fabrication, car restoration, sheetmetal work, engine conversion
retro car restoration and tuning
|
|
Peteff
|
posted on 24/2/06 at 02:06 PM |
|
|
I use a hand held mask while I tack stuff up, then I use my head mask with the "nod" facility (slacken the screws off). I fitted a sponge
bung where it drops down so it hits my chin and doesn't go too far, the wonders of gaffer tape technology
yours, Pete
I went into the RSPCA office the other day. It was so small you could hardly swing a cat in there.
|
|
JB
|
posted on 24/2/06 at 04:45 PM |
|
|
One way of getting a farily good weld without a lot of practice is to do lots of short runs.
Turn the power right up then cut the blob off the end of the wire, position your torch and wire end, holding the torch and supporting the nozzle with
your fingers. This ensures a steady hand, do not try to weld in mid air.
Now just do a short squirt of weld. The high power will ensure good penetration and the short squirt ensure you do not burn through. Just do a lot of
these short bursts moving the torch and cutting off the blob each time.
When you get better you can make each run slightly longer.
Top welding machines have a pulse facility which basically does the above for you as you weld. It means you can run high power with time between for
the weld to cool.
John
|
|
JC
|
posted on 24/2/06 at 08:03 PM |
|
|
Thanks guys. The frustrating part is that practise welds on scrap were going well - guess I've made another piece of interesting shaped
sculpture (sell on e-bay??!!).
I'll try again, slower, steadier, more current, less wire. Watch for results next week!!!! 
|
|
Wadders
|
posted on 24/2/06 at 08:10 PM |
|
|
theres nothing to stop you grinding it back, and welding over the top once you've perfected your technique. shame to scrap the whole thing.
Originally posted by JC
Thanks guys. The frustrating part is that practise welds on scrap were going well - guess I've made another piece of interesting shaped
sculpture (sell on e-bay??!!).
I'll try again, slower, steadier, more current, less wire. Watch for results next week!!!!
|
|
Stu16v
|
posted on 24/2/06 at 09:30 PM |
|
|
Another thing that hasnt been mentioned (but I have only skimmed throught the thread...) is it is worth 'shining up' the metal in the
general weld area first, as well as the earthing point. The metal may *look* clean, but a quick rub with some emery cloth etc will make quite a
difference, especially with a hobby MIG...
Dont just build it.....make it!
|
|
mggareth
|
posted on 24/2/06 at 11:46 PM |
|
|
Hi i would guess your using co2 try using Argon / argo shield (argon oxygen mix)
It makes a big difference
Gareth
|
|
NS Dev
|
posted on 25/2/06 at 02:07 AM |
|
|
Yes (agreed as we used to use argoshield in the fab shop) but I only use crappy CO2 "at home" and get results easily as good as with
Argoshield, except I seem to get more spatter with C02. Anti-spatter spray is cheap tho!!!
Retro RWD is the way forward...........automotive fabrication, car restoration, sheetmetal work, engine conversion
retro car restoration and tuning
|
|
NS Dev
|
posted on 25/2/06 at 02:09 AM |
|
|
quote: Originally posted by JC
Thanks guys. The frustrating part is that practise welds on scrap were going well - guess I've made another piece of interesting shaped
sculpture (sell on e-bay??!!).
I'll try again, slower, steadier, more current, less wire. Watch for results next week!!!!
no probs, just remember up with the amps, down with the wire and loadsa practice!!
cheers
Nat
(cripes theres 2 of me drifteing a car roond a bend there, goodness me I need to work on me driving and fast god forune to have wheels i.e. 4 of them
now, so I can sprk the damn machine up and give her a damn tharshing)
[Edited on 25/2/06 by NS Dev]
Retro RWD is the way forward...........automotive fabrication, car restoration, sheetmetal work, engine conversion
retro car restoration and tuning
|
|