JoelP
|
posted on 30/1/06 at 08:06 PM |
|
|
my wheel problems
im having trouble getting the wheels onto my trailer. Having finally got one centrebore ground up so the wheel fits, my studs are now at least 4
threads too short for the nuts. Can anyone tell from the picture if i can change them for longer ones?
As an aside, theres a picture of the wheel and the bit out of the die grinder - an awesome sharp bit i got today. It wipes the floor with the stone
type bits that came with the tool.
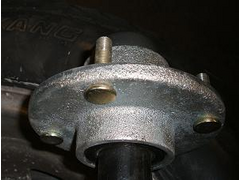 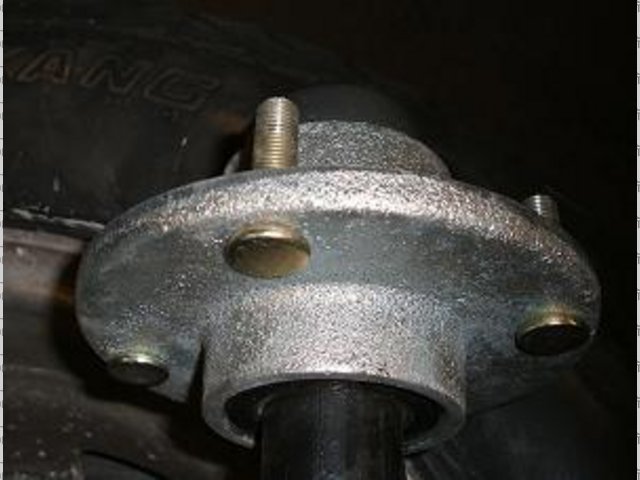 Rescued attachment suspension1.JPG
|
|
|
JoelP
|
posted on 30/1/06 at 08:07 PM |
|
|
the alloy, complete with a notch for the grease nipple to sit in.
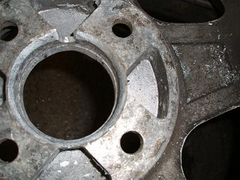 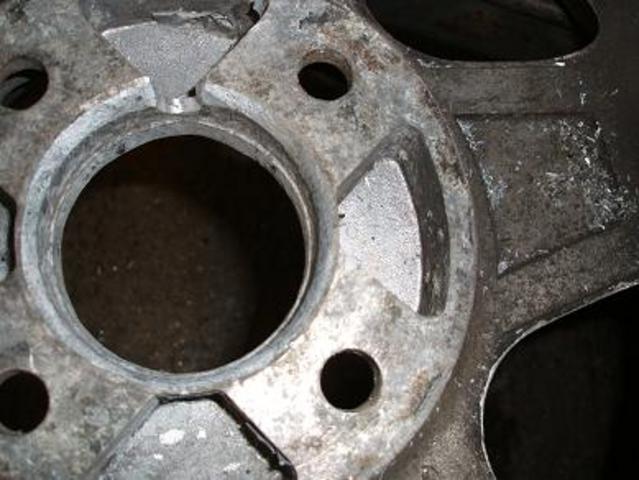 Rescued attachment wheel1.JPG
|
|
JoelP
|
posted on 30/1/06 at 08:07 PM |
|
|
and the bit
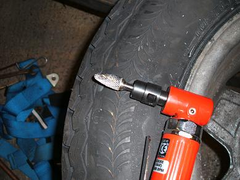 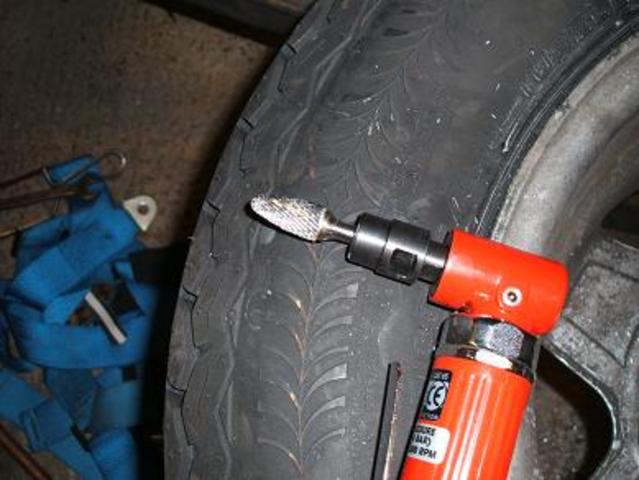 Rescued attachment wheel3.JPG
|
|
birt
|
posted on 30/1/06 at 08:33 PM |
|
|
You should be able to buy longer studs, what are they off originally? Try clicking here:
RALLY DESIGN. You will have to pop the old ones out with a hydraulic press.
They may knock out with a big hammer but I wouldn't recomend it. Similarly you should press the new ones in really.
Marc
|
|
clbarclay
|
posted on 30/1/06 at 11:17 PM |
|
|
My brothe had a similare problem when hi stuck alloys on a rover, The treads didn't go all the way through the nuts.
According to halfrauds the industry standard is a minimum of 8 turns on the nut. My brother got about 8 1/4 turns, he keeps a regulare eye on them but
so far they have not come loose or given any trouble.
|
|
indykid
|
posted on 30/1/06 at 11:50 PM |
|
|
sva inspectors only want to see 6 turns so he should be okay
however, if the thread pitch on a wheel stud is 1.5mm, that means for 6 turns of thread, there'll be 9mm of 'engaged' stud.
i've just measured an m12 nylock, and there's 8.5 mm of thread before the nylon.
since the same size nut is used to clamp the lower ball joint into the bottom of the upright, this one still copes even though it takes far more
loading than that shared by the 4 wheel studs and nuts. would it not therefore seem reasonable to assume that a wheel nut can cope with only being
engaged by 6 threads?
i'm not saying i'm right, and may have missed the main issue, but would welcome someone to put me right if that is the case. i do like to
learn from these things.
incidentally joel, how many turns do the nuts go on to on the trailer wheels?
tom
|
|
DaveFJ
|
posted on 31/1/06 at 08:54 AM |
|
|
just as an aside.... why do you want alloys on a trailer ???
Dave
"In Support of Help the Heroes" - Always
|
|
Kissy
|
posted on 31/1/06 at 09:58 AM |
|
|
because he can.
|
|
JoelP
|
posted on 31/1/06 at 10:16 AM |
|
|
the wheels vaguely match the car wheels, plus they were cheaper than new steels, and as kissy says, because i can! But if i'd've known how
much effort it would involve i wouldntve bothered!
I'll count the turns this evening cheers for your thoughs so far chaps. 
|
|
Fred W B
|
posted on 31/1/06 at 11:11 AM |
|
|
quote:
just as an aside.... why do you want alloys on a trailer ???
You don't understand.. out here it's not a proper car related trailer unless it's got alloys. I've seem kart
transporter/mobile workshops with 4 x 17" momo GT2's on!
Cheers
Fred WB
|
|
Confused but excited.
|
posted on 1/2/06 at 07:17 PM |
|
|
EXACTLY!
Tell them about the bent treacle edges!
|
|
Liam
|
posted on 1/2/06 at 08:41 PM |
|
|
quote: Originally posted by indykidhowever, if the thread pitch on a wheel stud is 1.5mm, that means for 6 turns of thread, there'll be
9mm of 'engaged' stud. i've just measured an m12 nylock, and there's 8.5 mm of thread before the nylon.
since the same size nut is used to clamp the lower ball joint into the bottom of the upright, this one still copes even though it takes far more
loading than that shared by the 4 wheel studs and nuts. would it not therefore seem reasonable to assume that a wheel nut can cope with only being
engaged by 6 threads?
i'm not saying i'm right, and may have missed the main issue, but would welcome someone to put me right if that is the case. i do like to
learn from these things.
I've wondered before why wheel nuts tend to have so much thread engagement. I put it down to the extreme vibration of their environment coupled
with the fact that no locking method is used, presumably cos the frequency of removing them makes this impractical.
But then the 'opposite' type of wheel nut commonly used (more of a bolt really that screws into holes in the hub) only have the thickness
of the hub to thread into which is probably no more than 8mm like a normal nut. So kind of throws that idea out the window.
Liam
|
|